Nitrogen+Syngas 391 Sep-Oct 2024
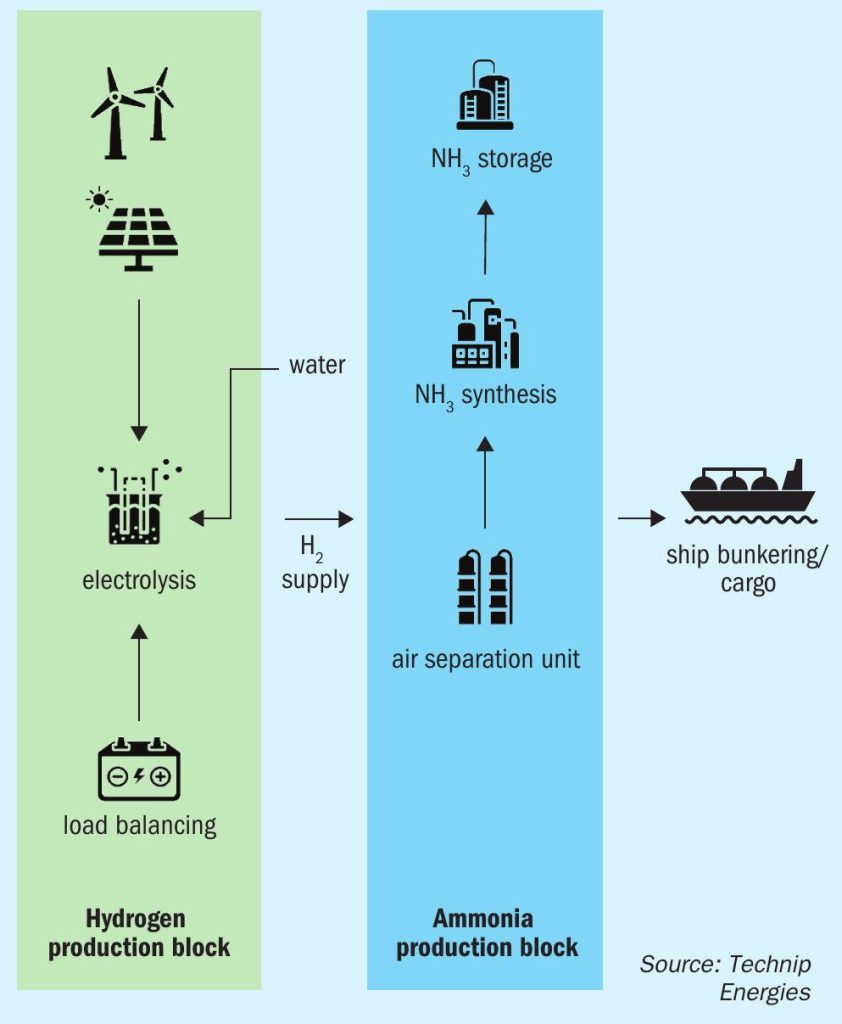
30 September 2024
The odyssey of green ammonia: optimising levelised cost
GREEN AMMONIA
The odyssey of green ammonia: optimising levelised cost
Green ammonia production facilities can be situated in remote areas with access to often fully off-grid renewable power supply. This article examines plant concepts and discusses the challenges and solutions for these plant architectures. Through a case study, an efficient and innovative methodology to compare options and optimise the sizing of the plant is presented. The methodology addresses the intermittency of the power production, the flexibility limits of the main process units, and the costs of investment and operation, using proprietary techno-economic dynamic simulation software, Odyssey.
Ammonia today and tomorrow
Ammonia, traditionally derived from fossil sources, has been used in various industries such as fertilizers and chemicals. Recently, the shift towards green ammonia – ammonia created using renewable energy through water electrolysis – signals a change in market trends. The future of the ammonia market will not only rely on its established applications but also on new potential uses, namely as a maritime fuel, power generation fuel, and as a carrier for hydrogen. Market experts anticipate that the ammonia industry could expand two to five times over the next 30 years, with most production plants likely transitioning to cleaner versions like green or blue ammonia, depending on regional contexts.
For decades, Technip Energies has led the construction of large-scale ammonia facilities across the globe. Its portfolio includes over 30 projects in both conventional and low carbon ammonia.
The current challenge of green hydrogen derivatives like ammonia is clear: bridging the gap between them and their conventional alternative. To meet this challenge, Technip Energies and John Cockerill, global market leaders in Hydrogen & derivatives EPC and OEM, joined forces in November 2023 to create Rely, a unique provider of competitive, integrated green hydrogen and power-to-X solutions providing end-to-end solutions to the complete value chain.
The green ammonia chain starts with renewable power generation, water electrolysis, ammonia synthesis, and can extend further to hydrogen regeneration if ammonia is used as a H2 carrier, as shown in Fig. 1.
Regardless of its final use, the first technology blocks are about producing renewable power, green hydrogen, and ammonia; this is the part of the chain where intermittency and flexibility matter most, and thus on which the present article focuses.
Bridging electrons to the ammonia molecule: process basics
Renewable power (REN), supplied either by the grid or off-grid, is the starting block of green ammonia production (Fig. 2). Most transported as high voltage alternating current (AC) through the power grid, a power conversion unit (PCU) is needed for voltage reduction and current conversion to direct current (DC), necessary for water electrolyser stacks. Within these electrolysers – whether alkaline water electrolysers (AWE), proton exchange membrane (PEM), or solid oxide electrolyser cells (SOEC) – water is split into hydrogen and oxygen in multiple cells comprising a stack, demanding roughly 4.5-5 kWh of power per Nm3 of hydrogen. This green hydrogen is then purified, dried, compressed, and directed to the ammonia synthesis loop. When pressurised electrolysers are used, intermediate hydrogen compression may be bypassed.
Green ammonia synthesis process consists of three steps: Feed gas compression, synthesis loop, and ammonia refrigeration. In feed gas compression, green hydrogen is mixed in stoichiometric proportions with nitrogen produced by cryogenic air separation (ASU) and the mix is compressed to enter the ammonia synthesis loop. The design of the green synthesis loop is very close to a conventional synthesis loop. Most licensors have references of standalone synthesis loops without the front-end syngas generation, using nitrogen and pipeline hydrogen, and develop solutions specific to the green ammonia industry, such as improving their dynamic process controls and material selection for better fatigue resistance.
The utility needs for a green ammonia facility are similar to those of a traditional plant, with key differences. The water treatment units need to be larger to supply purified water for electrolysis in addition to standard uses like cooling towers and steam generation. For cooling, a green ammonia plant might use cooling towers, air coolers, or hybrid systems, with the option for separate cooling circuits for hydrogen production and ammonia synthesis. The cooling requirements for hydrogen production tend to dominate, potentially doubling that of the rest of the plant. Compressed air and nitrogen are supplied from the ASU. The substantial electrical demands for producing green hydrogen mean that the power system is a significant portion of the plant’s capital expenses, shifting the project paradigm.
Flexibility of main building blocks
Green hydrogen and derivatives production technologies need flexibility to cope with variable renewable power sources. A green hydrogen plant can adjust its load relatively quickly. However, the ammonia synthesis process involves a high pressure and high temperature catalytic process as well as cryogenic parts, that need more stable operation. A conventional ammonia plant can only operate between 60-100% capacity with slow ramp rates. The cryogenic air separation unit has similar constraints.
How to cope with intermittency?
Numerous green ammonia initiatives consider off-grid, renewable powered ammonia production in remote locations. This article emphasises the variability of power supplies like solar or wind, as opposed to the stability of hydropower. Because weather can be unpredictable, these fluctuations occur seasonally, daily (as with solar), or at random times, thus affecting ammonia plant design and operations. These include rapid power changes, blackout periods, and frequent on-off cycles. From hydrogen creation to ammonia storage, plants should flexibly adapt to available power. While most electrolysis technologies such as pressurised alkaline or PEM can more easily adjust to the dynamics of power supply variability, ammonia synthesis is less adaptable. Ammonia production faces several challenges: typically steady-state plant operations with limited adaptability, equipment-specific operational constraints (such as turndown), and increased wear and fatigue due to instability. The goal is to manage these variations, maintain flexibility for fluctuating power supplies, and remain economically viable. Three primary targets must be achieved to succeed.
First target: Electrical grid stability
The plant should handle power outages and surpluses. Backup and essential power units can prevent black-outs, while batteries or other systems can store or sell excess power. Storing excess renewable energy can also maintain a more consistent green hydrogen output, and thus ammonia. Battery systems can also help with electrical load balancing.
Second target: Hydrogen production stability
The plant should limit and mitigate green hydrogen intermittency. Water electrolysers are flexible, but smoother operation extends their lifetime. The design capacity and number of balance-of-plant units, such as deoxidation, dehydration, and compression, should be carefully determined for hydrogen production stability.
Additionally, intermediate hydrogen storage buffers load variation, and provides a stable hydrogen feed to the ammonia synthesis loop. Hydrogen storage is pressurised, in pipelines, vessels, or buried pipes. The storage should allow continuous ammonia production, smoothen load fluctuation, and minimise stoppages. Nitrogen is also stored to buffer the ASU output, which is less flexible.
Third target: Ammonia production flexibility
A green ammonia plant can be designed to vary its output depending on the process and the renewable energy sources, and this is currently a strong trend in the industry.
The key parameters of an ideal flexible green ammonia plant are:
- Ramp-up/down rates: as fast as possible, up to 3%/min for some licensors;
- Number of start/stop operations: as many as possible during the year;
- Minimum turndown: as low as possible, 10% achievable by several licensors;
- Idle or stand-by mode: sustainable for a long time;
- Time required to start-up: as short as possible;
For higher flexibility and faster start-ups, electrically-driven compressors are often selected, using steam generated from process heat to power a steam turbine generator.
To ensure reliable and safe supply of all utilities, adequate storage capacity is crucial. Water treatment units, which are sensitive to load changes, may also need back-up power.
Rely has developed Clear100+, a standardised 100 MW green hydrogen plant solution optimally conceived to offer performant, affordable, safe and certain production at scale. Offering an optimal balance of plant design, it is suited for flexibility range from 15-100%, integrating John Cockerill’s proven pressurised alkaline electrolyser technology with high reactivity to load variations. The Clear100+ is designed for seamless integration with a downstream ammonia production unit, making it an ideal solution for projects connected to renewable electricity.
New type of plants, new challenges, new methods
Considering an off-grid green ammonia plant, powered only or mainly by renewable intermittent power sources, changes the way to size the plant at feasibility stage. Indeed, given an objective of annual ammonia production, the size of the plant (hydrogen and ammonia production) depends on its load factor which is a function of renewable installed capacity, of renewable power source load factor and of the plant’s operating philosophy. Various sizing combinations of renewable power sources, hydrogen plant and ammonia plant can lead to the same annual production, but for different costs.
For early-stage sizing optimisation at project inception, Rely proposes a versatile, dynamic, techno-economic simulation tool called Odyssey (Fig. 3). Developed by Seed Energy, a spin-off from CEA, it is now incorporated within Technip Energies as of June 2023.
Odyssey serves two main purposes:
- a high-level dynamic simulation tool, using process and technology data to simulate plant operations over its lifetime and calculate total power or product yield;
- a techno-economic simulator, utilising investment and operational cost data to estimate the plant’s total discounted cost over its lifespan.
Odyssey is especially adapted to assess evolution of the plant production considering an intermittent source of power (or product), and the corresponding levelised cost of product.
It performs parametric or optimisation studies simulating multiple design configurations and operating philosophies, comparing them and selecting the optimum sizing for the plant.
A case study using solar power
In this study, let’s consider a project aimed at generating green ammonia using only solar power in a remote location (Fig. 4). The plan is to install 1 GW of solar energy, with flexible ammonia production target. The main task will be to conduct techno-economic optimisation to determine the most cost-effective plant design and operation to minimise the cost per ton of ammonia. This includes determining the size of various components: The electrolysis and ammonia synthesis capacities, an intermediate hydrogen storage for when the electrolyser is not producing, and a battery energy storage system to keep essential systems running without sunlight. Here, hydrogen is produced near the solar farm, while ammonia synthesis occurs close to a port terminal. The two sites are connected by a pipeline serving also as hydrogen storage. While the ammonia site uses grid power, the electrolysis facility relies solely on solar or stored battery power.
The model is fed with technical data such as potential renewable power production from the site. Odyssey considers the daily and annual evolution of power production as well as the degradation and ageing occurring during the plant lifetime.
Fig. 5 presents an example of the potential power profile used as input of the analysis.
Technical performance data for the plant are also integrated in the model: electrolysers efficiency, utility systems power consumption, ammonia synthesis unit power consumption, as function of the load and of the size of the plant. Any degradation and ageing data available can also be simulated. The model is made as closely representative as possible of the behaviour of the plant for any size and any condition of operation. The model includes all flexibility data for the different units: start-up, turndown and ramp-up/down rates are required to correctly simulate the transient phases.
Different operating philosophies can be envisaged both for electrolysis and ammonia synthesis. The operating philosophy shall define how the electrolysers will react depending on the variation of renewable power. Typically for an off-grid condition, hydrogen production will be set to follow the variations of power production. Power requirement of the whole plant will also be minimised during the night to avoid the need for large battery energy storage. In some configurations, more advanced strategies can be proposed, and, for example, for hydrogen plants connected to a grid, operating philosophies related to the variation of electricity price can be envisaged and simulated. The ammonia synthesis unit is less flexible: Start and stop of this unit daily is not conceivable. Hydrogen storage is thus required to feed the ammonia plant when there is no hydrogen production. Still, different operating philosophies can be envisaged for this unit, with relative flexibility. In this article, two operating philosophies are compared:
- conventional continuous and stable ammonia production;
- flexible ammonia production depending on hydrogen availability.
More advanced operating strategies depending on forecast of power/hydrogen production could also be proposed depending on project specificities.
When an operating philosophy is defined for the plant, with a given size of electrolysers, hydrogen storage and ammonia synthesis unit, Odyssey can be used to quantify the evolution of power consumption, hydrogen production and ammonia production along the plant lifetime. Fig. 6 shows the dynamic variations of production rates over time.
Yet, to compare various configurations and operating philosophies, economic data are required in the analysis. The model includes preliminary investment and operational costs for each unit modelled in the facility. These costs are estimated depending on the unit size to allow more realistic assessment when comparing different plant sizes.
For each studied dataset (technical data, economic data and operating philosophy), an optimisation study is carried out with the tool. It involves simulating multiple configurations with different sizes of electrolysers, battery energy storage, hydrogen pipeline (used as hydrogen storage) and ammonia synthesis units. For each case, it assesses the total hydrogen production, total production of ammonia and total cost, over the plant lifetime. This analysis facilitates the calculation of the levelised cost of hydrogen (LCOH) and ammonia (LCOA) for each configuration.
Typically, the results are presented on a graph where each dot corresponds to one simulated configuration, showing the LCOA and the ammonia average production over the plant lifetime. The best configuration is found along the Pareto front combining minimum LCOA and maximum ammonia production.
For the first operating philosophy (Fig. 7), with constant ammonia production, the configuration showing the minimum LCOA also produces the maximum quantity of ammonia: 600 t/d, obtained with a 700MW electrolysis plant, a 600 t/d capacity ammonia plant, a 150 MWh battery energy storage and 32,000 m3 of hydrogen storage in a pipeline between the two sites.
For the second operating philosophy (Fig. 8), the ammonia production and its corresponding hydrogen consumption is allowed to decrease during the night, when there is no hydrogen production. A larger ammonia plant is required to produce the same quantity of ammonia, with a lower load factor. At the same time, it decreases the required pipeline storage volume and allows increasing the electrolyser size, producing more hydrogen and in the end more ammonia, with a reduced total cost.
The selected configuration from Fig. 8 results in the lowest LCOA, which is 8% less than the 1st operating philosophy.
Additionally, the average ammonia production is increased to 700 t/d, an increase of 17% compared to the first philosophy. Other configurations under this second operating philosophy could yield even higher ammonia outputs, albeit with a higher LCOA. If the project values the higher production of ammonia sufficiently to outweigh the increased costs, another configuration from the Pareto front might be preferrable.
Renewable power source: wind, solar or both?
Depending on the type of power source (wind, solar, or mix, with or without back-up from the grid) and its load factor, sizing of the electrolysers and ammonia synthesis unit can vary largely. The sizing indicated in this article cannot thus be extrapolated easily to other projects. The example in Fig. 9 shows that the optimisation of two different architectures, both off-grid green ammonia plants with two production sites linked with a hydrogen pipeline result in very different configurations, due to the nature of the power source (solar versus wind) and the selected operating philosophies.
Breaking down the LCOA
Finally, Fig. 10 presents examples of cost breakdown constituting the LCOA for green ammonia plants:
- The left diagram shows an off-grid facility: 35% of expenses from renewable energy and 38% from hydrogen production. The ammonia synthesis & terminal represent 27%. Economically, it’s justifiable to oversize the ammonia unit to lower overall LCOA.
- Conversely, the grid-connected plant on the right has a higher electricity cost. Here, electrolysers operate with higher load factor, decreasing the relative hydrogen production cost, while the ammonia section represents 30% of total costs.
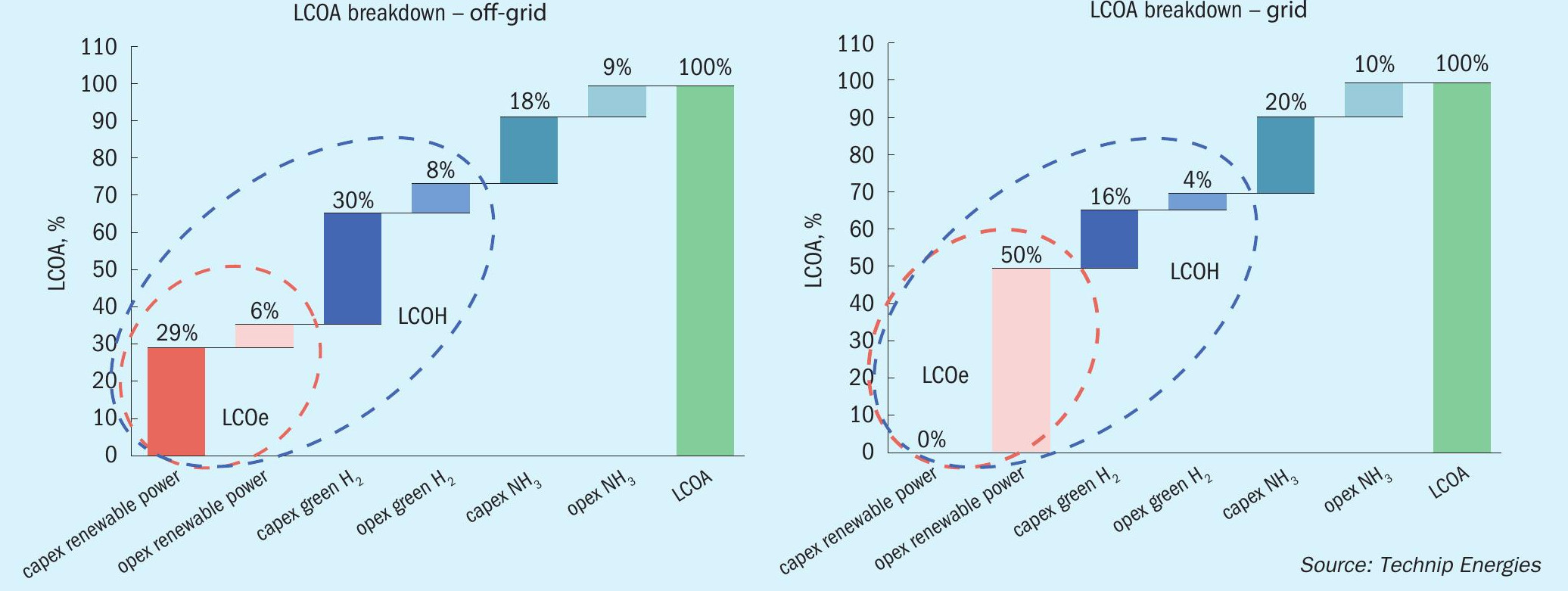
The main challenges for off-grid green ammonia production facilities are production variability and managing intermittency. New methods and tools are needed to optimise the design of green ammonia facilities, incorporating greater flexibility whilst remaining competitive. Rely’s versatile and fit-for-purpose method using Odyssey allows early framing and orientation of project architecture. Using power profiles, historical technical and economic data, with little input data needed, Odyssey techno-economic optimisation studies evaluate multiple plant configuration options and select optimal plant sizing from early project stages.
Thanks to the relative comparisons between options and preliminary LCOAs associated, Project can confidently select capacity and develop the design, to further refine and optimise the sizing. This endto-end approach is key to making the right choices and optimising the LCOA.
Green hydrogen production cost makes up the majority of the LCOA. With LCOH reduction as its key driver, Rely’s Clear100+ solution offers a standardised 100 MW green hydrogen plant. It offers unparalleled flexibility, thanks to a design specifically adapted to fluctuating renewable power sources. Easily integrated with a downstream ammonia unit, it makes an optimal end-to-end solution for off-grid green ammonia projects.