Sulphur 413 Jul-Aug 2024
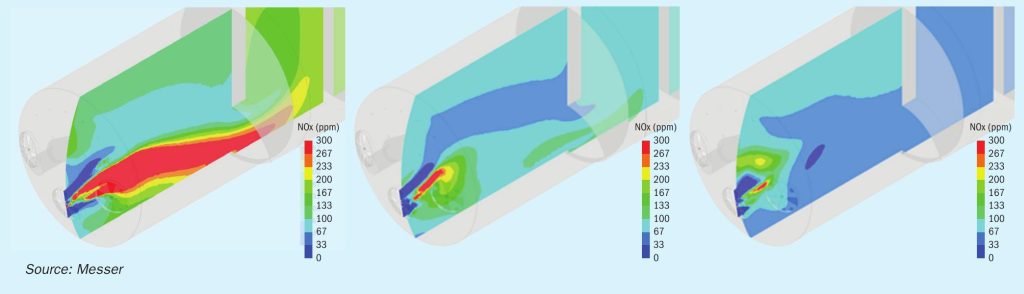
31 July 2024
Boosting sulphuric acid production with oxygen
SPENT ACID RECOVERY
Boosting sulphuric acid production with oxygen
A plant operating a spent acid decomposition furnace as part of its sulphuric acid production facility desired to increase acid production primarily by processing additional spent acid while making minimal modifications to the plant equipment and operations. The Messer solution entailed introducing oxygen in two steps, both as an enrichment to the combustion air and by direct injection into the furnace. The resulting performance improvements exceeded the project objectives for acid production and spent acid decomposition, without increasing NOx emissions. This paper provides a summary of the system start-up and tuning and presents the resulting improvements and lessons learned.
Sulphuric acid is used in petroleum refining as a catalyst for the alkylation of isobutane with C3-C5 olefins to produce higher octane gasoline for motor vehicle use. The process causes the sulphuric acid to become “spent” as it is contaminated with impurities such as water and hydrocarbons. Disposal of spent acid is not economical, and the preferred solution is to regenerate it in a spent acid recovery (SAR) unit. In recent years the volume of spent acid production has increased significantly. The investment required to construct new SAR units can be prohibitive, so production facilities look for opportunities to increase the capacity of existing equipment.
The first step in the SAR process consists of a decomposition furnace in which the spent acid is converted to sulphur dioxide (SO2), which is subsequently cleaned, oxidised to sulphur trioxide (SO3) and ultimately used to produce fresh sulphuric acid. Other sulphur-containing streams such as raw sulphur may also be introduced into the furnace to increase the amount of SO2 produced. Since the decomposition of the spent acid is endothermic, supplemental fuel is required to maintain the furnace outlet temperature. An increase in the production capacity of the SAR decomposition furnace may be limited by operational, product quality or environmental constraints that cause bottlenecks in the process.
There are well-established strategies for increasing the capacity of a furnace to decompose more spent acid. One is to preheat the combustion air to improve thermal efficiency by reducing the amount of fuel required. This accounts for the additional heat needed for the reaction, but there are practical limits for the maximum temperature to which the air may be heated. Another strategy is to supplement the combustion air with excess oxygen, which provides a way to increase the amount of oxygen available for reaction while reducing the overall volume of the combustion air due to the corresponding decrease in the combustion air nitrogen volume. This allows more fuel to be fired in the furnace to generate the necessary heat to decompose more spent acid. However, there are safety concerns that limit the extent of oxygen enhancement in the combustion air.
Both approaches allow for more spent acid to be decomposed while maintaining the appropriate levels of furnace exit gas temperature (FEGT) and excess oxygen concentration, without significantly increasing the pressure drop across the furnace. Unfortunately, they each result in higher adiabatic flame temperatures and lead to higher rates of NOx formation. Higher NOx can lead to product quality concerns in the form of increased nitre concentration in the acid produced. Facilities with stringent environmental regulations are not able to increase their NOx emissions and must therefore innovate to achieve their spent acid processing goals.
The reference plant operates an SAR unit in which the spent acid decomposition furnace was the primary bottleneck preventing the plant from achieving its authorised acid production rate and limiting the rate at which spent acid could be processed. The customer performed process simulations that indicated the potential to increase throughput by oxygen enrichment, thereby increasing the amount of spent acid feedstock for sulphuric acid production. Since Messer has a long history of working with the customer to supply industrial gases and technology solutions, the company reached out to Messer for assistance with the analysis. The project team, with decades of NOx control experience, ran several additional process simulations and used CFD modelling to test alternative solutions. These iterations helped Messer determine the conditions needed for the furnace to process more spent acid, produce more SO2 , and meet the existing operational and environmental constraints.
Process description and objectives
The plant is equipped with a spent acid decomposition furnace for producing SO2. The furnace has a cylindrical shape and is divided into multiple segments by internal walls designed to redirect the streamlines of the combustion products to increase residence time and to achieve the desired mixing level. The furnace is equipped with multiple burners which fire a mixture of a fuel and preheated combustion air. There are multiple ports through which spent sulphuric acid or other sulphur-containing streams may be injected. To maximise the conversion of the input streams to SO2, the furnace exit gas temperature and excess oxygen concentration are maintained at typical conditions to maximise SO2 production.
The capacity improvement project presents multiple challenges. Increasing the production of pure sulphuric acid requires a greater volume of SO2 exiting the furnace. This is problematic because the entire SAR process train is fan limited, meaning that the existing fans that move the gases through the process are operating at the maximum pressure drop. Increasing the amount of spent acid that can be introduced into the furnace as a feedstock is challenging because the decomposition of the spent acid is endothermic, so additional fuel must be fired to supply the necessary heat to complete the reaction and maintain the desired FEGT. The combustion products of the fuel increase the volumetric flow rate and result in a higher pressure drop and lower residence time through the fixed geometry components of the SAR process train. This also has a negative impact on the performance of the downstream process equipment. Higher firing rates through the existing burners can elongate the flame such that it impinges on the back wall of the first mixing chamber in the furnace. This can result in materials of construction issues along with poor combustion quality and an increase in products of incomplete combustion.
The ability to achieve the objectives was further constrained by the NOx mass emission limit. Raising the concentration of oxygen in the combustion air entering the burners causes the adiabatic flame temperature to increase and results in higher NOx emissions. Increasing the amount of fuel fired to decompose additional spent acid has a double-negative effect. Assuming the NOx emission rate remained unchanged on a mass per unit of heat input basis, a higher fuel rate would generally produce a linear increase in the NOx mass emissions. However, a higher fuel firing rate also results in a larger, hotter flame and produces higher rates of NOx formation per unit of heat input, so the impact of higher fuel flow is compounded. Therefore, to prevent the NOx mass emission rate from increasing, the rate of NOx formation on a mass per unit of heat input must actually be decreased.
Approach
As noted previously, the SAR unit is limited by the capacity of the existing fans to push more gas through the process. The use of pure oxygen to displace a fraction of the decomposition furnace combustion air is an established solution that has dual benefits associated with the reduction in the amount of nitrogen passing through the process. The oxygen enrichment of the combustion air allows the process to operate more efficiently with less nitrogen acting as a heat sink, and the volume of nitrogen that is removed can be replaced with additional volumes of SO2, leading to higher production capacity.
The decomposition furnace utilised multiple sulphur-containing feedstock streams that contributed to the total amount of SO2 and ultimately pure acid produced by the process. Of the streams, the spent acid is the most economical source of sulphur because it is a revenue source for the facility. Other feedstock may be cost-neutral or considered to be an operating expense. The calculation of the financial benefit is further complicated by the need to account for the additional fuel required for the endothermic spent acid decomposition reaction, whereas the oxidation of some sulphur-containing feed streams is an exothermic reaction that contributes heat to the process energy balance. When all factors are considered, an SAR plant’s most lucrative operating mode is one in which the amount of spent acid processed is maximised.
The economic benefit of using an existing SAR unit to produce more pure acid while using higher feed rates of spent acid is obvious. Although, since both spent acid decomposition and acid production result in higher volumetric flow rates, the solution for achieving these benefits with a fan-limited process is less straightforward. The potential improvement from oxygen enrichment can be determined using a simple simulation for the mass and energy balance.
However, a simple simulation is not capable of predicting the higher rate of NOx formation that results from the impact of oxygen enrichment on the adiabatic flame temperature. Even if the impacts of higher NOx on the product quality and the environment are not considered, there are material and safety limitations to the amount of oxygen that can be mixed with the combustion air upstream of the burners.
Since the process requires higher amounts of oxygen enrichment and the amount of oxygen that can be mixed with the combustion air has practical limitations, it follows that some of the oxygen must be introduced separately from the burner. This approach requires the application of a complex CFD simulation with numerous submodels that are utilised to determine temperature and gas concentration profiles in the furnace to identify the appropriate location and manner of injection for the additional oxygen.
Process simulations
To achieve the stated objectives numerous factors need to be evaluated:
- the amount of additional fuel that must be introduced to supply the heat for decomposing the higher spent acid rates;
- the amount of oxygen needed to offset the higher SO2 volume produced in the furnace;
- the amount of oxygen that should be added to the combustion air compared to how much is injected directly into the furnace;
- how to inject the oxygen into the furnace to maintain the existing mixing and reaction chemistry while reducing the rate at which NOx is formed.
Each of these factors must be continually re-evaluated as the process conditions change (e.g., the overall production rate or the relative amounts of spent acid, raw sulphur and any other sulphur-containing feed streams that are being fed to the furnace).
A two-step process simulation approach was utilised to evaluate the aforementioned factors and provide insights that would inform the design and implementation of the system. In the first step, Unisim was used to establish the mass and energy balance for the decomposition furnace. These values were then input into CFD models of the process containing about four million computational cells. The models incorporated numerous submodels, including those for chemical reactions, two-phase flows, turbulence, radiation, wall conditions, droplet vaporisation, and NOx formation.
Post-processing of the model results provided graphical depictions of numerous furnace conditions such as velocity vectors and temperature profiles, along with species concentrations including oxygen, sulphuric acid, SO2, NOx, and fuel. The baseline operation of the furnace was modelled, and then the furnace parameters were adjusted to reflect the changes in spent acid feed rate, the amount of oxygen injection, and the overall acid production rate. The results were used to indicate how changes to the location and amount of oxygen introduced into the furnace would affect the overall process conditions. In particular, the relative predictions for the NOx formation rate proved valuable in developing the design of the system. Fig. 1 presents some of the results of the CFD simulations.
Apparatus
The process simulations provided the information used for the design of the oxygen supply and injection system. The supply system provides gaseous oxygen on demand to a metering skid controlled by the plant distributed control system (DCS). The metered oxygen is piped from the skid to a manifold adjacent to the decomposition furnace. There are two sets of metering skids and manifolds, one for the oxygen enrichment of the combustion air and the other for the oxygen injection into the furnace. The oxygen flows from the enrichment manifold to a sparger located in the combustion air duct. CFD modelling was used to design the sparger so that the oxygen mixes completely with the combustion air prior to where it splits to supply the individual burners. The furnace manifold has multiple outlets so that oxygen may be delivered to more than one location simultaneously. The furnace injectors are designed to penetrate the furnace wall by a specified amount and are manufactured from a higher alloy that allows them to survive the conditions in the furnace. They deliver a sonic flow of oxygen to achieve the desired distribution and mixing with the gases in the furnace interior. The DCS is programmed to control the oxygen flow for a given operating condition and the corresponding decrease in the amount of combustion air needed. The DCS also determines the split in the fraction of oxygen used for combustion air enrichment, while the balance is injected into the furnace. The oxygen supply program works within the existing operating control parameters of the system that maintains the proper temperature and excess oxygen concentration at the furnace outlet.
Presentation of results
The demonstration focused on two primary objectives. The first was to determine the effectiveness of additional oxygen for increasing process capacity. The goals for the capacity increase consisted of two subparts, one of which was the ability to process greater volumes of spent acid while the second was to produce higher amounts of pure acid.
Since there are multiple sources of sulphur being fed to the furnace, the increase in spent acid consumption was not linearly related to the sulphuric acid production rate. This was fortuitous due to the greater number of process constraints limiting the pure acid production as compared to the ability to process spent acid. The second primary objective was to maintain the NOx emission rate at or below the baseline levels. Due to the additional heat input required to process more spent acid, the NOx concentration had to decrease on a lb/MMBtu basis to maintain the same mass emission rate. The results associated with each of the primary objectives are presented in the following sections, and the data presented have been normalised to protect the site’s process information.
Processing capacity improvement
The testing results of increasing both the acid production and the rate of spent acid processing are presented in Fig. 2. (Please note that these operating conditions are the same in all subsequent figures.) The trend lines represent a linear fit of the individual data points collected. At each condition, the primary variables were the oxygen flow rate and the amount of spent acid and other sulphur-containing feed streams. The process air and fuel flows were then adjusted to maintain the target FEGT and excess oxygen concentration. The process was allowed to reach steady conditions and then held for a sufficient time to obtain an accurate representation of the resulting performance. One-minute averaged data were collected by the DCS and these were later extracted and averaged over the duration of the individual test condition to produce the data points presented in the figure.
Fig. 2 shows a moderate improvement in the sulphuric acid production rate as the oxygen flow rate was increased. These data are somewhat misleading because the sulphuric acid production rate was intentionally restricted due to a number of constraints that occurred futher downstream in the process. These bottlenecks prevented the process from sustaining the maximum sulphuric acid production, and most of the testing occurred at rates less than 10% above baseline. However, some shorter-term results were obtained that suggested that a 15% increase was readily achievable.
The limitation of the sulphuric acid production rate was accomplished by reducing the rate of the other sulphur-containing feed streams to offset most of the additional sulphur entering the furnace as spent acid. This represented a preferred mode because the other feed streams are typically either an operating expense or cost-neutral but plants receive payment to process spent acid. Factoring in the oxygen cost and the additional fuel required to decompose the spent acid, the economics of this scenario were far superior to the baseline.
Variability in the spent acid data is generally due to changes in other process variables. For example, there were often test conditions in which different spent acid flow rates were evaluated at a single rate of oxygen flow. Since some of these test conditions are not representative of the ‘ideal’ at a particular oxygen flow rate, the slope of the trend line skews slightly lower than what would be achievable under normal operating conditions. Even so, the data shows that the performance target of 30% increase in the spent acid processing rate was achieved.
Emissions reduction
The primary challenge for increasing the spent acid processing rate was the regulatory requirements that limited the amount of NOx emissions. As described previously, both increased oxygen in the combustion air and the higher fuel firing rates required to decompose the spent acid tend to increase NOx formation rates. A key aspect of the demonstration was to determine how well the NOx could be managed by a combination of oxygen enrichment of the combustion air and direct furnace oxygen injection. Fig. 3 illustrates the outcome of that evaluation. Note that the normalised spent acid scale is presented on the left-hand y-axis and the normalised NOx mass emission rate is on the right side of the plot. The initial testing focused on adding oxygen to the combustion air as the spent acid rate increased. As expected, this caused the NOx emission rate to increase dramatically, and the testing had to be suspended to avoid exceeding the time-averaged regulatory limit. The results showed that with oxygen enrichment of the combustion air, only a 5% to 10% increase of spent acid could be achieved before exceeding the target NOx limit.
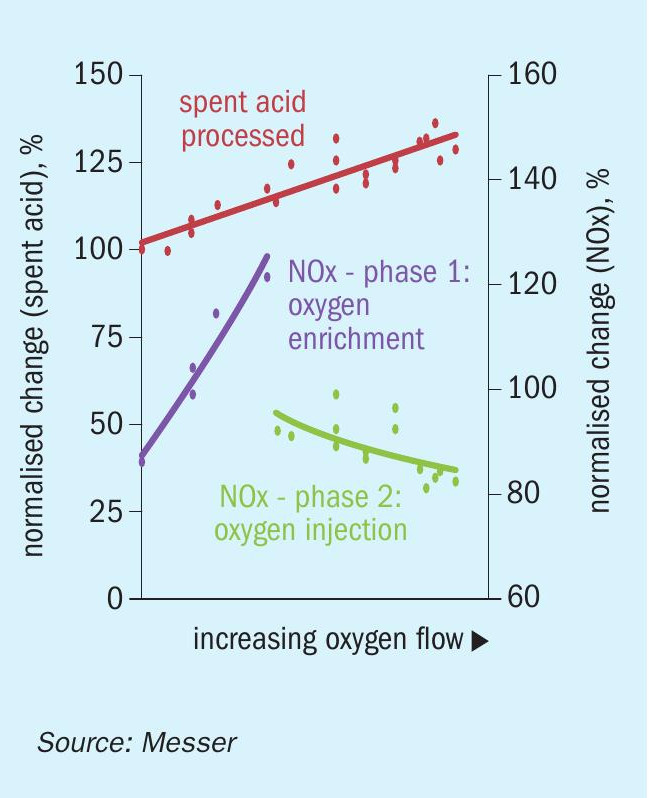
The next phase of the evaluation was to begin switching some of the oxygen supplied to the process from combustion air enrichment to direct furnace injection. As seen in Fig. 3, the furnace oxygen injection had an immediate effect in reducing the rate of NOx formation and the mass emission rate of NOx continued to decrease with increasing oxygen flow. This is significant because the reduction in NOx is occurring while the spent acid processing rate and the corresponding fuel firing rate are both increasing. These conditions also align with those presented in Fig. 2, in which the pure acid production rate has increased by 5% to 10%. Therefore, the NOx concentration is decreasing even more dramatically than that depicted by the mass emission data in the figure. The conditions shown in the figure are all at steady state while the operators were able to maintain the FEGT and excess oxygen concentration at their normal targets.
The CFD modelling indicated that there are two primary drivers associated with direct furnace oxygen injection for the reduction in the NOx formation rates. The first is the change in the stoichiometric ratio of air to fuel in the primary flame zone. The amount of combustion air decreases as the oxygen flow rate increases, and when the oxygen is injected directly into the furnace there is much less air/oxygen being introduced through the burner. This results in the burner flame stoichiometry being less fuel lean, causing a scarcity of available oxygen for NOx formation. At the same time, the oxygen injected at other locations in the furnace allows for the combustion process to be completed in the first chamber at lower temperatures which are less conducive to NOx formation. The scarcity of oxygen in the flame also helps prevent the oxidation of any fuel-bound nitrogen to NOx. The second driver in the rate of NOx formation revealed by the CFD results is that the volume of the high-temperature flame zone is greatly reduced. The smaller volume translates to less time for nitrogen to dissociate and potentially be oxidised to form NOx.
Fig. 4 demonstrates the effect of increasing oxygen flow rate on the NOx mass emission flow rate as the spent acid processing and pure acid production rates increase. While this figure only shows the acid production rate, these are the same operating conditions shown in Fig. 2, where the spent acid processing rate reaches 130% of the baseline. The approved NOx target depicted in the figure represents the NOx mass emission rate that provides the site with a sufficient cushion to be able to operate long-term without approaching its regulatory limit. The test conditions are the same as those shown in Fig. 3 and illustrate the reduction in NOx mass emissions with increasing levels of direct furnace oxygen injection. The results of the testing proved that the SAR unit can operate long-term with moderate levels of oxygen injection and maintain elevated rates for spent acid processing and pure acid production without exceeding the existing NOx limit.
Once the test data was compiled and analysed, there were additional environmental benefits identified because of the increased amounts of oxygen injection. One of the most dramatic of these was the reduction in the amount of energy required to decompose a unit of spent acid as the oxygen flow rate increased. The improvement in the energy efficiency of the enhanced oxygen combustion is caused by the reduction in the amount of ambient nitrogen that accompanies the lower air flow rates. The nitrogen acts as a heat sink on the process, and removing it means that a larger fraction of the heat introduced to the process can go toward spent acid decomposition.
Fig. 5 demonstrates this trend and uses the term “carbon intensity” to represent the energy efficiency improvement with higher oxygen levels. These values were calculated by summing the different sources of heat introduced to the process and dividing by the mass of spent acid processed. This calculation included the reduced amount of heat contained in the preheated combustion air as the air flow rate decreases with increasing oxygen flow. At the higher oxygen injection rates, and as the spent acid processing rate increased by 30%, the carbon intensity (or heat per mass unit of spent acid) decreased by 23%.
In another emission-related observation from system operation, the plant noticed that at a given pure acid production rate, the stack emissions of SO2 decreased with increasing oxygen flow. In the SAR unit, the SO2 exits the furnace and is sent to a catalytic converter to be oxidised to SO3. The converter is highly efficient, but some fraction of the unoxidised SO2 ends up being emitted from the stack. It is believed that the decrease in the volumetric flow rate through the converter increases the residence time and produces a higher conversion efficiency. The plant has reported that its stack SO2 emissions have decreased by up to 30% at a fixed acid production rate when oxygen flow is increased. This feature bears further investigation in the future.
Summary and next steps
A plant desired to increase the capacity of its SAR unit to process spent acid and to make pure spent acid while maintaining its NOx emissions at or below its current levels. A concept was developed to displace some of the combustion air used in the process with pure oxygen to reduce the volumetric flow rate through the furnace at a given spent acid processing and pure acid production rate. The oxygen could either be used to enrich the combustion air or injected directly into the furnace. A process mass and energy balance simulation and a CFD model of the decomposition furnace were developed to determine the impact of introducing oxygen at different rates and locations and to predict the performance improvements and resulting NOx emission rates. Based on the results of the simulations, the team developed an oxygen supply and delivery system designed for the unit.
Testing of the system demonstrated that displacing some of the combustion air with pure oxygen allowed the furnace to process 30% more spent acid while increasing pure sulphuric acid production from 5% to 10%. Due to the ability to reduce the feed of other sulphur-containing feed streams to offset the higher spent acid rates, the economics of this solution were very attractive. The testing showed that oxygen enrichment of the combustion air would cause a significant increase in the NOx emission rate. However, by injecting oxygen directly into the furnace and separate from the burners, the mass emissions of NOx were found to decrease with increasing production rates. As the spent acid processing rate increased by 30% and the acid production increased by 5% to 10%, the NOx decreased by 10% to 15%. The data also indicated that the displacement of air by pure oxygen increased the efficiency of the process and the amount of heat input required to process a unit of spent acid decreased by 23%.
Additional activities are planned for the continued evaluation of this approach, the first of which is the continued operation of the current process at the elevated rate of oxygen injection to confirm that the performance can be maintained. The system has been in operation for over a year and has produced results that are consistent with those obtained during the initial demonstration testing. A plan is being developed to perform additional testing to better assess the impact of oxygen addition upstream of the catalytic converter to improve conversion efficiency and reduce stack SO2 emissions. It is also hoped that a second SAR unit can be identified to conduct analysis and testing of the oxygen addition to verify that similar performance improvements are achievable and possibly to identify additional benefits of the technology.
Reference