Fertilizer International 525 Mar-Apr 2025
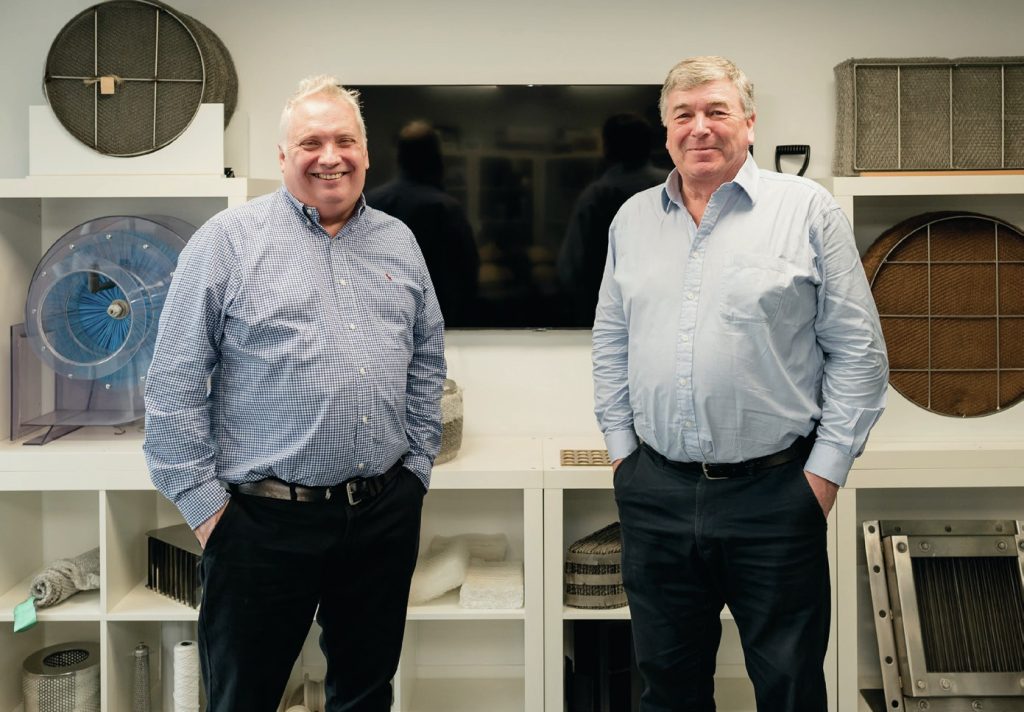
18 March 2025
Begg Cousland – more than 70 years in the making
DUST & EMISSIONS SCRUBBING
Begg Cousland – more than 70 years in the making
In this exclusive interview, Fertilizer International sat down with Graeme Cousland, Managing Director, and Martyn Dean, Sales Director, Begg Cousland Envirotec Limited, ahead of the CRU Phosphates+Potash Expoconference in Orlando at the end of March.
Introduction
Begg Cousland Envirotec Limited has long-standing experience in the manufacture of both:
• Knitted wire, mesh pad type demisters
• Fibre bed type candle filters.
The company combines this with in-depth expertise in solving wet gas cleaning problems across a variety of industrial applications. In many cases, this includes designing and supplying complete filtration systems as a turnkey package, as well as tailoring mist eliminators to address particular customer problems.
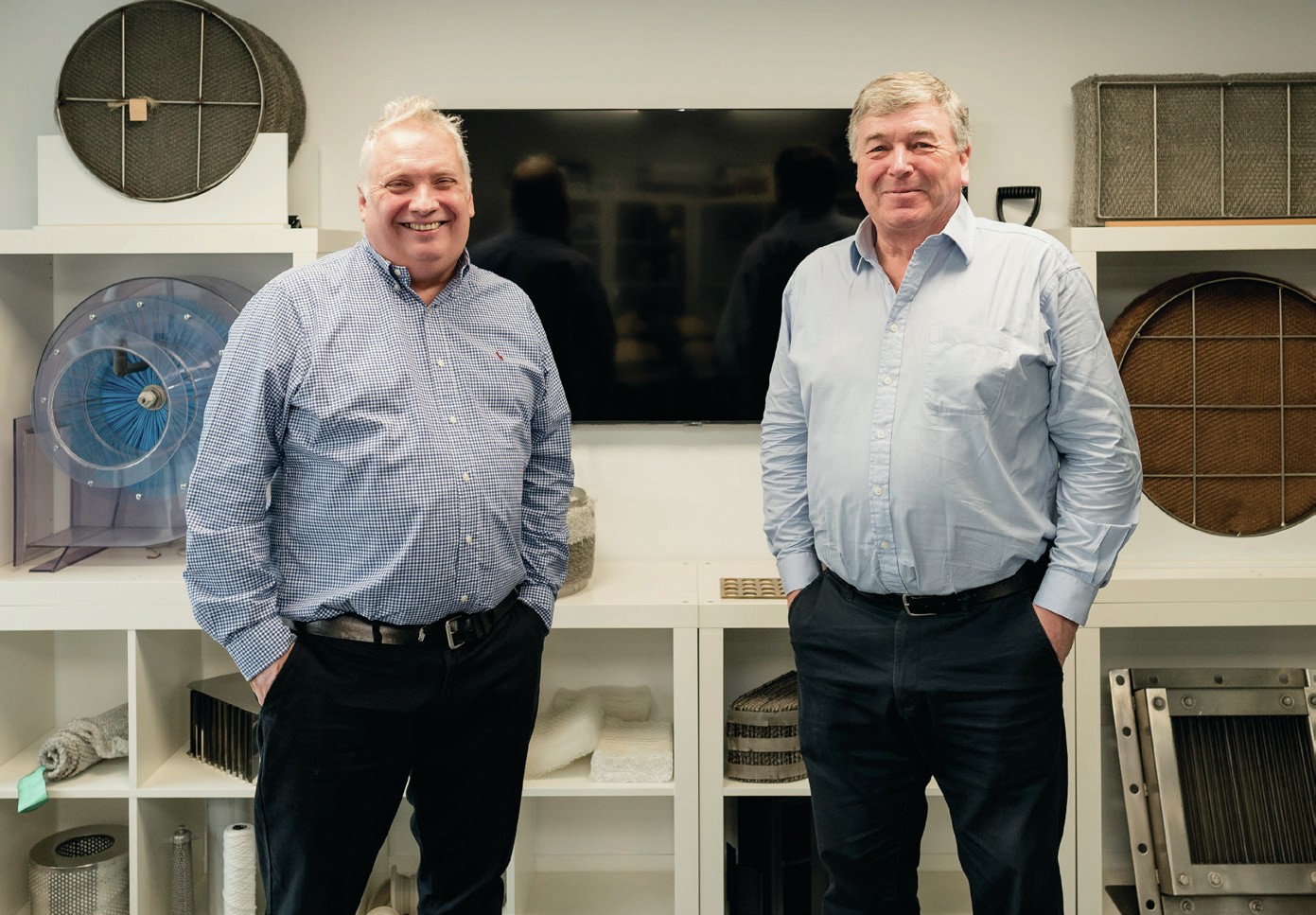
Quality has always been of paramount importance to Begg Cousland. Its products are manufactured under direct control according to strict quality procedures. Key market applications include, but are not limited to:
• Chemicals production, e.g. fertilizers, process chemicals and petrochemicals
• Non-ferrous metals smelting off-gas treatment
• Pharmaceuticals production Electronics industry Oil & gas production
• Pulp & paper industry.
Fertilizer International sat down with the company’s leadership team, Graeme Cousland (GC) and Martyn Dean (MD) in February for an in-depth discussion about dust and emissions control and scrubbing technology.
Proudly Scottish, internationally focused
Graeme and Martyn, it’s a privilege to have the opportunity to speak to you both today. Begg Cousland has been in business for many decades, can you provide our readers and CRU conference delegates with a brief overview of this proudly Scottish but internationally focused manufacturing and export business, its origins and its involvement in the fertilizer industry?
GC: “Begg Cousland has a history going back 170 years. It was in the 1950s when we changed, from only being wire weaver, to making a variety of wire products and started knitting wire to make demisters.
“So that was the point at which we got into mist elimination and then in the 1960s we added the fibre bed technology, so we were able to catch smaller mist and not just droplets, and from the 1970s onwards those products became the main turnover, main income for the company.
“In the 1980s, we started adding gas scrubbing, gas cleaning technology, so we could sell these package systems to the fertilizer industry, other industries as well. After 2012, the company became Begg Cousland Envirotec which has now been running for 12-13 years.
“In the introduction you very correctly mentioned quality – that’s always of paramount importance – but I would also add process knowledge too. What has also been of paramount importance, since the 1960s, is that we didn’t just make or copy something, we actually built the process knowledge which is still here today – and it’s understanding processes that allows us to solve customer problems better.”
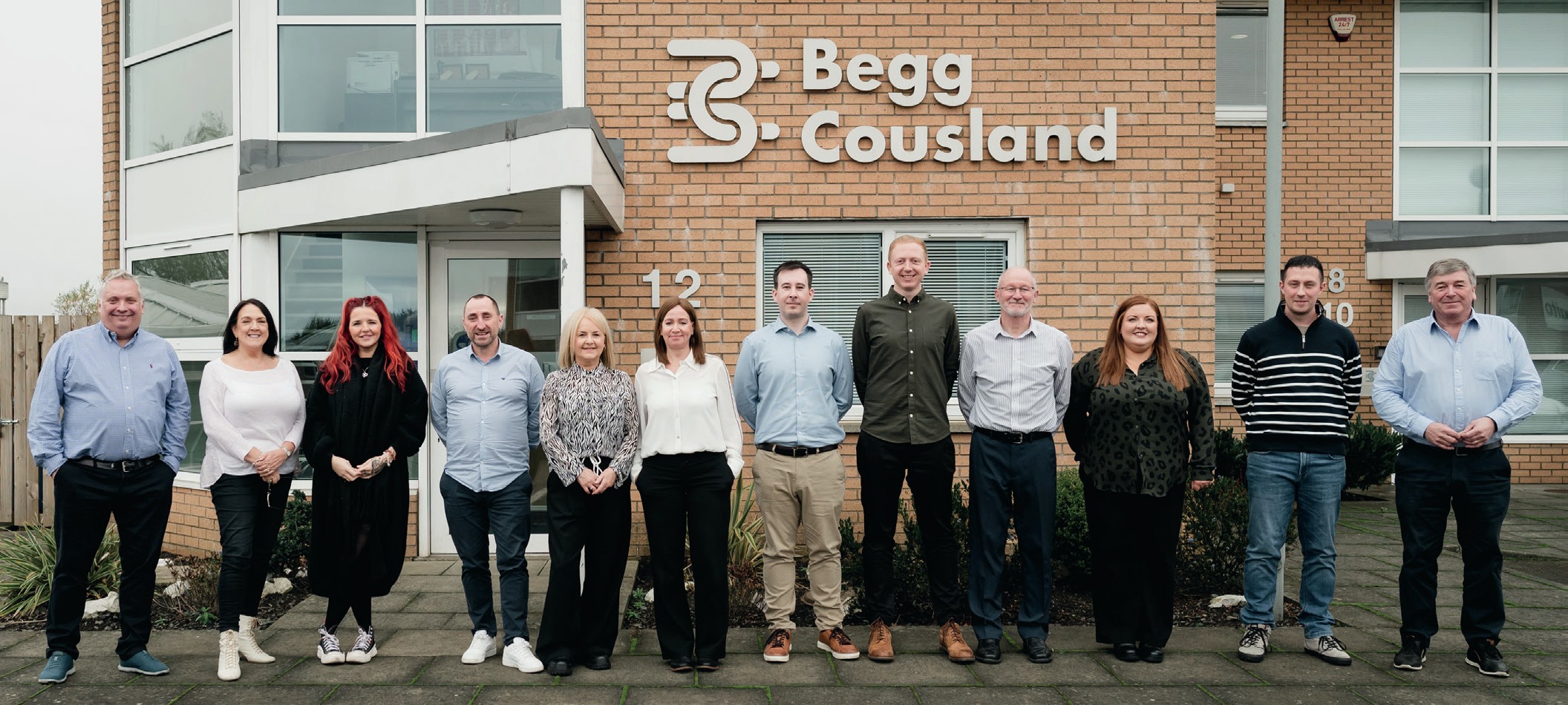
MD: “We’re not just a products company, you know. Yes, many of our competitors do just sell product. But we sell product and service and knowledge – and that comes as a package.
“Begg Cousland now exists as Begg Cousland Envirotec, the sales, marketing and engineering arm in the UK, and we have a daughter company Begg Cousland SRL that does all the manufacturing in Italy nearer to market demand – which is in Europe and globally.
“We’ve still got highly experienced process engineers within our UK sales and marketing team, and we’ve actually improved the manufacturing quality by moving to Italy in 2015. Our new large factory there is in a very good stainless-steel fabrication and machine building area.”
“We have a unique rotary brush scrubber called the Becoflex. It’s a modified ventilator with a brush that can do mass transfer and de-dusting in one step – and it can be used with dryers, pre-dryers, conveyors and at the back end of granulators.”
MD: “Because of Brexit, Simon, more by accident than design, we had the two companies and very quickly pivoted manufacturing and started taking orders directly into Italy. Having the two companies, one foot outside of Europe and one foot inside Europe, has been highly beneficial for the business.”
GC: “We’ve also had a licensee in China for more than 24 years – a strong relationship which has been our foundation in that country. They manufacture for the Chinese market and for products included in EPC supplies by Chinese contractors outside of China. And for the last 10 years there’s also been a production facility in India for their domestic market as well.”
Unique product offering
Begg Cousland is well known throughout the industry as a manufacturer of high-quality demisters and candle filters. What’s so special about the company’s two product ranges and what do they offer the nitrogen and phosphates industries and sulphuric acid producers?
MD: “In mist elimination, it’s actually more than two product ranges – we have demisters, coalescers, candle filters etc. When you move into nitrogen fertilisers, yes, you can incorporate these mist elimination products – it could be ammonium nitrate filters, for example, going back to the early days of Hydro Supra (Yara) – but the focus is more likely to be on gas and dust scrubbing.
“We have bespoke engineered processes for prilling towers, a unique rotary brush scrubber called the Becoflex. It’s a modified ventilator with a brush that can do mass transfer and de-dusting in one step – and it can be used with dryers, pre-dryers, conveyors and at the back end of granulators.”
“This rotary brush scrubber is unique to the marketplace. It’s very flexible, self-cleaning, less prone to fouling and it lends itself to the phosphate industry as well, where there’s a lot of sticky components.
“The Becoflex is niche but liked by a lot of EPC contractors and end-users and also has nitrogen fertilizer applications as well. I mean, there’s 12 of these units in and around the dryers and pre dryers at a big explosives-grade ammonium nitrate complex in Australia, for example.
“Then, in a partnership with a Belgian company, we do crossflow scrubbers with structured mesh packings. These do the de-dusting first and then do mass transfer, by optimising performance with different mesh apertures.”
GC: “You would also use a crossflow scrubber for phosphoric reactor fumes, for example.”
MD: “Actually, we can offer rotary brush scrubbers, venturi scrubbers or crossflow scrubbers – or a combination of all the above.
“Then you have crossflow scrubbers for FSA – the big markets for that are Morocco and Saudi Arabia. Any kind of phosphate rock you attack you’re going to produce fluorine. Silicon tetrafluoride will break down to HF and you produce fluorosilicic acid (FSA) as a result.
“Depending on what process is used, we can also remove HF or ammonia with conventional packed bed scrubbers. Each Customer is different, each application is different.”
“We draw on all of our experience and like to see ourselves as service providers, rather than as an equipment supplier – you get that service along with the equipment.”
GC: “We’ve just got a new order for internals for a cross-flow scrubber in India. For us, everything’s customised. Yes, we have our ‘most common’ products, but we don’t have a standard product.”
Well positioned for the future?
What changes are Begg Cousland observing in the fertilizer industry – particularly in terms technological innovation and advances?
GC: “We want to put the Becoflex brush scrubber that Martyn talked about in combination with a crossflow scrubber Because it would be able to remove more dust more efficiently and with less liquid – rather than simply belting it with showers of water at the inlet to the cross-flow scrubber – so it would have energy savings and effluent savings.”
MD: “A lot of the cross-flow scrubbers, Simon, have a venturi that uses maybe 5-6 times the amount of liquid as a spray at pressures of 3.5-4.5 bar. Whereas our Becoflex uses 15-20% of the liquid at 0.5 bar – so you’ve got the energy saving straight away with less liquid and lower motive pressure.
“The Becoflex moves the air as well – because you always need a fan. It’s not as efficient as a standard ventilator, but it’s 65-70 percent efficient. So, you you’ve got all these benefits and the opex is less.”
GC: “For sulphuric acid plants, we developed two innovations in conjunction with Outotec, now Metso. The first was a wetting system for candle filters developed for two different reasons.
“Firstly, to be able to absorb sulphur trioxide during plant start-up to abate startup fumes – which could last for eight hours or more. Secondly, to deal with NOx problems, by helping solubilise crystals which, if they form, reduce the capacity of the plant and use more energy. So, this was a double-edged problem-solving solution.”
MD: “We’ve done candle wetting systems for a long time, but this one was a bit more unique. Instead of having a spray nozzle, at the top or the bottom, it’s like an annular ring where you introduce the liquid directly into the fibre bed – which also has benefits.
“We’ve actually reversed engineered this into a lot of systems which were using spray nozzles. Because introducing uniform liquid into the fibre bed is a far more efficient way to wet the filter.”
GC: “The second thing we developed with Metso Outotec was a vertical demister system. This meant you could install and remove the demister panels through the roof of the tower – so nobody needed to go inside the tower.
“So, this was a safer design without loss of performance that also saved time – to be able to change the demister in hours rather than days. Quick is also important to a customer in Southern Africa with one of these systems, because of the dirty environment, the demister blocks within about six months. They can now change this demister quickly without having to have a big shutdown or restricting their production for long periods.”
MD: “We’ve evolved over the years so if environmental regulations change, we change the approach.”
CRU Phosphates+Potash Expoconference
Based on attendee feedback, last year’s CRU Phosphates event in Warsaw was one of the most popular and successful in the conference’s history. What is Begg Cousland hoping to achieve when the phosphate and potash industries convene again in Orlando near the Lakeland phosphate district at the end of March?
GC: “It’s a perfect place to keep building our relationship with the major players who are in the Lakeland area and will anyway be at the conference. We would like to push some of our equipment and technologies more into the North American market.”
MD: “Geographically, it’s quite fortuitous as it’s near Lakeland. There are ongoing projects and people we met in Warsaw last year – so it’s natural for Begg Cousland to stay onboard and go to Lakeland.
“A lot of the main players will be there. The whole Lakeland area is a hotbed of people that are in the phosphate industry.
“It’s about catching up. There’ll be people there we don’t know, or a new project we don’t know about – we attend for the market intel as well.”
A leadership double act
Graeme and Martyn, I’ve known you both since joining the industry in 2015. I think people are interested in your successful long-term business partnership – and why that works so well to the benefit of the company.
MD: “We’ve consciously changed the company dynamic so that the majority of our process engineers are focused on customer support. We draw on all of our experience and like to see ourselves as service providers, rather than as an equipment supplier – you get that service along with the equipment.
“We’re also smaller, more dedicated, not part of a multinational that just pushes product, product, product. That has its benefits since we can react a lot quicker – you don’t have to go through layers of bureaucracy.”
GC: “With our 70 years of mist elimination, we have customers today who have been customers over the 70 years. It’s repeat customers coming back – which is a reflection of the company’s reputation, customer support and quality. That remains at the core of what we do, as is the fact that, with Martyn and I together, it’s a small team making quick decisions.”