Nitrogen+Syngas 393 Jan-Feb 2025
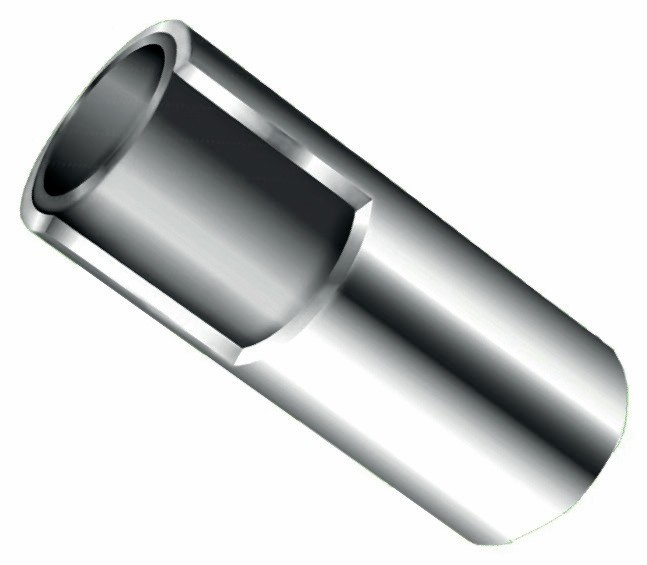
31 January 2025
Advanced material solutions for urea production
ALLEIMA
Advanced materials of construction for urea production
Alleima, a renowned manufacturer of advanced stainless steels and special alloys, has been at the forefront of developing corrosion-resistant alloys tailored for the urea industry since the 1970s. This article describes the key products developed by Alleima, their applications, and the benefits they offer to the urea production industry.
The corrosive challenge in urea production
Urea production involves the synthesis of ammonia and carbon dioxide under high pressure and temperature, resulting in a highly corrosive environment due to the presence of ammonium carbamate. Equipment failure due to corrosion can lead to costly downtime and maintenance, making the selection of appropriate materials crucial for ensuring the durability and efficiency of urea production plants.
Alleima’s advanced material solutions
Alleima’s extensive experience and broad portfolio of tailored material solutions for urea plants enable effective corrosion mitigation, regardless of process design and material preferences. The key products developed by Alleima for the urea industry include:
- Alleima® 3R60 Urea Grade (UNS S31603)
- Alleima® 2RE69 (UNS S31050)
- SAF™ 2906 (UNS S32906)
- Bimetallic Tubing (Alleima® 2RE69 with Zirconium 702)
The key products include both austenitic and duplex alloys that are extensively used in urea plants. The chemical composition of the alloys can be seen in Table 1.
Alleima® 3R60 Urea Grade (UNS S31603)
Alleima® 3R60 Urea Grade is an enhanced version of AISI 316L, characterised by higher purity and higher alloying content than standard 316L. These features make the microstructure of Alleima® 3R60 Urea Grade very austenite stable, preventing the formation of ferrite. As a result, the grade is highly resistant to both general and intergranular corrosion in the process solutions used in urea manufacturing.
In urea plants, Alleima® 3R60 Urea Grade is typically used for high-pressure piping or in equipment where the temperatures are relatively low. The grade requires passivation air to not actively corrode in the carbamate solution. Depending on the temperature, different corrosion rates can be expected.
Alleima® 2RE69 (UNS S31050)
Alleima® 2RE69 is an austenitic material specifically developed for use in the most severe conditions in urea plants. The grade is characterised by excellent corrosion resistance to ammonium carbamate and outstanding resistance to intergranular corrosion, owing to its well-balanced chemical composition. The grade has high purity with very low or zero ferrite content.
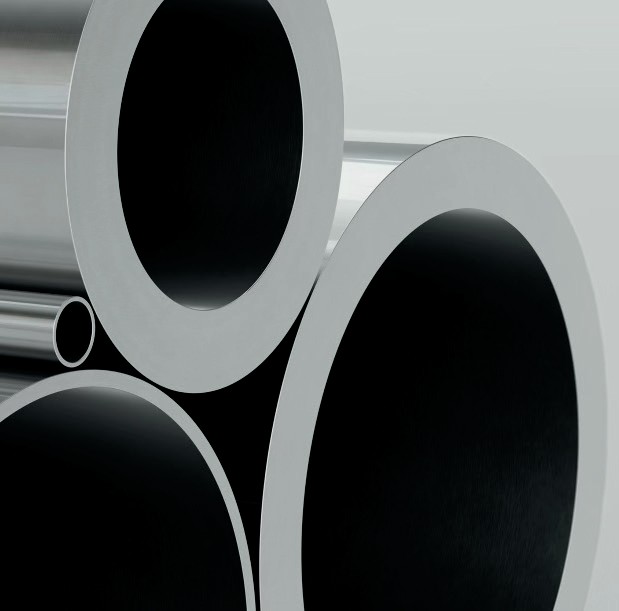
Alleima® 2RE69 can be used successfully in the high-pressure section of urea plants, where its use as stripper tubes, carbamate condenser tubes, and high-pressure piping is common, see Fig. 1. Despite the advantages of Alleima® 2RE69, it relies on passivation air and may be susceptible to stress corrosion cracking (SCC) if the boiler feed water or process steam contains chlorides. Nevertheless, Alleima® 2RE69 has a solid track record, with installations in the stripper section lasting for more than 35 years, confirming the grade’s optimal properties.
SAF™ 2906 (UNS S32906)
SAF™ 2906 is an austenitic-ferritic stainless steel developed for use in the urea synthesis process. The grade has been optimised for superior corrosion resistance against carbamate solutions with low oxygen content, enhancing both plant safety and productivity.
SAF™ 2906 has excellent resistance to general corrosion, intergranular corrosion, pitting corrosion, and chloride-induced stress corrosion cracking (SCC). Its resistance to general corrosion makes SAF™ 2906 suitable for the construction of the high-pressure synthesis section of a urea plant, as it does not corrode actively in the carbamate solution, even with extremely low concentrations of oxygen in the system. Moreover, SAF™ 2906 is immune to condensation corrosion, which can be a problem for equipment constructed from 316 UG and 25-22-2 type materials.
The combination of outstanding corrosion resistance and high mechanical strength of SAF™ 2906 offers significant design advantages compared to Alleima® 2RE69 and Alleima® 3R60 Urea Grade, allowing equipment to be designed with thinner wall thicknesses. SAF™ 2906 can be used successfully in the high-pressure section of the urea plant for all components, including stripper tubes, condenser tubes, high-pressure piping, valves, and liner plates.
Bimetallic tubing (Alleima® 2RE69 with Zirconium 702)
In certain urea production processes, the conditions and design temperatures of the urea stripper can be particularly high, where neither Alleima® 2RE69 nor SAF™ 2906 can be used effectively due to increased corrosion rates. Under these conditions, reactive metals like zirconium or titanium are normally preferred to have acceptable corrosion rates. However, titanium is prone to erosion problems which can limit the lifetime of the urea stripper. Zirconium exhibits excellent corrosion properties in carbamate solutions. The drawback with zirconium is the high cost and low mechanical strength making a mono tube solution non-feasible for the high-pressure stripper in a urea plant.
Bimetallic tubing using a Zirconium 702 inner tube and Alleima® 2RE69 outer tube enables the use of zirconium where it is needed and is a well-proven concept for the HP strippers, see Fig. 2. The outer component in Alleima® 2RE69 provides the mechanical strength, and ease of vessel fabrication, with a stainless-steel cladded tube sheet and welding being pure stainless-to-stainless. The zirconium acts as a corrosion barrier and is only used where it is needed, as the tube inner layer, giving a cost-effective solution. The bimetallic tube is a premium solution for the most demanding environments.
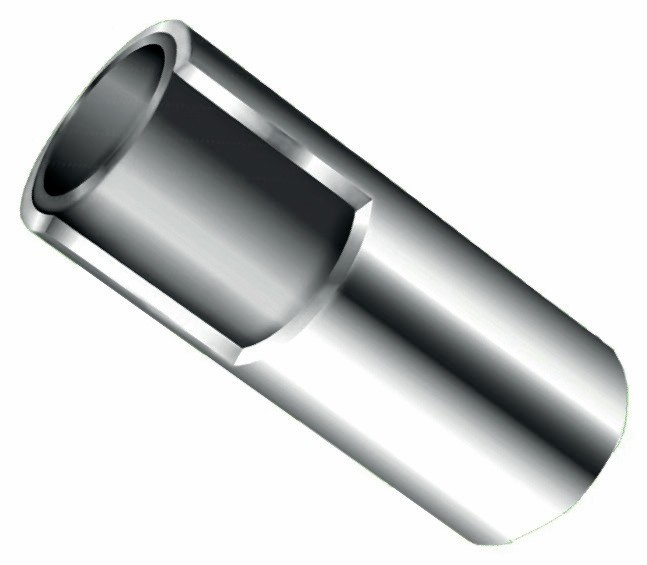
Innovation and sustainability at Alleima
Alleima’s origins date back to 1862 when the company was founded as Sandvikens Jernverk by Göran Fredrik Göransson, a pioneer in using the Bessemer method for steel production on an industrial scale. The manufacturing of stainless steel began in 1921, and in 1924, the first seamless stainless-steel tubes were introduced to the market, marking the beginning of Alleima’s journey.
Today, Alleima is a leading manufacturer and developer of high value-added products in advanced stainless steels and special alloys. The company’s product offerings cover a wide range of industries and applications, including seamless tubes and products in advanced stainless steels, industrial heating elements and heating systems, wire for medical devices, as well as a wide range of strip steel and strip-based products. Innovation is key to Alleima’s success, with a portfolio of over 900 active alloy compositions and more than 850 patents.
Alleima’s fully integrated value chain, from R&D to end-product, ensures industry-leading technology, quality, sustainability, and circularity. For example, Alleima’s stainless steel contains 80% recycled steel and uses fossil-free energy sources. The company is also investing a large and increasing share of its strategic R&D budget in the green transition and is committed to the UN Sustainability Goals (SDGs) and Science Based Targets initiative (SBTi).
The urea production industry faces significant challenges due to the highly corrosive nature of the process environment. Alleima’s extensive experience and broad portfolio of tailored material solutions for urea plants enable effective corrosion mitigation, ensuring the longevity and efficiency of urea production plants. By staying at the forefront of material science, Alleima aims to support the urea industry in achieving higher efficiency, safety, and sustainability in its operations. The company’s ongoing investments in research and development, coupled with its dedication to quality and customer satisfaction, position Alleima well to address future challenges and opportunities in the industry.
STAMICARBON
Advanced materials and equipment for fertilizer production
Stamicarbon, the nitrogen technology licensor of NEXTCHEM (MAIRE Group), has a long history of innovation with the application of technology in mind. These applications have often required experience with and expertise in materials. Reliability has always been an important value for Stamicarbon as it is applied to equipment supply, communication, and actions. As the company ventured into different technologies, such as ammonia and nitrates, new equipment based on different applications and varied materials was needed, but with the reliability and expertise of Stamicarbon.
Stamicarbon continuously enhances its material and high-pressure equipment portfolio to meet the evolving demands of modern fertilizer production, ensuring unmatched performance throughout a plant’s lifecycle. For grassroots plants or revamp projects, regardless of the plant licensor, Stamicarbon sets the standard for advanced materials and equipment, ensuring efficient, reliable operations with minimal environmental impact.
The super duplex revolution
The urea production process operates under extreme conditions of high temperature and pressure, requiring the condensation of ammonium carbamate as an intermediate compound. This leads to highly corrosive circumstances unless proper alloys are applied and passivating conditions are created. Addressing these challenges requires advanced materials and high-quality equipment capable of withstanding such aggressive environments while delivering long-term reliability and efficiency.
In the 1990s, Stamicarbon, in partnership with Sandvik (now Alleima), revolutionised urea equipment production materials with the development of Safurex® , a proprietary super duplex stainless steel. Safurex® was specifically designed to eliminate corrosion in fertilizer plants, effectively resisting active ammonium carbamate corrosion, chloride-induced stress corrosion cracking, and other challenges unique to high-pressure urea synthesis equipment.
The super duplex steel, now offered as E-type material, provides a wide range of advantages that make it an indispensable material in urea synthesis. It provides exceptional resistance to key types of corrosion, ensuring durability and reliability in aggressive chemical environments. Its independence from passivation air simplifies plant operations, reducing block-in length, operational complexity, costs, and risks. With improved mechanical properties and superior weldability, E-type steel enhances durability while minimising the risk of structural failures.
Thanks to its superior strength compared to conventionally used materials, less material is needed for the same functionality. The consequently reduced weight facilitates not only savings but also easier handling and installation, while its durability significantly minimises the need for frequent inspections and maintenance, leading to substantial operational cost savings. It has also demonstrated exceptional reliability, with over 2 million combined on-stream hours achieved without a single tube rupture, proving its capability to ensure safe and uninterrupted performance.
Stamicarbon equipment material extends the lifespan of equipment, improves overall plant process performance, and offers higher operational flexibility. This includes the ability to withstand extended block-in times and resilience to upset conditions, making it a versatile and robust solution for demanding urea production environments. Additionally, Stamicarbon’s collaboration with specialist steel mills has allowed for continuous material innovations, including the development of tailor-made chemical compositions to meet specific challenges in urea synthesis, ensuring superior corrosion resistance and mechanical performance.
Tailored solutions for every application
Urea production demands materials that combine durability and ease of maintenance. Stamicarbon addresses these needs with advanced materials that eliminate the need for passivation air, simplifying operations and reducing complexity.
As Stamicarbon’s business has expanded beyond urea in recent years, the need for different materials for different applications has increased. That’s why Stamicarbon Equipment, SEQ, has been introduced. It brings together the innovation expertise, material knowledge and materials categorised into three classes based on their application within the nitrogen fertilizer industry:
- U-Class: Designed for urea applications, with particular tailoring to high temperature/pressure and corrosive environments, such as in urea synthesis equipment.
- A-Class: Tailored for ammonia applications, with particular tailoring to high temperature and embrittling environments, such as in ammonia converters.
- N-Class: Developed for nitrate applications, with particular tailoring to corrosive environments.
This diversity allows Stamicarbon to offer highly specific solutions that align with the unique requirements of different processes, further enhancing the efficiency and reliability of fertilizer production facilities.
Proprietary equipment
The market increasingly demands innovative solutions to reduce operational expenses, energy consumption, and emissions. By leveraging decades of expertise, Stamicarbon offers clients reliable, high-performance equipment tailored to specific applications using various specialised materials classes.
Stamicarbon combines advanced materials know-how with unparalleled expertise to deliver high-quality proprietary equipment for urea production, including:
- High-pressure strippers – efficiently recovering ammonia and carbon dioxide while maintaining exceptional durability.
- High-pressure carbamate condensers – designed for energy-efficient heat exchange.
- Urea reactors (Fig. 1) – featuring high-efficiency trays and U-Class steel internals for maximum conversion efficiency.
- High-pressure piping and valves – engineered for reliability in extreme operating conditions.
- Liquid dividers and mixing tees – optimised for uniform performance and reduced operational complexity.
Stamicarbon maintains a solid span of control over its supply chain, working with top-tier fabricators. With thorough supply chain monitoring and quality checks at every critical stage, Stamicarbon ensures that each piece of equipment meets the highest standards. This approach ensures the quality and availability of critical equipment and spare parts made from proprietary U-class super duplex stainless steel. Moreover, the extension of Stamicarbon’s supplier base provides clients with maximum flexibility and access to multiple sources of qualified and reliable suppliers, ensuring optimal solutions for every need.
Stamicarbon’s materials have been successfully installed in numerous urea plants worldwide. The equipment has consistently demonstrated unmatched reliability, helping operators achieve long-term efficiency while reducing maintenance requirements.
Full life cycle support
Stamicarbon’s full life cycle support offered to fertilizer producers includes plant troubleshooting and equipment inspections required to ensure that customers’ equipment remains in optimal condition and performs reliably. These inspections can help detect issues like stress corrosion cracking and condensation, allowing for timely recommendations for repairs, operational adjustments, and procedural improvements. Accurate forecasting of equipment longevity and maintenance needs further ensures seamless operation and minimises unexpected downtimes.
In addition, to address unexpected emergencies like unplanned shutdowns, Stamicarbon provides 24/7 support through its dedicated emergency response team, ready to react immediately and ensure the plant’s operations remain safe and uninterrupted.
By incorporating these advanced reliability measures, Stamicarbon not only addresses current operational challenges but also establishes a solid foundation for long-term sustainable, high-efficiency performance across the lifecycle of its equipment.
Recent cases
Stamicarbon’s proprietary equipment made with Safurex® super duplex steel has been integral to most of its urea projects, demonstrating customers’ trust in its reliability and efficiency in urea production. Some of the recent applications include:
- North America: An urgent relining of a urea reactor was completed using super duplex steel, marking the first full reactor relining from zirconium to this advanced material.
- China: For the Ultra-Low Energy urea plant of Jiangsu Huachang Chemical Company, the customer has selected high-pressure equipment made of super duplex stainless steel. Stamicarbon will design and supply this proprietary equipment, enhancing the plant’s energy efficiency and operational reliability.
- Sub-Saharan Africa: A world-scale integrated ammonia and urea complex will utilise super duplex steel for high-pressure equipment, with Stamicarbon set to supply these components for the plant.
- Egypt: A state-of-the-art urea melt and granulation plant for El-Nasr Company for Intermediate Chemicals will feature high-pressure equipment made of super duplex stainless steel. Stamicarbon will design and deliver this equipment to ensure superior reliability and operational efficiency.
These cases highlight the versatility and reliability of super duplex steel, chosen by customers for its unmatched performance in diverse projects.
Driving the future of urea production
Stamicarbon’s expertise in material science and equipment design underscores its commitment to advancing the fertilizer industry. By combining innovative materials with decades of engineering experience, the company delivers solutions with Stamicarbon Equipment that enhance safety, performance, and sustainability for fertilizer producers worldwide.
SAIPEM
SATURN31™ – the new material for urea applications from Saipem and Tubacex
Saipem is a global leader in the engineering and construction of major projects for the energy and infrastructure sectors, both offshore and onshore. As such Saipem is committed to supporting its clients on the energy transition pathway towards net zero, with increasingly digital means, technologies and processes geared for environmental sustainability.
As licensor of its Snamprogetti™ Urea Technology, Saipem offers its clients state of the art services aimed at prolonging equipment life and improving performances and product quality.
The urea environment is one of the most challenging for materials due to the severe operating conditions to which they are exposed. In the Snamprogetti™ urea process, the high-pressure section due to the operating temperatures, pressures and relatively high content of carbon dioxide faces the most critical conditions.
To cope with these demanding conditions, Saipem provides end users with state-of-the-art high-pressure equipment. Initially, Saipem’s focus has been on ensuring proper manufacturing through stringent quality controls, reviews, and qualifications. In this phase AISI 316L UG and 25/22/2 Cr/Ni/Mo, materials readily available on the market, were selected as they ensured satisfactory performance. In particular, non-ferrous materials such as titanium and zirconium, were also applied for the urea stripper thanks to their strong resistance to corrosion phenomena at even harsher operating conditions.
SATURN31™
The development of SATURN31™ was dealt with a multi-optimum approach due to the need to simultaneously satisfy corrosion, manufacturing and constructability requirements.
The new material had to have better corrosion resistance than 25/22/2 Cr/Ni/Mo, and consequently of AISI 316L UG, with lower corrosion rates even in absence of oxygen; the intent being the minimisation of the overall quantity of air circulating in the urea unit and avoiding the need of a dedicated feed of oxygen to the stripper bottom.
To grant smooth manufacturing activities, the new material was required to have excellent weldability and machining properties, thus ensuring the quality of high-pressure equipment so far achieved. In addition, better mechanical properties than those of the materials available on the market were also looked for to allow a reduction of the overall weight laying on structures and foundations.
Having the goal to achieve different simultaneous optimums, the development started from numerical simulations to identify the most promising options in terms of chemical composition which were then tested by means of laboratory heats; industrial heats were then performed on the composition finally selected.
The new highly alloyed super duplex steel, SATURN31™, has high chromium and nitrogen contents and moderate additions of molybdenum, tungsten, and cobalt. The well-balanced chemical composition and an optimum solution annealing treatment ensure a final microstructure having a homogeneous distribution of austenite and ferrite bands free from intermetallic phases and precipitates (Fig. 1). This combination of alloying elements has excellent resistance to urea solutions with or without oxygen and, furthermore, guarantees a very high resistance to localised corrosion, such as pitting and crevice corrosion.
Corrosion properties
The corrosion resistance of SATURN31™ at high temperature and in a solution even more aggressive than that of the urea stripper bottom has been studied by immersion tests in an autoclave. Corrosion tests have also been performed on samples installed in industrial strippers.
SATURN31™ has shown outstanding corrosion resistance in both the presence and absence of oxygen (see Fig. 2).
Mechanical properties
SATURN31™ possesses very high mechanical strength (Fig.3). Having a yield strength of double that of AISI 316L UG and 25/22/2 Cr/Ni/Mo materials, significant reductions in pipe and tube thicknesses can be foreseen with beneficial impacts on equipment and bulk weight and on the total cost of the plant. The ductility of SATURN31™ is also high, making the new super duplex steel readily formable through fabrication processes such as bending or expansion.
Welding
The weldability of the new highly alloyed super duplex steel has also been tested: in urea environments, also in the welds, high mechanical properties and excellent corrosion resistance are achieved.
Trials have also been successfully conducted to assess the weldability of SATURN31™ with 25/22/2 Cr/Ni/Mo, confirming the possibility to combine the two materials; this could be useful, for example, in case of re-lining interventions on high pressure equipment.
Updates on SATURN31™
After its official presentation in 2022, SATURN31™ has been adopted as a material of construction for the internals of high-pressure equipment. A few sets of urea stripper ferrules (Fig. 4) have been installed as first industrial applications. Considering the accurate and delicate design of this kind of internal, these have been workshop trials confirming its excellent machining and weldability properties.
Next to come are high pressure equipment linings and other internals, for which SATURN31™ , thanks to its characteristics opens up new possibilities to achieve better operating performances.
With the completion of ASME code certification, SATURN31™ will also be used in the manufacturing of pressure parts, such as tubing for urea strippers and carbamate condensers, piping and relevant fittings.
Conclusions
SATURN31™ , the new material for urea applications by Saipem and Tubacex, has been developed to ensure high corrosion resistance, mechanical strength and weldability. After comprehensive tests, SATURN31™ has demonstrated excellent qualities under all the above aspects, resulting in an ideal material for the aggressive environment of the urea high pressure section granting longer equipment life.
Following the first industrial application of SATURN31™ in urea stripper ferrules, the next application will be as a liner material and for the fabrication of other internals of high-pressure equipment such as SuperCups.
Following ASME code certification, SATURN31™ will also be used in the manufacturing of pressure resistant components for equipment and piping. This step will open the way to design and manufacture the complete range of high-pressure equipment in SATURN31™.
TOYO ENGINEERING CORPORATION
Latest advancements in duplex stainless steels for TOYO urea plants
Toyo Engineering Corporation (TOYO) has been using duplex stainless steels (DSSs) for high pressure synthesis equipment of urea CO2 stripping process since the early 1980s. DP28W™, a DSS developed based on years of accumulated knowledge, has demonstrated excellent corrosion resistance through its successful track record. This article discusses the performance of DP28W™ in a commercial urea plant, along with the latest process, ACES21-LP™, from the perspective of corrosion resistance.
Three-year immersion test at one of TOYO’s urea plants
The use of advanced materials possessing high corrosion resistance in a urea environment is especially important to enhance the long-term reliability of facilities in a urea plant. The corrosion resistance of welded joints is degraded, especially in the heat affected zone (HAZ), compared with base metal due to the formation of harmful precipitations from welding heat input.
DP28W™, developed specially for urea plant applications, has an optimised chemical composition considering the effects of heat input in welding to ensure excellent corrosion resistance of welded joints. To compare the corrosion resistance of DP28W™ with various commercial grades of 25Cr DSSs (DSS-A, DSS-B, DSS-C), an immersion test was carried out in a commercial urea plant over three years. Welded test coupons of those DSS were mounted in the top and bottom sections of the ACES21™ urea reactor.
Fig. 1 shows the equivalent corrosion rates of those test coupons against DP28W™ and Fig. 2 shows macroscopic photos of those cross-sections. Equivalent corrosion rates of DSS-A, DSS-B, and DSS-C were higher than 1, indicating that the corrosion resistance of DP28W™ is superior to the other DSS.
Macroscopic photos of the cross-sections showed that no remarkable corrosion was observed at the HAZ of DP28W™. DSS-B showed significant corrosion in both base metal and weld metal.
The corrosion resistance of DSS-C base metal was better than that of DSS-B, but significant localised corrosion was observed at the HAZ. DSS-A shows good corrosion resistance both in the base metal and the HAZ.
As mentioned above, there is considerable variation in the corrosion resistance of 25Cr DSS including its welded joints even with a similar chemical composition. This suggests that the selected grade, in this case DSS-A, can be used in urea carbamate solution depending on the corrosiveness of the environment.
TOYO and Nippon Steel Corporation are jointly developing a new grade of DP28W™ with the aim of further improving the corrosion resistance at the HAZ by optimising the alloying elements and by applying strict microstructural control in the manufacturing process. This will contribute to improved reliability of facilities in urea plants.
Material selection concept for TOYO’s latest ACES21-LP™ process
ACES21-LP™, TOYO’s new generation urea process, has enhanced features such as lowest synthesis pressure, highest CO2 conversion, further energy savings, and lighter weight of high-pressure equipment in the synthesis section1. The amount of passivation air introduced into the CO2 has also been reduced. This requires the risk of active corrosion under such severe conditions to be accurately determined and the appropriate materials to be selected accordingly.
The dissolved oxygen concentration in the urea carbamate solution is at its lowest in the stripper and the operating temperature is at its highest in the synthesis section. Therefore, the stripper has the most corrosive environment in this section. The stripper outlet gas stream is also expected to be extremely corrosive in case it is condensed.
For this reason, it is necessary to select materials with superior passivation properties, specifically DSSs instead of austenitic stainless steels. DP28W™ which has excellent corrosion resistance and is easily passivated even with less dissolved oxygen in ammonium carbamate solution, and is considered the first choice among DSSs.
As previously reported2, TOYO has promoted the application of online corrosion monitoring, called AOCM™ (advanced online corrosion monitoring), in urea plants. TOYO is considering the application of AOCM™ in the synthesis section of ACES21-LP™ to further improve the long-term reliability of the equipment as well as the selection of appropriate materials according to the corrosive environment.
In fact, the application of AOCM™ has already begun in an existing commercial urea plant. As shown in Fig. 3, the wall thickness of a DSS pipe is continuously measured online. It has been demonstrated from the data on the wall thickness that the measurement accuracy of AOCM™ is sufficient for corrosion risk assessment. ACES21-LP™ can be realised without the risk of unexpected severe corrosion through optimising material selection in combination with using AOCM™ .
A more competitive and economical design
The addition of chromium is essential to enhance the corrosion resistance of stainless steels used in urea carbamate solution but it also promotes the precipitation of harmful phases and worsens workability in hot working. In DSSs, the tendency is accelerated when the chromium content is higher than 25%. Especially for large size components, such as thick piping or valves, difficulty in temperature control to avoid precipitation and poor workability lead to low yield rate of products, which results in a higher unit price. Among high chromium DSSs, such negative effects are minimised for DP28W™ by the addition of tungsten instead of molybdenum which keeps its excellent corrosion resistance.
Meanwhile, as a competitive and economical option, TOYO is developing a 25Cr DSS for large components (see Fig. 4), which shows less precipitation and good workability.
References