Fertilizer International 520 May-Jun 2024
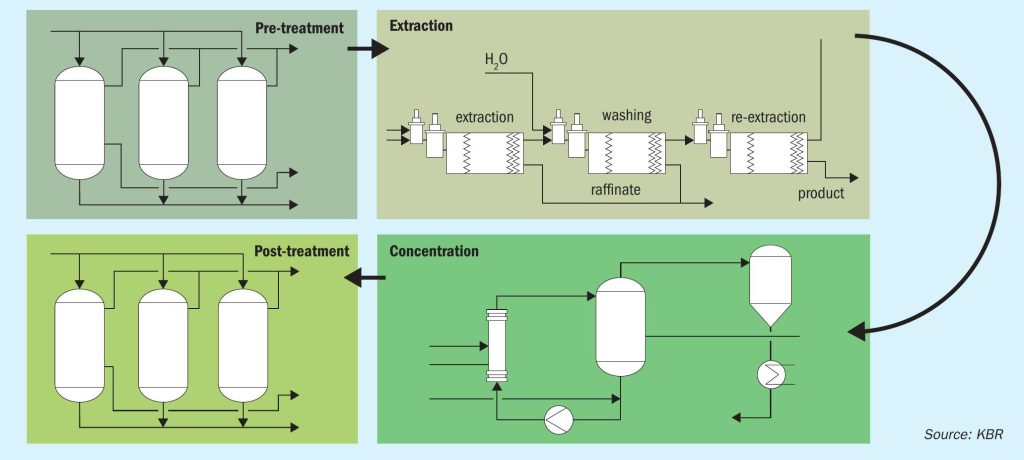
31 May 2024
KBR’s proprietary phosphoric acid purification technology
PURIFIED PHOSPHORIC ACID
KBR’s proprietary phosphoric acid purification technology
KBR designs and builds customised phosphoric acid purification plants tailored to the individual demands of clients. Christopher Heikkilä, KBR’s Business Development Manager, outlines the process design requirements and the challenges associated with impurities removal.
Overview
Phosphoric acid is commonly produced by the wet process to different quality standards. Green or merchant-grade acid (MGA), for example, can be directly used in fertilizer production without further purification, whereas most other applications require the removal of impurities to produce purified phosphoric acid (PPA).
Technical-grade PPA, for example, can be used to produce sodium tripolyphosphate (STTP), water-soluble fertilizers (WSFs) for fertigation and foliar applications, various other crop nutrient products, detergents, and animal feed additives. Food-grade PPA suitable for food industry and pharmaceutical applications requires further purification.
Addressing impurity removal challenges
The impurities present in green phosphoric acid, such as fluoride, chloride, iron, aluminium, sulphur and organic matter, can cause corrosion, erosion-corrosion, and scaling in industrial equipment. The removal of these impurities is a complex process that involves a range of methods (solvent extraction, precipitation, stripping, absorption etc.). These are selected, as follows, according to the types of impurity present and their concentration:
- Solvent extraction is used for removing impurities such as F – , Cl – , and Fe 3+ from phosphoric acid.
- Precipitation, while a suitable removal method for Fe 3+ and Al 3+ , is not effective for other impurities such as F – and Cl – .
- Stripping and absorption are mainly used to target and remove specific impurities to reach high purity requirements.
Selecting the right method is crucial for efficient and cost-effective purification. A typical four stage process (pre-treatment, extraction, concentration, post-treatment) is shown in Figure 1.
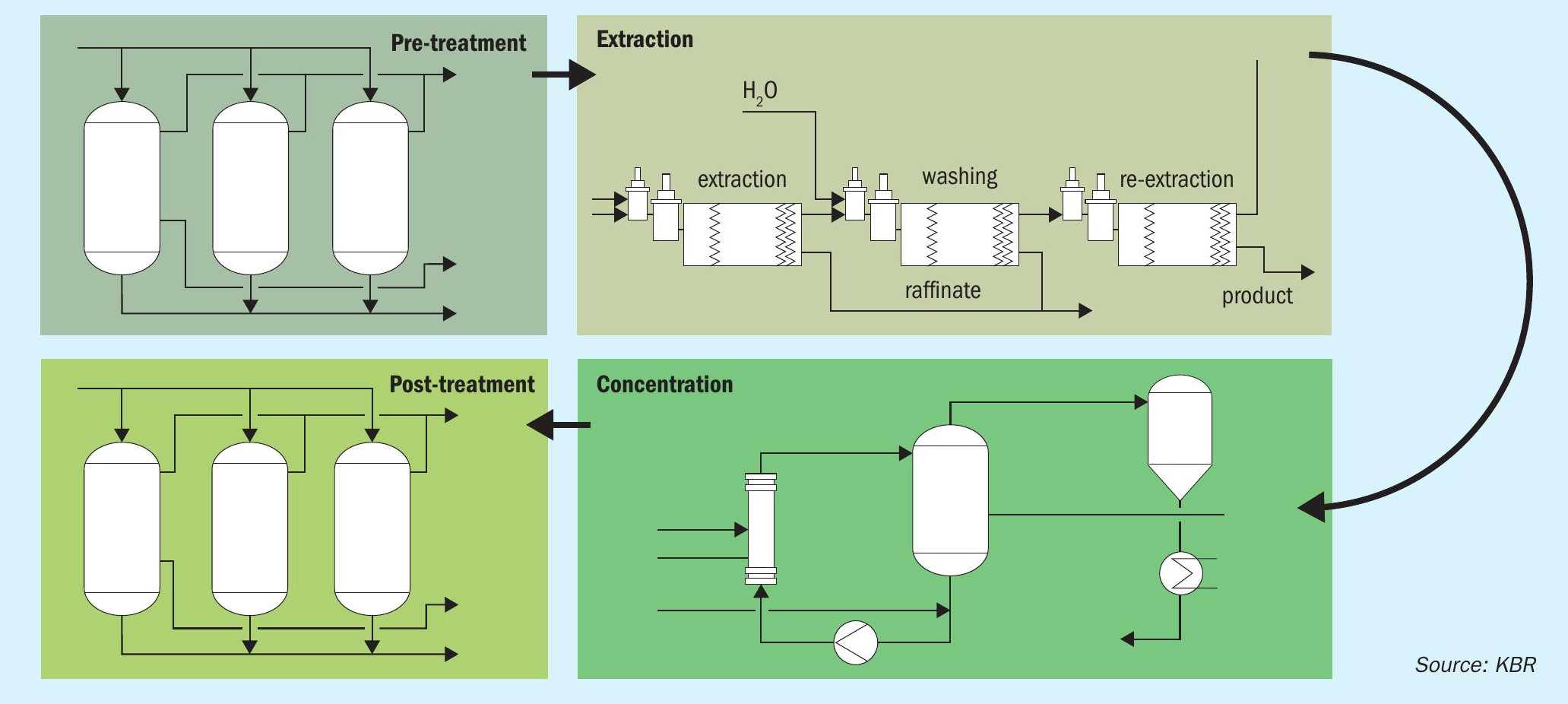
Technical-grade and food-grade PPA production
KBR has the key design advantages necessary to produce both technical- and food-grade PPA from green phosphoric acid.
“KBR worked with a Middle East client to design a phosphoric acid purification plant to convert phosphoric acid from merchant-grade to food-grade using its proprietary purification process.”
- Firstly, thorough lab testing and piloting are crucial steps in PPA production. By defining an optimised process flow sheet, they help to ensure that the final product meets the required quality standards.
- Secondly, project experience and references play a crucial role in ensuring high-quality phosphoric acid production. KBR’s experienced team of professionals can leverage this to optimise the production process, reduce costs, and improve the overall quality of the product.
- Careful material selection is yet another area where KBR has a key design advantage due to its extensive knowledge gained from applied processes. This ensures that the plant has long lifetime, with minimal downtime for maintenance, while delivering a final product of the highest quality.
- Energy recovery is also important for cost reduction and improving the overall efficiency of the production process.
- All KBR plants are tailor-made and optimised for specific client needs. This eliminates unnecessary or overdesigned equipment.
Project case study
KBR worked with a Middle East client to design a phosphoric acid purification plant to convert phosphoric acid from merchant-grade to food-grade using its proprietary purification process.
Through extensive lab testing and piloting campaigns, KBR obtained valuable data for designing and engineering the phosphoric acid purification plant – ensuring the client’s specifications for the purified product were met.
The phosphoric acid purification plant was designed to produce 51,667 t/a (100% P 2 O 5 ) of purified food-grade phosphoric acid. The proposed plant consisted of a single production unit comprising of following sections:
- Pre-treatment including the precipitation of SO 4 , F and As followed by solids separation, organic removal and concentration of the pre-treated acid.
- Solvent extraction including extraction, scrubbing, stripping and scrub raffinate concentration.
- Post-treatment including concentration, fluoride removal and decolourisation stages.
- Raffinate washing with kerosene to remove entrained solvent (tributyl phosphate).
- The purification plant was designed to deliver a final purified phosphoric output (62% P 2 O 5 ) from a merchant-grade phosphoric acid feed (50-54% P 2 O 5 ).