Sulphur 416 Jan-Feb 2025

31 January 2025
Decarbonisation in the sulphuric acid industry
DECARBONISATION
Decarbonisation in the sulphuric acid industry
New concepts focused on the transfer and combination of existing sulphur and sulphuric acid technologies to support decarbonisation of the sulphuric acid industry are being investigated. In this article three research projects are discussed: sulphur dioxide depolarised electrolysis for green regeneration of spent acid, use of renewable heat and catalyst to the splitting process from sulphuric acid to SO2 for reduction of fossil fuel consumption, and sulphur as an energy vector.
Dimitrios Dimitrakis, Dennis Thomey, Christian Sattler (DLR German Aerospace Center) Martin Kuerten, Jonas Michels (GRILLO Chemicals GmbH)
Industry is seeking new concepts and ideas to reduce the use of fossil energy sources in favour of renewable energy like green electricity and solar energy. The sulphuric acid industry has the possibility to contribute to this goal with new technology approaches. Grillo Chemicals, a sizable player in the European fresh and spent acid market, together with the research centre Deutsches Zentrum für Luft- und Raumfahrt (DLR), and other research institutes are part of an international consortium working on different research projects. The projects focus on the transfer and combination of existing technologies with new ideas, applying innovative concepts to established sulphur and sulphuric acid technologies. The main objective of this article is to present these approaches and broaden the outlook for possible synergies and new opportunities. While the approaches discussed are R&D projects, there are already very promising results for steps towards commercial implementation.
Sulphur dioxide depolarised electrolysis
Research project EU-HySelect1 for green regeneration of spent acid focuses on the implementation of sulphur dioxide depolarised electrolysis (SDE) in a sulphuric acid recycling plant. SDE is a modified water electrolysis concept producing hydrogen and sulphuric acid out of SO2 and water. In this electrolysis, sulphur dioxide and water form sulphurous acid, which is used to depolarise the anode. Sulphuric acid is produced yielding two protons and two electrons, which pass through the electrolyte separator and are conducted via an external circuit respectively, towards the cathode, where they are recombined forming hydrogen. This requires electrical power with a theoretical cell potential of only 0.17 V corresponding to about 14% of conventional water electrolysis exhibiting a theoretical voltage of 1.23 V2 .
Fig. 1 shows a schematic representation of sulphur dioxide depolarised electrolysis.
The sulphur dioxide depolarised electrolyser has the potential to significantly reduce the amount of electrical power required compared to conventional water electrolysis and offers promising effects for hydrogen production, especially in an industrial context. So far, reported experimental SDE electrolysers are cloned from water PEM stacks, consisting of two electrodes and a proton exchange membrane, which allows H + ions to pass through, similarly to PEM fuel cells. The electrode active layers are usually made of carbon-supported platinum catalysts. In this configuration, reasonable potentials (0.7 to 0.9 V) might be obtained at current densities 0.2 to 0.4 A/cm2 at 60-80°C, however SO2 carryover through the PEM membrane leads to its reduction to elemental sulphur (Pt catalyses this reaction) and parasitic losses, reducing SDE performance in terms of hydrogen produced. This decreases the reliability of the process as frequent cleaning of the system is required and formed sulphur needs to be properly disposed of.
Current efforts are aimed at tackling engineering challenges in terms of SO2 carryover, corrosion resistance and industrial scale-up of the process. These efforts focus on the development of catalysts, membranes and membrane electrode assemblies (MEAs), without the use of critical materials (Pt or Pd), such as Au, and a significant decrease of SO2 crossover, as is the case for polybenzimidazole (PBI) membranes. The experimental SDE setups developed in DLR are designed to guide the jump from the lab-scale SDE unit to a 30 to 40 kWel pilot unit electrolyser, which is planned for installation in the premises of Grillo.
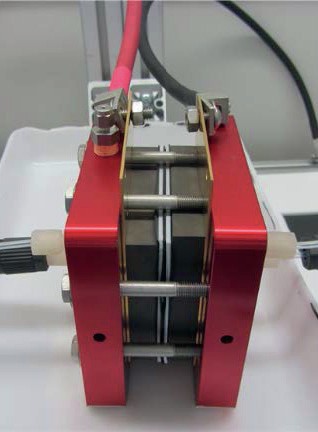
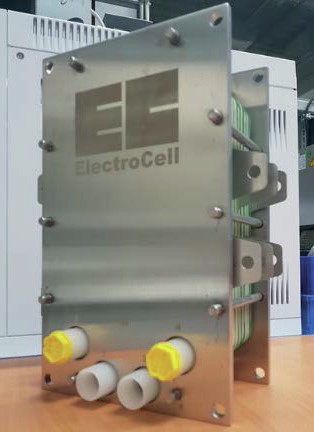
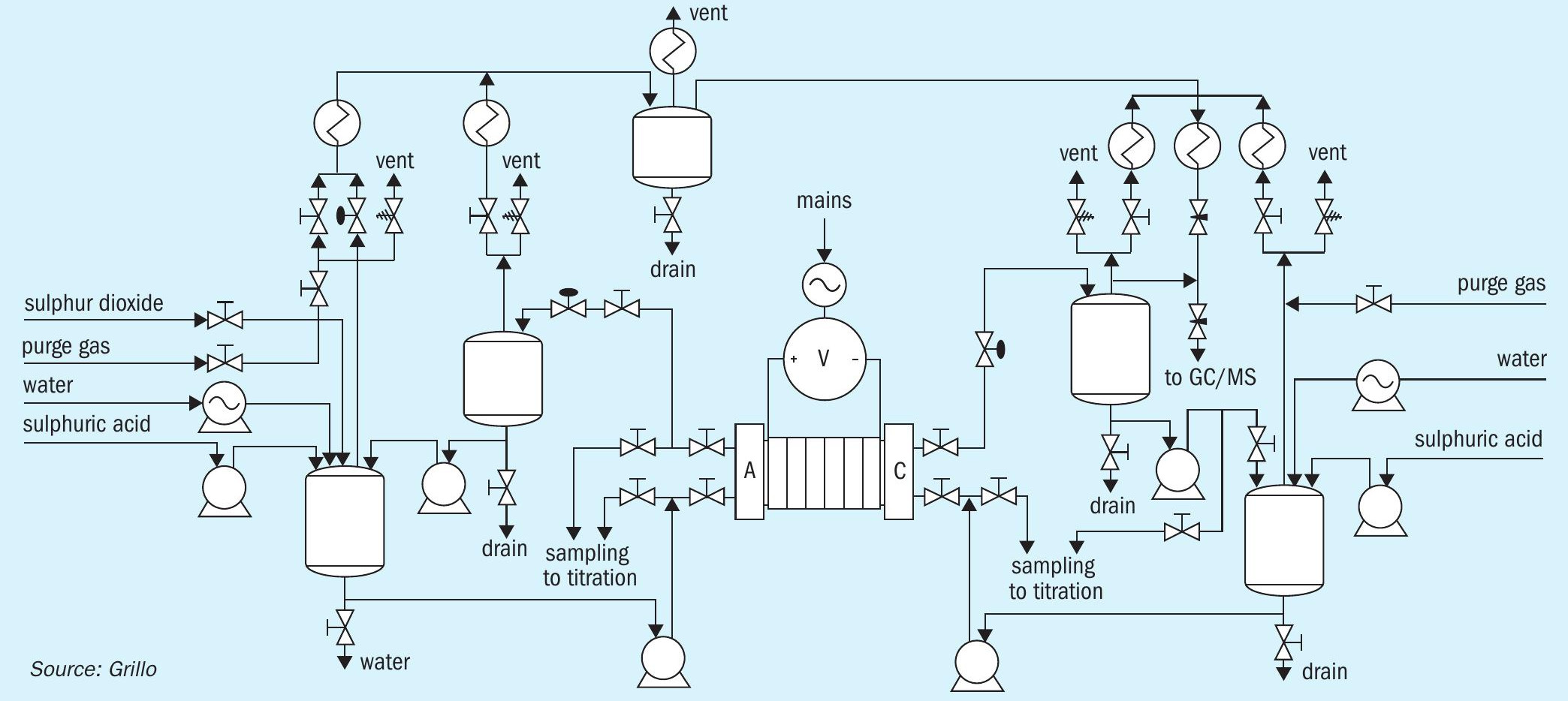
Fig. 2 shows the cell and stack for SDE in the experimental setup at DLR and Fig. 3 is a block flow diagrams of the SDE experimental setup at DLR.
Produced hydrogen can easily be used for thermal processes, i.e. the combustion of spent sulphuric acid in recycling processes as in Fig. 4. Numerous possible implementations in other industrial processes exist, where SO2 is a waste stream that cannot be directly converted to sulphuric acid, for example, applications within sulphuric acid production with a sulphur burner, in the non-ferrous metal industry and in fertilizer production.
Sulphuric acid splitting
Another research focus towards a circular economy is the improvement of the splitting process from sulphuric acid to SO2. The use of catalysts to lower the required temperature of the splitting reaction and the use of renewable heat in the thermal process for reduction of fossil fuels consumption are promising options. Renewable heat can be supplied to the process via concentrating solar technologies (e.g., heliostat field and solar tower) or via options for renewable heat storage (latent heat or chemical energy storage).
Catalytic sulphuric acid splitting
Sulphuric acid splitting (SAS) is the sum of the thermal dissociation of sulphuric acid (H2SO4) first to water (steam) and sulphur trioxide (SO3 ) and the subsequent catalytic dissociation of SO3 to sulphur dioxide (SO2) and oxygen (O2). These two reactions, sulphuric acid decomposition (SAD) and sulphur trioxide splitting (STS), are performed experimentally in combination: concentrated sulphuric acid from a reservoir is vaporised and driven first through a medium-temperature zone where its stoichiometric dissociation into steam and SO3 takes place; the vapour mixture is then passed through the catalytic reactor at higher temperatures where the STS reaction is performed.
With respect to catalytic materials for SO3 splitting, if expensive PGM-based catalysts are to be avoided, the next best possible solution is single or mixed oxides of abundant transition metals5,6,7 . Indeed, many studies, have demonstrated that certain metal oxide compositions can ensure catalytic activity quite close to that of Pt/ Al2O3 benchmark catalysts8,9 . Such state-of-the-art oxide catalytic phases with, in principle, long-term stability (≥500 h) as well as limited deactivation (2-7%) as evaluated by lab- and pilot scale reactors (Fig. 5) include principally iron oxide (Fe2O3) or CuO-based compositions10,11,12. These oxides require temperatures of 800-900°C at 1 atm to achieve conversions close to equilibrium. Formation of stable sulphates is a common problem for both oxides and noble metals supported on oxides. Deactivation of metal oxides due to sulphate formation becomes more significant at lower reaction temperatures. Metal vanadate-based catalytic formulations suitable for lower temperature SO3 splitting catalysis, i.e. ≤ 650°C have been proposed, specifically, Cu-V based catalysts13 and (partially) molten phase vanadates14.
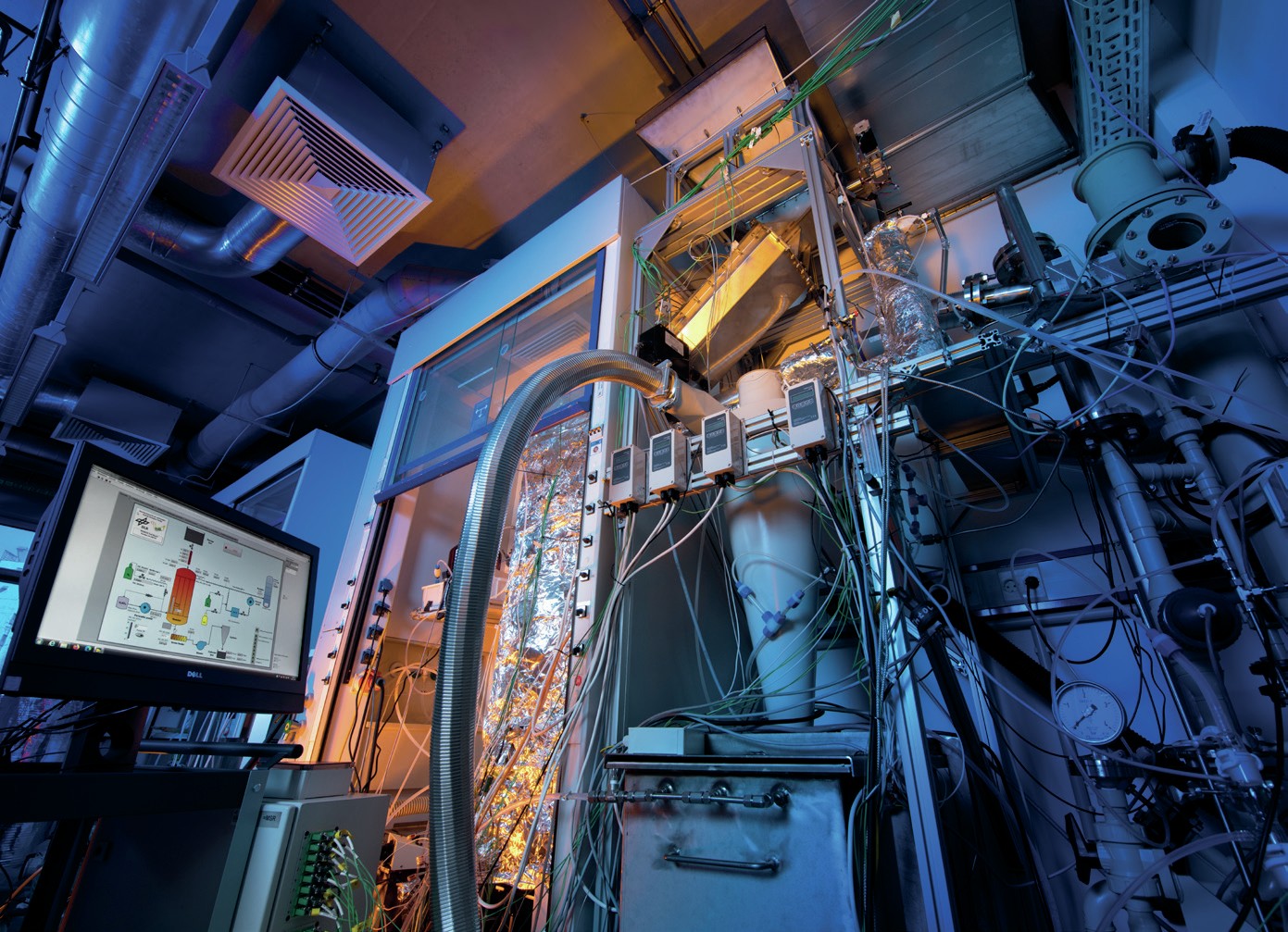
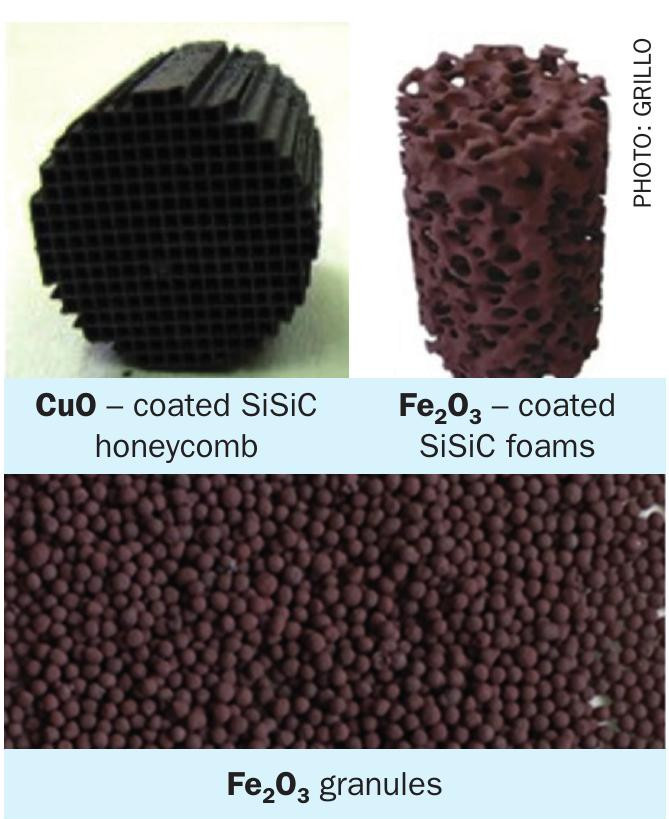
Sulphuric acid splitting with renewable heat
The high-temperature endothermic reaction of the catalytic sulphuric acid splitting can be driven with renewable heat in so-called allothermal reactors (Fig. 7). This term was first coined by the nuclear energy research community to exploit the high temperature (in the range of 900°C) of the helium gas stream from nuclear very high temperature reactors (VHTRs)19. In an allothermal SAS reactor, a heat transfer fluid (HTF), is heated and then is fed to the reactor featuring a shell-and-tube heat exchanger design. The HTF flows downwards on the shell side supplying the necessary heat for the STS reaction in the upper part of the reactor and for the SAD reaction in the lower part. On the tube side, rising sulphuric acid vapours come into contact with a non-moving catalytic bed containing the catalyst in various structured forms like granules, pellets, honeycombs or foams15,20, as already presented in Fig. 6.
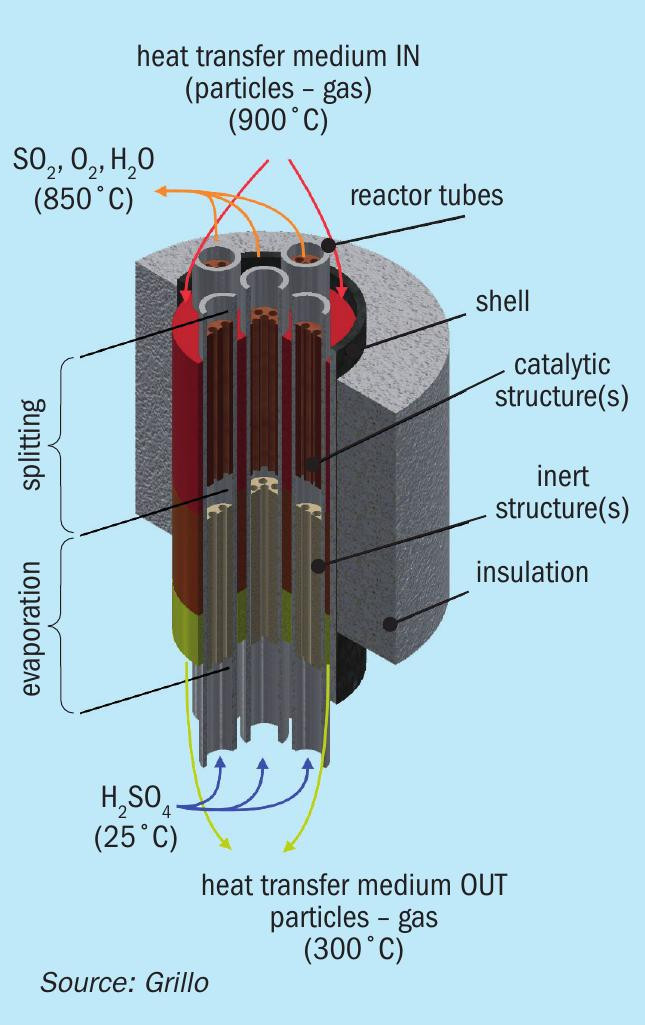
Obviously, for such an operation, the HTF should be heated via renewable heat to a temperature exceeding the temperature required for STS (850 to 900°C). This can be accomplished with different approaches in a sustainable way. Concentrating solar technology (CST) systems come into play as a means to supply high-temperature renewable heat as the necessary energy source for the performance of this endothermic step, specifically CST tower plants2,22,23. Two such solar receivers for towers developed recently, capable of reaching the required temperature for SAS (and above) with a very promising commericalisation potential are shown in Fig. 8. The first is a centrifugal receiver developed by DLR utilising ceramic (bauxite) particles that reached a temperature of 950°C24,25. The second, developed by the company Synhelion, is based on direct absorption of thermal radiation by a gaseous HTF, similar to the well-known greenhouse gas effect26 that can reach temperatures in the range of 1,500°C. In the former, particles can be used to sensibly store solar heat in a hot storage system (tank); the latter is also coupled to a porous solid thermal energy storage (TES) system. Thus, both can be employed also off-sun to thermally drive the SAS reaction in cases of either diurnal solar radiation interruption or overnight, guaranteeing SO2 production. Alternatively, a third non-solar option for driving the SAS reaction with renewable heat (Fig. 8 right) could be by using latent heat, stored by a technology such as SiBox provided by company 1414°. In this case the latent heat storage module is charged with low-cost renewable energy when prices are low and stores it as heat in a silicon storage media. It can then consistently provide high-temperature air up to 900°C to the downstream SAS process.
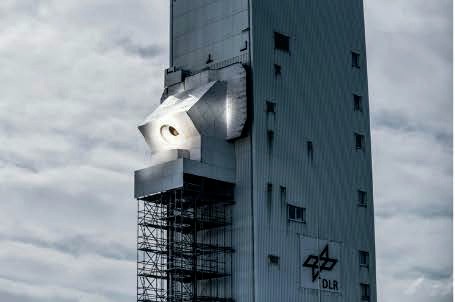
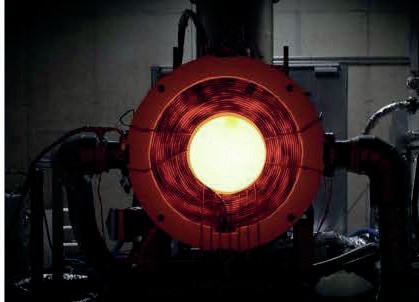
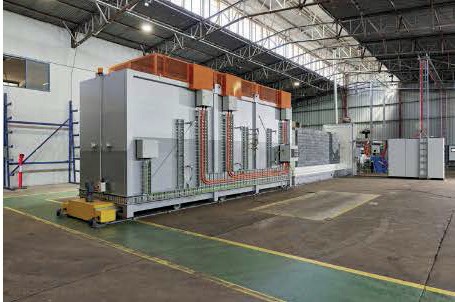
The hybrid sulphur cycle
An interesting approach is the combination of the above-mentioned steps, the SDE with the catalytic splitting of sulphuric acid in (allothermal) reactors driven by renewable (e.g. solar) heat. The combination of both steps in a single process is called the hybrid sulphur (HyS) cycle, as presented in Fig. 9, originally proposed in 197523 and developed by Westinghouse Electric corporation. The process is called hybrid because of the combination of the thermal decomposition of sulphuric acid with the electrochemical oxidation of SO2 with water (electrolysis) to yield hydrogen and re-generate sulphuric acid which is completely recycled in the process.
The HyS cycle is one of the most promising water-splitting (WS) thermochemical cycles (TCs) which combined with concentrating solar technologies (CST) has an inherently much higher theoretical efficiency potential than e.g., photocatalysis. Thermochemical water splitting cycles are a series of consecutive chemical reactions, their net sum being the splitting of H2O to H2 and O2. DLR and GRILLO are investigating the experimental demonstration of the HyS cycle within the EU-funded project HySelect, with planned operation of the demo plant in 2026. A schematic of the proposed plant is shown in Fig. 10.
Sulphur as an energy vector
A further project, albeit with a lower technology maturity, opens up opportunities for sulphur as an energy vector in order to overcome the disadvantages of hydrogen. Instead of storing hydrogen it is possible to convert the produced SO2 from sulphuric acid splitting with a downstream disproportionation reaction into elemental sulphur and sulphuric acid (Fig. 11). The renewable heat stored in the form of elemental sulphur is simple to store and to transport and ready to be used as an industrial energy carrier, dispatchable and on-demand when the energy is needed. DLR is investigating this so-called solid sulphur (SoSu) cycle with an international consortium in the EU-funded project Sulphurreal31. The project sets forth an innovative approach for thermochemical direct storage of concentrated solar irradiation harvested energy to solid elemental sulphur, a very energy-rich chemical to be used both as a chemical energy vector and seasonal storage medium for solar thermal energy as well as a renewable carbon-free source for power or high temperature heat generation. The concept is a combination of three major process steps, namely the decomposition of H2SO4 (as described in the previous sections), SO2 disproportionation and elemental sulphur combustion, as originally proposed by General Atomics31.
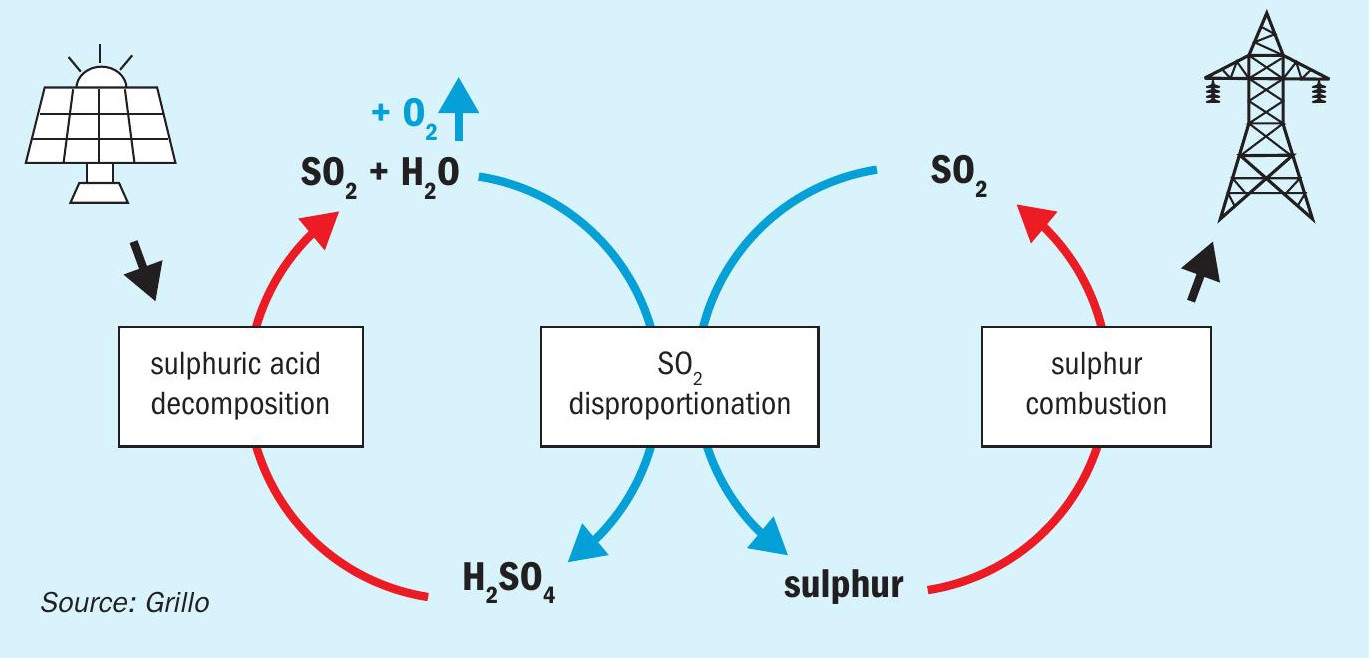
The solid sulphur cycle is a combination of the same sulphuric acid splitting reaction, followed by the disproportionation of SO2 into elemental sulphur (S) and H2SO4. Elemental sulphur can then be combusted in air on demand to produce high-temperature heat and SO2. The SO2 from combustion can be converted back into H2SO4 to close the cycle via industrially established processes. The reactions of the SoSu cycle are summarised in Table 3.
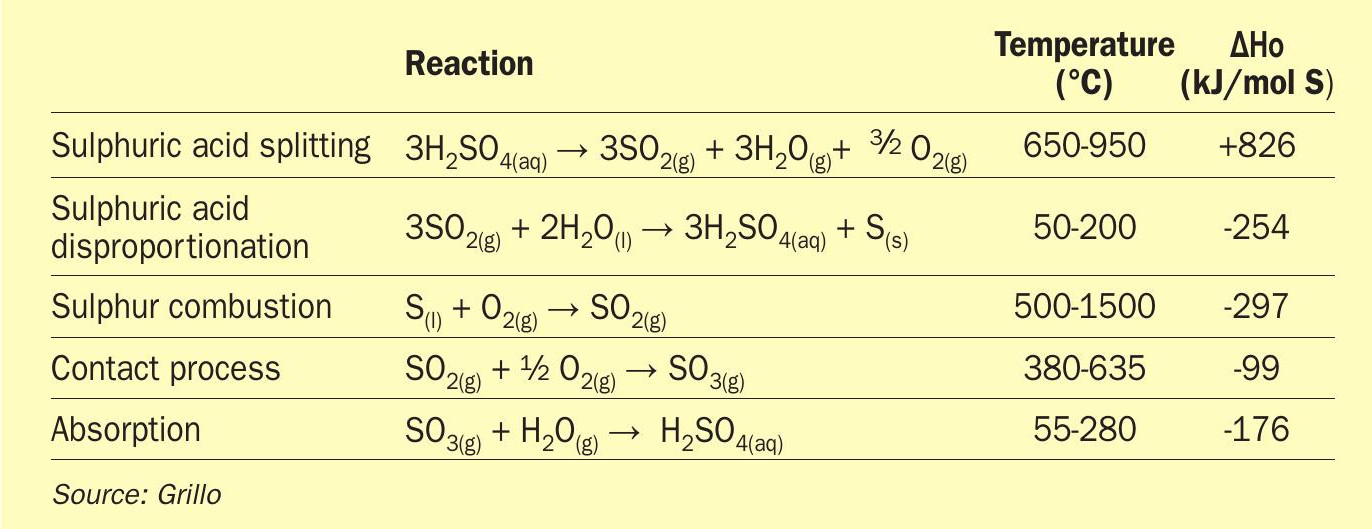
Outlook
Three approaches have been presented (sulphur dioxide depolarised electrolysis, catalytic sulphuric acid splitting, sulphur as an energy vector) that are being actively pursued as viable add-on or supplementary technologies to existing industrial operations. These approaches carry great promise for a meaningful next step in decarbonisation of the industry by using sulphuric acid technology.
References
Acknowledgments
The authors wish to acknowledge Project EU-HySelect. This project is supported by the Clean Hydrogen Partnership and its members Hydrogen Europe and Hydrogen Europe Research under the Grant Agreement Nr. 101101498.