Nitrogen+Syngas 391 Sep-Oct 2024
30 September 2024
Double temperature scrubbing for cleaner exhaust air
FERTILIZER FINISHING TECHNOLOGY
Double temperature scrubbing for cleaner exhaust air
Casale’s fluid bed granulation tail gas treatment for nitrogen-based fertilizer employs double temperature scrubbing technology, which handles the granulator exhaust air separately from the cooler exhaust air. The technology can combine dust removal with ammonia abatement in the same installation to meet strict tail gas limitations such as 10 mg/Nm3 for dust and 10 mg/Nm3 for ammonia. Ken Monstrey of Casale explains the key features of the Casale scrubbing technology.
The Casale fluidised bed granulation finishing technology for nitrogen-based fertilizer was originally developed by Green Granulation Technology (GGT). This fluid bed granulation was coupled with the in-house developed “double temperature” scrubbing process to remove the dust from the airstream and guarantee cleaned tail gas emitted to the atmosphere. Casale fully acquired GGT in 2022 as a company as well as the full IP portfolio and references in the market.
Typically, a fluidised bed granulation process uses considerable airstreams through the system in order to realise adequate cooling of the fluidised bed layer and provide the much needed movement of particles inside the bed. The cooling is required for e.g, urea-based processes in which the heat of crystallisation of the liquid urea feed must be removed from the granulator in order to keep the bed temperature within acceptable limits. The movement in the bed is vital for the process to produce prime quality product and ensure efficient and homogenous product build-up. Since there are no moving/motorised parts in the granulator, the fluidisation air together with the atomisation air of the liquid sprayers, are the driving forces to realise the movement in the bed. Without proper movement, the liquid nozzles do not receive enough fresh seeds to spray on and the spray zones would be overloaded leading to low water evaporation and a final product with high moisture content.
In most cases, the granulator is followed by at least one fluidised bed cooler in order to cool down the product before further handling and finally sending it to storage or bagging. The air going through the fluid bed cooler(s) also entrains some dust released from the friction between the particles.
The resulting airflows, for the granulator this is the sum of fluidisation air and atomisation air and for the cooler(s) this is all of the cooling air, have to be cleaned before they can be vented to the atmosphere. For this purpose, Casale makes use of the patented “double temperature” scrubbing technology, using horizontal scrubbers with vertically installed droplet separation stages.
Double temperature scrubbing
In the double temperature scrubbing technology, the granulator exhaust air is handled separately from the cooler exhaust air. There are two individual scrubbers (which can be combined in one vessel for the smallest plant capacities), one granulator scrubber and one cooler scrubber, that feature specific treatment of the air according to the nature of the pollutants.
The double temperature technology can be applied in various fields, with references in urea granulation, ammonium nitrate granulation, but also the more complex fertilizer production processes like urea with ammonium sulphate (UAS). The technology can combine traditional dust removal with ammonia abatement in the same installation. The number of stages installed in each scrubber is determined by the emission restrictions determined at the design stage. Very strict tail gas limitations such as 10 mg/Nm³ for dust and 10 mg/Nm³ for NH3 can be met by the Casale scrubbing technology.
The vast majority of the dust and NH3 originates in the granulator. The dust particle size can range from 0.5 mm particles to sub-micron particles. The coolers only account for minor traces of dust, which consists of larger and easy-to-catch dust particles and minor traces of NH3 . Therefore, the air treatment in the granulator scrubber is much more intensive than the treatment required in the cooler scrubber.
The granulator exhaust air starts its treatment in the inlet duct of the granulator scrubber where it is intensively mixed with aqueous scrubbing solution from the rich solution scrubber tank. This intensive wetting followed by the droplet separation in the first stage of the granulator scrubber will remove the majority of the dust, leaving only the smallest dust particles in the airstream.
Similar to the granulator exhaust air, the combined coolers exhaust air flows start their treatment in the inlet duct of the cooler scrubber where there is also an intensive mixing with aqueous scrubbing solution, but in this case, the liquid from the lean solution scrubber tank is used. This intensive wetting followed by the droplet separation in the first stage of the cooler scrubber is adequate to remove the dust from the coolers.
The essence of the “double temperature” lies in the introduction of lean scrubbing solution from the cooler scrubber tank to the second stage of the granulator scrubber. Fine atomisation of this lean and colder solution into the saturated, warmer airstream from the first stage of the granulator scrubber leads to an immediate condensation effect and the formation of micro-mist. The dust scrubbing of tail gas carrying a wide variety of dry dust particles is most effective when the dust particles can be transformed into droplets. The dust particle is dissolved in the droplet and is carried to the droplet separators where small droplets are transformed into bigger droplets by the coalescence effect inside the scrubber pads. When forming the micro-mist in the second stage of the granulator scrubber, the sudden condensation will transform the remaining dust particles, which can be as small as sub-micron level, into droplets. Since these micro-mist droplets are too small to be de-misted, the droplets must first grow in size by coagulating with other droplets in the airstream. This happens by the coalescence action inside the demister stages. By transforming the sub-micron dry dust particles into droplets that are large enough to be separated from the air stream, the dust comprising exhaust air from the system can be efficiently cleaned before venting.
The airstreams are moved through both scrubbers by the negative pressure from the exhaust air fan(s). To protect the fan(s) and to avoid any droplet carry-over to the stack, a dry final demister stage is installed in the scrubber outlet.
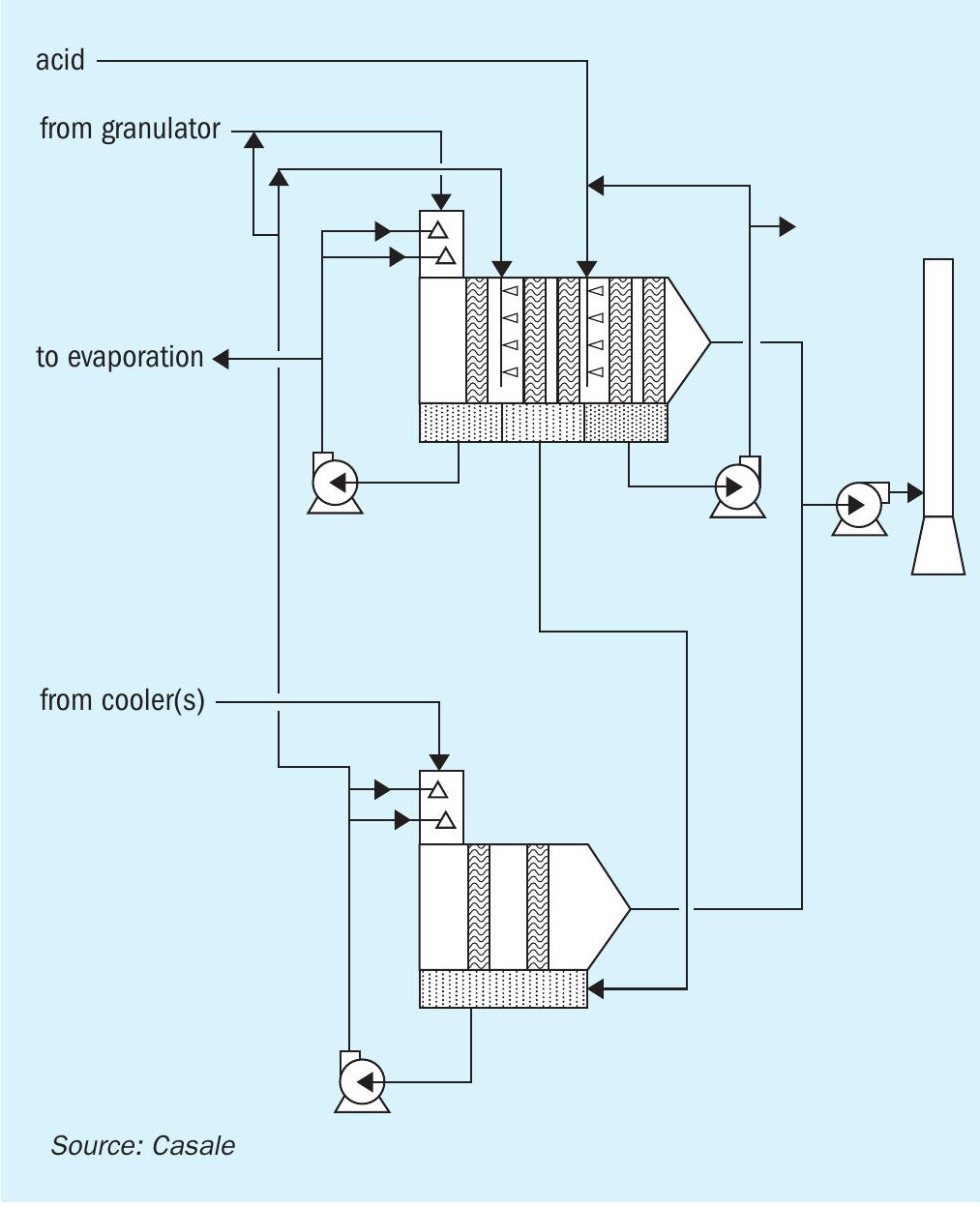
One of the main dust sources in the fluid bed granulation process is the recycled oversize product that was crushed by the roll crushers to serve as seed material for the build-up of granules. Part of this crushed material is so fine that it is carried out of the fluidised bed by the airstream and is entrained to the granulator scrubber. Another source of dust is the dust created by the friction between granules and the surficial solidified crystals that remain on the skin of the granules when these are dried in the non-sprayed zones of the fluidised bed layer. Both these dust sources produce dust particles that are relatively large in size and quite “easy” to catch. The more challenging very fine dust particles are formed by the sprayers. In the case of urea granulation, these are on the one hand fine urea solution droplets that crystallised before hitting a fluidised particle and on the other hand ammonium cyanate (NH4OCN), an isomer of urea, that is stripped out by the high temperature of the urea feed and the atomisation air surrounding the urea liquid nozzles. When stripped in the sprayer, the ammonium cyanate will split into two elements, NH3 gas and cyanuric acid gas. These two gaseous elements will recombine as a base acid reaction to ammonium cyanate, and form sub-micron dust particles. The ammonium cyanate is unstable and when further cooled down (in the scrubbers) the ammonium cyanate will transform into urea (NH4OCN → (NH2)2CO). Scrubbing out the sub-micron particles would require very fine filtering resulting in a very high pressure drop over the system. Thanks to the double temperature action in the Casale scrubbing technology, the sub-micron particles are transformed into relatively large droplets that can be recovered in the consecutive coalescence and demister stages.
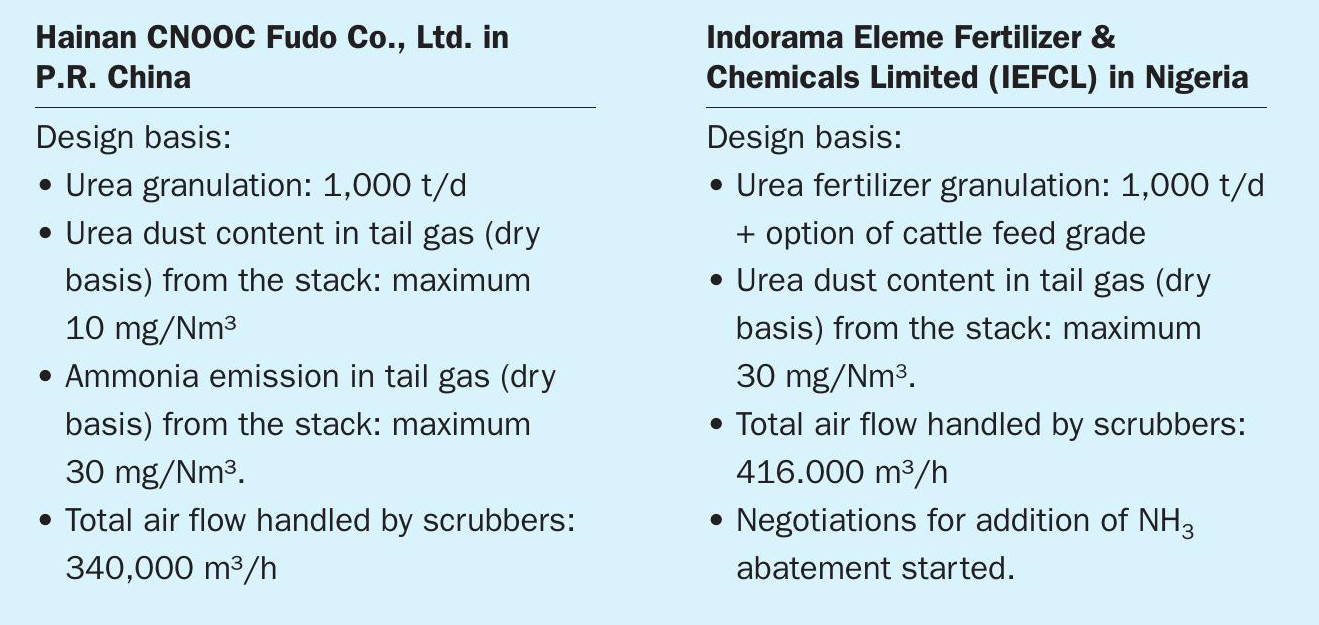
Also in other processes such as ammonium nitrate and UAS fluid bed granulation, sub-micron “dust” particles are formed and need to be removed by the double temperature action.
Removing NH3 from the tail gas
Apart from dust, the fluid bed granulation of nitrogen-based fertilizers also features an amount of free NH3 in the tail gas. The NH3 is present in the liquid feed to the granulator sprayer array and is stripped out by the action of the atomisation air surrounding the liquid nozzle. Depending on the feed to the granulator, urea, ammonium nitrate, urea + ammonium sulphate or others, the amount of free NH3 may differ. Residence time at elevated temperature will increase the amount of free NH3 and hence the feed concentration will largely determine the NH3 content. Most of that free NH3 is stripped out at the sprayers and will be entrained by the exhaust air.
Recovering the NH3 from the gas flow can be realised by adding an acidic abatement agent to the scrubbing liquid and binding the NH3. Sulphuric acid or nitric acid are the most common abatement agents. In ammonium nitrate, the choice for HNO3 is logical whilst the NH3 and HNO3 will react to form ammonium nitrate that is recycled to the evaporation section. In UAN, the choice for H2SO4 is logical whilst the NH3 and H2SO4 will react to form ammonium sulphate that can be recycled to the process. In urea production, there is the choice between H2SO4 and HNO3 , where the ammonium sulphate can be removed from the process to serve as a by-product or the recovered urea-ammonium nitrate solution can be sent to a liquid UAN production unit.
The NH3 abatement can be realised in a separate stage where the acid is added under pH control and where the recovered ammonium salt is collected in a closed loop with a dedicated tank. In case the ammonia salt is allowed to be recycled in the granulation process, there is no need for a separate tank. The same principle is valid when the scrubbing liquid can be sent to a UAN preparation unit.