Sulphur 415 Nov-Dec 2024
30 November 2024
Sulphur Industry News Roundup
Sulphur Industry News
AZERBAIJAN
Contracts awarded for SRU upgrade
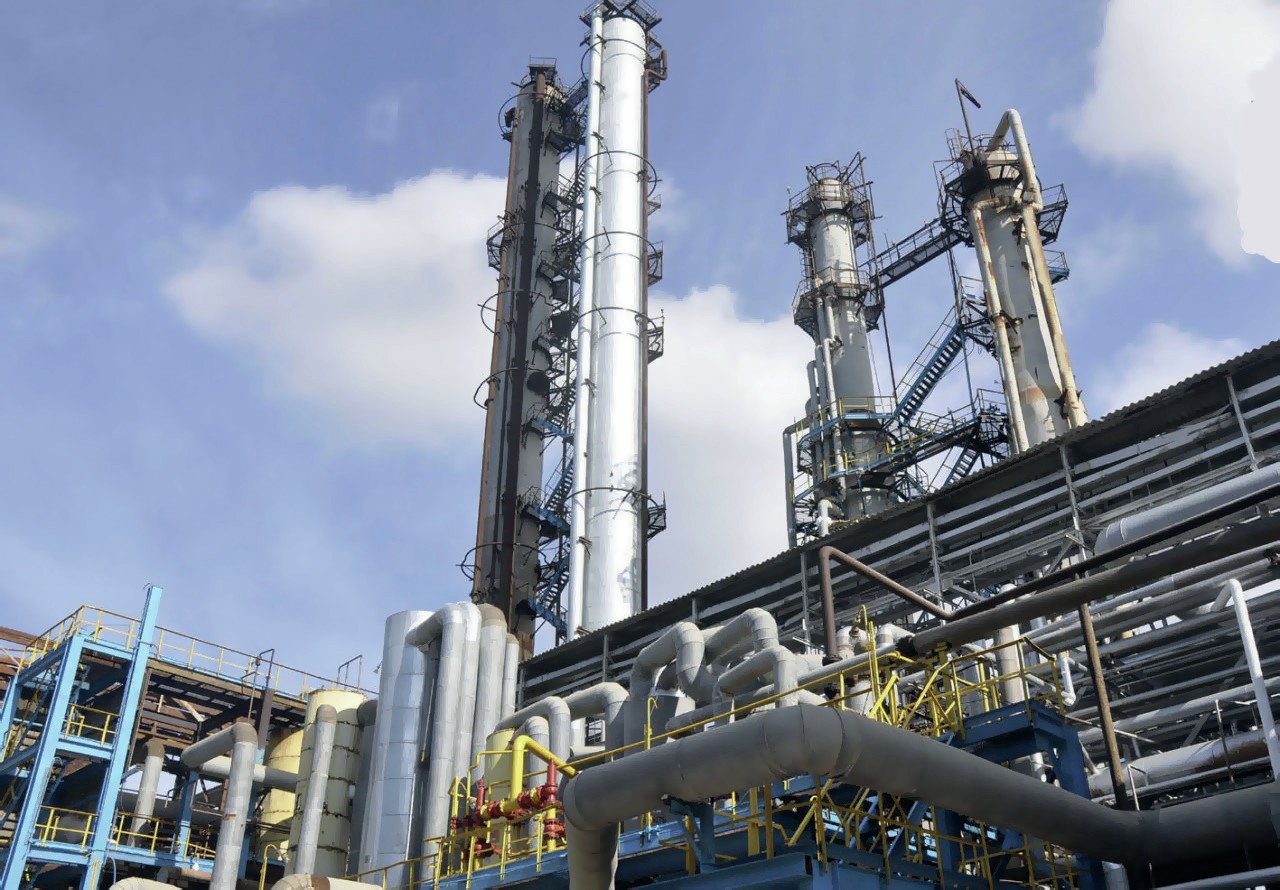
NextChem has been awarded two contracts to upgrade and expand the capacity of the Heydar Aliyev Oil Refinery (HAOR) industrial complex in Baku by state oil company SOCAR. As part of the contract, NextChem will conduct a technological assessment and deliver a process design package to upgrade the existing sulphur recovery unit (SRU) with oxygen enriched air, a cost-effective and flexible solution for expanding its current sulphur production capacity. Additionally, NextChem will provide the licensing and the process design package based on its proprietary NX SulphuRec TM technology for a new SRU. NX SulphuRec TM is a portfolio of proprietary sulphur recovery technologies, based on the integration of modified Claus and tail gas treatment processes, aimed at reducing the environmental impact of acid and sour gases produced during the refining process.
Alessandro Bernini, CEO of NextChem’s owning group Maire, commented: “These awards confirm the mutually beneficial relationship with SOCAR to develop Azerbaijan’s natural resources transformation activities. We are eager to further support the upgrade of the Baku HAOR complex with our technologies that ensure the highest environmental standards.”
KAZAKHSTAN
KPO completes gas reinjection project
Karachaganak Petroleum Operating BV (KPO) says that its KEP-1A project has safely achieved first gas reinjection. The project milestone was reached with the successful operation of the fifth compressor at full discharge pressure, enabling gas from the Karachaganak Processing Complex (KPC) to be reinjected into the reservoir through the new gas reinjection system for the first time. The company says that this demonstrates KPO’s ongoing commitment to safe, responsible and efficient operation of the giant Karachaganak field. The compressor is set to significantly boost gas re-injection volumes, maintaining reservoir pressure and extending the field’s liquid production plateau. The project has progressed successfully despite external challenges such as geopolitical tensions, logistical restrictions, and a “supply chain crisis”. KPO is a joint venture between Eni, Shell, Chevron, Lukoil and state-owned KazMunaiGaz.
The parallel $730 million KEP-1B project is also under construction, including a sixth injection compression facility, gas dehydration unit, expansion of the gas gathering network and other associated facilities. Like KEP-1A, the EPC contractor is Italy’s Sicim. Completion is expected in 2026. However, while much of the associated sour gas is reinjected, the Kazakh government has also been pressing the project partners to move forward with a long-standing plan to build a dedicated 3.6 bcm/year gas processing plant to increase supplies of network gas to consumers in the country, which would boost sulphur recovery from the project.
Kashagan partners in talks on sulphur fine
Partners in the huge Kashagan project have reportedly restarted talks with the government of Kazakhstan over a prospective $5 billion lawsuit for alleged breaches of sulphur storage regulations. The Kashagan oil field is operated by the North Caspian Operating Consortium (NCOC), which includes Eni, Shell, ExxonMobil and TotalEnergies. The Kazakh government claims that NCOC breached its permitted sulphur stockpile of 700,000 tonnes by an additional 1 million tonnes, as well as alleged releases of sulphur dioxide and untreated waste water. The operating companies have not commented on the matter, but there is a widespread belief in the industry that the government is attempting to use the fine as leverage for financial advantage, as they did in a similar situation with KPO a decade ago. Bloomberg reports that there is an no fault offer on the table of $110 million of investment in social projects recoverable from the production sharing contract, and a social development fund, as well as an agreement over LPG pricing in exchange for the removal of the fines. NCOC won a court challenge to the environmental rulings, but this was overturned by an appellate court decision, and the case has moved to the country’s Supreme Court.
NextChem to collaborate on SAF
During the Kazakhstan-Italy Forum held in Milan in early October, NextChem and state gas company KazMunaiGas (KMG) signed an agreement to collaborate on advancing energy transition initiatives, using NextChem’s proprietary technology portfolio and process engineering capabilities. These initiatives aim at contributing to the decarbonisation and upgrade of Kazakhstan’s industry, in particular for the production of sustainable aviation fuel and low-carbon hydrogen through CO 2 capture, as well as for the implementation of circular solutions. NextChem and KMG will evaluate the feasibility of development initiatives in the country, involving NextChem sister company Tecnimont for the assessment of engineering, procurement, and construction activities when projects advance to the execution phase.
Alessandro Bernini, CEO of Maire, commented: “As one of the world’s leaders in the energy space, Kazakhstan is a strategic and valuable partner for us. In fact, the combination of the Country’s resources with our Group’s technologies and engineering know-how represents a unique opportunity to drive the global shift towards a sustainable and low-carbon economy. We are eager to make this journey together”.
UNITED STATES
New lithium sulphur battery ‘gigafactory’ announced
Lithium sulphur batter manufacturer Lyten has announced plans to invest more than $1 billion to build the world’s first lithium-sulphur battery “gigafactory” near Reno, Nevada. It will have the capacity to produce up to 10 GWh of batteries annually at full scale. Phase 1 of the facility is scheduled to come online in 2027. Lyten’s factory will manufacture cathode active materials (CAM) and lithium metal anodes and complete assembly of lithium-sulphur battery cells. Lyten says that its lithium-sulphur cells have a high energy density, enable up to 40% weight savings compared to lithium-ion cells and 60% less than lithium iron phosphate (LFP) batteries.
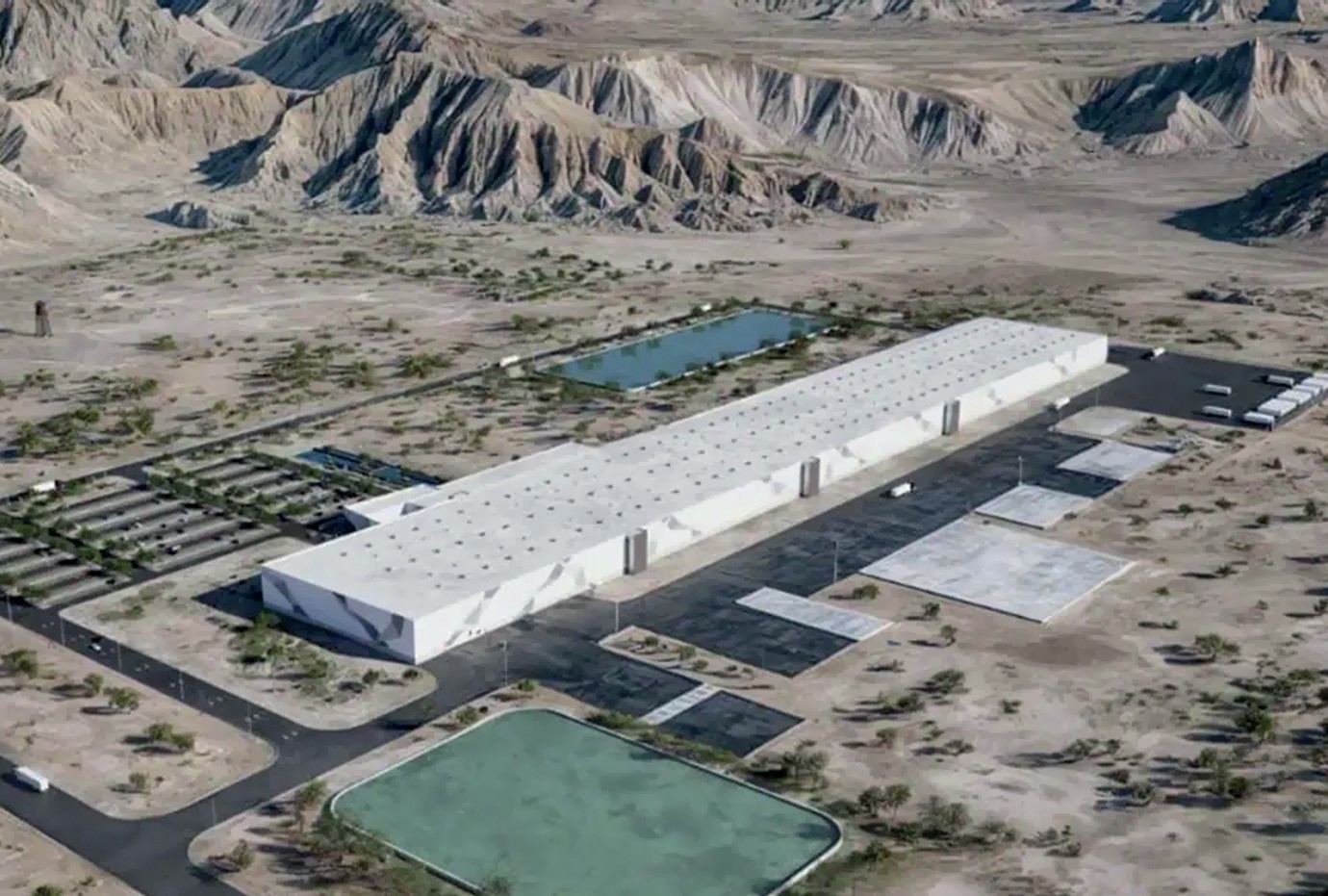
CSB launches investigation into H2 S leak
The US Chemical Safety and Hazard Investigation Board (CSB) says that it is launching an investigation into a fatal release of hydrogen sulphide at the Pemex petroleum refinery in Deer Park, Texas, on October 10th. Two contract workers died as a result of the release, and an additional 13 workers reportedly were transported to local medical facilities.
CSB Chairperson Steve Owens said, “This is a very serious incident that caused multiple fatalities and injuries and potentially put the surrounding community at risk.”
The release at the Pemex refinery, which is located about 18 miles east of Houston, also prompted a shelter-in-place order for two neighbouring cities, and a portion of Texas State Highway 225 was closed temporarily.
UNITED ARAB EMIRATES
Linde to supply CCS for Hail/Ghasha
Linde Engineering has won the contract to provide carbon capture technology for ADNOC’s $17bn Hail and Ghasha sour gas field development project. The deal has been awarded to Linde as a subcontract by NextChem, a subsidiary of Italy-based Maire, the main EPC contractor for the onshore package of the Hail and Ghasha project. As part of its contract, Linde will provide its adsorption-based carbon capture technology Hisorp CC, plus the core units, to capture and purify CO2 for carbon capture and storage (CCS).
Hisorp CC is an electrically-driven technology that combines pressure swing adsorption with cryogenic separation and compression to achieve CO2 capture rates of over 99%. The process does not require steam for regeneration, so it does not increase the carbon footprint, Linde says.
INDIA
Siwertell commissions sulphur unloader for Paradeep Phosphates
Bruks Siwertell says that it has commissioned a second Siwertell ship unloader for Paradeep Phosphates Ltd (PPL) in India. The new ST 640 D-type ship unloader joins a similar Siwertell unit at the port of Paradeep, in Odisha province. PPL’s first unloader was delivered in 2006 and was part of the port’s environmental transformation. PPL, part of the KK Birla Group and the OCP Group of Morocco, is a major manufacturer of phosphate fertilizers and is Asia’s second largest producer of diammonium phosphate (DAP), sourced from its plant close to the port.
“PPL has very high expectations of Siwertell technology,” said Bengt Svensson, Senior Contract Manager, Bruks Siwertell. “The delivery of our original Siwertell ship unloader, almost two decades ago, saw PPL switch from open-air sulphur handling with grab cranes, to safe, fully enclosed, dust-free operations. It literally transformed the port environmentally and was a significant step-up in efficiency. To keep up with demand, PPL needed to increase capacity, but wanted to do this in the most sustainable and environment-friendly way possible, leading to the second order,” he added.
The new rail-mounted ship unloader operates on the same jetty as Bruks Siwertell’s previous delivery for PPL, and similar to the first unit, has the capacity to discharge sulphur from vessels up to 60,000 dwt in size, at a rated capacity of 1,500 t/h. It alternates handling this cargo with rock phosphate at a rate of 1,200 t/h and muriate of potash (MoP) at 1,050 t/h. Both units are fitted with the Siwertell Sulphur Safety System (4S), which was first developed over 30 years ago to minimise the risk of explosions when handling this volatile and corrosive material. In open-air handling systems, such as grab cranes, the flammable and explosive nature of s ulphur is not so much of a problem, but becomes an issue for enclosed systems. However, sulphur should be contained, and its dust minimised, as it is damaging to the environment.