Sulphur 416 Jan-Feb 2025
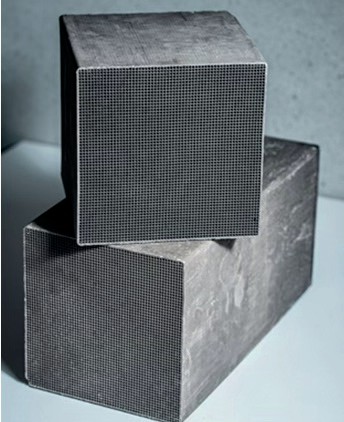
31 January 2025
A novel catalyst for sulphur dioxide oxidation
SULPHURIC ACID CATALYSTS
A novel catalyst for sulphur dioxide oxidation
This study introduces a new platinum-promoted honeycomb catalyst for sulphur dioxide (SO2) oxidation, designed to enhance energy efficiency and reduce emissions in sulphuric acid production. Compared to conventional vanadium oxide based catalysts, the platinum-based catalyst demonstrates higher catalytic activity, lower ignition temperature, and significantly reduced toxicity.
Sulphuric acid (H2SO4) is the world’s most important industrial chemical, with applications in a wide range of sectors, including fertiliser production, petroleum refining, wastewater treatment and chemical synthesis. The primary method of producing sulphuric acid is the contact process, a highly efficient process that uses catalysts to convert sulphur dioxide (SO2) to sulphur trioxide (SO2), which is then absorbed in diluted sulphuric acid to produce strong sulphuric acid or oleum. This catalytic conversion process has largely replaced older methods due to its higher yield, efficiency and environmental benefits.
The use of highly efficient catalysts in the production of sulphuric acid offers several advantages, such as increased reaction rates and energy efficiency, ultimately reducing production costs and emissions. As a result, catalytic processes in sulphuric acid production are critical to meeting the high demand for this versatile acid while minimising the environmental impacts associated with large-scale chemical production.
State of the art catalysts are based on vanadium pentoxide (V2O5) on Kieselguhr extrudates which, in addition to their negative environmental impact based on their classification as toxic, environmentally harmful and hazardous, have practical limitations in operation due to limited catalyst activity and durability.
P&P Industries’ platinum-promoted honeycomb catalysts (see Fig. 1) are designed to take both material durability and catalyst activity to new levels, enabling higher conversion and increased plant capacity while reducing capex and opex.
Catalyst development
The new platinum-promoted honeycomb catalyst, which was invented by P&P is highly cost efficient, due to effective employment of platinum as an active phase in combination with a tailor-made washcoat on a sturdy and resilient ceramic support. The recipe as well as the manufacturing process are patented and proprietary.
Methodology
Catalyst characterisation
The catalyst samples were manufactured in accordance with the P&P wash coating process. The material properties of PPH (platinum-promoted honeycomb) catalysts were analysed using a scanning electron microscope with energy-dispersive X-ray spectroscopy. The operational properties of the materials are withdrawn from the operational experience of P&P sulphuric acid plants and laboratory test results.
The catalyst activity was evaluated on a test rig at the P&P Technology Center, which was equipped with a gas mixing station, a temperature control module and online gas analysis. The gas concentration, volumetric flows and temperatures were selected as representative of those encountered in industrial applications.
Test case
A production plant with a capacity of 1,000 tonnes of H2SO4 per day was used as a test case. The design of the catalytic reaction and the corresponding converter were investigated. The feed streams were defined as shown in Table 1 and Table 2. Conversion calculations were performed according to the Sulphuric Acid Manufacture Analysis, Control and Optimization Book (Second Edition, 2013), supported by P&P’s own knowledge of real catalyst performance in industrial operation and laboratory test results.

Test results
Material characterisation
Historically, platinum-based catalysts for the oxidation of SO2 have contained a wasteful amount of precious metal immobilised on a support, for example, asbestos. Improved manufacturing techniques have enhanced metal dispersion and surface accessibility through increased porosity, resulting in a dramatic reduction of over 100 times the amount of platinum used, as shown in Fig. 2. Furthermore, the porosity of the washcoat was tailored to highly effective ignition behaviour.
The main criticism, beneath the cost, of the use of noble metal supported catalysts is their susceptibility to catalyst poisoning. However, state-of-the-art gas cleaning techniques such as hot gas filters, scrubbers and (wet) electrostatic precipitators have largely eliminated catalyst poisoning, making PPH catalysts an alternative to state-of-the-art vanadium pentoxide catalysts.
In addition to significantly reduced precious metal consumption, innovative manufacturing techniques, such as the P&P wash coating process, enable vastly improved material properties, as summarised in Table 3. Firstly, the honeycomb shape of the PPH catalyst, compared to the extruded vanadium pentoxide, greatly reduces the pressure drop (see Fig. 3), allowing either reduced main blower power consumption or increased flow rates, thereby increasing overall plant efficiency. Second, PPH catalysts exhibit increased mechanical stability, which has a positive impact on catalyst lifetime due to increased hardness and largely avoided attrition losses, eliminating the need for periodic catalyst screening. However, increased mechanical stability comes at the cost of higher bulk density and therefore higher specific gravity. This obvious disadvantage is completely overcome by the increased catalyst activity resulting in reduced catalyst volume, as discussed in the following section.

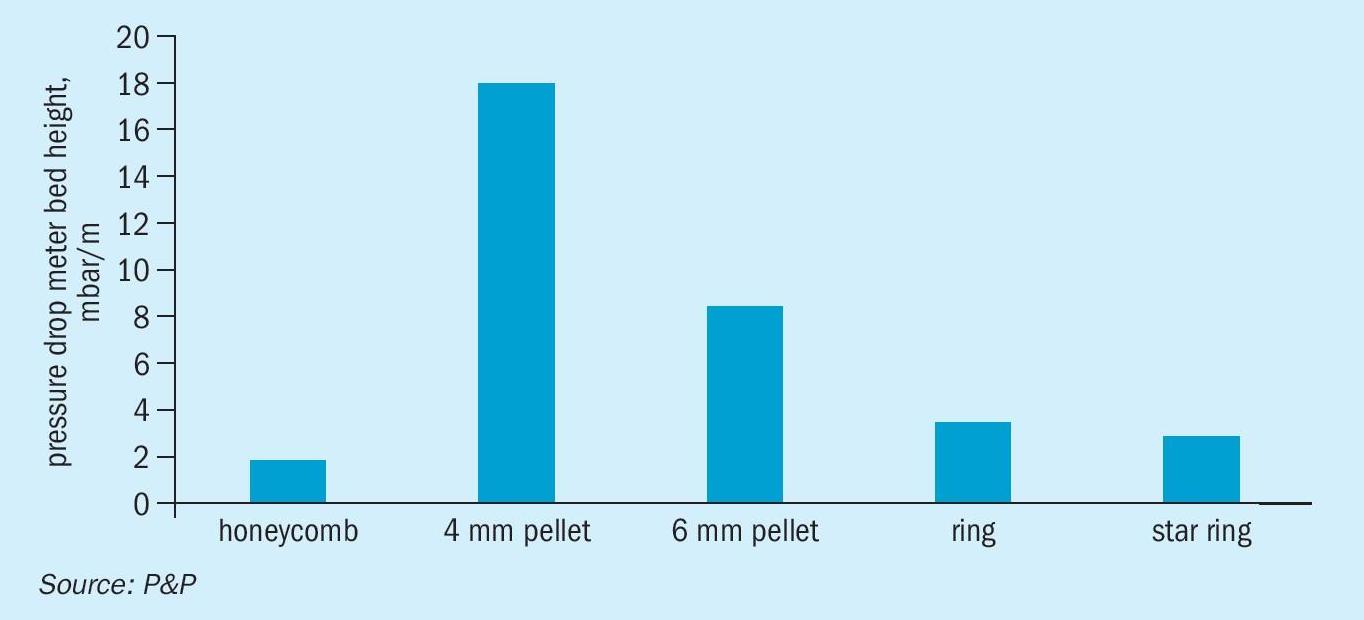
The geometric surface area of the honeycomb ceramic monolith itself, which is already higher than the geometric area of bulk catalyst extrudates (see Table 3), is further increased to reach a very high BET (Brunauer- Emmett-Teller) surface of the monoliths.
The analysis also shows a high dispersion of platinum on the accessible surface of the porous layer, which explains the greatly reduced platinum requirement. Furthermore, by applying a gas exchange layer, the amount of inaccessible active material is reduced, allowing the precious metal to remain sustainable. This is a big advantage against so called fully extruded precious metal catalysts. Due to the relatively low thickness of the gas exchange layer, diffusion lengths within the catalysts are reduced, resulting in improved conversion characteristics.
Catalytic performance of PPH
In the P&P Technology Center, the catalytic performance of the previously discussed PPH catalyst was evaluated in comparison to state-of-the-art vanadium pentoxide-based catalysts (obtained by P&P clients for detailed analysis). To this end, a comprehensive testing of the operational window of each individual catalyst sample was conducted, varying temperature but fixing gas velocity and gas composition. Fixed conditions were selected according to the actual process design of P&P. For each catalyst system, two qualities were tested at identical space velocities.
A comparative analysis of the turnover results is presented in Fig. 4. It is evident that PPH catalysts exhibit a remarkably reduced ignition temperature, thereby enabling their operation at considerably lower hurdle inlet temperatures. This offers two significant advantages. Firstly, the potential for higher SO2 conversion prior to reaching thermodynamic equilibrium, and secondly, the possibility of high heat recovery rates.
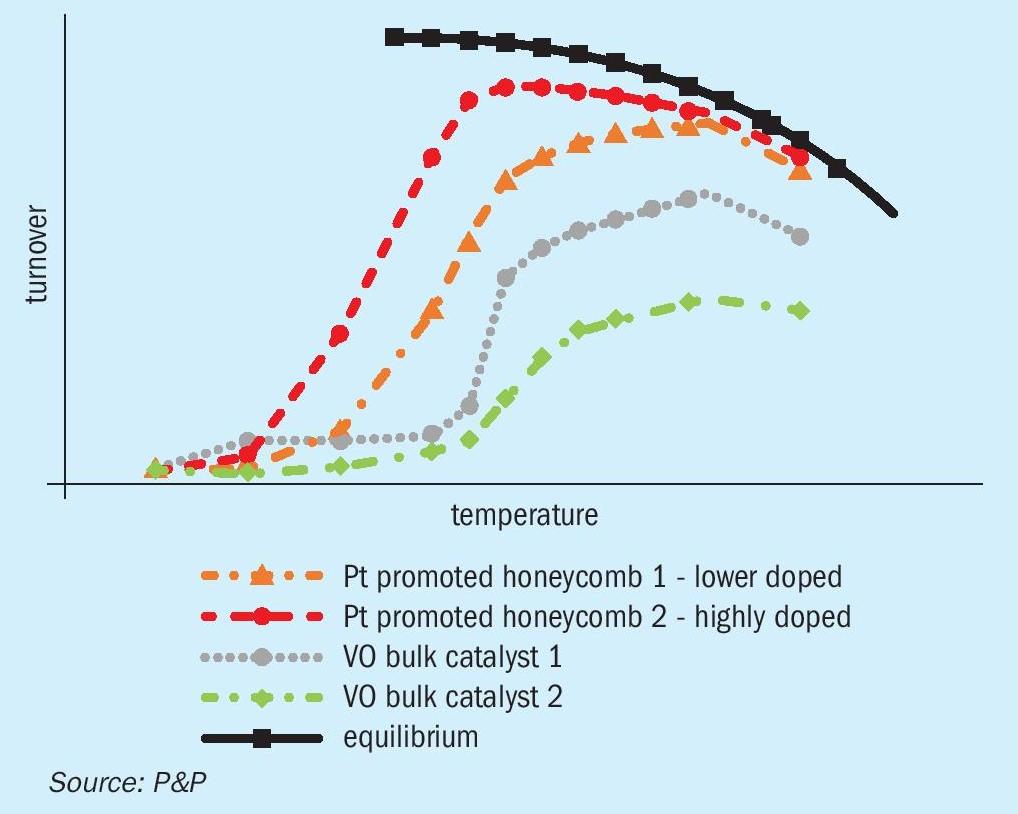
The experimental data indicate that, as the temperature increases, the ignition occurs relatively rapidly and approaches the thermodynamic equilibrium for the PPH catalysts. In contrast, vanadium-based catalysts display a comparatively slower ignition rate at elevated temperatures. This phenomenon may be explained by the shorter diffusion lengths observed within the gas exchange layer, the increased surface area, and the superior catalytic activity exhibited by the highly dispersed platinum particles.
From the kinetic and thermodynamic analysis presented, it can be concluded, that an up to three-fold reduction in catalyst volume replacing vanadium pentoxide catalyst with P&Ps PPH catalysts for the conditions tested is possible. This challenges the previously held assumption that the increased bulk density would be a disadvantage, for the necessary catalyst volume is much lower with PPH catalysts.
Impacts on process reactor design
In accordance with the experimental catalyst assessment conducted at the P&P Technology Center, a representative reaction and reactor design for a 1,000 t/d test case has been developed. The initial reaction conditions are presented in Table 1 and Table 2. In the case of the vanadium pentoxide catalyst, the inlet temperature for hurdles 1-3was fixed at 420°C, while the inlet temperature for hurdle 4 was reduced to 360°C, both in accordance with the specifications for standard and caesium-promoted vanadium pentoxide catalysts that are commonly used in this field, respectively. For PPH catalysts, inlet temperatures of 350°C for hurdles 1-4were chosen in agreement with analysed experimental data. Calculations for the theoretic conversion (SO2 conversion fully reaches the thermodynamic equilibrium) was performed with identic settings as for PPH catalysts. Overall, the process is designed in a three-plus-one configuration, with acid making through absorption occurring between catalyst hurdles 3 and 4.
The results of the thermodynamic and kinetic assessment of the heat-up paths are presented in Fig. 6. In accordance with thermodynamic expectations, a reduced inlet temperature indicates the potential for enhanced SO2 conversion, thereby highlighting the significance of low ignition temperatures, as demonstrated by the PPH catalyst. Consequently, the overall SO2 turnover prior to intermediary acid making is estimated to be 2.5% higher for the PPH catalyst than for vanadium pentoxide-based catalysts, as illustrated in Fig. 7. Despite the ability of caesium-promoted vanadium pentoxide catalysts to significantly reduce the inlet temperature at hurdle 4, the total SO2 turnover across all four hurdles remains below the levels achieved with PPH catalysts investigated in this study.
From the shown data it is obvious, that lowered gas inlet temperatures to especially the first hurdles boost the total conversion to a level which cannot be compensated by reducing inlet temperature of the last hurdle due to application of specialised and costly caesium-promoted vanadium pentoxide catalysts solely.
In consideration of the kinetic and thermodynamic aspects, a prospective example reactor configuration was designed. The corresponding results are presented in Fig. 8. The inlet and outlet gas streams are based on the results of the kinetic and thermodynamic calculations performed on the PPH catalyst. The total demand for the PPH catalyst in order to achieve the four specified hurdles is about 65 m³. In comparison, the use of 200 to 220 m³ of vanadium pentoxide catalysts would be required to achieve the same conversion, reflecting the superior performance of the PPH catalysts. Prior to the initial hurdle, the installation of a protective layer of inert packing, designed to filter residual dust from the inlet gas stream, could be considered, contingent on the specifications of the inlet gas in the design case. The indicated pressure drop for the dust guard is analogous to that anticipated for vanadium pentoxide catalysts per hurdle and is consistent with the data presented in Fig. 3.
The presented reactor setup is in compliance with established standards for emission limits. The indicated 38 ppm SO2 at the sack corresponds to 108 mg/Nm³ and 99.98% conversion. This is therefore below the limits set out in the German TA Luft (less than 400 mg/Nm³, greater than 99.9% total conversion). An analysis of the vanadium pentoxide thermodynamic data (total conversion of SO2 = 99.84 %) may indicate the necessity for additional SO2removal techniques or an increase in catalyst amounts to achieve closer alignment with the thermodynamic equilibrium, in order to comply with the regulations of TA Luft. It should be noted that this emission rating is to be considered as an example of the possibilities of the order of magnitude, for the reachable emission limits and should not be understood as binding figures for every possible design case.
Transforming the hurdle volumes into steel construction reveals the possibility to reduce overall reactor size. This results in a reduction in investment costs associated with the steel construction. In the presented case study, the cost of the steel construction material can be reduced by a factor of three (see Fig. 9), which correlates with the proposed threefold reduction in catalyst volume. The investment cost can be significantly reduced, contingent on the grade of steel utilised in the construction process.
The PPH catalyst exhibits not only enhanced activity but also superior durability, resulting in minimal attrition loss. In contrast to vanadium pentoxide catalysts, no screening is required. A comparison of the costs associated with the screening of vanadium pentoxide catalysts is presented in Fig. 10. While the investment cost for the catalyst is comparable between the PPH catalyst and vanadium pentoxide catalysts, the replacement of the catalyst due to attrition loss (10% loss per year assumed) results in an increase in investment cost of up to 1.5 over a ten-year period. These are only indicative values to show the possibility of the technology.
In contrast to vanadium pentoxide-based catalyst, which is classified as hazardous waste and must be disposed of accordingly, PPH catalyst can be recycled in order to recover the precious metals that have been applied. The quantity of recovery is dependent upon the quality of the applied PPH utilised in the process. After the end of life, a recycling quote of about 75% of the platinum metal is expected.
Transition of theoretic knowledge into real world applications
The PPH catalysts are characterised by a square base area, which renders them particularly suited to rectangular reactor cross-sections. Nevertheless, as the base area is considerably smaller than the reactor diameter, the PPH catalyst can be installed in a circular reactor cross-section without any issues. The use of ceramic fibre materials ensures that bypass formation is avoided. The PPH catalyst has been installed and operated in plants designed by P&P in locations across the globe for over a decade.
The PPH catalysts are thereby not only installed in plants for manufacturing of sulphuric acid but also in the waste gas treatment applications such as carbon monoxide oxidation in metallurgical or power plants, respectively.
Especially waste gas treatment in metallurgical plants show challenging gas compositions as the removal of all potential catalyst poisons is almost impossible. However, the PPH catalyst system developed by P&P and operated by customer in the metallurgical sector provides high resilience for catalyst poisons.
As an example, a catalyst which was heavily poisoned by arsenic was tested on the Catalyst Performance Unit of P&P’s Technology Center. No sufficient activity in the temperature range of 380°C to 480°C was detected. After several hours at 480°C, the arsenic could be removed by thermal evaporation.
The PPH catalyst showed excellent performance in CO oxidation with high bearing SO2 gases in metallurgical applications. Despite the poisoning situation, Pb, HF, Hg and Cd were also present in the gas phase, the catalyst shows excellent turnover performance. While thermal oxidation with natural gas is often used, the application of PPH catalysts is advisable as high energy saving can be achieved due to low operation temperatures (of about 150 to 200°C). For gas streams containing the poisons described in the upper section, higher temperatures are recommended for in situ regeneration of the catalyst.
Expanding PPH catalysts to new dimensions of SO2 oxidation
Although the PPH catalyst has demonstrated its resilience in the challenging gas atmospheres encountered in metallurgical processes, a common catalyst issue remains unresolved. The conversion of high-concentration SO2 streams, which are typical for metallurgical processes involving gases, remains a challenging task. The conversion of up to 35% SO2 observed in these gases has been found to exceed the thermal limits of state-of-the-art vanadium catalysts, resulting in their complete destruction within a short period of time.
The mechanism of vanadium catalyst destruction at elevated temperatures is well documented and attributed to the collapse of the porous structure and sintering of the catalytically active species, which ultimately results in the loss of catalytic activity.
Consequently, complex and costly workarounds, such as process gas recycling or SO2 dilution, were developed to safeguard the catalysts.
At the P&P Technology Center, a novel PPH catalyst was developed with the objective of determining its ability to handle these gas streams containing high concentrations of SO2 without the need for workarounds, such as dilution or gas recycling. The catalyst exhibits a considerably lower ignition temperature and increased temperature resistance in comparison to current PPH catalysts. These characteristics were achieved through the development of a novel formulation of the P&P wash coating process.
The results shown in Fig. 11 were obtained by expanding recent experimental data on the novel PPH catalyst to a potential converter design for 35 vol-% SO2 in the inlet gas. The extended operational window, which encompasses a range of temperatures from low to high, enabled the conversion of approximately 95% of the SO2 over three hurdles in one reactor. The presented design aligns with the observed conversion yields of conventional sulphur oxidation plants but increases sulphuric acid production drastically. When coupled with the P&P heat transfer system, which employs thermal salt, the enhanced heat generation can be readily managed, and the associated costs remain within the range of standard sulphuric acid plant designs.
P&P Industries AG employs a step-by step approach to carefully validate and enhance catalyst performance in laboratory, demonstration, and pilot-scale settings, prior to commercial application. By understanding the challenges faced by customers, P&P can provide needed catalyst solutions that have a remarkable impact.
For this very valuable development P&P Industries is currently looking for a partnership to construct a pilot plant as a proof of concept.
Conclusion
PPH catalysts produced with P&P’s proprietary technique have shown superior catalytic properties over state-of-the-art vanadium pentoxide catalysts. Catalytic activity, ignition temperature and pressure drop were lifted to a new level enabling reduced capex and opex while improving environmental footprint of the processes at the same time.
The presented technology has proven itself as a reliable product in industrial sulphuric acid manufacturing. P&P’s platinum-promoted honeycomb catalysts are successfully installed in over 30 plants all over the world.
Even PPH catalysts can be applied in challenging environments such as metallurgical processes underlining the resilience against catalyst poisoning.