Sulphur 412 May-Jun 2024
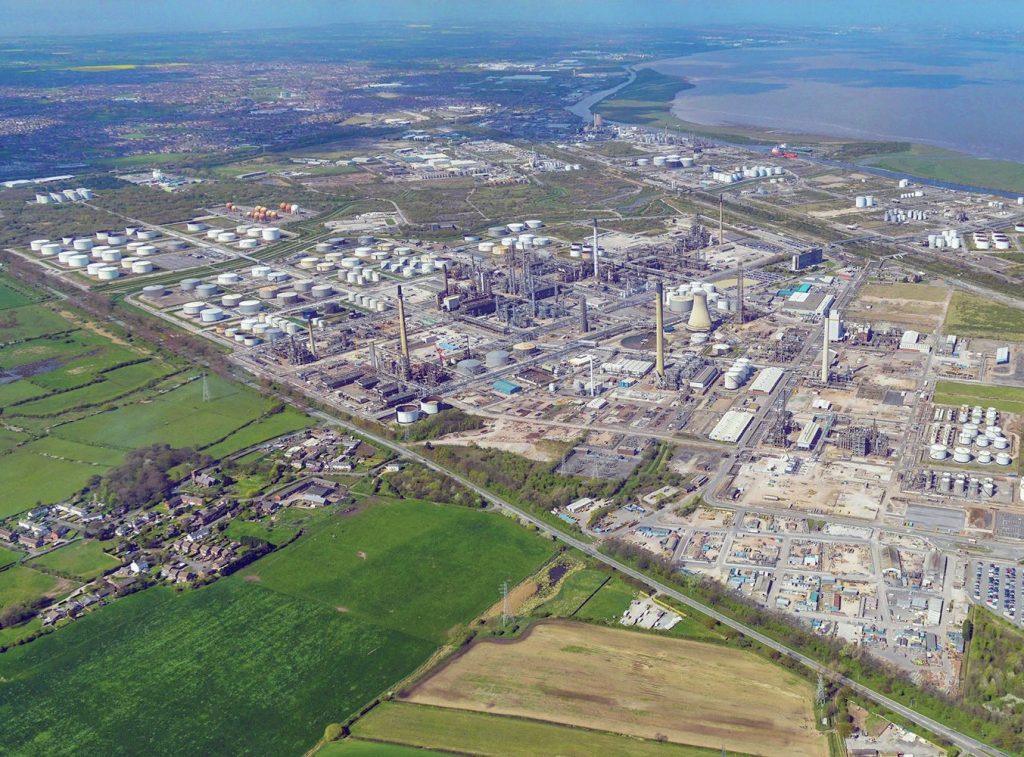
31 May 2024
Refineries and the energy transition
REFINERIES
Refineries and the energy transition
As refiners adapt to the transition to a lower carbon economy, different strategies are likely to impact upon sulphur output.
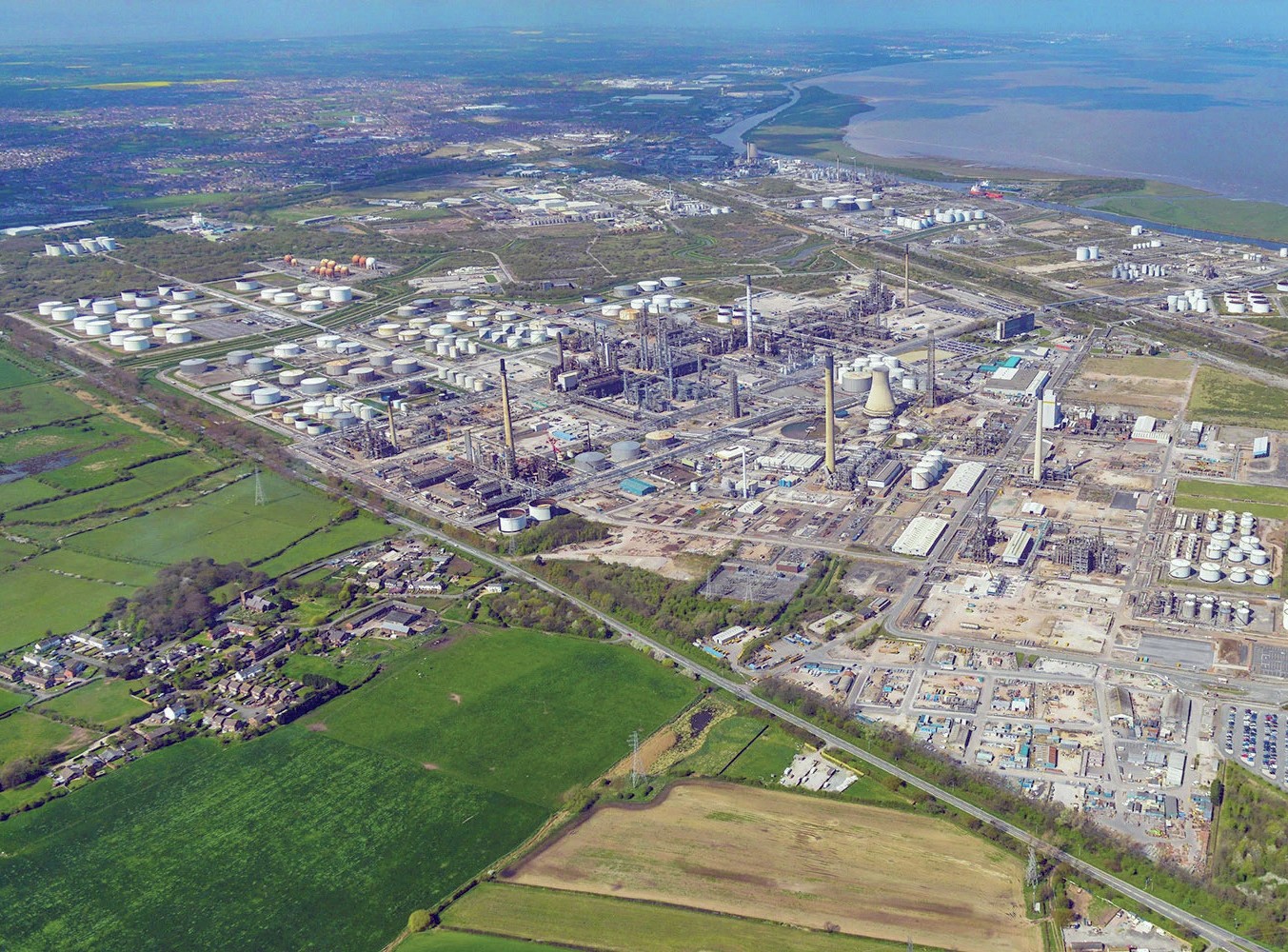
At present oil refining produces 32 million t/a of elemental sulphur, just under half of the total global supply of 67 million t/a. However, the global transition towards a lower carbon economy is leading to much greater uptake of electric and hybrid vehicles, eating into the demand for liquid fuels, which are the main source of demand for refinery products at present.
Demand is unlikely to fall rapidly. Some sectors are hard to electrify, such as aviation fuel or long-haul goods vehicles, both of which use middle distillates. However, demand from passenger cars, which is the largest segment of consumption, is likely to fall faster than these sectors, and overall refinery throughputs are forecast to peak and plateau from around 20252035, before beginning to fall thereafter, though some models see throughput falling earlier, from around 2030. But even with flat demand, there will be pressure on refiners to decarbonise their operations to a greater or lesser extent, depending on local regulatory environments, and these will in turn necessitate changes in operations or product mix.
Refinery strategies
Broadly speaking there are four strategies for refiners in dealing with these pressures;
1. Increase energy efficiency. Refining is an energy-intensive activity, and energy requirements have increased over the years to meet demand for cleaner fuels, e.g. in hydroprocessing to remove sulphur. Energy accounts for about 60% of the cash operating costs of EU refineries, a proportion that has doubled over the last 20 years as a result of increasingly stringent product specifications, higher refinery complexity and increasing energy costs. Many refineries already recover most of the heat generated, but most are not able to use low temperature streams such as very low pressure steam or hot condensate. Some efficiency gains can be achieved via cogeneration, but in e.g. Europe most refineries already integrate generation into their operation. Many refineries are looking at switching to renewable energy feeds for electricity, heat and even hydrogen production via electrolysis.
2. Switch to lower carbon products. Most (ca 85%) of the carbon emissions associated with liquid fuels are produced when they are burnt. If the carbon in the fuel comes from a lower carbon source, then it is a more environmentally friendly product. A number of refineries are converting to produce biofuels. In Italy, Eni has converted or is converting its refineries at Porto Marghera, Gela and Livorno, and in the US Phillips 66 is converting its Rodeo refinery to produce biodiesel. The current vogue for sustainable aviation fuels (SAF) is another manifestation of this trend.
3. Capture and store carbon emissions. Where suitable disposal sites are available, capturing and sequestering carbon dioxide is an option some refineries are embracing, such as Essar Oil’s Stanlow refinery near Liverpool, United Kingdom. Reducing precombustion emissions entails removal of carbon from the fuel gas system using reforming (steam or autothermal) or gasification technologies. The CO2 from the reforming processes is captured, and the hydrogen is used for downstream fired sources. Oxygen injection is also possible to increase the CO2 in the stack, thereby improving CO2 removal. Alternatively, post-combustion capture can be achieved via amine adsorption.
4. Switch to other production. While demand for liquid fuels may peak, demand for other petrochemical products is likely to continue to rise. For this reason, some refiners are looking for opportunities to adjust or modify their production to increase their output of naphtha, propylene, and reformate, where margins tend to be higher than for liquid fuel production.
A combination of these strategies is of course possible, depending in refinery configuration. However, challenges remain, such as cost and pressure on margins and utilisation, or finding ways to minimise the amount of bottoms sent to the bunker fuel pool, demand for which is also shrinking. Residue conversion techniques such as solvent deasphalting may assist with utilising refinery bottoms.
Closures
The alternative of course is closure of assets. Between 2023 to 2028, global refining capacity is expected to grow by 5.1 million barrels/day, based on currently announced capacity, whereas demand is expected to increase somewhere between 0 and 4.6 million bbl/d over the same period. North America and Europe are most susceptible to closures, with Wood Mackenzie forecasting that Europe may lose as much as 5 million bbl/d of capacity by 2050 and North America a similar amount. Asia and the Middle East are the only regions expected to see net capacity gains in the 2030s, with large chemicals integrated sites coming online, with net capacity losses not expected until the 2040s.
Competitiveness will be the key for refiners to survive this environment, requiring both strong margins and low carbon intensity of operation; the former perhaps derived from petrochemicals or renewable fuels, with better margins, the latter from investment in reducing emissions.
Sulphur production
The good news for the sulphur industry is that most of these transition strategies for refiners do not involve a reduction in sulphur production. Greater energy efficiency, a switch to renewable power sources and green hydrogen, or the installation of carbon capture and storage technology will still see the amount of sulphur recovered stay roughly the same. However, conversion to bio-refineries or of course closure will impact upon refinery sulphur output, meaning that refinery sulphur volumes are likely to begin falling in the US and Europe over the next few years. New refinery capacity in Asia will balance this at least as far as the end of the decade, but the current wave of ‘mega refineries’ in Asia will be over by about 2028, and it remains uncertain how much new capacity will be built beyond that. CRU’s current forecasts see overall global refinery sulphur output rising to 35 million t/a by 2026, and remaining roughly constant at that level for at least the next couple of years, but switching away from western markets towards eastern ones.