Fertilizer International 521 Jul-Aug 2024
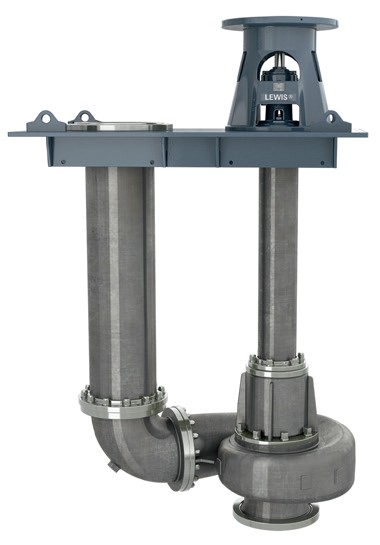
31 July 2024
Who’s who in pumping equipment
PROCESS EQUIPMENT
Who’s who in pumping equipment
We profile leading suppliers of tailor-made pumps to the phosphate, potash and sulphur industries.
WEIR
Weir – serving the fertilizer industry for over 130 years
Weir as developed an international reputation in the design and manufacture of pumps and valves for the sulphur, sulphuric acid and phosphoric acid industries.
History of Lewis® Pumps
Back in 1891, Charles S. Lewis founded Chas. S Lewis and Co., Inc., a family business that used customised alloys to modify OEM (original equipment manufacturer) pump lines for the beer pasteurisation and bottle cleaning industries.
By the turn of the century, in 1906, the company commenced manufacturing pumps in-house and later developed and manufactured its first sulphuric acid pump in 1914 – the start of a specialisation which has continued to the present day. Expertise and experience in sulphuric acid equipment developed over time and, in 1975, the company manufactured its first sulphuric acid valve.
Lewis ® sulphuric acid pumps and valves are used widely in the fertilizer industry, as sulphuric acid is consumed in the manufacture of many fertilizers that are produced today. Because fertilizer producers require operationally reliable sulphuric acid plants with heavy duty equipment installed, they naturally turn to Lewis ® pumps and valves.
As the 20th century drew to a close, the company became part of the Weir Group in 1994. The subsequent implementation of Weir’s well-established manufacturing excellence programmes at Lewis has delivered even greater levels of quality and high performance.
In 2012, the first Lewis ® molten salt pump was manufactured. These highly engineered centrifugal pumps are integral to molten salt circulation systems used in the solar power industry.
“We have developed a full range of pumps engineered for the unique requirements of molten salt. With over 100 years of experience focused on high density and high temperature, we have been able to develop a pump which has a superior feature set to provide high reliability and low operating costs,” says Bob Elliott, managing director of Weir’s North American operations.
Today, with more than 130 years’ experience behind it, Weir still manufactures its trademark wide range of Lewis ® pumps and valves – and has made significant investments in developing and enhancing its product line to better serve the industries in which it operates.
Strong customer focus
With customers in more than 100 countries, careful manufacturing planning is the key focus for satisfying customers in Weir’s view. This includes identifying the most requested spare parts and ensuring stock is constantly replenished for these needed items.
Maintaining stock levels is an in-depth project that involve collating data on spare parts usage – to truly understand customer requirements – and actively stocking items that will meet customer expectations during emergency situations. To successfully deliver on these guarantees, Weir has adopted a LEAN manufacturing strategy that shares global best practices and training between all Weir factories.
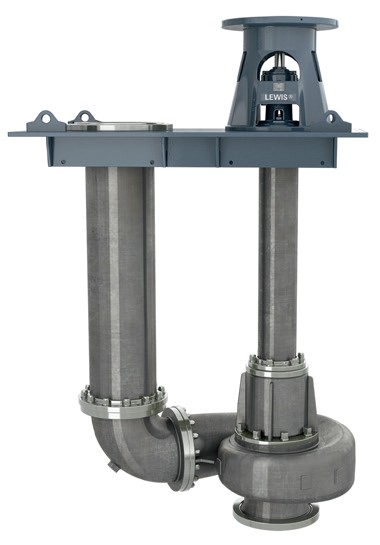
The company’s most recent improvement efforts include moving 92 percent of all factory equipment into product cells. This links-up the most requested spare parts with new replenishment techniques, creating close bonds with key suppliers and reducing the overall lead-time to target and strengthen spares availability.
Investment
Weir recently invested in the modification of its test stand area for axial flow pump testing. This enables engineers to test all pumps extensively, under real-life working conditions, before they leave the facility.
In addition to the 42,000 square feet of manufacturing and office space, the company has opened a new 57,000 square feet distribution centre that allows Weir to ship products to customers around the world with ease.
“We have streamlined our process to allow all departments to review the orders on a daily basis. This allows all departments to ask questions at the time the orders are processed, improving the flow throughout our system,” says Elliot.
He concludes: “Throughout the last 130 years, we have remained dedicated to the market and the customers we serve and this can be witnessed through the evolution of our Lewis pumps and valves. Our product innovations and dedicated group of employees will not only provide better service to our valued customers but will enable us to continue to deliver solutions to our customers for another 130 years and beyond.”
SULZER
Sulzer – a world leader in pumping and agitation
Sulzer is a global leader in pumping and agitation equipment with a history dating back to 1834. Headquartered in Winterthur, Switzerland, the company operates from more than 180 production sites and service centres located in some 50 countries around the globe.
Rotating equipment, separation and mixing technologies
Sulzer’s Flow Equipment division offers dedicated rotating equipment for core fertilizer processes, while its Chemtech division supplies components and services for separation and mixing technologies. The company’s portfolio also extends to specific water treatment technologies via its affiliate Nordic Water.
Building on more than 180 years of experience with a wide array of chemical and fertilizer industry applications, Sulzer guarantees high-quality process equipment for an extensive range of applications:
• Phosphate rock beneficiation
• Production of all grades of phosphoric acid
• Manufacture of phosphate, potash, and compound fertilizers
• Production of molten sulphur and sulphuric acid
• Water handling in cogeneration and cooling water units
• Water intake, transport, and treatment including desalination
• Wastewater treatment.
Sulzer’s position as the leading pump supplier in the industry derives from decades of continuous product development with industry-leading fertilizer companies, as well as from strategic acquisitions and industry expansions. Sulzer acquired Ensival-Moret in 2017, for example, and continues to develop their renowned range of pumps to complete Sulzer’s product offering.
Currently, Sulzer offers a comprehensive portfolio of reliable high performance pumps:
• Vertical and horizontal axial flow pumps (CAHR, CAHR-V)
• Slurry and heavy slurry pumps (AHL-STAR WPP, PLR, EMW)
• Process overhung pumps (SNS, AHL-STAR A, CPE, EMTECH, PRE)
• Between bearing pumps (MBN, ZPP, SMD, MSD)
• Vertical pumps (SJT, SJD, JTS, VA, VM, VAS)
• Liquid ring vacuum pumps (VRN).
Besides pumps, Sulzer also designs agitators (Scaba and SALOMIX ™ ) for applications in molten sulphur, phosphate rock beneficiation, phosphoric acid, potash, and fertilizer production plants. Sulzer offers a complete range of impellers adapted to each application. These are designed to suit the required levels of agitation for clean or slightly contaminated liquids, slurries, high-viscosity fluids, or for gas dispersion.
The endurance of Sulzer’s equipment comes from its use of a broad range of construction materials, its decades of accumulated expertise when it comes to optimal pump selection, and the modular construction of its pumps and agitators. All of these factors contribute to significantly longer equipment lifespan and minimal downtime.
Sustainability, innovation and choice
The life cycle and sustainability of process equipment play a major role in Sulzer’s vision for the future. The company’s customer offering ensures the lowest possible energy consumption, while fulfilling application requirements, and includes: IoT-based digital monitoring solutions like Sulzer Sense; quick spare parts availability; own-brand, high-quality mechanical seals; and comprehensive on-site and off-site maintenance services.
Sulzer supports the development of new technologies and the scale-up of existing processes by designing tailor-made equipment and adapting existing products to new conditions. Two examples of tailor-made high-performing equipment are Sulzer’s cooler circulation pump used in phosphoric acid plants and its tower circulation pump used in sulphuric acid plants. For both of these applications, the required capacity has needed to increase constantly to meet customer requirements. Also, the ability to keep operating using one single pump – instead of two or more pumps – has significantly reduced capital and operational expenditures.
Sulzer extensive range provides customers with flexibility when selecting equipment, even when these pumps were originally designed for purposes outside the fertilizer industry. Some purification technologies used in the processing of phosphoric acid and potash, for example, require high-pressure pumps with quite small flows. Sulzer has been able to supply suitable high-pressure pumps for these applications in the required construction materials – thanks to its comprehensive range of equipment developed for the power and oil & gas industries.
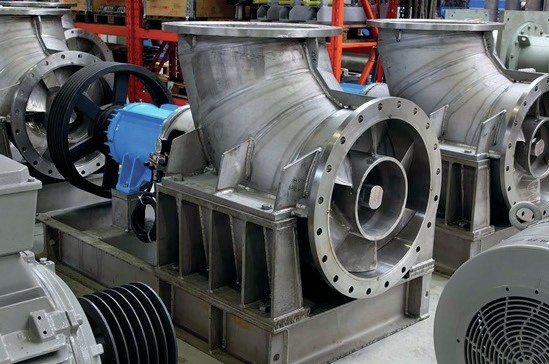
DÜCHTING PUMPEN
Specifically designed with corrosion and abrasion in mind
Privately owned German company Düchting Pumpen has more than 80 years of experience manufacturing advanced centrifugal pumps specifically designed for service in corrosive and abrasive conditions.
Delivering quality through experience
Düchting offers best-in-class reliability and performance in challenging environments that expose pumps to severe erosive-corrosive wear. These include industries such as fertilizer production, flue gas desulphurisation, seawater desalination, mining and mineral processing, sand and gravel dredging and chemical pigment manufacturing.
In keeping with its company motto (‘Quality through Experience’), Düchting’s sophisticated pump products are highly valued by its industrial customers. The company combines expertise in hydraulic design – using high-performance computational fluid dynamics (CFX) software – with strong capabilities in pump construction, machining, assembly, testing and commissioning.
An extensive portfolio
Düchting offers an extensive portfolio of single-stage and multi-stage centrifugal pumps. By providing customers with tailor-made, customised equipment as standard, the company aims to provide the best operational performance possible.
Minimising maintenance and energy consumption also ensures the lowest lifecycle costs. Partnership arrangements in strategic global locations have also strengthened the company’s reputation for efficiency, reliability, innovation and thorough after-sales service.
Düchting’s portfolio consists of:
• Single-stage hard metal slurry pumps
• Multi-stage dewatering and high-pressure booster pumps
• Non-metallic low-pressure slurry pumps – these combining diamond-like abrasion resistance with a lifetime anti-corrosion warranty.
Metallic pumps are offered in either super duplex stainless steel or high chrome iron alloys, depending on the application and individual requirements and parameters. For highly challenging fertilizer production conditions, Düchting offers the SICcast mineral cast pump series together with SIConit after-market coating refurbishment capabilities.
SICcast – a unique technology
SICcast is a unique proprietary technology designed more than 30 years ago to combat erosion-corrosion wear. The material consists of an engineered matrix of silicon carbide particles and epoxy resin binder that is mixed under vacuum and then heat-cured into high precision moulds at Düchting’s German production plant.
Once cured, SICcast’s finished hardness is close to that of diamond on Moh’s scale. SICcast is so hard that machine finishing with diamond-tipped tools is necessary to produce the wet end components for Düchting’s MC and MCC pump lines.
SICcast is specifically designed to combine complete corrosion resistance with diamond-like abrasion resistance. SICcast pumps are ideal in challenging slurry mediums that shorten service life and reduce the reliability of hard metal (duplex stainless steel or high chrome/ nickel alloys) slurry pumps that are more susceptible to erosive-corrosive wear. All wetted components in Düchting’s MC and MCC pump lines are completely constructed of SICcast. This design eliminates any contact between the slurry medium and metallic components during operation.
Aftermarket refurbishment of existing worn equipment is also possible through the company’s SIConit refurbishment process. This repair service uses a unique coating technology that combines a SICcast EP135 coating material with a cold curing chemical hardening agent. Once cured, SIConit can also be machine finished with diamond-tipped tools to completely revamp and repair existing worn components (see photo). This returns them to as-new condition with SICcast’s superior protection against corrosion and abrasion.
Düchting’s SICcast mineral cast slurry pumps and aftermarket SIConit refurbishment capabilities are widely used in both phosphate and potash fertilizer production. This is due to their ability to combine optimal performance with equipment longevity and reliability in highly corrosive and abrasive services. Applications include:
• Phosphoric acid
• Sulphuric acid
• Gypsum slurry
• Phosphate rock slurry
• Tailings slurry
• Silicate/sand slurry
• Brine and salt slurries.
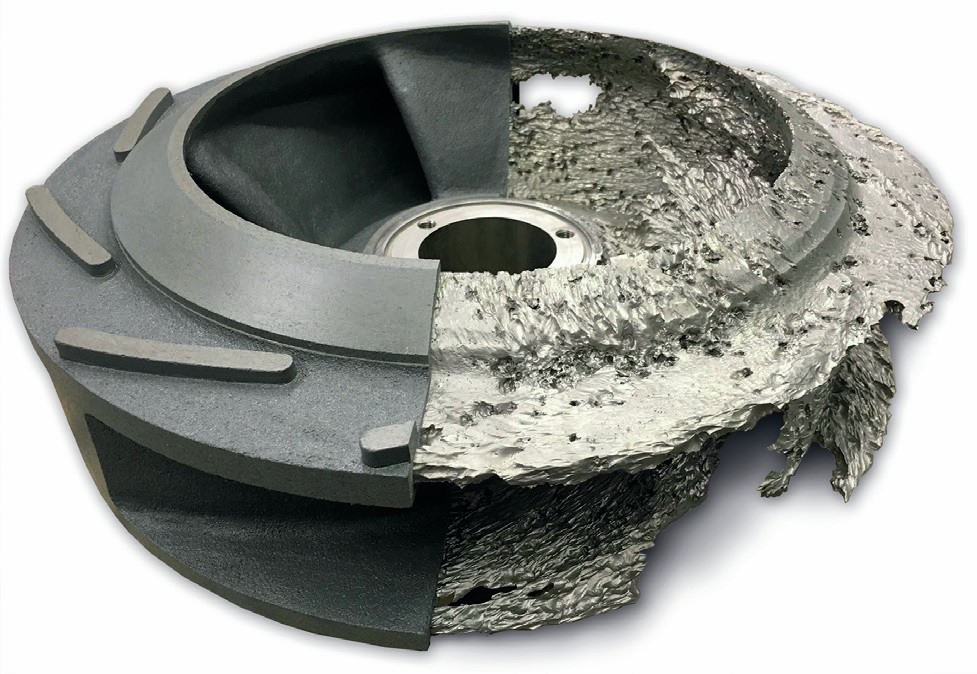
A wide range of fertilizer industry applications can also benefit from SIConit refurbishment. These include worn components from existing metallic slurry pump wet end parts, agitator mixer impellers, piping sections, reducers, collection basins, diverters, etc.
ITT INDUSTRIAL PROCESS
Durable equipment for overcoming challenges
Fertilizer manufacturing requires equal parts expertise and endurance. Harsh operating environments expose equipment to high levels of erosion and corrosion, meaning operators need durable equipment to overcome the built-in challenges.
For decades, operators have turned to ITT Inc for its iconic pumps that are renowned for durability and performance in transferring, dosing, and mixing chemical solutions. In fact, Goulds Pumps and Rheinhütte Pumpen are manufacturers of pumps for every stage of the fertilizer production process, from sulphuric acid production to mining and phosphoric acid plants to the final manufacture of fertilizers.
The full pump portfolio covers slurry, axial flow and chemical process pumps to ANSI and ISO standards, including sealless pumps. Goulds Pumps and Rheinhütte Pumpen specialize in high alloys for chemical pumps ranging from 316SS to zirconium and other special alloys, as requested, as well as a wide range of elastomeric, ceramic and plastic materials. The company’s non-metallic pumps offer distinct advantages when handling severely corrosive materials, while its magnetic drive pumps are designed for applications where leakage cannot be tolerated.
And while the pumps are essential to the fertilizer industry, ITT’s provides a comprehensive range of complementary products and services for producers at every stage of fertilizer production. ITT Engineered Valves offers valves that resist corrosion from harsh chemicals, while i-ALERT Solutions offer condition monitoring to identify potential issues before they lead to disruptive downtime, which can be extremely costly to repair. All products and services are backed by ITT’s comprehensive support network, featuring preventative maintenance programmes, spare parts management and field services.
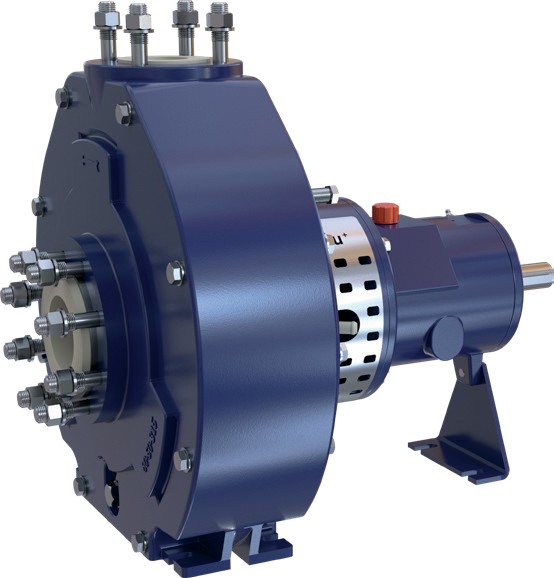
ITT’s extensive experience handling some of the world’s most hazardous and corrosive chemicals allows partners to get the most from their equipment and operations. When something does go astray, operators need a trusted resource who will work with them to identify problems – and then determine the best solutions that can be implemented quickly and efficiently. It’s not always the equipment either; sometimes the operation just needs a slight tweak.
RCNKu chemical pump in plastic
RCNKu pumps have a horizontal, single-stage, end-suction, top-discharge centrifugal design, standardised to EN 22858, ISO 2858 and ISO 5199. They are used for handling chemically aggressive and/or inflammable liquids within the wide field of chemical processing and environmental technology. The closed impeller of RCNKu units makes them suitable for clean liquids, with options offered for either fluids with a small solids content (RCKu) or for larger solids, the RCFKu version. This versatility makes it a perfect choice for certain fertilizer industry applications.
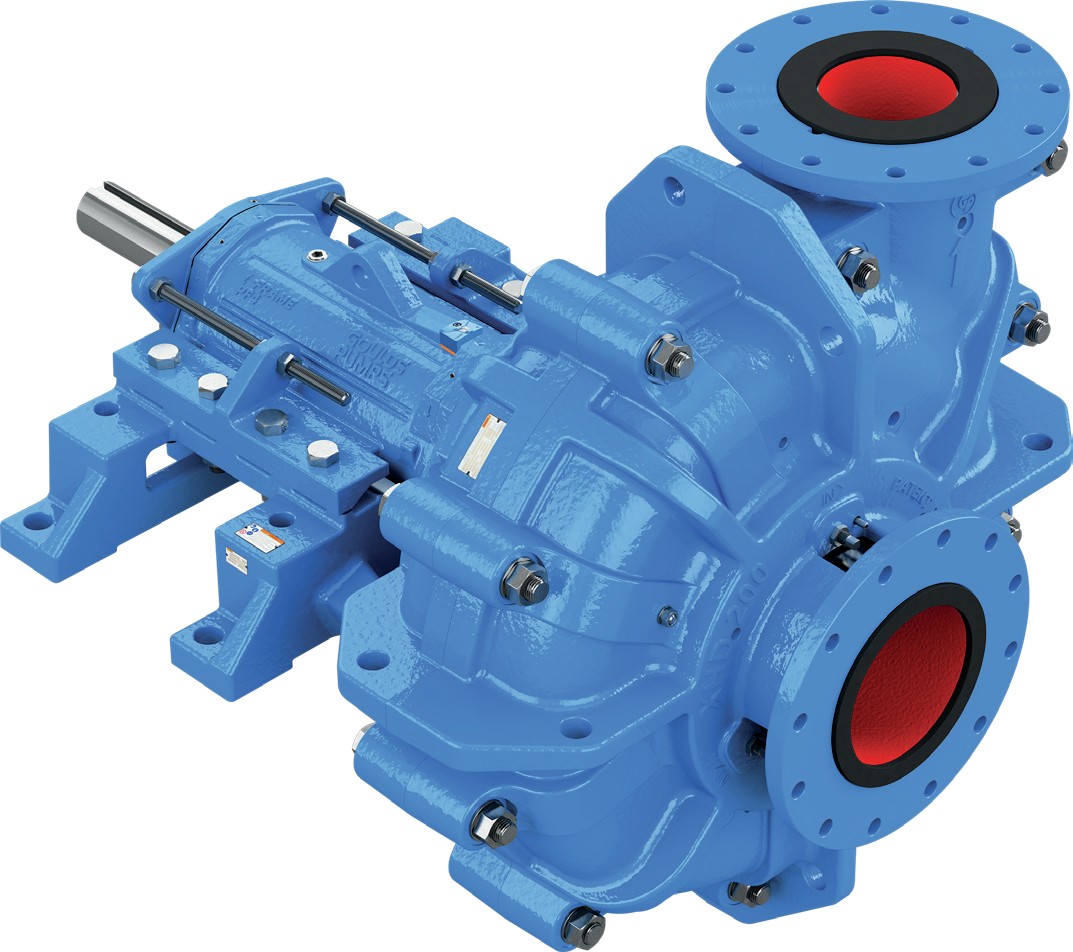
XHD Heavy Duty Slurry Pumps
The XHD pump range provides the next generation in severe-duty slurry pumping by incorporating the latest technology, including computational fluid dynamics (CFD) analysis. Built-in features offer numerous benefits that help customers address rising operating costs and other challenges. The range, with its large-diameter, high efficiency impellers, thicker liners, and interchangeable metal and rubber wear parts, is designed for use within heavy-duty slurry applications. These features were developed to address customer feedback on ‘pain points’ from comprehensive surveys. Other notable features include the ease of impeller removal. This is removed via an impeller-release collar in a position where parts would otherwise seize up in rough operating conditions. The impeller has a patented machined thread that provides the user with a reliable method for realignment during assembly to the shaft.