Nitrogen+Syngas 393 Jan-Feb 2025
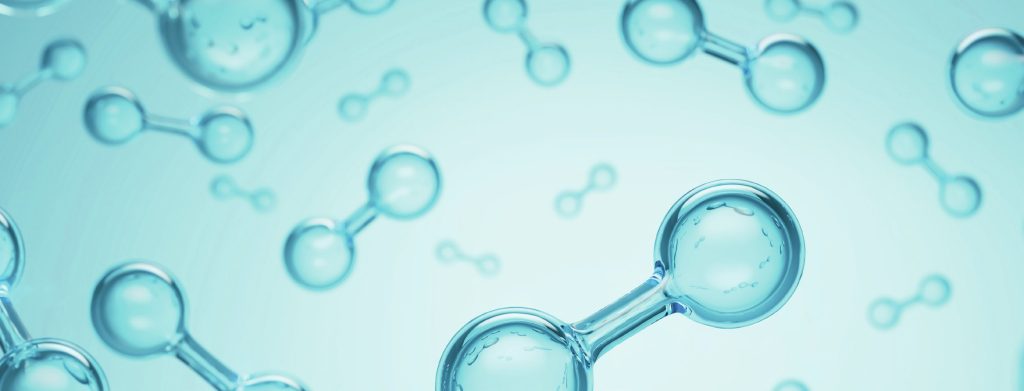
31 January 2025
Blue hydrogen at scale
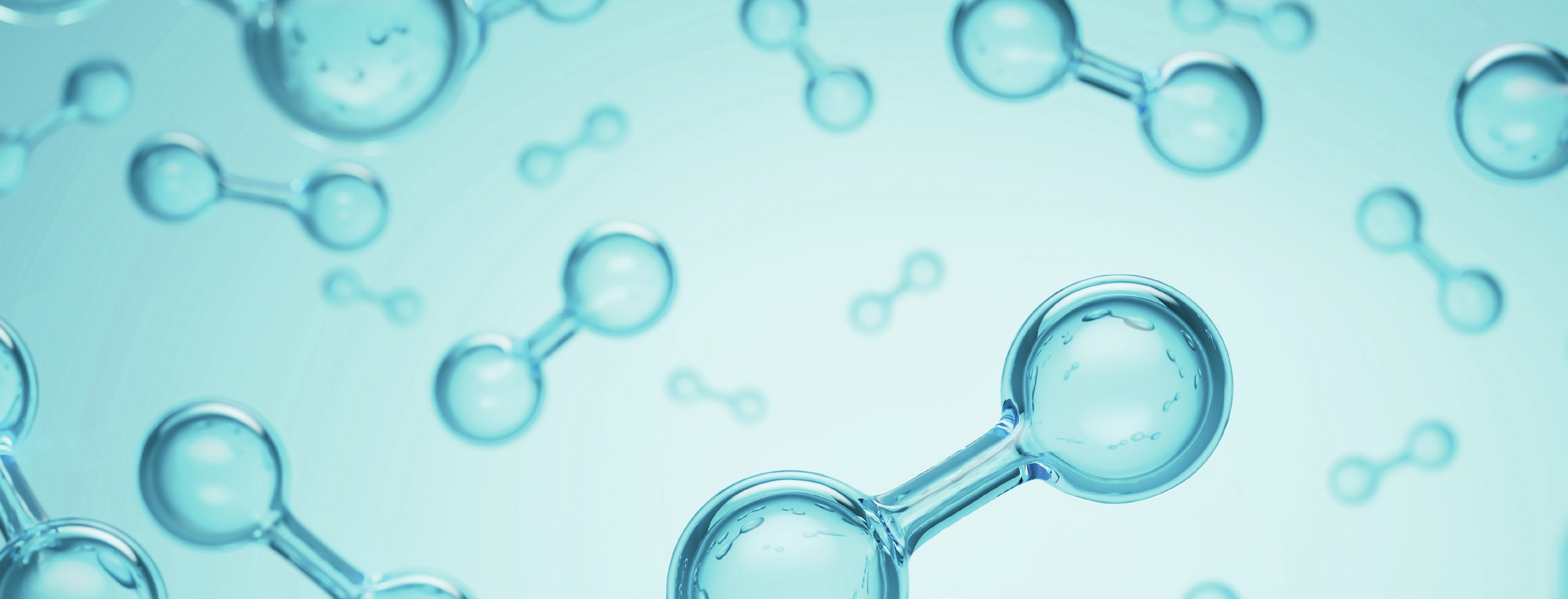
JOHNSON MATTHEY
Strategies and technological solutions for large-scale blue hydrogen production
As nations around the world work towards ambitious net-zero carbon targets, blue hydrogen has emerged as a crucial technology for decarbonisation. Produced from natural gas with integrated carbon capture, utilisation, and storage (CCUS), blue hydrogen offers a scalable solution to reduce emissions across industries while leveraging existing infrastructure.
Hydrogen’s role in decarbonisation
Hydrogen’s versatility makes it indispensable to the energy transition. It serves as a clean energy carrier and feedstock, supporting a wide range of applications from industrial processes such as ammonia and methanol production to energy storage and hydrogen-powered fuel cells for transport. These capabilities enable hydrogen to play a pivotal role in reducing emissions, particularly in hard-to-abate sectors like steelmaking, refining, and heavy transportation.
While electrolytic (green) hydrogen, derived from water electrolysis powered by renewable energy, will play a crucial role in decarbonising our energy mix, its scalability is currently limited by high costs and infrastructure constraints. Blue hydrogen addresses this challenge by utilising well-established natural gas reforming technologies alongside CCUS to produce low-carbon hydrogen at scale. This allows industries to decarbonise today without waiting for renewable energy infrastructure to fully mature.
Advanced technologies for blue hydrogen production
The production of blue hydrogen relies on two primary reforming technologies: steam methane reforming (SMR) and auto-thermal reforming (ATR). Both processes convert methane into hydrogen and carbon dioxide, with the latter captured to minimise emissions.
Johnson Matthey’s LCH™ technology is a leading example of this process. By combining ATR with gas-heated reformer (GHR) technology, LCH technology achieves CO2 capture rates of up to 99% while optimising thermal efficiency. The GHR pre-reforms approximately 30% of the natural gas, reducing methane slip and ensuring high hydrocarbon conversion. Operating at elevated pressures, the system also lowers the energy required for CO2 compression and storage.
Compared to conventional SMR processes, LCH technology consumes 15% less natural gas and reduces operating costs, making it particularly suited for largescale projects where both economic and environmental considerations are critical.
The essential part of the value chain to decarbonise the industry is CCUS systems. These systems separate CO2 from reforming processes using advanced materials like solvents and membranes before compressing it for storage or utilisation. Captured CO2 is typically stored permanently in geological formations, such as depleted oil and gas reservoirs, or used in applications like enhanced oil recovery and building materials production.
In the HyNet initiative, one of the UK’s first blue hydrogen projects developed by a consortium including Vertex Hydrogen, CCUS plays a central role. At the Stanlow Manufacturing Complex, hydrogen will be produced using JM’s LCH technology, which enables CCUS. The captured CO2 will be transported via pipelines to Liverpool Bay for permanent storage. This project demonstrates how integrating CCUS with blue hydrogen production can significantly reduce regional emissions.
Infrastructure and hydrogen hubs
One of blue hydrogen’s most significant advantages is its compatibility with existing natural gas infrastructure. Pipelines, storage systems, and industrial facilities can be repurposed to transport and store hydrogen, minimising upfront capital costs.
HyNet exemplifies this approach by integrating hydrogen production with a robust distribution network. The project repurposes salt caverns in Cheshire to store up to 35,000 tonnes of hydrogen, ensuring supply reliability while balancing energy demand. Such regional initiatives create hydrogen hubs where production, distribution, and consumption are concentrated, driving economies of scale and fostering collaboration.
H2H Saltend, developed by Equinor and utilising JM’s LCH technology, is another notable example. This 600 MW facility blends low-carbon hydrogen into natural gas supplies, reducing emissions at the Saltend Chemicals Park – 0.9 million tonnes of CO2 per year will be captured and transported through the proposed Humber Low Carbon pipeline to the Northern Endurance Partnership (NEP) storage facility. By supporting industrial operations and energy generation, the project illustrates the scalability and versatility of blue hydrogen in meeting decarbonisation goals.
Economic viability and policy support
Scaling blue hydrogen production requires addressing economic challenges. Government support is essential to bridge this gap. Incentives like carbon pricing, subsidies, and contracts for difference (CfD) stabilise revenue streams, encouraging investment in large-scale projects.
Public-private partnerships, such as those underpinning HyNet, enable resource sharing and risk mitigation, aligning industry efforts with national climate policies. Clear and consistent regulatory frameworks are also crucial. For example, standardised hydrogen certification systems and emissions accounting rules help create a stable market environment that fosters investor confidence.
Efficiency is central to blue hydrogen’s competitiveness. Innovations in catalyst design and heat recovery systems are reducing the energy intensity of production processes. LCH technology exemplifies this by recovering heat generated during reforming processes, optimising thermal efficiency and lowering operational costs.
The integration of renewable energy further enhances sustainability. Renewable electricity can power auxiliary systems, such as compressors and preheaters, reducing the carbon footprint of blue hydrogen production. These measures align blue hydrogen with broader decarbonisation goals while ensuring its cost-effectiveness in a competitive energy market.
Conclusion
Blue hydrogen provides an immediate and scalable solution for decarbonising industries while supporting the transition to a low-carbon economy. As demonstrated by initiatives like HyNet and H2H Saltend, regional hydrogen hubs are key to accelerating adoption and creating sustainable industrial ecosystems. By integrating advanced technologies as used in the LCH technology, leveraging existing infrastructure, and aligning with supportive policies, blue hydrogen can deliver significant emissions reductions across critical sectors.
In the next edition of Nitrogen+Syngas Johnson Matthey will explore the use of its LCH technology in the production of blue ammonia.
TOPSOE A/S
Unleashing the power of low-carbon hydrogen
According to the International Energy Agency (IEA), hydrogen production contributes to a staggering 830 million tons or 3% of global CO2 emissions annually. This highlights the urgent need to decarbonise hydrogen production. However, the potential of hydrogen extends far beyond reducing emissions in its own production process. It can also serve as a preferred energy carrier, decarbonising multiple sectors, either in its pure form or as converted into ammonia. The Hydrogen Council estimates that hydrogen production will increase eight to ten times by 2050, underscoring the critical importance of decarbonising hydrogen production.
Traditionally, hydrogen is produced through steam methane reforming using fossil-based feedstocks like natural gas, LPG, or naphtha. This type of hydrogen production without CO2 capture is known as “grey hydrogen”. To address this, one promising approach to decarbonise hydrogen production is through water electrolysis powered by renewable energy. The resulting hydrogen is completely green, leaving no CO2 footprint throughout its production and use. Companies like Topsoe have successfully commercialised electrolysis solutions that can be used as standalone hydrogen units or in hybrid setups, combining them with traditional hydrogen production. However, a major challenge in deploying green hydrogen at a large scale is the limited availability of renewable power capacity.
To unlock the full potential of hydrogen in reducing CO2 emissions, it is crucial to supplement green hydrogen with other clean hydrogen sources known as “low-carbon hydrogen” often referred to as “blue hydrogen.” Low-carbon hydrogen can be produced by integrating traditional production methods with innovative clean technologies. This can involve revamping existing grey hydrogen plants or constructing new low-carbon hydrogen plants from scratch.
By decarbonising hydrogen production and exploring a range of clean hydrogen sources, we can fully harness the potential of hydrogen in the global energy transition, leading to significant reductions in CO2 emissions. This article presents options to further optimise the existing low carbon hydrogen technology to increase natural gas efficiency, reduce cost and increase CO2 capture even further.
SynCOR™ reforming
SynCOR™ reforming is an advanced auto-thermal reforming process, but unlike other ATR processes, SynCOR™ operates at a significantly lower steam-to-carbon ratio and takes place within a single reactor. In the SynCOR™ reactor, process gas enters and combines with oxygen and additional steam, undergoing combination of oxygen combustion and steam reforming simultaneously.
Among the various low-carbon intensity (CI) hydrogen technologies, the SynCOR™ process demonstrates the lowest opex. Its steam-to-carbon ratio of 0.6 is 3-5 times less than SMR or conventional ATR systems, meaning smaller equipment and piping sizes, which is particularly advantageous at larger scales where standard size ranges can be maintained even at high capacities.
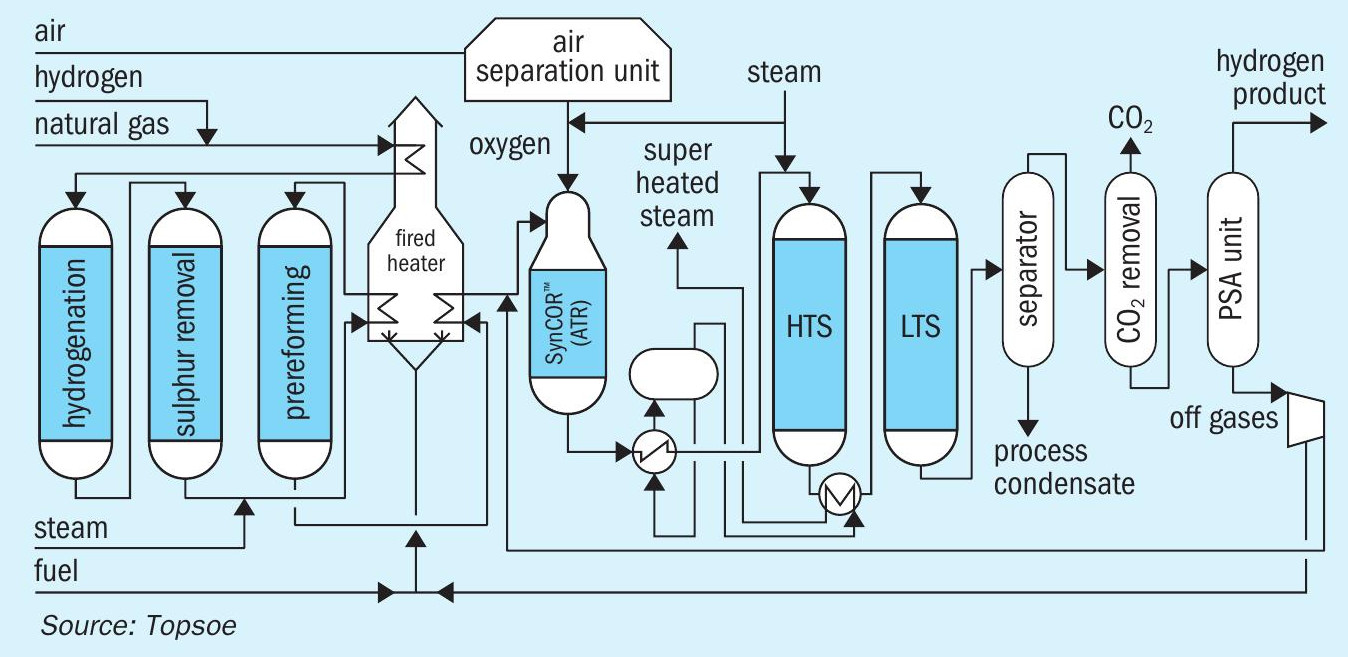
External fuel demand is exceptionally low, enabling a high carbon-recovery rate of over 99% inside the process plant without the need for capturing carbon in the flue gas. This makes SynCOR™ highly suitable for low-carbon hydrogen production, and for deployment in mega-scale plants.
Topsoe’s SynCOR™ technology has undergone 70 years of development, with the first generation SynCOR™ (ATR) released in 1958. Subsequently, Topsoe has developed a second generation SynCOR, which operates at low S/C ratio. Since then, many large capacity plants have been set up using SynCOR™ for the different applications, such as GTL (gas-to-liquid), TIGAS™ (natural gas to gasoline), syngas. Topsoe SynCOR™ has gained over 300 years of cumulative operational experience, which makes it the most mature technology for low-carbon hydrogen and low-carbon ammonia projects. Currently, the largest operational SynCOR™ reactor produces 510 kNm3 /hour of hydrogen, with a single-train capacity limit of 825 kNm3 /hour.
Topsoe can integrate the hydrogen plant with numerous globally recognised CO2 capture technologies to achieve the ultra low-carbon hydrogen at low cost of production.
SynCOR™ without fired heater
In some cases, the target product of a plant is fuel-grade hydrogen which may contain limited amounts of contaminants such as N2, CO, and CH4. As no final hydrogen purification is needed, this simplifies the overall process by avoiding the cost intensive PSA unit. On the other hand, no PSA off-gas is available as fuel for fired heaters. This fuel could then come from either imported natural gas or by increasing the size of the plant and use the product hydrogen as fuel.
An alternative is to avoid the use of fuel entirely by not including fired heaters in the process lineup. Such a process is illustrated schematically in Fig. 2. The required preheating for the individual units is carried out by using steam as the heating medium. All reactors can easily accept a wide range of feed temperatures.
The advantage of this layout is low capex and especially a higher efficiency and consequently a lower opex. Furthermore, essentially all CO2 formed in the plant may be captured from the process gas as there are no flue gas emissions.
The product contains minor amounts of CO and CH4 which will be converted into CO2 when the fuel grade hydrogen is combusted. These carbon molecules in the product hydrogen are also considered as part of the CO2 emission. In Table 1, a comparison of key parameters for a fuel grade hydrogen plant is provided with and without fired heaters for a case study for production of 200,000 Nm3/hr of fuel grade hydrogen. In both cases no PSA is used. The advantage of not including fired heaters in the plant is evident both from an opex and capex perspective. The oxygen consumption is as expected higher in the case without fired heaters due to the lower preheat temperature to the SynCOR™ ATR reactor. However, in this case, this is more than offset by the reduced natural gas consumption and lower capex with a net result of a lower levelised cost of hydrogen.
The SynCOR™ for production of low-carbon hydrogen offers both low capex and opex as well as high utilisation of the feedstock with corresponding very low CO2 emissions per unit of hydrogen produced. The SynCOR™ solution is already the technology with the highest reformer efficiency compared to market alternatives. However, building upon this platform, an alternative solution with an even higher efficiency has been developed by Topsoe.
The process solution is illustrated in Fig. 3. The scheme combines the SynCOR™ technology with a heat exchange reformer (HTER-s) upstream and in series with the autothermal reformer (ATR). The HTER-shas been developed utilising the basis of a number of other Topsoe heat exchange reformers which for decades have been in operation for example in hydrogen, synthesis gas and ammonia plants. These heat exchange reformers have been developed to operate at aggressive conditions to minimise capital and operating costs while still avoiding metal dusting. In a similar fashion, the novel HTER-s has been designed to operate at relatively low steam-to-carbon ratios compared to alternatives thus reducing the size and duty of the reactor. The new SynCOR™ solution with HTER-s also enables very high carbon recovery rates in excess of 99% inside hydrogen plant.
A comparison of the key parameters for a case of production of blue hydrogen with and without HTER-sis provided in Table 2.
Table 2 illustrates that the introduction of HTER-s enables even further optimisation of the SynCOR™ scheme for production of blue hydrogen. The efficiency is higher while the oxygen consumption, the CO2 emissions, and the capex are all reduced. The net result is a reduction of the levelised cost of hydrogen from what is already a small number.
eREACT™ in low-carbon hydrogen production
Another approach is to use electrified reactor technology known as eREACT™ for steam methane reforming for example for production of low-carbon hydrogen. In this approach, the steam reforming reactions take place within a catalytic reactor heated by power preferable from renewable sources. This eliminates the need for hydrocarbon fuel as a heat source thus avoiding flue-gas emissions from the reformer. The energy density of the eREACT ™ process allows for a significantly smaller reactor size compared to traditional SMR units. The eREACT™ process is mostly targeted towards low and moderate low-carbon hydrogen production at sites where adequate renewable power is available.
Almost all of the CO2 formed in an eREACT™ based process can be economically recovered using a CO2 removal unit. More than 99% of the CO2 can be captured making eREACT™ an excellent choice for low-carbon hydrogen production in scenarios where electricity prices are favourable. The eREACT™ based process has been successfully demonstrated and is currently under commercialisation in a number of plants.
eREACT™ offers a significant advantage in energy efficiency, enabling a 30-40% reduction in natural gas consumption for hydrogen production compared to traditional SMR, which is achieved through the high efficiency of the eREACT™ technology. This makes eREACT™ a highly efficient electric reforming technology.
Conclusion
The SynCOR™ technology with the high single line capacity and carbon recovery in combination with the lowest opex and capex is unmatched by other solutions for production of low-carbon hydrogen. The proven track record with SynCOR™ at high capacities makes it an ideal choice for low-carbon intensity hydrogen production. Nevertheless, Topsoe has continued to develop and optimise solutions for decarbonisation at scale. The new technologies together with SynCOR™ will provide an even stronger suite of solutions for meeting different requirements in the market.
eREACT™ is pushing this innovation step even further, by taking a leap into electrification of low and moderate capacity low-carbon hydrogen production with the help of renewable power.
The new technologies have been presented for production of low-carbon hydrogen. However, all the described solutions are ideally suited also for production of synthesis gas for a range of fuels and chemicals synthesis such as ammonia and methanol. Many such plants based on SynCOR™ are in operation today at high capacities and the new solutions will also be employed to produce low-carbon methanol and ammonia.
CASALE
ROX® by Casale: Redefining low-carbon hydrogen production
As global initiatives to mitigate climate change intensify, hydrogen has emerged as a cornerstone of the transition to a low-carbon economy. Among the various hydrogen production methods, blue hydrogen – derived from hydrocarbon feedstocks with integrated carbon capture and storage (CCS) – has gained significant attention due to its potential to serve as a cleaner energy source while leveraging existing fossil fuel infrastructure.
The ROX® process
Casale, with over a century of experience in the design, licensing, and provision of proprietary equipment for syngas plants producing ammonia and methanol, has integrated its most advanced technologies into a cutting-edge flow scheme that addresses the stringent requirements of ultra-low-carbon blue hydrogen production for the energy transition:
- Casale’s auto-thermal reforming (ATR) technology generates hydrogen through oxidative reforming, forming the cornerstone of the ROX® flow scheme.
- Technip Energies’ Technip Parallel Reformer® (TPR) provides supplementary reforming, eliminating the need for external steam export by utilising recuperative reforming.
The combination of ATR and TPR technologies forms the foundation of the ROX® (Recuperative OXidative Reforming) scheme, offering a scalable solution with exceptional operational flexibility.
Key features and advantages
The ROX® scheme boasts a hydrogen production capacity of up to 600,000 Nm³/h (2 GW) in a single train and supports customisable carbon capture rates of up to 99%, achieving a carbon intensity of less than 0.1 kg CO2 per kg of hydrogen (Scope 1).
The process can be tailored to meet each client’s specific needs based on factors such as decarbonisation goals, feedstock availability, and operational requirements. By optimising design parameters, ROX® achieves the lowest possible levelised cost of hydrogen (LCOH).
Hydrogen and syngas generation
Hydrogen plays a pivotal role in refining and chemical processes. Steam methane reforming (SMR) has long been the dominant method for converting fossil feedstocks, such as natural gas and refinery fuel gases, into high-purity hydrogen at capacities ranging from a few thousand Nm³/h to over 250,000 Nm³/h.
When aiming to expand capacity and/ or reduce carbon emissions, an ATR-based plant offers a superior solution, providing higher conversion efficiency and facilitating near-complete CO2 capture. This technology is already widely used in various industrial applications, including ammonia and methanol production, gas-to-liquid processes (e.g., Fischer-Tropsch), and oxo-processes (e.g., hydroformylation). It is now gaining increased relevance due to the evolving targets driven by the need for energy transition.
Innovative process flow
Fig. 1 shows a schematic flow 10 diagram of the ROX® process. The main steps are outlined below:
Feedstock preparation and pre-reforming
- Primary feedstocks, such as natural gas or higher hydrocarbons, undergo pretreatment to remove impurities (e.g., sulphur, chlorine, and mercury).
- The pretreated feed is introduced into a pre-reformer, where higher hydrocarbons are converted into methane. This stage enhances operational safety by minimising coking risks and allows for higher preheating temperatures, lower steam-to-carbon (S/C) ratios, and reduced oxygen consumption. The pre-reformer reactor with axial-radial design (Fig. 2) is one of the technologies available in Casale’s portfolio and has 9 industrial references.
Reforming section
- The primary feed gas is preheated in a fired heater designed specifically for Casale’s ATR process.
- In the ATR reactor, feed gas and oxygen are mixed in a turbulent diffusion flame, enabling optimal combustion and catalytic reforming. The proprietary water-cooled ATR burner ensures stable performance and extended equipment lifespan.
- The TPR reactor operates in parallel with the ATR, further reforming the gas and using heat recuperation to achieve efficient methane conversion and balanced steam generation.
Shift conversion and CO2 capture
- The syngas passes through high temperature shift (HTS) and low temperature shift (LTS) reactors to maximise hydrogen production. These technologies are available with Casale axial-radial flow path, with more than 40 reactors in operation.
- Heat recovery from exothermic reactions supports steam generation, while CO2 is separated using amine-based absorption or cryogenic fractionation, depending on the plant’s design and size.
Hydrogen purification
The purified hydrogen stream, with a purity exceeding 99.9%, is ready for industrial applications. CO2 captured during the process can be compressed and transported for sequestration or utilisation.
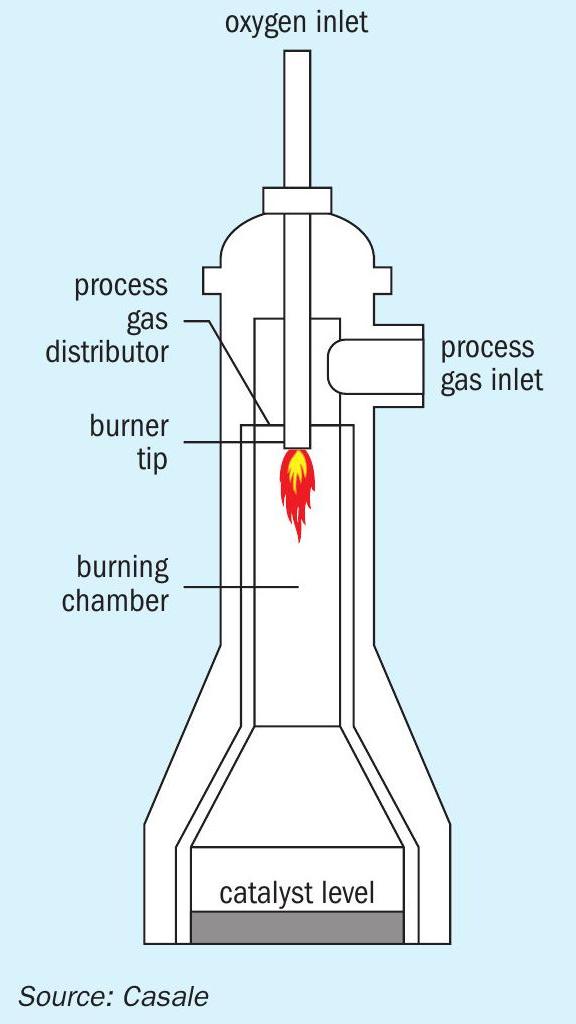
Technical differentiators
Auto-thermal reforming (ATR)
Casale’s ATR design incorporates a refractory-lined pressure vessel and proprietary water-cooled burners. The system ensures uniform temperature distribution, enhancing catalyst performance while mitigating thermal stresses (Fig. 3).
- Proven operation across 15 industrial plants with capacities ranging from 30,000 Nm³/h to 630,000 Nm³/h.
- Soot-free combustion and an advanced fluid dynamics design prevent refractory hot spots and maximise catalyst longevity.
- Patented water-cooled burner that assures solid performance, safe operation and a lifespan of more than ten years, as demonstrated in the industrial references (Fig. 4).
Performance benchmarks
Compared to traditional SMR and standalone ATR schemes, the ROX® flow scheme demonstrates significant efficiency improvements, as shown in Table 1 for a case study for a 590 MW HHV hydrogen plant.
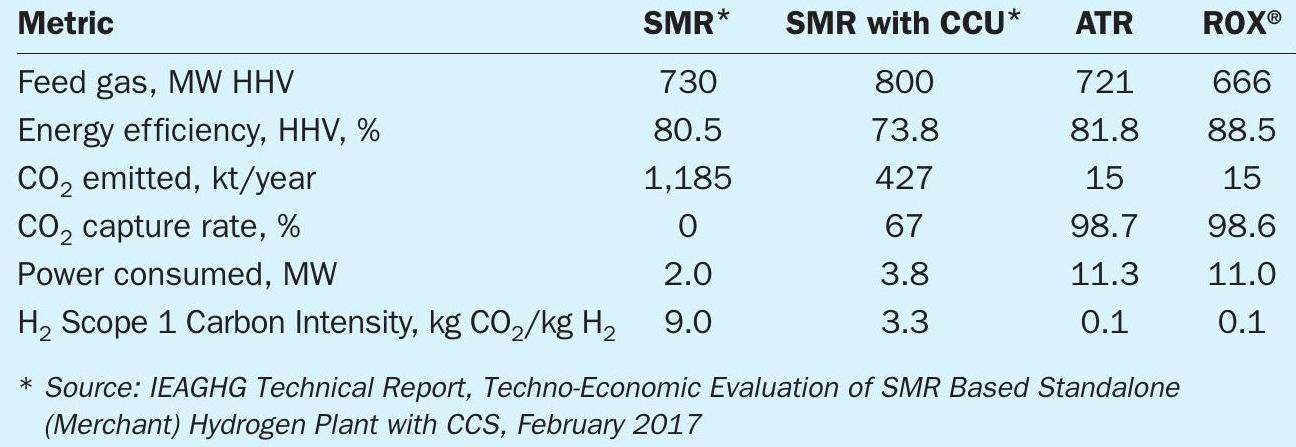
Key highlights:
- 25% reduction in oxygen demand compared to standalone ATR processes, lowering air separation unit (ASU) costs and power consumption;
- 6% feed gas savings;
- near-zero CO2 emissions from flue gases, achieved through low-carbon fuel utilisation and PSA purge gas recycling.
Sustainability and scalability
The modular design of the ROX® process enables rapid deployment and seamless integration with renewable energy sources, further reducing carbon intensity. By combining proven technologies with innovative flow schemes, Casale delivers a robust solution for blue hydrogen production, supporting global decarbonisation goals.