Nitrogen+Syngas 392 Nov-Dec 2024
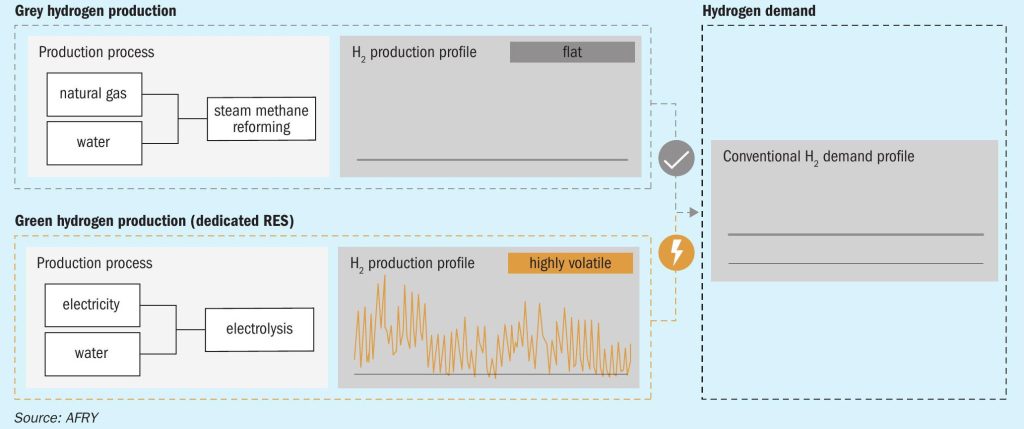
30 November 2024
Making RFNBO compliant ammonia competitive
GREEN AMMONIA
Making RFNBO compliant ammonia competitive
One of the key challenges of producing RFNBO (renewable fuels of non-biological origin) compliant ammonia is managing the intermittency associated with renewable energy sources for hydrogen production. Furthermore, the additional costs associated with managing this intermittency can be significant. In this article, Dr Solomos Georgiou of AFRY Management Consulting explores those additional costs as well as potential ways to achieve cost savings and make RFNBO-compliant ammonia production competitive against conventional ‘grey’ ammonia.
Green hydrogen production often requires the direct use of electricity from renewable energy sources such as solar and wind. The intermittency of the electricity source and the subsequent hydrogen production profile leads to significant volatility when compared to the conventional way of producing hydrogen using steam methane reforming (SMR); in other words, ‘grey’ hydrogen. At the same time, the conventional demand profile for hydrogen is generally flat (or very defined) as it is driven by the downstream industrial process (Fig. 1). As a result, for green hydrogen to be comparable to SMR in meeting offtake demand profiles, it requires flexibility solutions and/or ways to minimise the volatility of hydrogen production. Importantly for the competitiveness of green hydrogen, this needs to be done in a cost-effective way.
In this article ‘green’ and ‘RFNBO’ is used interchangeably. Similarly, ‘grey’ and ‘SMR-based’ are also used interchangeably.
With sufficiently large hydrogen storage, supply and demand in a green hydrogen-based system can be balanced, and offtaker demand profiles could be met. However, having a very large hydrogen storage capacity can be prohibitively expensive and practically infeasible (e.g., due to available space); thus, making it uncompetitive against existing hydrogen supplies.
AFRY has analysed the cost competitiveness of green hydrogen against SMR, using AFRY’s proprietary Hydrogen Optimisation Tool. This tool uses mathematical optimisation programming techniques to minimise the levelised cost whilst satisfying the constraints/requirements set, either on the supply side or the demand side. The tool has capabilities to enable key drivers and insights to be determined regarding the production of hydrogen and its derivatives. It is worth noting that in this article only a small fraction of the tool’s capabilities is used.
To quantitatively assess the impact of key factors AFRY has analysed several illustrative case studies that are summarised in Fig. 2.
As a base case, an ammonia production system utilising 100% RFNBO compliant hydrogen whilst simultaneously optimising only hydrogen storage capacity has been modelled. This results in significantly more expensive ammonia production than a SMR-based system. More specifically, the levelised cost of ammonia production (LCOA) of a SMR hydrogen-based system is 79% cheaper than the RFNBO hydrogen-based system in the base case (Fig. 3a). The single biggest cost element in LCOA of green ammonia is hydrogen storage, which, in the base case requires a very large capacity and is the only optimisation considered.
This demonstrates how uncompetitive green hydrogen-based ammonia can be when only considering the optimisation of hydrogen storage. It is necessary, therefore, to consider the optimisation of other components’ capacity and operation for hydrogen production. In this case study, the key components considered are solar PV, onshore wind, electrolyser and hydrogen storage.
Co-optimisation of renewable energy sourcing, electrolyser, and hydrogen storage ensures that appropriate resources are used cost efficiently leading to improvements in the cost competitiveness of green ammonia. In the illustrative case study here, a 58% decrease in LCOA was achieved through co-optimisation (Fig. 3b). In addition, hydrogen storage requirements decreased to a more reasonable level. Even though it is still about double the cost of a grey hydrogen-based system, it is a significant cost reduction that could close some of the cost gap between grey and green ammonia.
Although traditionally ammonia production has been considered a relatively inflexible process (possibly because it was not needed when using SMR), introducing some flexibility could help reduce the overall levelised cost of production. Even assuming existing ammonia production technology with limited flexibility, a further 14% LCOA decrease can be observed whilst still meeting the same annual ammonia demand, despite the need to have a slightly larger ammonia production plant (Fig. 3c).
If some technology improvements are assumed aimed at increasing the flexibility of ammonia production e.g., by relaxing its operational limits, additional cost savings of 26% are seen compared to the system with optimised hydrogen production (Fig. 3c). Furthermore, hydrogen storage capacity requirements also decrease through the enhancement of ammonia production flexibility. In summary, the greater the flexibility of ammonia production the better green hydrogen production can cope with the volatility in renewable power generation. By this point, ammonia production based on fully green hydrogen has significantly reduced and approaches the cost of grey hydrogen-based ammonia, closing the gap to only 48%. This is a significant cost saving compared to the gap of the base case and optimised H2 case at 376% and 100%, respectively.
However, industrial offtakers do not necessarily need 100% RFNBO to comply with the relevant European obligations. Therefore, AFRY has examined the impact of blending grey hydrogen with green hydrogen whilst still meeting the 42% RFNBO obligation. Hence, industrial offtakers, including ammonia producers, could take advantage of potentially cheaper grey hydrogen and still satisfy their RFNBO obligations.
Even assuming that the SMR plant supplying grey hydrogen is completely segregated (i.e. works independently from the green hydrogen production plant), a decrease in LCOA of 19% can be seen compared to the previously cheapest case (i.e. the highly flexible ammonia plant). That is whilst still meeting the 2030 RFNBO obligation of 42% (Fig. 3d).
For a fully integrated system where the SMR and electrolytic production are co-optimised (still within SMR flexibility constraints), the LCOA savings increase to 23% (Fig. 3d). Therefore, despite flexibility constraints of SMR, there could be additional savings through the integration of grey and green hydrogen production. Cost benefits from co-optimised grey-green integrated systems could potentially be even greater in less flexible ammonia production systems. Furthermore, a less obvious benefit achieved from co-optimisation is achieving this level of cost savings with a smaller increase in ammonia production capacity. This potentially avoids a significant increase in capital expenditure while still achieving a decrease in LCOA.
The analysis presented here demonstrates how the optimal selection of technologies and solutions can significantly improve the competitiveness of RFNBO compliant ammonia. In the case studies considered in this article, optimisation across the key components results in a system that could comply with the 2030 European RFNBO obligations whilst being only 14% more expensive than grey ammonia. Therefore, the funding gap to be covered by subsidies and/ or a voluntary green premium by offtakers has significantly shrunk making the compliance with RFNBO policies more achievable.
In summary, yes, ammonia production using green hydrogen can be expensive; yes, ammonia production using green hydrogen might have its technical challenges; but optimal and project tailored solutions could potentially make RFNBO compliant ammonia attainable and competitive.