Fertilizer International 522 Sept-Oct 2024
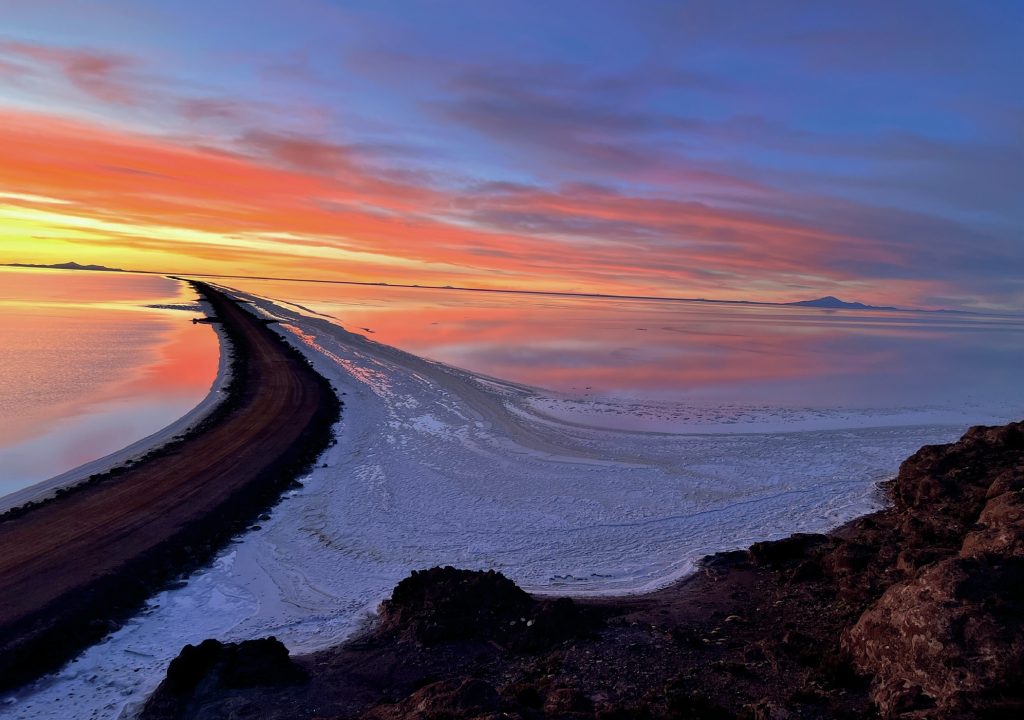
30 September 2024
Ulexandes – the leading Latin American boron producer
Ulexandes – the leading Latin American boron producer
We profile Ulexandes, a fast-expanding supplier of agricultural boron products with production plants in both Bolivia and Peru.
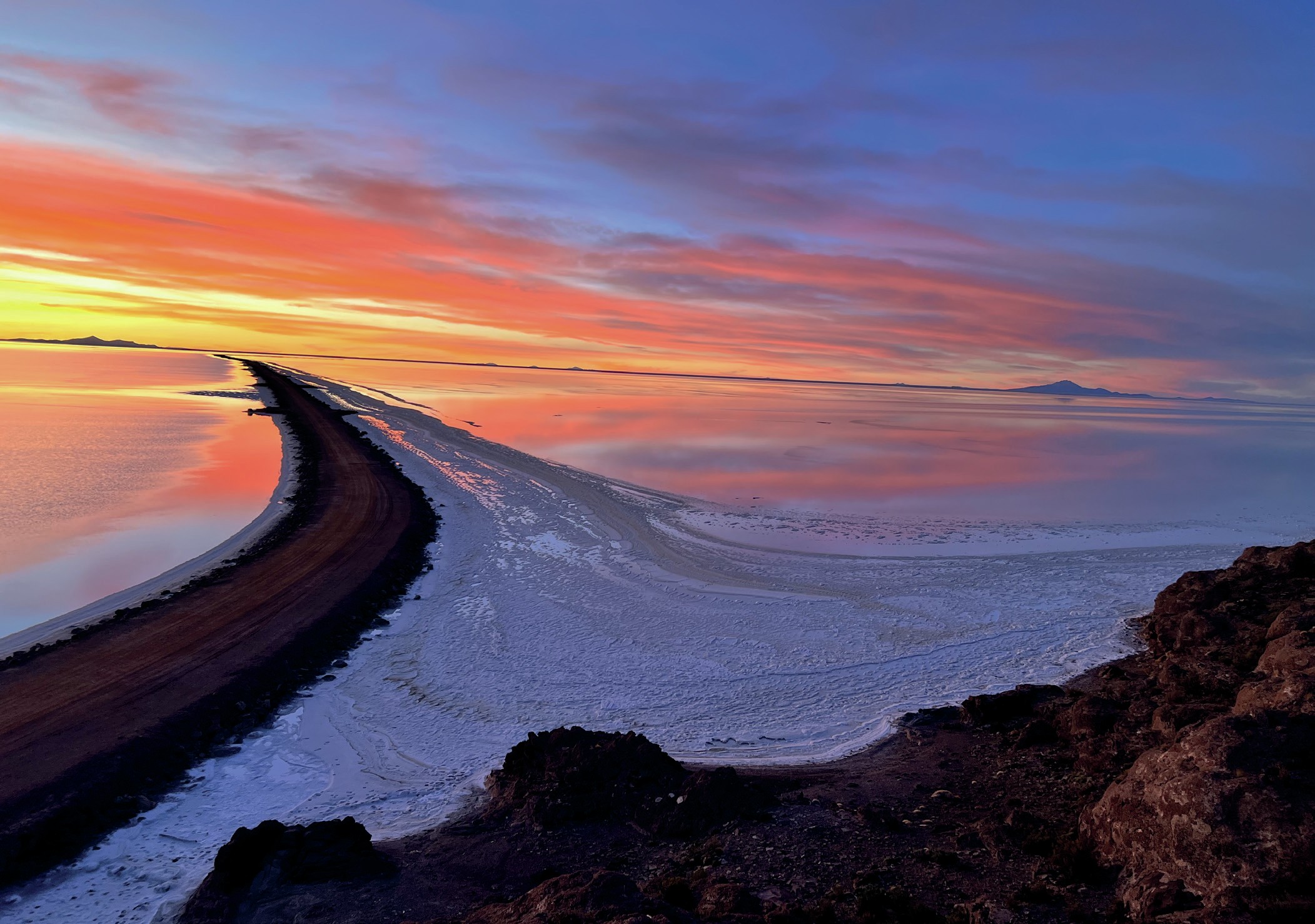
Introduction
Founded 25 years ago, Ulexandes is one of South America’s biggest boron suppliers and operates three production plants in Peru and Bolivia (see timeline). These source their mineral raw material, ulexite, from the Uyuni salt flat (Salar de Uyuni) in Bolivia and the Lake Salinas (Laguna Salinas) in Peru (Figure 1).
The company has invested in expanding its annual production capacity to 60,000 tonnes, with production growing at around 12 percent per annum on average – output having increased by 120 percent since 2013.
Product portfolio
Ulexandes offers ulexite products in both granular and powder form as part of its product portfolio. These are all produced using proprietary micronised granulation technology (MGT)
Granular products are suitable, firstly, for direct application to crops where applying granules may offer advantages and, secondly, for incorporating boron into blended fertilizers. They include:
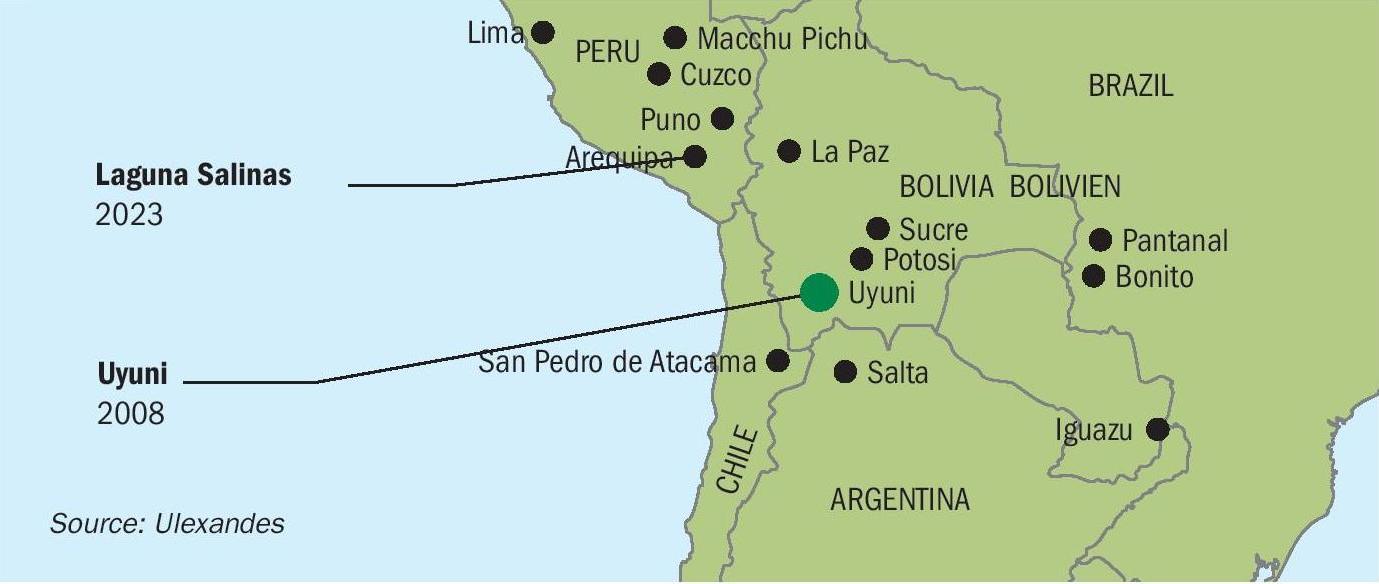
TIMELINE
1999 Ulexandes started in Antofagasta, Chile
2003 Began operating from Arequipa, Peru
2008 Opened a second production plant at El Alto, La Paz, Bolivia
2019 Started a production plant in Matarani, Peru
2023 New production plant under construction at Oruro, Bolivia
2024 Plans to open another production plant in Santa Cruz, Bolivia
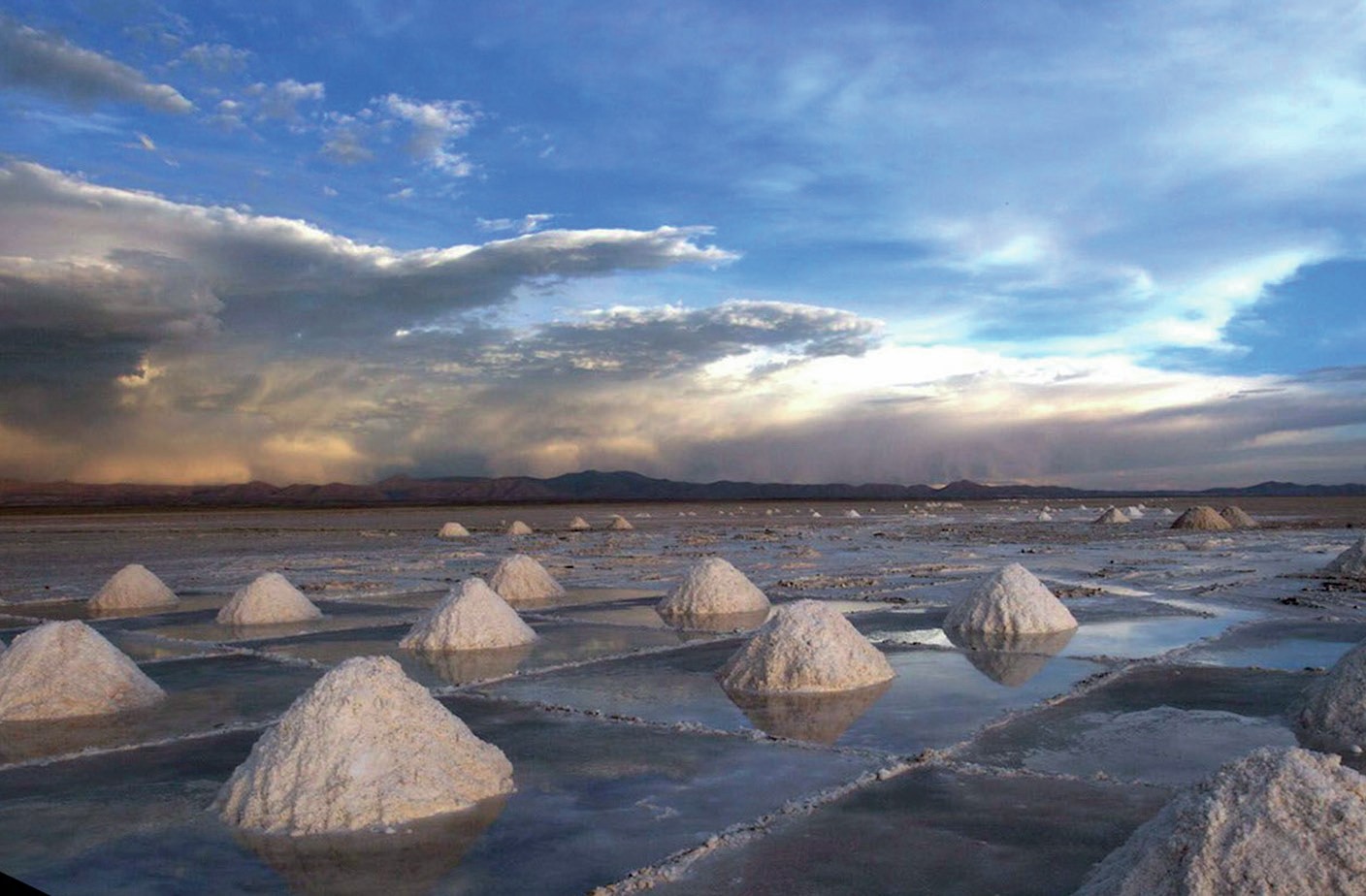
- Boron 10G: 10 percent boron content typical with formula NaCaB5 O9 .8H2 O
- Boron 15G: 15 percent boron content typical with formula NaCaB5 O9
The company’s powder products are suitable for: direct soil application to correct boron deficiencies in perennial plantation crops; the production of solid compound fertilizers; and the coating of compound or blended fertilizers. They include:
- Ulex 33: 10 percent boron content typical with formula NaCaB5 O9 .8H2 O
Ulex 46: 15 percent boron content typical with formula NaCaB5 O9
The following customised ulexite products are also available:
- Ulex 46 FINEST
- Ulex 40 FINE 200
- Ulex 40 FINE 325
- Boron 15 Microgranular
- Boron 15 Forestry
- Granular Copper Sulfate
Mineral extraction at Salar de Uyuni
Salar de Uyuni is the world’s largest salt flat, occupying an area of nearly 11,000 square kilometres in the Andes, southwest Bolivia.
The salt deposits at Uyuni are 120 metres deep and are a valuable source of lithium, boron, potassium, magnesium, calcium and sodium. Ulexite ore is extracted from 11 salt layers present at Uyuni with an individual thickness of 1-10 metres.
As a first step, due to the size of the salt flat, geological and technical studies are used to locate the most suitable mining areas for ulexite. After site selection, the mineral raw material is usually extracted at a depth of between 3-6 metres below ground level. Extraction of the ulexite ore is carried out using both heavy machinery and manual labour. This ensures that the raw material selected is largely free from impurities, prior to the on-site refining process.
After extraction, the raw material is refined in a washing and conditioning area to remove the remaining impurities, primarily sulphate and chloride, a process that takes around five days.
After refining is complete, the raw material is dried naturally over a 6-8 day period until its moisture content reaches the required levels for the production process. Chemical and physical quality control tests are used to verify that the raw material is suitable for onward transport by road and rail to the production plant.
Production process
Raw materials are processed to produce granulated and powdered ulexite containing boron at different specified concentrations. On arrival at the plant, laboratory analyses are carried out to correctly allocate the raw material during the production process.
Processing begins with grinding. Conveyors carry the raw material through a series of different mills for homogenisation and size reduction. Agglomeration and granulation equipment is then used to obtain a granular end-product with a particle size of 2-4 millimetres.
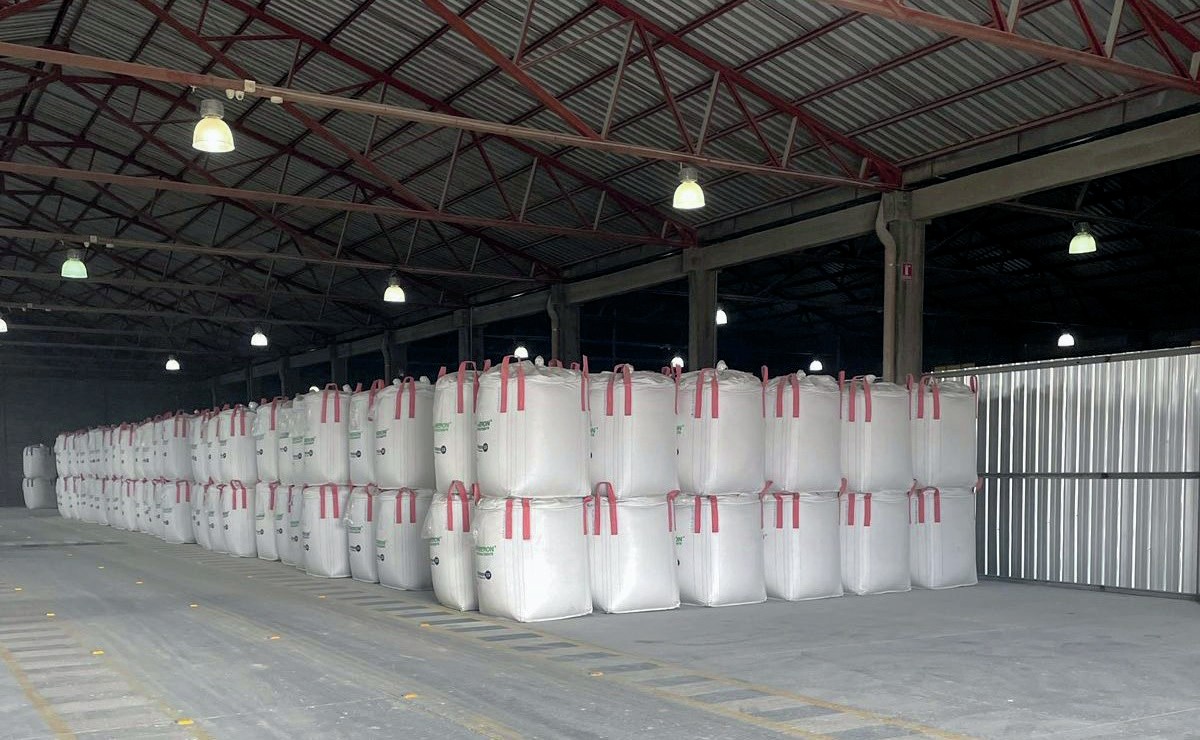
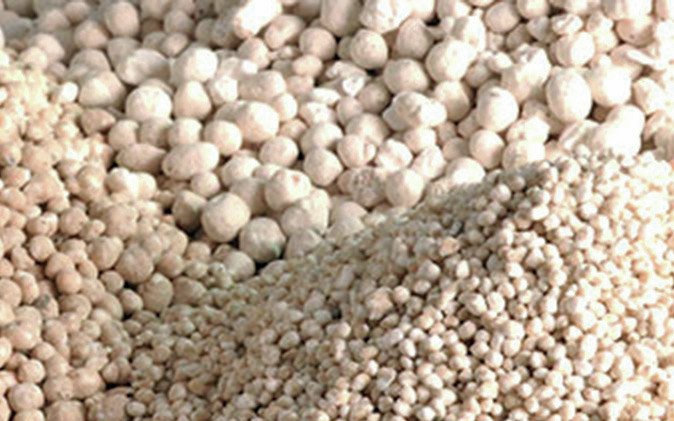
Granules are then dried to adjust their boron oxide concentration and ensure this meets customer requirements. In the final processing stage, granules undergo particle size classification for quality compliance.
Ulexandes maintains high stock levels of ulexite at its plants and warehouse. This guarantees a sufficient supply of raw materials for at least three years of continuous production. This ensures the availability of high quality finished products to customers and provides the company with the ability to promptly deliver these at all times.
Quality control
Ulexandes produces high-quality granulated and powdered ulexite products containing different concentrations of boron. The company is committed to delivering high quality products within a guaranteed technical specification. A well-equipped quality control laboratory with highly trained staff provides customers with the confidence that delivered products will always meet the highest standards. Quality controls checks are carried out at every stage from initial extraction to final packaging. Rigorous quality control during the production process includes checks for hardness and humidity every five minutes.