Nitrogen+Syngas 389 May-Jun 2024
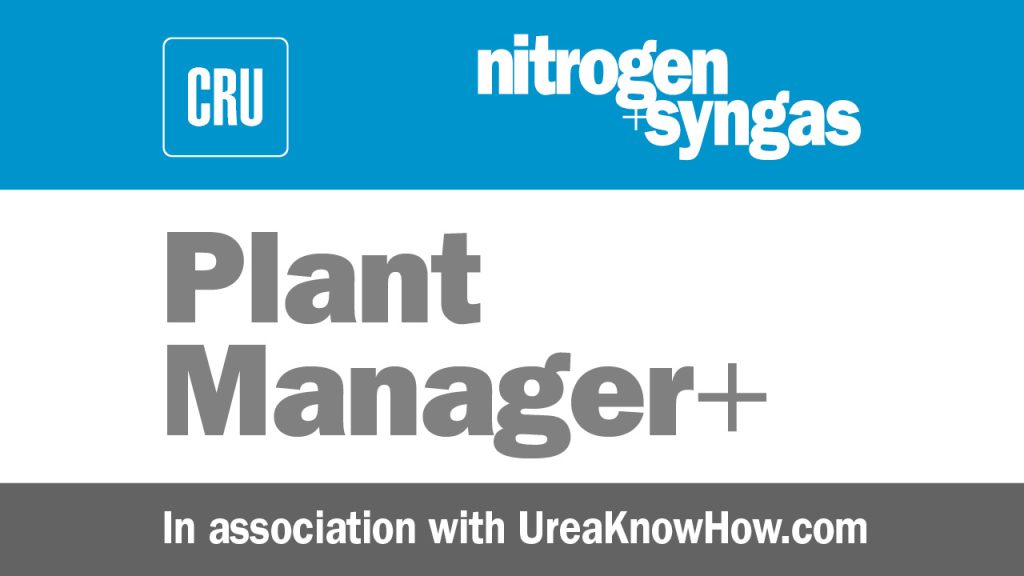
31 May 2024
Problem No. 73: Practical guidance on reducing biuret formation in urea
Biuret is a chemical compound with the chemical formula HN(CONH2 )2 , also known as carbamylurea. It is a commonly occurring undesirable impurity in urea-based fertilizers, as biuret is toxic to plants. Biuret is formed from urea, according to the following overall reaction:
2NH2 CONH2 → NH2 CONHCONH2 + NH3 urea biuret ammonia
The formation of a relatively high biuret content in urea is a particular problem when urea production plants are running at lower loads. The reasons for this, and potential solutions to it were the topic of a recent discussion on the ureaknowhow.com forum. This article is a summary of that discussion, which involved experienced plant engineers and managers from Saudi Arabia, India, Pakistan, Iran and Venezuela.
The discussion was initiated by two queries: The first query was about the relationship between production plant load and biuret content in the final product. The enquirer had one ammonia plant shut down and wanted to utilise all the excess CO2 from another ammonia plant to maximise urea production. They were worried that product quality would be off spec with respect to biuret if the urea plant was operating at 70% load.
The second query was from someone whose plant had a biuret content in the final product above 0.9 wt-% in one of their units, even when the plant load was 100%. They had tried to reduce this content by using all the recommended procedures (reducing the level of the decomposers holders, reducing the temperature of the high-pressure stripper). They wanted to know if there are any other ways to reduce the biuret content.
Biuret formation at reduced loads
In response to these queries, a forum participant suggested that at reduced load biuret can be controlled by the following measures:
- Keep urea solution levels in the holders (separators in the recirculation and evaporation section and the urea solution tank) as low as possible i.e. MP/LP/vacuum section.
- Keep the NH3 /CO2 ratio slightly on the higher side.
- Maintain the urea stripper temperature ~ 198-200°C for Snamprogetti technology.
- For plants using a prill tower, the urea melt delivery line to the prill tower is normally jacketed with low pressure steam; here the urea melt gets both residence time and temperature. Reduce the jacketing steam in this line during low load operation.
- If dust solution recovery is ongoing, reduce its flow rate.
He went on to say that the maximum allowable limit of biuret in the final product is set 1.0 wt-% at his plant. In normal operating conditions biuret is maintained < 0.9 wt-%, however at low load operation it sometimes exceeds 0.9 wt-%, but remains less than the set limit. If the biuret content exceeds the allowable limit, shipment of product is stopped and the urea is stored in bulk storage, from where it is recovered again in the form of a solution.
At this point, another participant asked if it is possible to add on-spec urea in order to reduce the level of biuret content in the stored off-spec urea.
The reply to this was that off-spec product (whether due to moisture, biuret, prill shape, fines etc.) is diverted to bulk storage (separate from on-spec stored urea). From these off-spec piles of urea, a solution of ~ 70-80 wt-% concentration is prepared to recycle back to the vacuum section.
Handling off-spec urea
A different participant then suggested another solution to handle off spec product: Pour fresh and on-spec urea (directly from the plant) via a tripper over the off-spec product in the bulk storage, until the stored product reaches the acceptable range. When this material is transferred to the bagging system it will then be further mixed more evenly.
A further participant warned against the practice of recycling the off-spec urea by dissolving it in water and passing it again through processing units such as the vacuum and prilling sections, saying that it would not solve quality product problems, as the level of biuret will increase again. In addition, the energy consumption of the steam in the vacuum section will increase.
Other practical steps
There were then several additional suggestions made, by a number of participants in the discussion: In a urea plant biuret formation is caused by two factors: one is residence time and the other is temperature. Therefore:
- Minimise the levels in the urea solution tank, evaporators, rectifier, HP stripper, level tank of rectifier outlet and suction of the melt pump and keep these as low as possible.
- Maintain minimum recommended temperatures in areas with higher than 50 wt-% urea concentration.
- Maintain a higher N/C ratio, if possible.
- Maintain a higher capacity, if possible.
- Check the urea melt pump efficiency: if you have lower efficiency you will have a higher temperature difference between the evaporator and the discharge temperature at top of the prill tower.
- Consider having two parallel melt lines to the prill tower. A reduced size line can be used at a low plant load to increase the velocity.
- Consider importing urea solution from other plants (if you have a second production line in the urea plant).
- For a temporary load reduction, the best option is still to store it as off-spec product and then mix it with on-spec product in the appropriate proportion.