Sulphur 412 May-Jun 2024
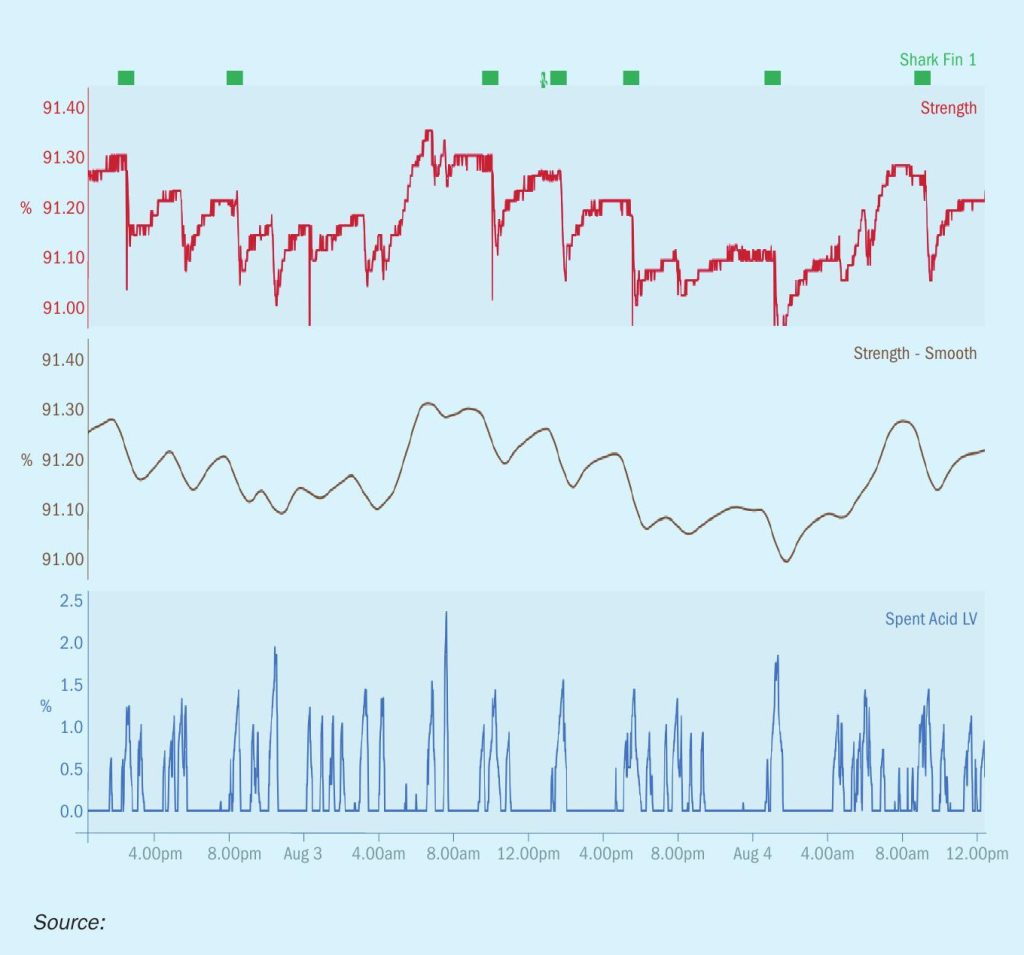
31 May 2024
Sulphuric acid in the age of technology
DIGITALISATION
Sulphuric acid in the age of technology
In today’s dynamic business landscape, digitalisation has become a powerful tool for companies seeking to enhance operations. By leveraging real-time plant data, organisations can create more meaningful interactions between operations teams, technical experts within the industry and the power of machine learning. David Dericotte and Linda Colby of Elessent Clean Technologies introduce the MECS® digital advisor, a web-based dashboard for plant performance assessment, troubleshooting and a supplemental mentoring tool for less experienced engineers and operators.
Traditionally, sulphuric acid plant operations have relied on legacy historian systems for data collection and knowledgeable staff with engineering insights and experience to interpret this data. These historian systems record process, lab and sometimes field-collected data without predictive algorithms, resulting in limited interaction with the operations team. However, the landscape is changing rapidly. Advanced analytics models, including machine learning and artificial intelligence, can be incorporated to go beyond traditional regression analysis. These tools can reveal hidden patterns and complex interdependencies, enabling more precise modelling of core plant functions for operations and maintenance planning.
In addition, it addresses down-to-earth, day-to-day needs for real-time collaboration, integrated turn-around planning, and mentoring of new hires.
MECS® digital advisor is a web-based dashboard that provides clients with a graphical way to visualise their plant data. It functions similarly to how subject matter experts (SMEs) would evaluate data to assess plant performance and troubleshoot issues. It is custom-built for each individual plant based on the customer’s latest set of P&IDs, instrumentation information, LIMS and CIMS data. Using the data from the instruments or tag data, custom dashboards are developed to visualise data via data trends, comparisons, ratios, data analytics and other leading indicators that predict plant performance. This is intended to help reduce process operational creep. Each graphic includes some level of explanation and operation direction. Dashboards can communicate progress on key improvement initiatives across multiple levels in the client organisation. Should the tracked key process variables or indicators exceed targeted limits or exhibit suspect behaviour, an event notification can be sent to SMEs and key customer personnel, if desired. Additionally, from the website, users can access, download, and print reports.
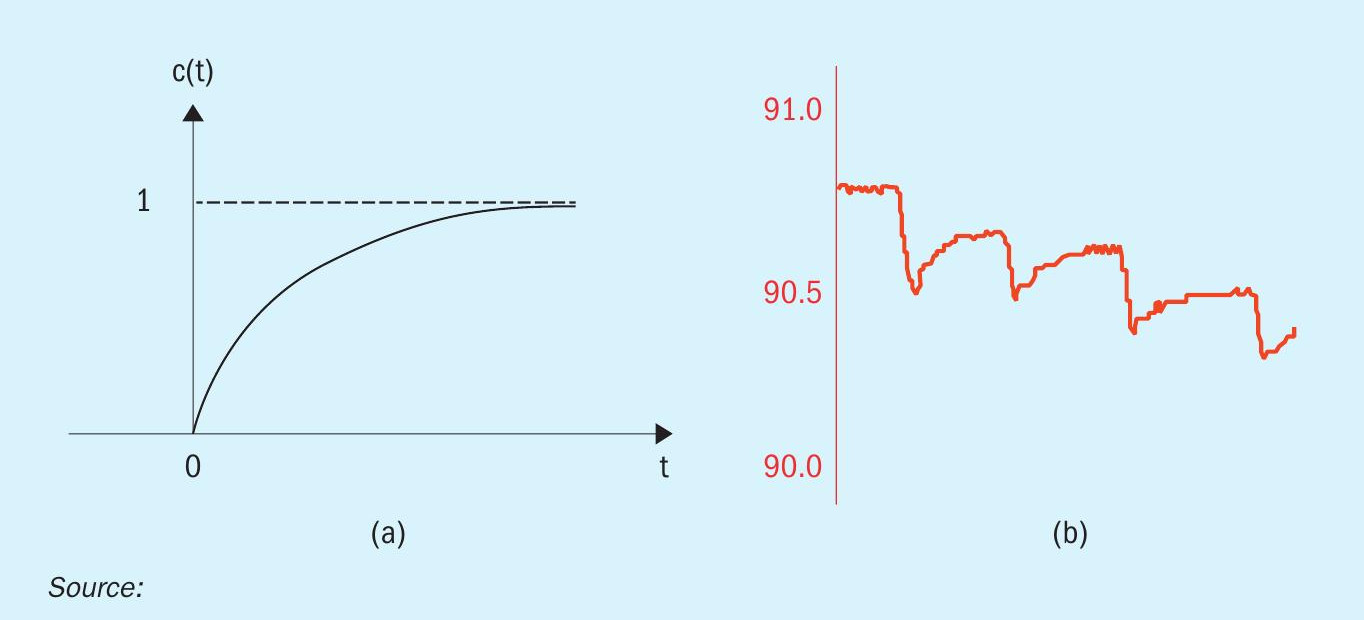
This type of in-depth data evaluation can also allow client and MECS engineers to better collaborate on turnaround planning. An example could be the review of the converter health. By comparing converter operational trends to previous MECS® PeGASyS™ data, catalyst screening and loadings can be better optimised.
Across multiple industries, companies are experiencing departures by many of their senior operations experts. And for new development grass roots acid plant applications, the plant sites can be remote with little surrounding infrastructure to facilitate quick, easy visits by experienced engineers. MECS® digital advisor can be set up to track changes and to make scripted recommendations on possible actions that can be reviewed through the website. If the problem persists, a call to one of the MECS SMEs may be warranted. It is one thing to see a change in a trend; it is another to understand what to do about it. MECS® digital advisor as well as developing a close relationship with MECS SMEs can provide mentoring to less experienced engineers and operators.
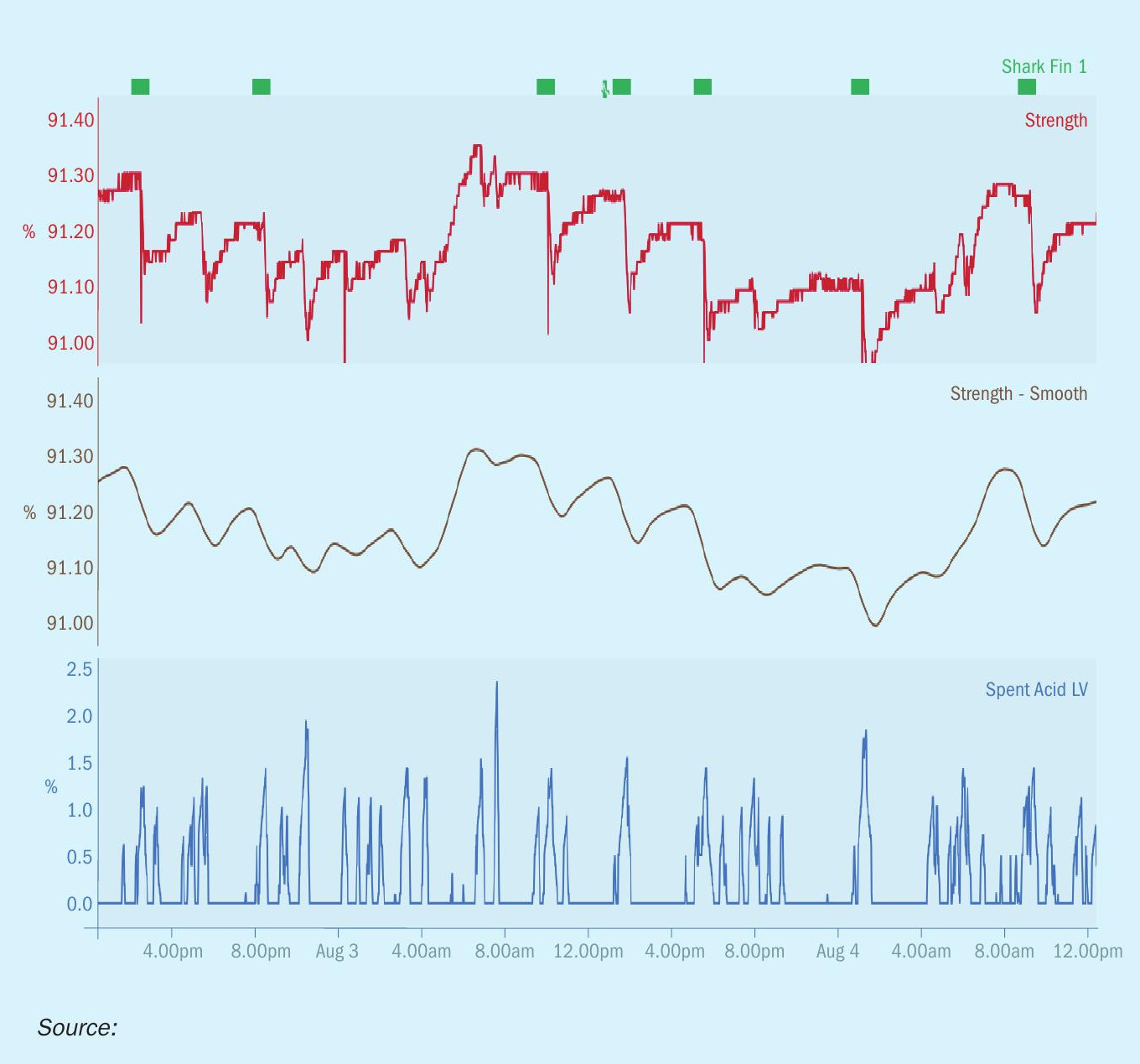
MECS® digital advisor is designed to work with multiple data historians and data transfer mechanisms. MECS has used AVEVA Cloud Connect, developed an Edge device, and REST API as possible front doors to facilitate data exchange. MECS partnered with RoviSys™ who applied its deep development experience to create the integrated engine and security design behind the MECS® digital advisor. Data security is key to protecting both client intake data and MECS know-how. One of the first objectives of this tool creation was securing the system. MECS incorporated tools from:
- Microsoft Azure Cloud Hosting
- Authentication by Microsoft -Entra (Azure AD and B2C.)
- 24x7x365 Security Monitoring by SOC – cybersafesolutions.com
- Antivirus and IDS provided by Sentinel One
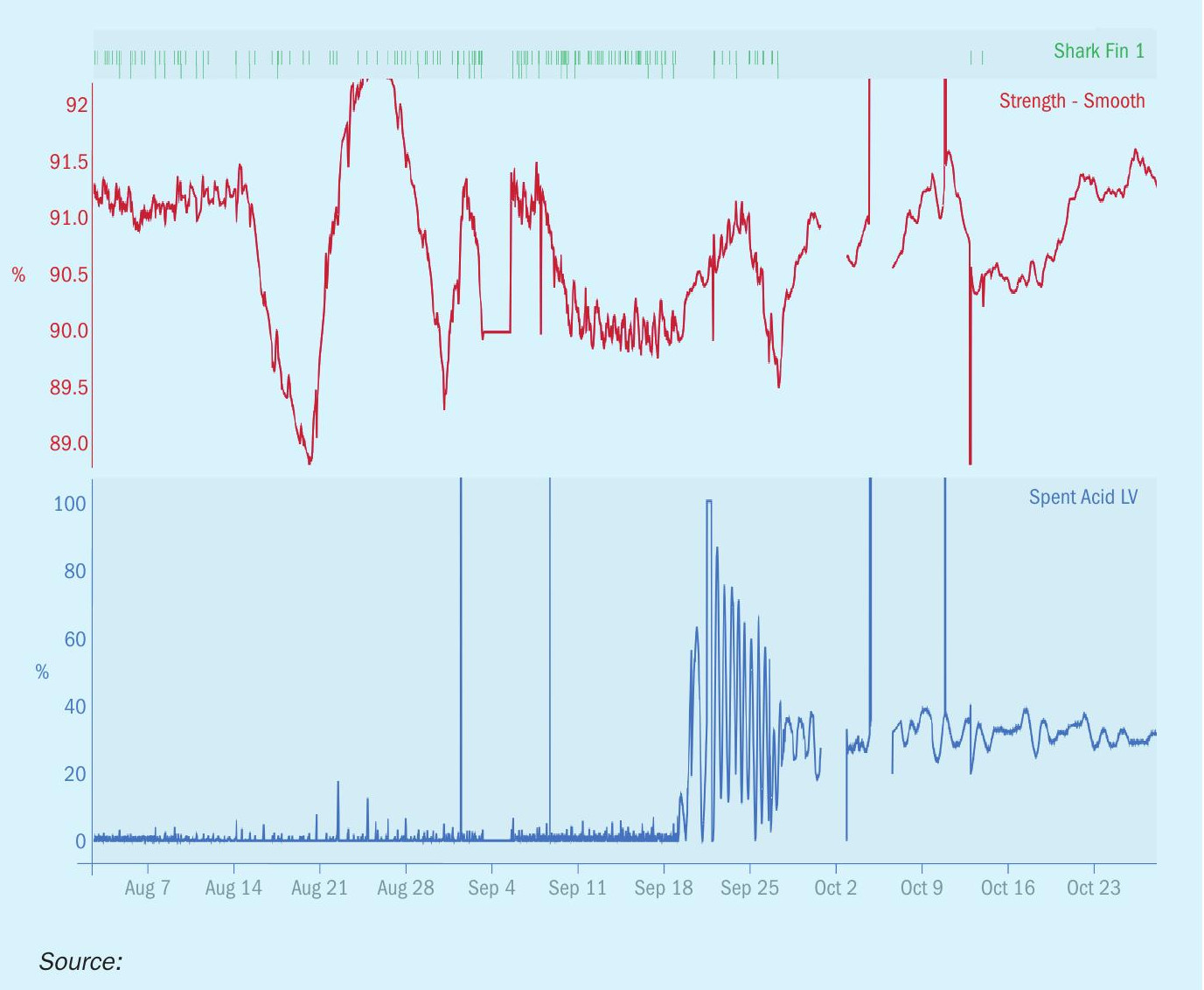
Safeguards using firewalls and multiple servers create a safe environment to share data.
Below are two different examples of how MECS® digital advisor is being used to better plant operations and safeguard equipment.
Spent acid strength is a key economic variable for sulphuric acid regeneration plants tied to alkylation units. Recently, using MECS® digital advisor to review detailed process data, an MECS SME noticed unusual behaviour in the output from a refractometer used to measure spent sulphuric acid strength, suggesting a problem with the instrument and/or the measurement environment or process control devices. After cross-checking several variables available within MECS® digital advisor, the SME confirmed that the observed response was real (not noise) and, within a few hours without having to interrupt the customer’s engineering team, completed a detailed root cause analysis, identified the core issue affecting the process and prepared a presentation on the situation that included a recommended response strategy to the customer’s operations team.
Using the tools available within MECS® digital advisor, including Seeq® (an advanced analytics, ML, & AI platform purpose-built for unlocking and visualising the insights hidden in time-series data), the SME walked the customer through the analysis work path, sharing background information to connect the core issue to the observed effects along with a historical analysis that quantified how frequently the issue had been occurring over the past several months. As the customer applied the MECS recommendations, the SME continued to monitor the key process variables via MECS® digital advisor to help the customer refine the solution and significantly improve the signal’s accuracy.
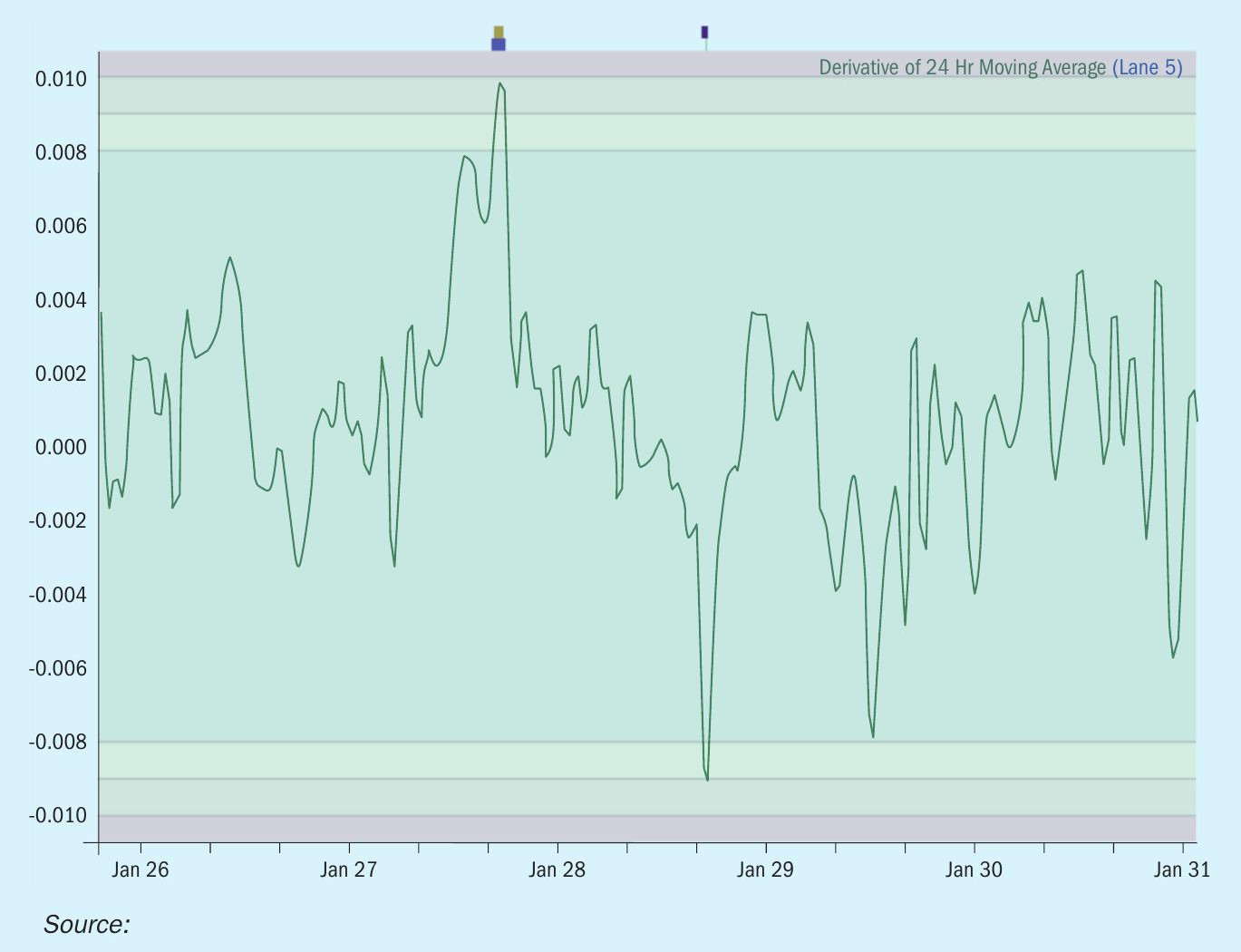
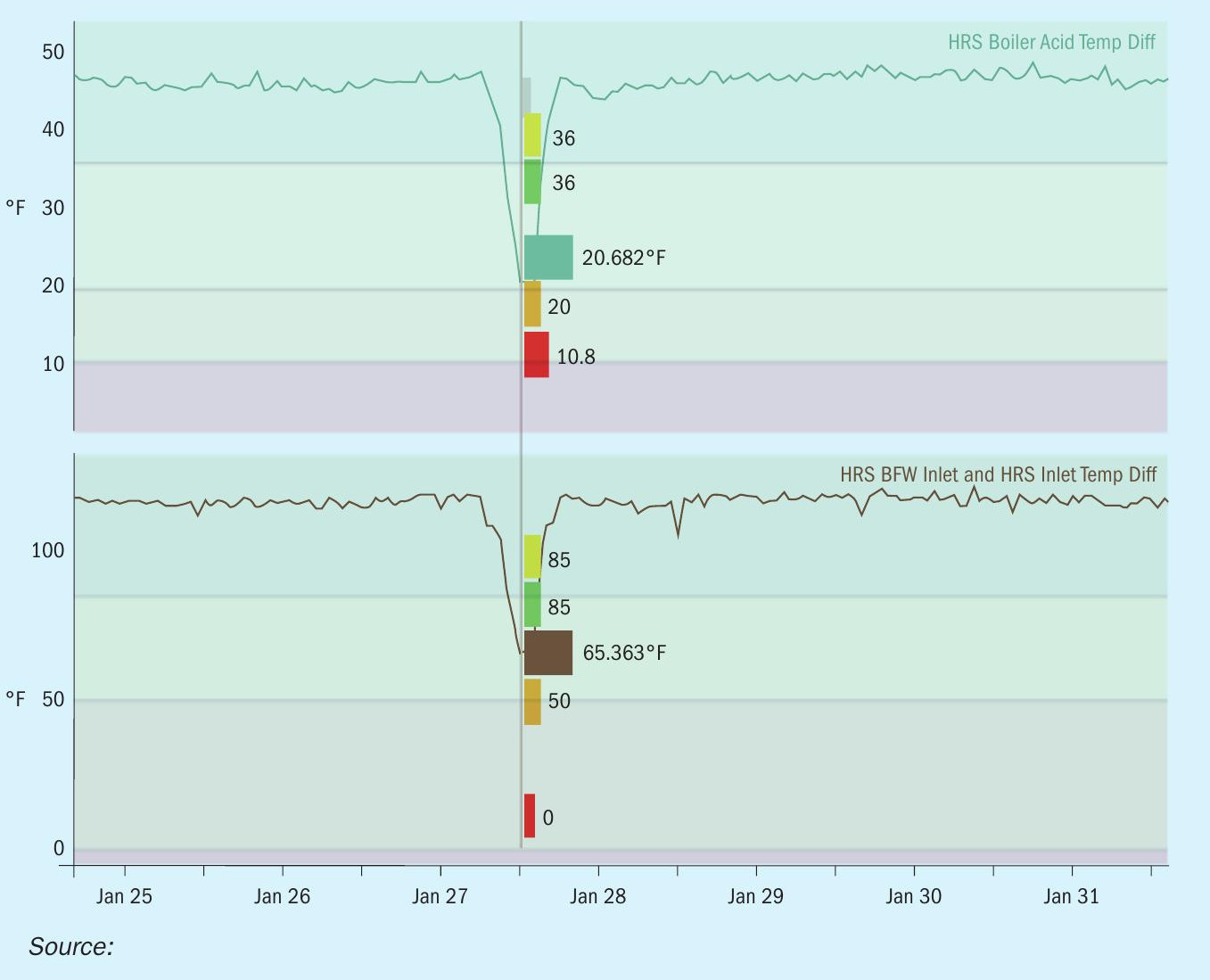
The next few figures illustrate the analytical journey described above. Observe, the solution “tuning” period in the middle of the chart in Fig. 3, where the spent acid level valve signal shows relatively high amplitude then levels out as the solution is refined, and the significant decrease in the detected pattern after the final solution as evidenced by the significant reduction/elimination of the green capsules at the top of the chart in Fig. 3.
The next example illustrates MECS’s efforts to continually improve methods for rapid detection of operational shifts within HRS™ units The earlier an issue is detected, and corrective action taken even before the alarm state is met, the better the outcome for the system.
In Fig. 4, the first derivative of HRS™ boiler steam generation to boiler feed-water ratio is tracked. Ideally, the slope should be flat, oscillating around zero. The system can statistically analyse the spikes in this ratio looking for a growing number of occurrences that may indicate an issue versus instrument or system noise. The system is also looking for a slowly rising trend that may indicate an equipment issue.
The HRS™ system instrumentation tracks the HRS™ boiler acid temperature in and out as well as the HRS™ boiler feedwater heater temperature in and out. Using this information graphically illustrates several delta comparisons (see Fig. 5). The HRS™ boiler feed water heater outlet temperature should always be less than the acid inlet temperature (bottom chart). The differential between the HRS™ boiler acid outlet temperature and the boiler inlet temperature should be greater than 6°C which is the trip point for the system (red zone), with the preference to be in the green zone about a 36°C delta. The colours provide banding that indicates a narrowing of the delta. And then in the example shown in Fig. 5, a return to normal, steady operation. Using this type of data, the operator and an MECS SME can work through an investigation decision tree.
Technology is changing fast. Operations and engineering teams and technical experts can harness these new tools to help improve the operations of a mature industry. Many key variables within sulphuric acid plants may need close monitoring for evaluation. MECS® digital advisor is designed to create an operations team that is more informed, more responsive, and able to focus more time on key priorities. It provides a novel approach to visualising data compared to traditional DCS screens and can be a supplemental mentoring tool for less experienced engineers and operators. It allows MECS SMEs to respond faster than the traditional fly-in boots-on-the ground approach.