Nitrogen+Syngas 392 Nov-Dec 2024
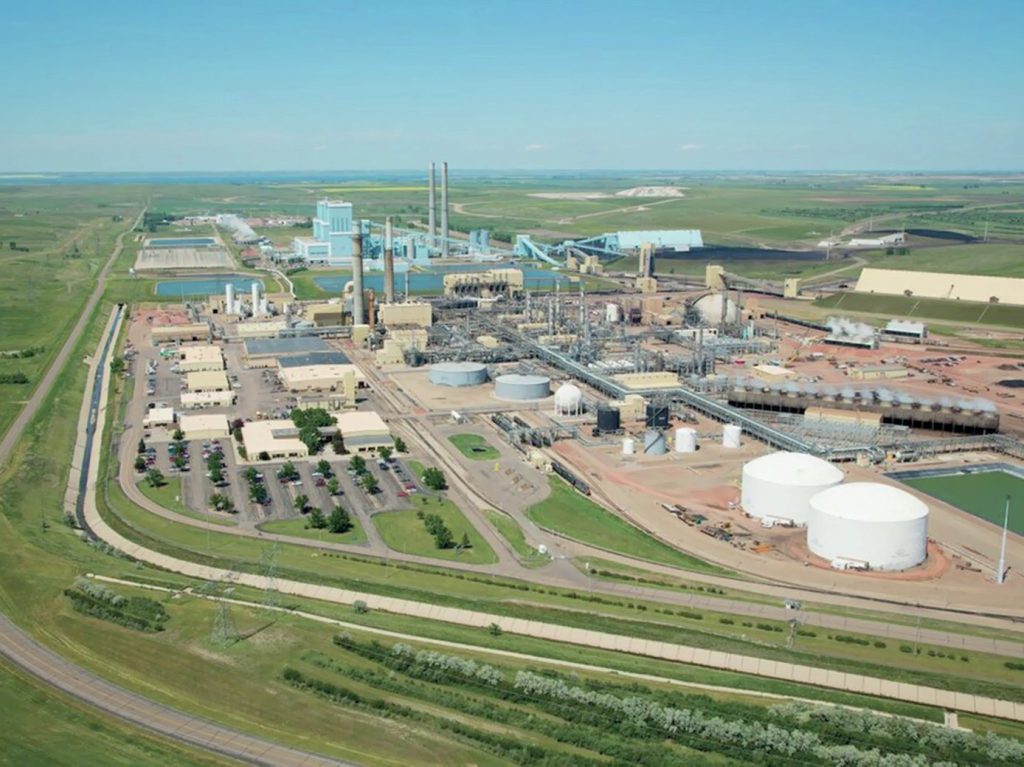
30 November 2024
Coal-based nitrogen capacity
FEEDSTOCK
Coal-based nitrogen capacity
In spite of increasing environmental concerns over the use of coal as a feedstock, it continues to provide around one quarter of the world’s ammonia. But in a world that is decarbonising, is there still a future for coal-based capacity?
But natural gas proved to be a cheaper and more tractable feedstock, requiring less pre-processing and swapping a cumbersome gasification reactor for a steam methane reformer (SMR). It allowed the scale-up of the ammonia process during the 1940s and 50s to plant sizes of 1,000 t/d and beyond, until by the 1970s it had become the dominant way of producing ammonia and downstream nitrogen products, a status that it still retains today.
Nevertheless, coal still had its adherents. In countries where natural gas was scarce and coal abundant, it could still be a much cheaper feedstock, particularly if used at large scale, in order to reduce the relative capital cost per tonne of expensive gasification sections. Figure 1 shows a resurgence of coal as a feedstock during the 1980s and 90s, as gas began to be used more and more in the power sector, driving natural gas prices upwards in North America, Europe and East and South Asia. This resurgence was however based in just a few countries where the economic conditions made coal attractive, particularly China, but also including Vietnam, India, South Africa and even the United States, which had pioneered gas-based production, but which also had major coal producing regions. Indian coal proved technically challenging for the gasifiers of the time, and in the US the sudden fall in gas prices caused by the fracking boom in the 2010s made life economically difficult for the coal-based plants there also, but China and Vietnam continue to operate coal-based capacity, and indeed China has become almost synonymous with coal-based ammonia production, with coal representing almost 80% of domestic ammonia production, and China representing 97% of all coal-based ammonia production worldwide.
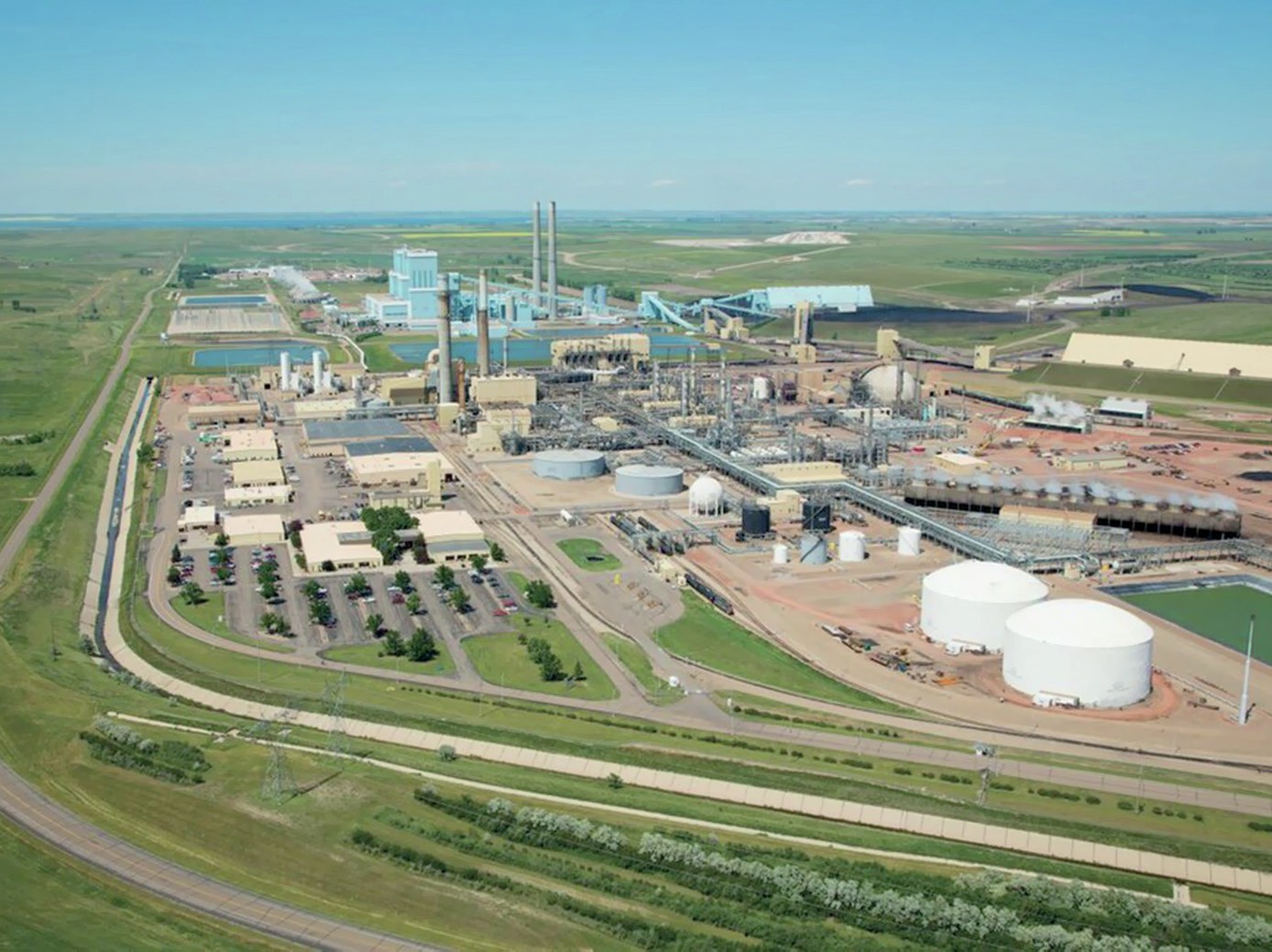
China
China is the world’s largest coal producer, mining around half of the world’s coal and consuming just over half (55%). China’s ammonia industry grew on the back of coal gasification, initially using fairly simple fixed-bed atmospheric pressure UGI gasifiers, which use air and steam rather than oxygen for the gasification process. While this makes them relatively cheap, it also means that they operate very inefficiently, and can only use high quality anthracite coal as feedstock. These plants, often small scale (<300 t/d) in the early days of China’s ammonia industry, proliferated across the country until there were several hundred in operation, many of them feeding ammonium bicarbonate production.
However, as China opened up economically in the 1990s, they faced competition from overseas ammonia producers, often using low cost natural gas in locations such as the Middle East. This led to a second wave of Chinese domestic production, some of it using natural gas in locations such as Hainan Island, and most of the rest switching to more modern fluidised bed or entrained bed gasification processes at larger scales (>1,000 t/d) and able to use cheaper bitumen or lignite coals. The wave of new Chinese ammonia plants meant that by 2018, around half of Chinese coal-based ammonia capacity was based on more modern gasification techniques, and many of the smaller and less efficient plants had shut down.2
From about 2015, China’s government took a decisive strategic turn, trying to pivot the economy from its previous concentration on industrial capacity towards consumer spending, and shifting towards more ecologically friendly policies, cleaning up the country’s major air pollution problems and moving to more sustainable use of energy. This has impacted on the ammonia and downstream fertilizer industry, leading to much stricter emissions limits and the closure of some of the most polluting plants, again often older capacity, or restriction of their operation during certain times of year, such as winter when major cities can be blanketed by smog. At the same time, however, China has continued to build coal-based capacity, replacing older and dirtier plants with more efficient and modern ones.
India
India built two coal gasification-based ammonia plants during the 1970s at Ramagundam and Talcher, but these suffered operating difficulties due to the high ash content of Indian coal (35-45%) and were closed down in the 1990s. India, like China, is a gas-poor but coal-rich country, and various plans for more ammonia capacity based on coal gasification were advanced over the decades, but the experience of the two 1970s plants acted as a brake on these developments. A new large scale (2,200 t/d ammonia, 3850 t/d urea) coal gasification-based ammonia plant at Talcher was proposed as long ago as 2007, and finally approved by the Modi government in the 2010s, but disputes over coal supply and the Covid19 pandemic have slowed the project, and it has still not yet commissioned, though construction, being conducted by China’s Wuhuan Engineering, is said to be close to completion. The plant will blend the local coal with 25% petroleum coke as feedstock in order to reduce its overall ash content. Once again, though, the plant’s troubled history seems to have functioned to put off new coal-based developments until the current plant can demonstrate that it works.
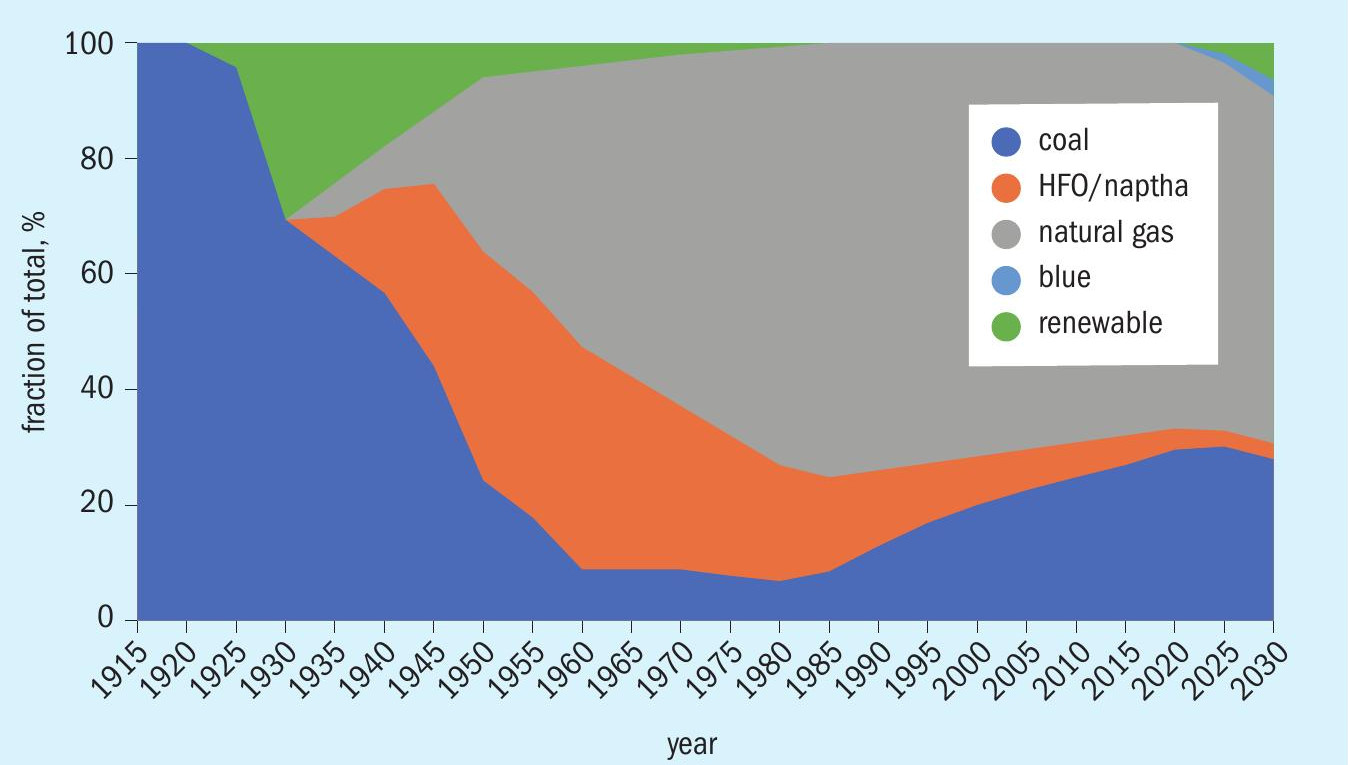
Indonesia
Indonesia operates a considerable amount of gas-based ammonia capacity across the archipelago. But the country is also a major coal producer, mining 687 million tonnes in 2022, or around 8% of the world’s coal, and coal generates around 45% of all energy used in Indonesia. The country has tried to developing two coal gasification projects, aimed at methanol production rather than ammonia. The first was to be built at Tanjung Enim, and was originally a collaboration between Air Products, state-owned coal producer Bukit Asam and national oil firm Pertamina. It would use 6 million t/a of coal to generate 1.4 million t/a of dimethyl ether (DME) via syngas and methanol steps, to replace imports of LPG. In 2022 Air Products inked a similar deal with Bakrie Group companies, PT Kaltim Prima Coal and PT Arutmin Indonesi for a coal-based methanol plant at Bengalon, East Kalimantan. However, Air Products exited both projects earlier this year, as Pertamina, which would have taken the offtake from the first plant, reportedly had cold feet over coal prices and the project’s economics, and the status of both projects now remains very uncertain.
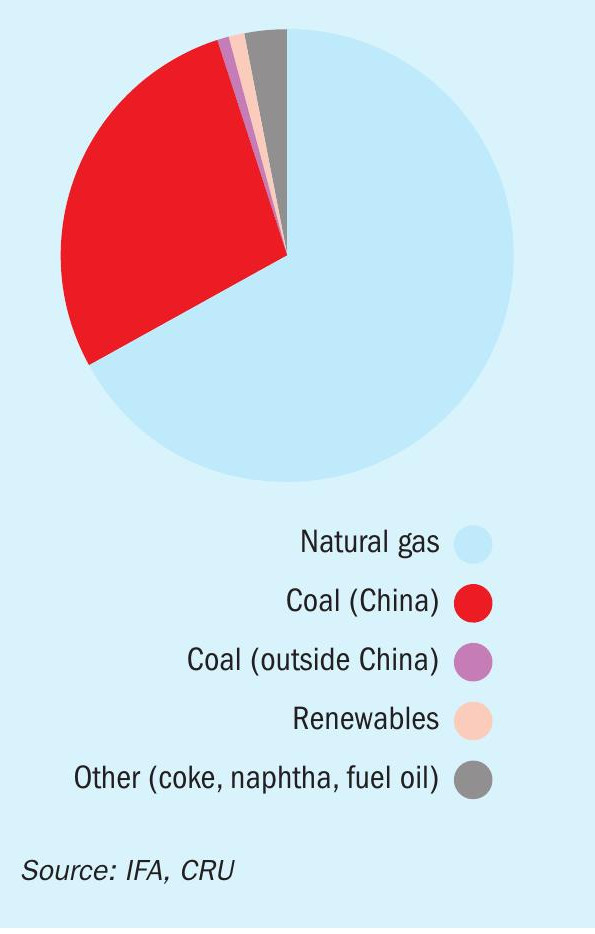
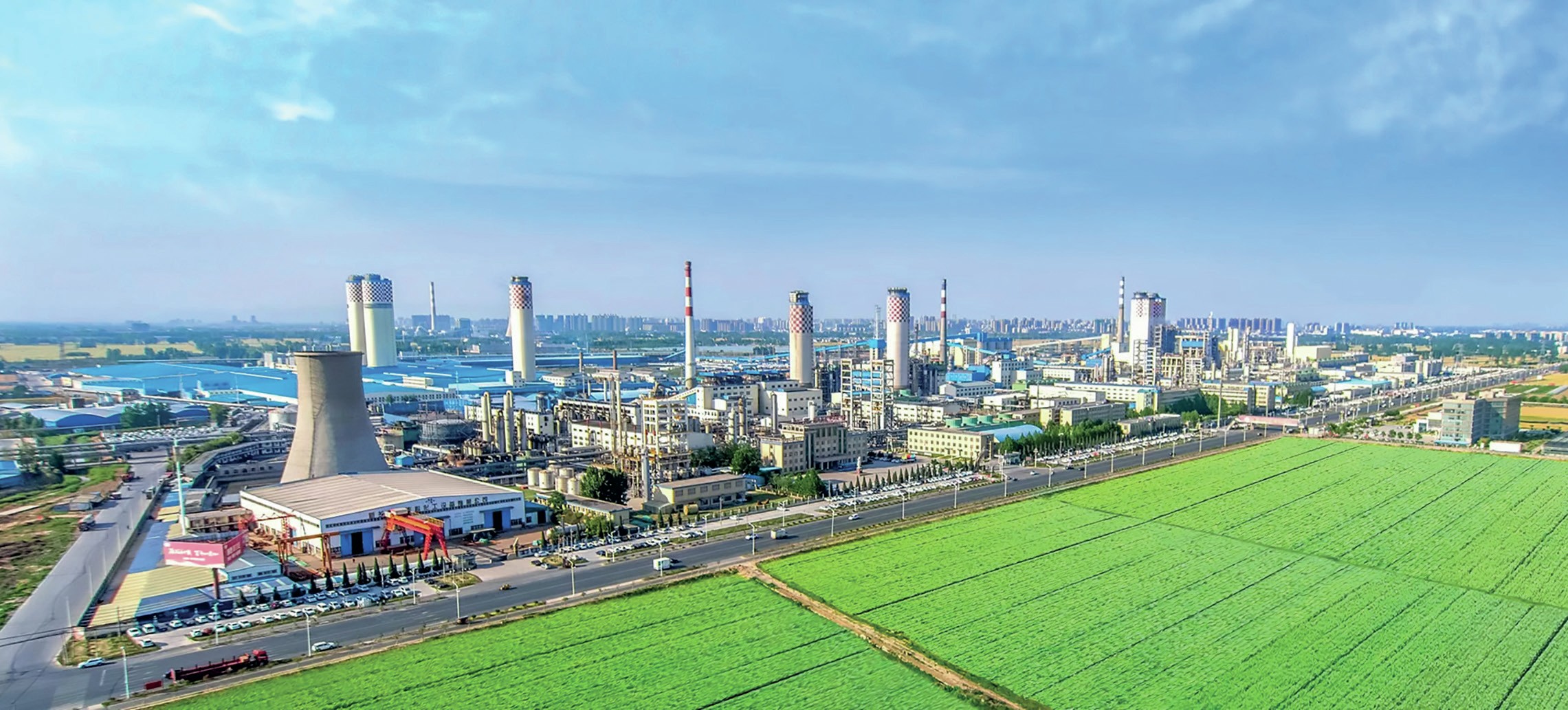
Emissions concerns
Looming large over all coal-based developments these days is the spectre of carbon emissions. Even the most efficient Chinese bituminous coal-based ammonia production generates on average 2.0-2.1 times as much carbon dioxide as an average natural gas-based plant. This means that there is pressure on existing coal-based capacity to ‘clean up’ its operation. The Great Plains Synfuels Plant at Beulah, North Dakota, which generates 400,000 t/a of ammonia from coal, is moving to carbon capture, utilisation and storage (CCUS).
Sasol’s major coal gasification site at Secunda in South Africa is facing challenges with the company’s commitment to a 30% cut in carbon emissions by 2030 and may be scaled down or closed.
Even China is beginning to introduce an emissions trading scheme – albeit at a low carbon price at present – which will affect the economics of coal-based production. At the moment, it seems almost inconceivable that any new coal-based plant could be built outside of China without incorporating CCUS, and existing plants are likely to move to CCUS or greener feedstocks, or face closure.
Within China, there are projects to convert some coal-based production to partial renewable feeds. A 20,000 t/a pilot plant came onstream near Chifeng City in Mongolia earlier this year developed by Envision, and the second and third phases of this project, planned for 2025 and 2028, are proceeding. Last year, Topsoe signed an agreement with Mintal Hydrogen Energy Technology as technology provider for a new green ammonia plant in Baotou, Inner Mongolia, in the heart of China’s coal-based ammonia production. The new plant will be the first ‘dynamic’ green ammonia plant in China, using technooogy which allows for considerable turn-down rates, allowing production of down to 10% of normal capacity. The first phase will have a 100% capacity of 1,800 t/d, with expected start of production in 2025 and will replace local coal-fired production. Inner Mongolia has considerable potential for wind energy, and China also has large scale domestic electrolyser production, bringing down capital costs. Overall, there are some 9 million t/a of renewable ammonia capacity under development in China, with perhaps 4-6 million t/a possibly in operation by 2026. In addition to this, in June 2024 the National Development and Reform Commission (NDRC) announced a new ‘ammonia industry special action plan’ with a target of 13 million t/a of CO2 emission reduction from the sector by 2025, mostly through the retirement and retrofit of older, more inefficient facilities. China has been pushing energy efficiency, fuel switching and renewable feeds rather than CCUS for its ammonia capacity because it has less experience and expertise in the latter.
The end of coal?
China remains the main bastion of coal-based ammonia capacity, and nowhere outside of China are there active projects in developing new coal based ammonia plants. China’s governmental decisions will in effect decide the future of coal-based ammonia, and while the sheer volume of ammonia produced by coal in China means that it will be with us for some years to come, there is now a major government push on conversion to renewable feeds, efficiency improvements and the replacement of the remaining older gasifiers with more modern ones. There will be a long tail of production as it gradually closes or switches, but it looks as though the writing is on the wall for coal as a means of generating ammonia.
References