Fertilizer International 525 Mar-Apr 2025
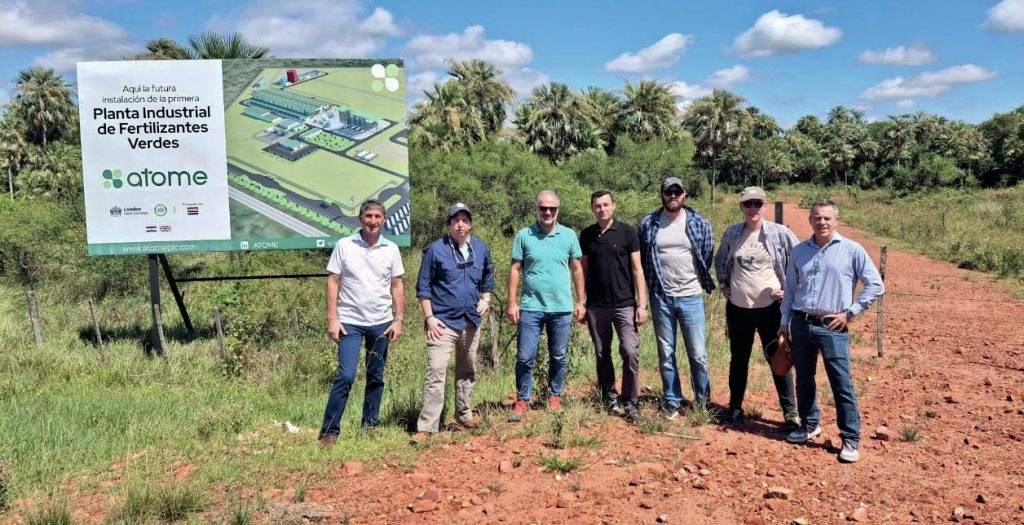
18 March 2025
Casale – leading the green fertilizer revolution
SUSTAINABLE FERTILIZER TECHNOLOGY
Casale – leading the green fertilizer revolution
Casale’s technologies, by transforming hydropower into green fertilizers, are helping ATOME’s Villeta project revolutionise the future of agriculture in Paraguay. This Latin American venture combines innovation with solid engineering and the very highest standards in project execution, as Francesco Baratto, the Head of Casale’s Syngas Department, explains.
Introduction
As the world irreversibly pivots towards low-carbon energy and industrial sustainability, the need for ‘green’ solutions in food and farming have also become a priority. Conventionally, fertilizers – while essential for boosting agricultural productivity – have been produced using energy-intensive methods that rely on fossil fuels and generate greenhouse gas (GHG) emissions.
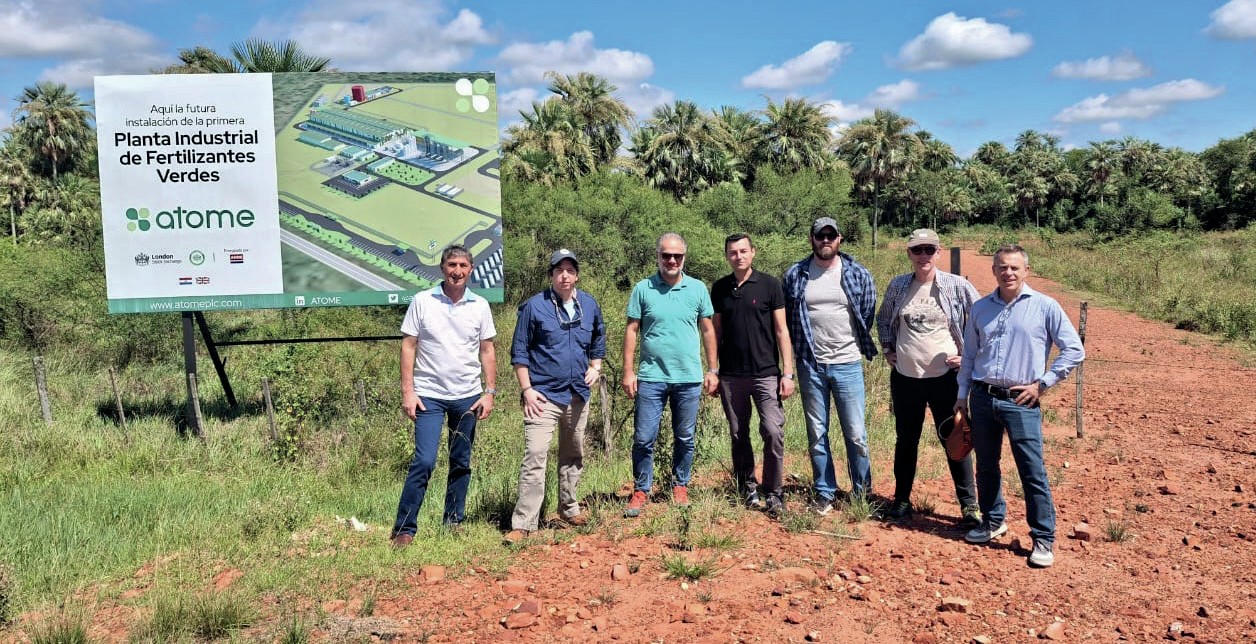
The Villeta project, located 35 kilometres from Asunción along the Paraguay River (Figure 1), will establish a world-scale green fertilizer production plant using Paraguay’s abundant hydropower. The project is designed to meet both domestic and international fertilizer demand while significantly reducing GHG emissions, offering an exemplary model for sustainable industrial development.
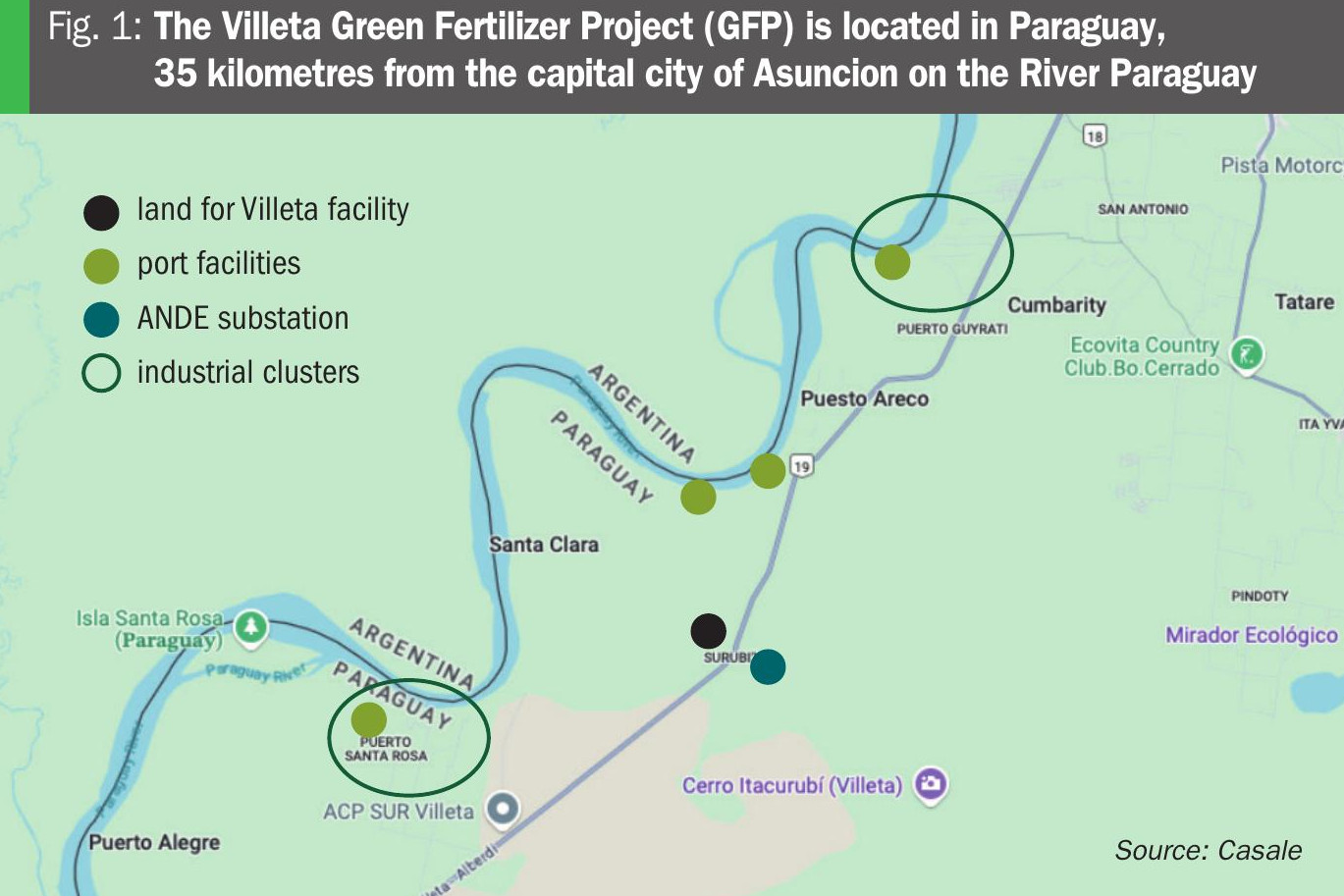
Paraguay – a land of opportunities
Paraguay is uniquely positioned to lead the green energy revolution. With nearly 99% of its electricity derived from renewable sources, primarily from the Itaipu Dam, Paraguay boasts one of the world’s greenest energy profiles. The country uses only 30% of its 50% share of Itaipu’s electricity, leaving a significant surplus available for industrial development.
Agriculture is the backbone of Paraguay’s economy, employing approximately 20% of its workforce. The nation is a leading sugar, stevia, and soybean exporter with its thriving agricultural sector driving substantial domestic fertilizer demand. Ag commodities, as well as supplying the domestic market, are vital for international trade, particularly with neighbouring Brazil and Argentina.
The demand for fertilizers in Paraguay is driven by the need to maintain and increase agricultural productivity. Ultimately, agricultural sector growth is also determined by fertilizer availability, given the strong linkage between fertilizer use and crop yields.
Fertilizers are essential for replenishing soil nutrients and supporting the cultivation of crops with high nutrient demand like soybeans and stevia. The Villeta Project, due to Paraguay’s strategic location, is well-positioned to serve both domestic fertilizer needs and the larger South American market – helping to guarantee regional food security by reducing dependency on imported fertilizers.
Villeta Green Fertilizer Project – the fundamentals
Spanning a 75-acre site in a designated free-trade zone, the Villeta project will produce green fertilizers using 100% renewable baseload electricity. Its location is ideal logistically, offering proximity to the river and the capital city with easy access to import and export routes. These excellent logistics – by enabling the efficient transportation of raw materials and finished products – are a major contributor to the project’s economic viability.
The Villeta Green Fertilizer Project is notable for the following key features:
- A 145MW power purchase agreement (PPA) with ANDE
- Advanced and efficient production technology capable of producing more than 250,000 tonnes per year of calcium ammonium nitrate (CAN)
- Zero-carbon production processes powered entirely by hydropower.
This world-scale green fertilizer plant aligns with global efforts to decarbonise agriculture while also contributing to economic growth in Paraguay. The project, by capturing and monetising Paraguay’s surplus hydropower, addresses the environmental impacts associated with traditional fertilizer production, making it a model for sustainable industrial development.
Key project partnerships
The Villeta project brings together a consortium of top level international and domestic partners:
- ATOME is a leading UK-based green fertilizer project developer listed on the London Stock Exchange. It is spearheading the project alongside a global pipeline of other green energy ventures with a total capacity of more than 600MW.
- Casale is implementing the project’s cutting-edge green fertilizer production solutions. The century-old engineering firm is renowned for its expertise in ammonia and fertilizer production technologies. The collaboration between Casale and ATOME began in 2022 with the award of the basic engineering design contract for the Villeta project’s green ammonia synthesis loop. Subsequently, the scope of Casale’s project work has expanded beyond engineering design to encompass the licensing of all core technologies — for ammonia synthesis, nitric acid, ammonium nitrate solution (ANS), nitrate granulation — and, most recently, providing all the necessary engineering, procurement and construction (EPC) services required to bring the entire project to completion
- Paraguay’s national electricity authority ANDE, as renewable energy provider, is the project’s backbone.
- Inter-American Development Bank (IDB) acts as the project’s international financial advisor, providing financial stability and credibility while ensuring project objectives align with sustainable development goals.
Collectively, these partner companies, by bringing a wealth of expertise and innovation to the project, should ensure its success and sustainability.
Technology and processes
The Villeta project stands out for incorporating advanced technologies designed to ensure high efficiency, sustainability and scalability (Figure 2). The project’s main technological pillars are outlined below.
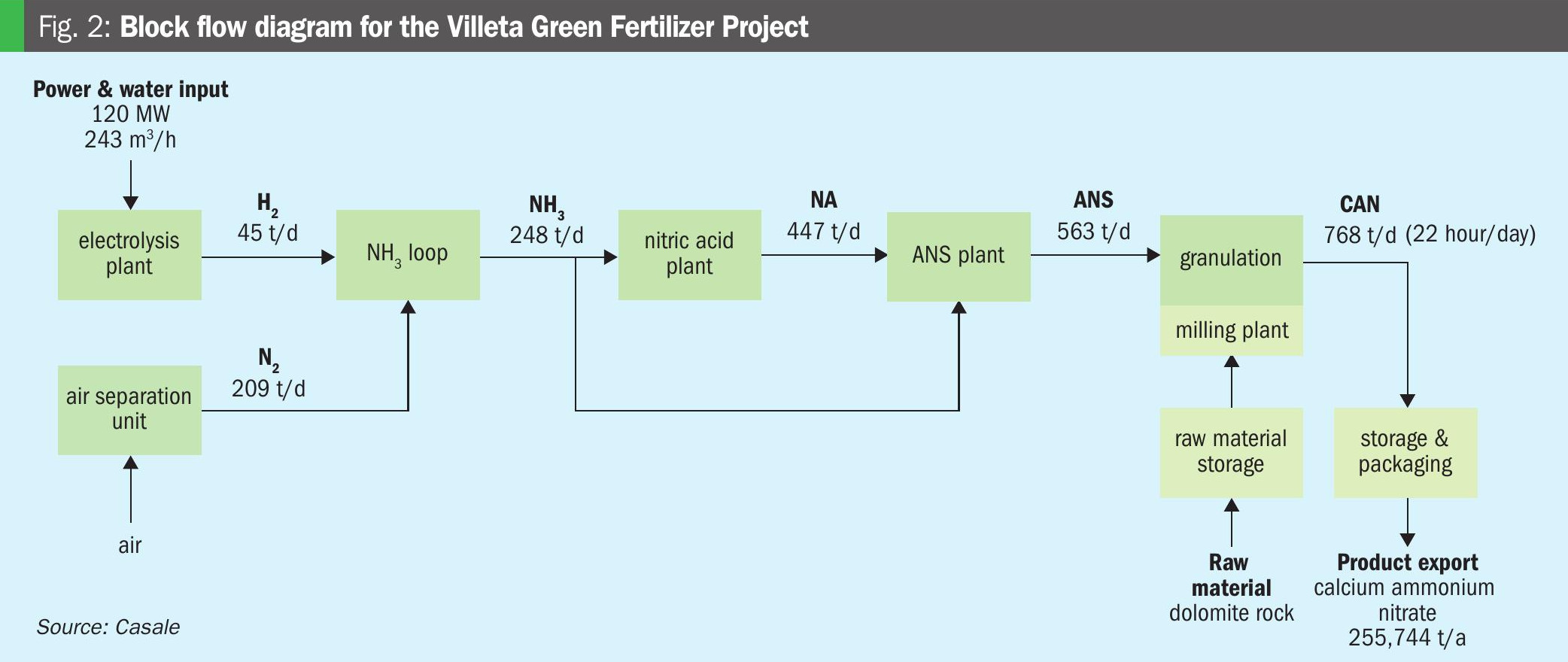
Hydrogen production
Hydrogen, a cornerstone of green ammonia production, will be generated using alkaline electrolysis (AEL) technology with the following key benefits:
- Proven track record: Alkaline electrolysis is a mature and reliable technology with over 100 years of industrial application.
- Efficiency challenges and mitigation: While AEL has a relatively low efficiency (approximately 5 kWh/Nm³ of H2 ), its robustness and cost-effectiveness ($700–1000 per kW) make it suitable for large-scale applications.
- Scalability: Modular designs enable rapid scaling to meet the project’s substantial hydrogen requirements (1,876 kg/h production rate).
Nitrogen production and ammonia synthesis
Nitrogen, another critical input for ammonia synthesis, will be supplied by a cryogenic air separation unit (ASU) with the capacity to produce 8,712 kg/h of nitrogen. The ASU provides a steady and high-purity nitrogen supply for continuous plant operations.
At the heart of the Villeta project is Casale’s SMART-N sustainable solution for small-scale green ammonia synthesis plants (Figure 3). SMART-N has the following unique advantages:
- Compact and modular design: Reduces the physical footprint and construction costs while enhancing operational simplicity.
- High conversion efficiency: The technology, by achieving an impressive ammonia-to-hydrogen conversion ratio of 5.64 kg NH3 /kg H2 , optimises resource utilisation.
- Proven track record: Casale has successfully installed over 100 ammonia synthesis loops globally, underscoring its reputation for reliability and effective delivery.
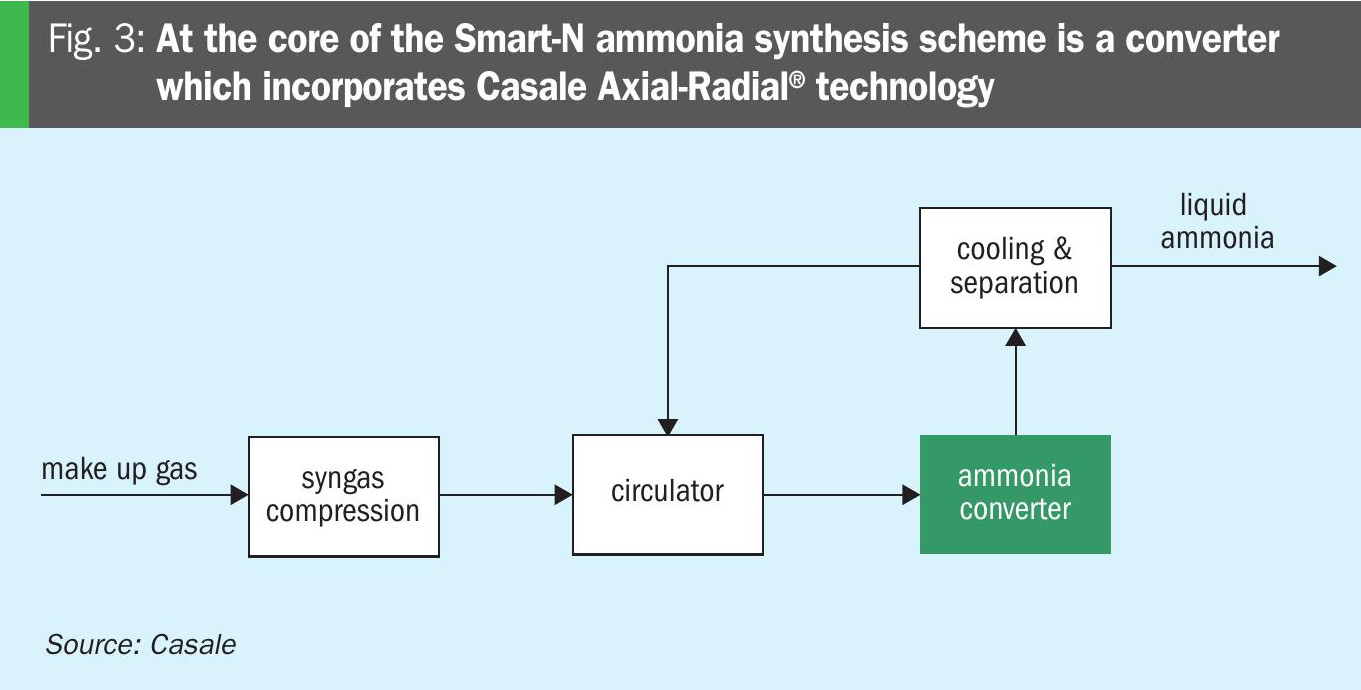
A distinctive feature of Casale’s Smart-Nammonia synthesis process is its ability to cope with a wide capacity range. If required, it can reliably operate with an erratic renewable power supply, yet still avoid or minimise the negative effects of cyclical operation and fatigue. Another key feature of the Smart-N synthesis loop is the lower number of equipment items required for green ammonia production – with a minimal configuration of just five items required. This reduces both capex and the project’s geographical plot size.
This process scheme is also extremely flexible – being able to produce either pressurised or atmospheric (cold) ammonia as an output.
Nitric acid production
The Villeta project will employ Casale’s dual-pressure DualPURE process for nitric acid production (Figure 4). DualPURE combines decades of experience with state-of-the-art technology and a proven. cost-effective design. Nitric acid plants based on this process offer reliability, high-energy efficiency and easy maintenance. They can also be customised to suit client requirements – for the fertilizer and explosives industries or other chemical applications – operating at up to azeotropic concentration.
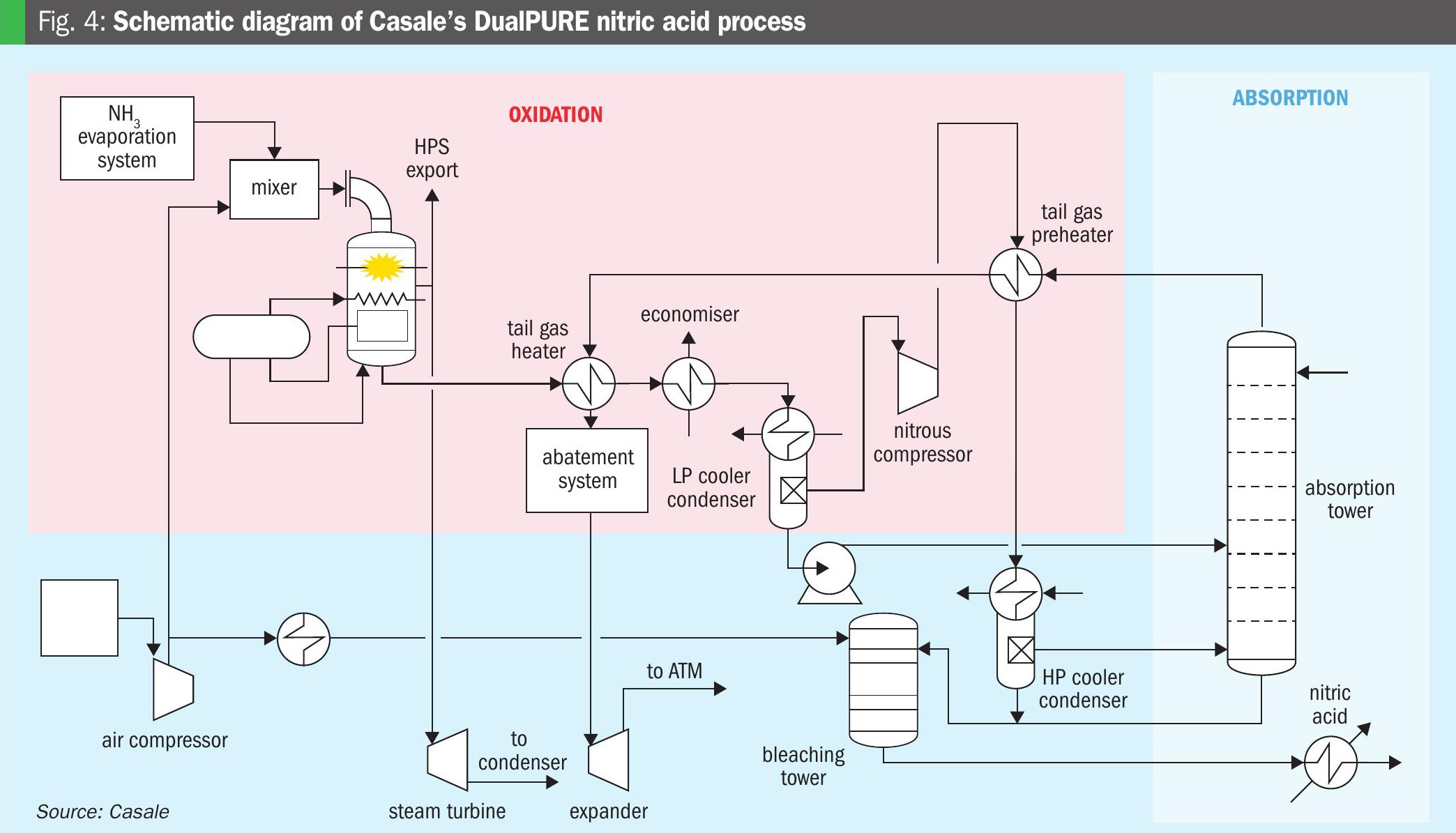
The DualPURE process is distinguished by:
- Lower ammonia consumption per tonne of nitric acid produced, through efficient mixing and the even gauze distribution provided by the design of the waste heat boiler (WHB) dome.
- Reduced platinum-rhodium catalyst losses, minimising operational costs and increasing the operational campaign length (up to 12 months).
- Low emissions via an extended absorption column design that operates at high-pressure to deliver superior NOx recovery while minimising selective catalytic reduction (SCR).
As its name suggests, DualPURE technology maximises overall plant efficiency by operating at two pressure levels (Figure 4) – this providing optimised conditions for ammonia oxidation and then nitrous oxide absorption:
- Ammonia oxidation occurs at 4-5bar, maximising ammonia conversion and reducing the precious metal losses of the gauzes.
- Nitrous oxides are absorbed at 11-13 bar, enabling high NOx recovery and increasing the conversion of NOx to nitric acid.
Granulation and fertilizer production
The final step of the green fertilizer production process requires the conversion of ammonia nitrate solution into granular fertilizers. This is achieved using two advanced Casale process technologies: NitroPIPE and NitroCULTIVA.
NitroPIPE is Casale’s technology for ammonium nitrate solution (ANS) production (Figure 5). This state-of-the-art process is intrinsically safe, reliable, highly efficient and easy to maintain, due to its cost-effective design backed by decades of experience. NitroPipe can also be customised to suit either fertilizer or explosives industry applications.
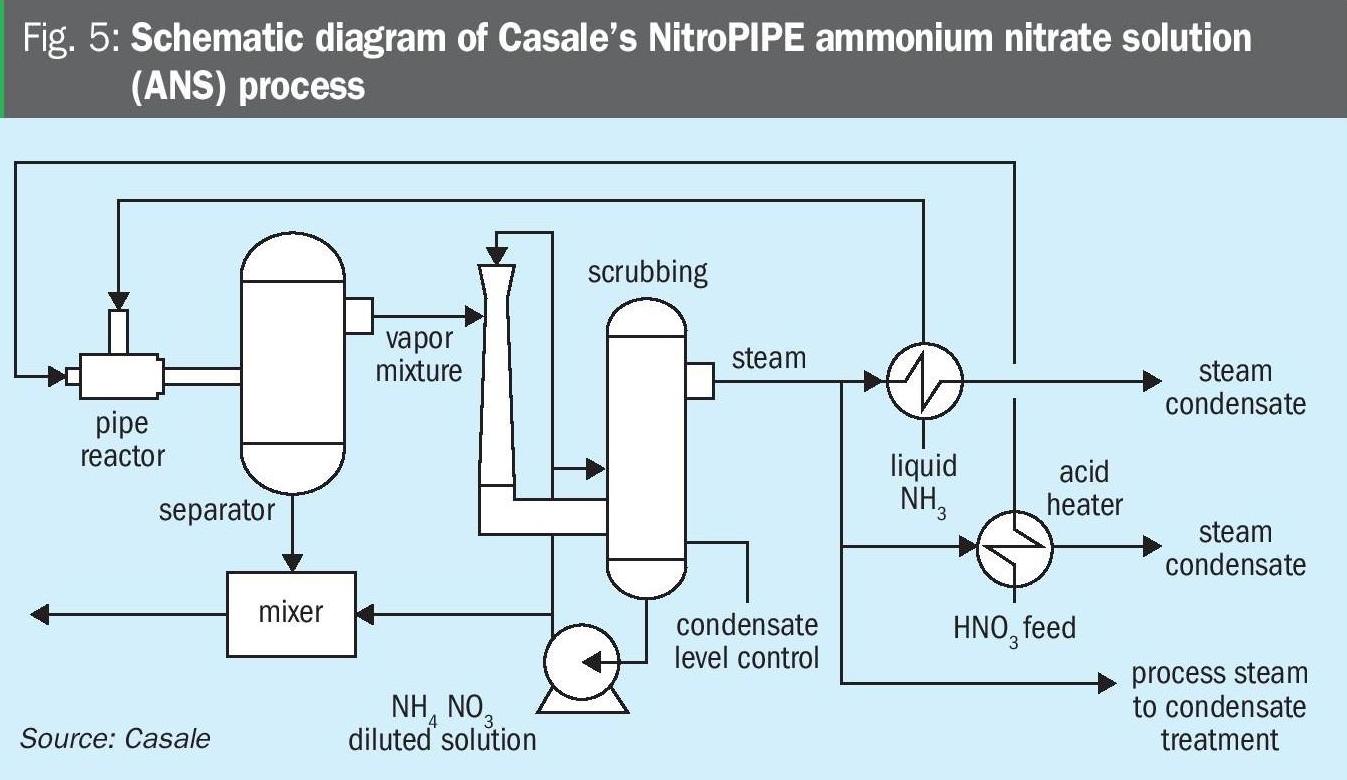
Central to the process is the specially designed, tubular Casale Pipe Reactor.
This is used to mix preheated ammonia and nitric acid feeds at a pressure of 6-8bar. Ammonium nitrate forms almost instantly in the Pipe Reactor releasing a significant amount of heat. On exiting the Pipe Reactor, hot ANS enters a separator at close to atmospheric pressure. The liquid ANS product collects at the bottom of the separator and is then sent to storage.
The NitroPIPE process offers simplicity and reliability due to its small reactor volume and minimal equipment requirements.
Casale’s NitroCULTIVA drum granulation technology generates high-quality granules with uniform size and durability, these being well-suited to the wide diameter field spreading techniques used in modern agriculture. This highly versatile technology has been successfully installed in more than 50 plants worldwide and can produce both ammonium nitrate (AN) and calcium ammonium nitrate (CAN) in the same unit.
The drum granulation plant (Figure 6) consists of the following major items:
- A rotary drum granulator: This sprays ANS over a moving bed of recycled particles. These consist of fines, dust, coarse ground particle, recycled final products, filler (e.g. limestone or dolomite), as well as solid raw materials, if required (e.g. ammonium sulphate or calcium sulphate).
- A rotary dryer: This uses hot air to dry the final product to 0.2% residual moisture content.
- A screen: This separates the on-size products from below-size and oversize materials.
- A dedusting and scrubbing system: This prevents pollution and minimises process losses by recovering ammonia and dust from all the gaseous effluents. Combined, these Casale process technologies meet the Villeta project’s ambitious output targets by collectively enabling the production of 768 tonnes per day of calcium ammonium nitrate (CAN).
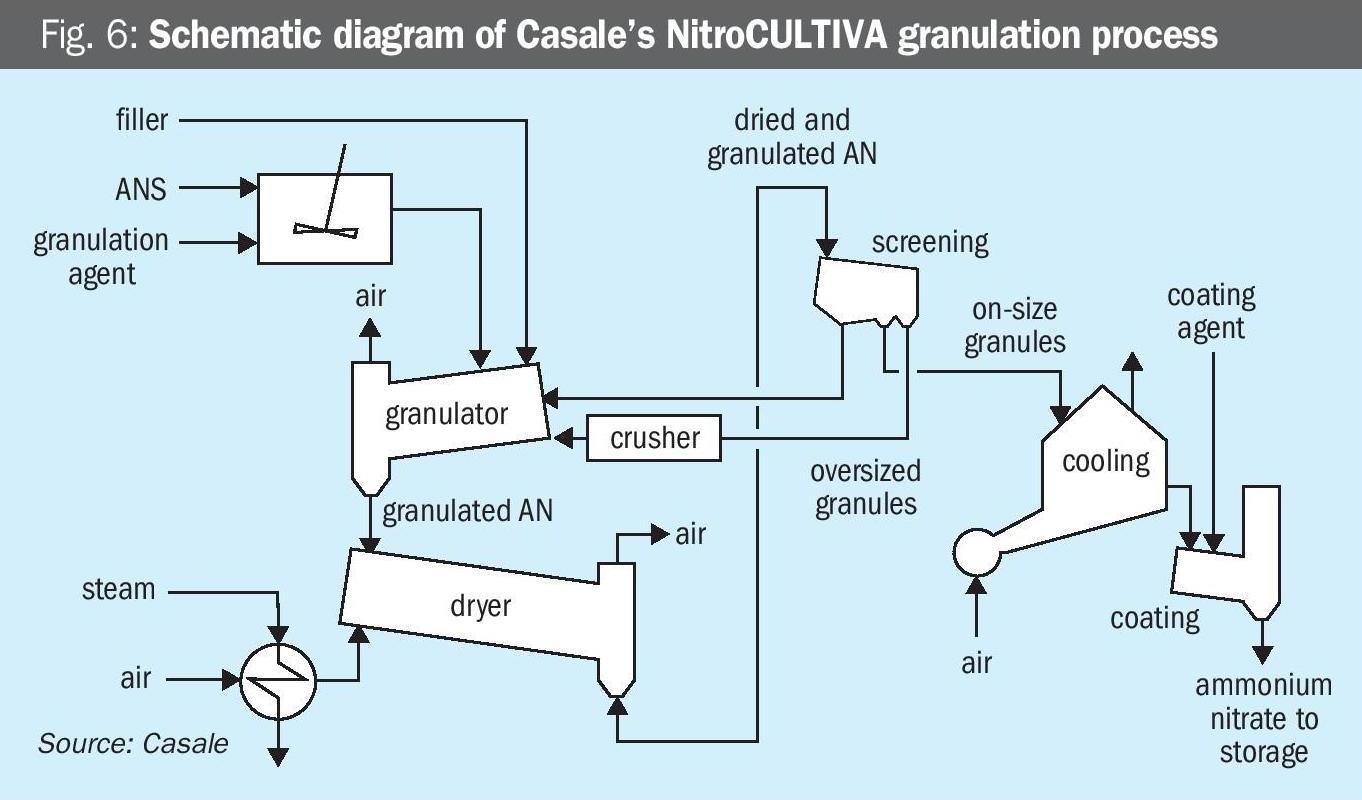
Environmental and economic benefits
The transition to green fertilizers is part of global efforts to combat climate change and reduce reliance on fossil fuels. By harnessing renewable hydropower, the Villeta project significantly reduces carbon emissions, effectively displacing up to 500,000 tonnes per annum of CO2 that would be generated by conventional nitrogen fertilizer production at the equivalent scale. The project’s environmental benefits extend beyond carbon reduction, by also promoting the efficient use of natural resources and supporting sustainable agriculture.
Additionally, the project enhances Paraguay’s trade balance and contributes to economic stability by:
- Creating construction, operational and associated supply chains jobs
- Attracting inward investment
- Widening the country’s export capabilities to include green fertilizers
- Supporting domestic agriculture, a sector that provide employment and is a major source of income for many Paraguayans.
Project status
As of the end of 2024, the Villeta project has achieved the following milestones:
- Securing a Power Purchase Agreement (PPA) with ANDE
- Obtaining environmental licenses and free-trade zone status
- Completion of the front-end engineering design (FEED) phase
- The signing of a Heads of Terms with Yara International for the long-term offtake of all of the project’s green fertilizer output
- The appointment of Casale as engineering, procurement and construction (EPC) contractor.
ATOME is close to making a final investment decision (FID) for the Villeta project with production currently scheduled to start in 2027.
Conclusions
The Villeta Green Fertilizer Project, by capturing Paraguay’s abundant hydropower and implementing cutting-edge technologies, provides a model for green industrialisation. Indeed, it sets a benchmark for the future of fertilizer production by aligning the twin goals of economic growth and ecological responsibility.
The project also exemplifies how renewable energy and industrial innovation can come together to address the dual challenges of environmental sustainability and agricultural productivity. This landmark venture notably combines innovation, entrepreneurialism and leadership with solid engineering and the very highest standards in project execution.
As this project illustrates, Casale remains firmly engaged in promoting sustainable development throughout the global chemical industry and is committed to transforming the production of essential chemicals.