Nitrogen+Syngas 391 Sep-Oct 2024
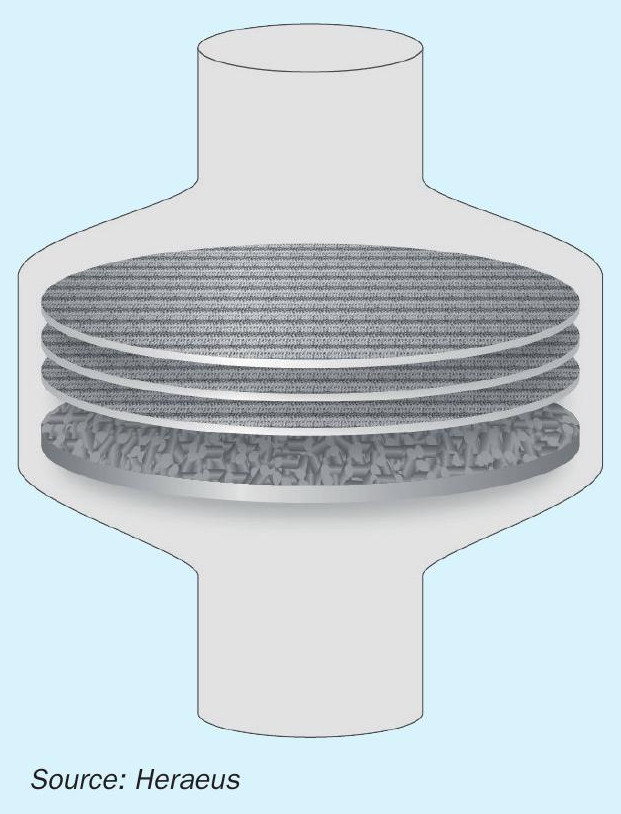
30 September 2024
Catalyst systems for N2O abatement
NITRIC ACID
Catalyst systems for N2O abatement
Innovative catalyst systems from Heraeus and Łukasiewicz Research Network – New Chemical Syntheses Institute contribute to reach climate goals by reducing N2O emissions during nitric acid production. Dr Uwe Jantsch and Jens Hesse of Heraeus Precious Metals report on the process performance results achieved for N2O reduction in nitric acid production using FTC gauze systems and iron oxide based secondary catalysts.
During the production of nitric acid, nitrous oxide gases are released into the atmosphere as a byproduct. This greenhouse gas has roughly 273 times the global warming potential of carbon dioxide and is a major contributor to global warming.
Heraeus Precious Metals is pushing for sustainable industry solutions and offers the possibility to reduce N2O emissions within the catalytic gauze system using its well-known FTC technology. This primary N2O abatement is fully customisable, making it suitable for full as well as partial loads. The catalytic gauze system in combination with secondary or tertiary solutions helps nitric acid producers to meet the latest abatement requirements in the demanding N2O emission markets. Besides catalytic gauze systems, Heraeus offers, together with its partner Łukasiewicz Research Network – New Chemical Syntheses Institute, secondary catalyst systems for further N2O emission reduction. Highly efficient catalysts from Heraeus and Łukasiewicz Research Network – New Chemical Syntheses Institute can significantly reduce nitrous oxide emissions up to 95%. Heraeus and Łukasiewicz Research Network – New Chemical Syntheses Institute as partners are installing this reduction technology in existing nitric acid plants around the world, supporting global climate goals and helping with the fight against global warming.
High performance catalysts
Heraeus and Łukasiewicz Research Network – New Chemical Syntheses Institute (formerly INS (Instytut Nawozów Sztucznych)) have a long-time partnership for the supply of high performance catalysts for nitrous oxide abatement in nitric acid production.
Heraeus, a leading producer of precious metal catalyst gauze systems worldwide for more than 100 years, is well-known for its gauze catalyst systems and services and has a global team and production facilities in Germany, USA, China and India.
INS, a well-known state centre in Poland since 1935, became part of Łukasiewicz Research Network in 2019 with 32 research institutes located in 12 cities across Poland. It is the third largest research network in Europe.
The innovative catalyst systems from both partners contribute to reach climate goals by reducing N2O emissions during nitric acid production.
Climate change status 2024
All of us recognise the signs of climate change on the planet: Human activities have raised the atmosphere’s carbon dioxide content by 50% in less than 200 years. Satellite data show that ice sheets are losing mass. Summer Arctic sea ice is shrinking by 12.2% per decade due to warmer temperatures and the average sea level has risen by nearly 4 inches since January 1993 (see Fig. 1).
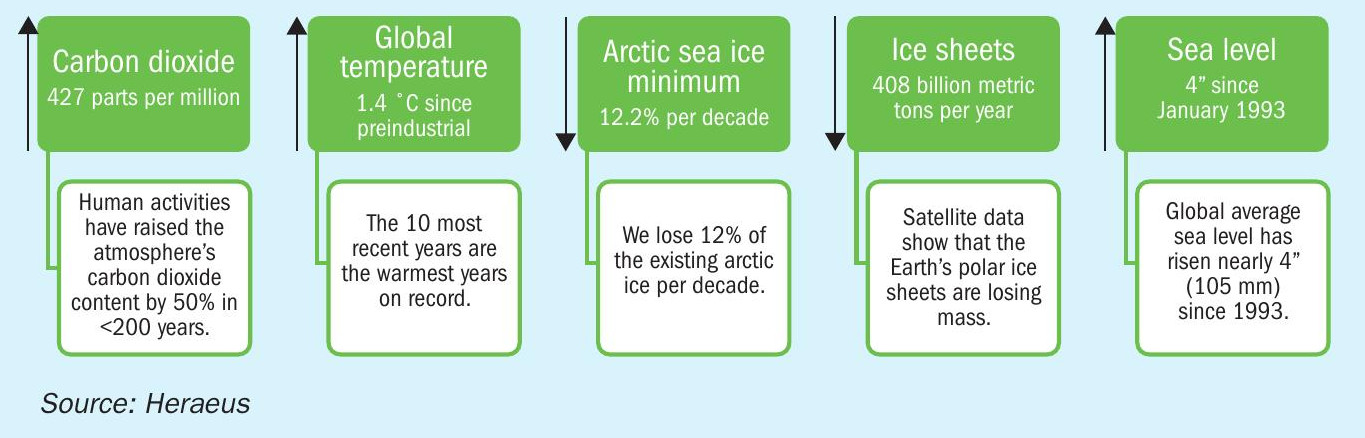
In addition, the earth’s average global temperature has risen by 1.4 degrees since the 1880s. This is the research result of several scientific organisations including NASA. The past ten years have also been the ten warmest years since records began2 .
N2O emission reduction in industrial nitric acid plants with limited space for secondary catalyst
During the oxidation of ammonia in the nitric acid production process, the greenhouse gas N2O is formed in a side reaction. It passes the nitric acid plant without any further reaction and is finally released to the atmosphere.
Main reaction:
2NH3 + 2.5O2 → 2NO + 3H2O
Undesired side reaction:
4NH3 + 4O2 → 2N2O + 6H2O
Once N2O has been released into the atmosphere, N2O remains there for a very long time and it contributes significantly to the global warming effect. In comparison to CO2 its global warming potential is higher by a factor of 273 according to the sixth IPPC report. Therefore, it is very important to use advanced catalyst technologies to reduce N2O emission in nitric acid plants.
Typically, the ammonia converters of existing nitric acid plants have been engineered without taking into account the space needed for secondary catalysts for N2O emission reduction. To make use of the high temperature generated during the NH3 conversion reaction, the secondary catalyst should be installed directly under the catalytic gauze system. However, the space between the catalytic gauze system and the cooling tubes in the reactor, as shown in Fig. 2, is quite limited and the design of the supporting structure does not meet the requirements of a secondary catalyst application. Before installation of secondary catalyst, a careful inspection and in most cases a redesign of the support structure is necessary.
Heraeus and Łukasiewicz Research Network – New Chemical Syntheses Institute have been looking for ways to reduce the emission of N2O since many years. In their role as partners Heraeus provides N2O abatement with catalytic gauze systems and Łukasiewicz Research Network – New Chemical Syntheses Institute produces secondary catalyst for N2O abatement – PKR-2 (iron oxide based). For international markets, Heraeus acts as an exclusive distribution partner of secondary catalyst from Łukasiewicz Research Network – New Chemical Syntheses Institute. Both catalysts are coordinated to achieve the highest N2O reduction rate.
Heraeus has been developing special FTC flex gauze systems which generate less N2O compared to state-of-the-art gauze systems, without sacrificing production capacity or NH3 conversion efficiency. The latest results from industrial tests show that with FTC flex gauze systems, the N2O emission can be reduced up to 70% compared to state-of-the-art gauze systems. Fig. 3 shows the low N2O emission of a low-pressure plant over the operating time. This can be achieved by using special FTC flex gauze systems with different PGM composition from top to bottom of the entire gauze system. This technology was patented and is available exclusively from Heraeus.
It is well known that catalyst gauzes lose precious metal weight by high temperature evaporation during operation of the nitric acid plants. Typically, this issue leads to changes of the chemical composition of the gauzes and an increase of N2O emission over time. Heraeus has managed to significantly reduce the N2O emissions over the entire production period. Nevertheless, the reduction of N2O emission with catalytic gauze systems is not sufficient to achieve the environment targets in future. In higher loaded medium or in high pressure plants, it is more difficult to achieve low N2O emissions with catalytic gauze systems only. Therefore, it is important to use additional N2O abatement technologies.
The installation of secondary catalysts directly under the FTC flex gauze system reduces N2O emissions further to a very low N2O emission level. The volume of secondary catalyst which can be installed under the FTC gauze system depends strongly on reactor type and design and condition of the mechanical supporting structure. Using the Fe2O3/Al2O3catalyst, the shape and the size of the secondary catalyst particles can be optimised and adjusted to the operating conditions of each plant. Depending on the available space under the catalytic gauze system and on the hydrodynamic gas flow conditions, the appropriate geometry of secondary catalyst will be recommended.
The graphs in Figs. 4 to 6 show examples of N2O emission reduction of medium pressure plants over the entire gauze campaigns, using Heraeus FTC flex catalyst gauze systems and INS secondary catalysts. In these cases, the extrudate type catalyst PKR-2 has been used in combination with high emission reduction FTC flex gauze systems.
Typically, a gauze campaign in a medium pressure plant lasts up to one year. Due to evaporation of platinum on the upper gauzes and absorption of Pt on lower gauzes the composition of the gauze layers changes with time. Additionally, the impurities carried into the reactor with the mixed gas partly deactivate the catalyst gauze surface over time. It results in a degradation of the catalytic activity and consequently in a slight decrease of NO conversion efficiency and hence in increasing N2O emissions. Fig. 4 shows the graphs of the N2 O emission, and the production efficiency results in a medium pressure plant with a long campaign length of around one year. The catalytic gauze system is the newly developed FTC flex gauze system with low N2O emission.
In Fig. 4 the N2O emission during the campaign was on average around 50 ppmv with a high and stable production efficiency during the entire production period. At the end of the campaign the N2O emission increases because of the deactivation effects of the gauze catalyst described above.
Fig. 5 shows the N2O emission and the production efficiency in the same plant after improvement of the process condition inside the burner. This resulted in some improvement of the production efficiency compared to the previous gauze campaign (Fig. 4) and the N2O emissions were kept in the same low range without changing the secondary catalyst. This was the result of the close cooperation between the customer and the supplier of the catalysts.
Fig. 6 shows the N2O emission of another medium pressure plant with a burner pressure of more than 5 bara. In this example the low N2O emission results were achieved by a well-adjusted combination of FTC gauze catalyst together with an iron oxide based secondary catalyst and a well-designed supporting structure. The campaign duration here is around six months. In this case the average N2O emission is below 40 ppmv.
Conclusion
Successful process performance results were achieved for N2O reduction in nitric acid production using FTC gauze systems and iron oxide based secondary catalysts. Innovative catalyst systems from Heraeus and Łukasiewicz Research Network – New Chemical Syntheses Institute have demonstrated their ability to efficiently reduce N2O emissions of nitric acid plants and support the nitric acid industry to achieve the environmental requirements.
References