Fertilizer International 525 Mar-Apr 2025
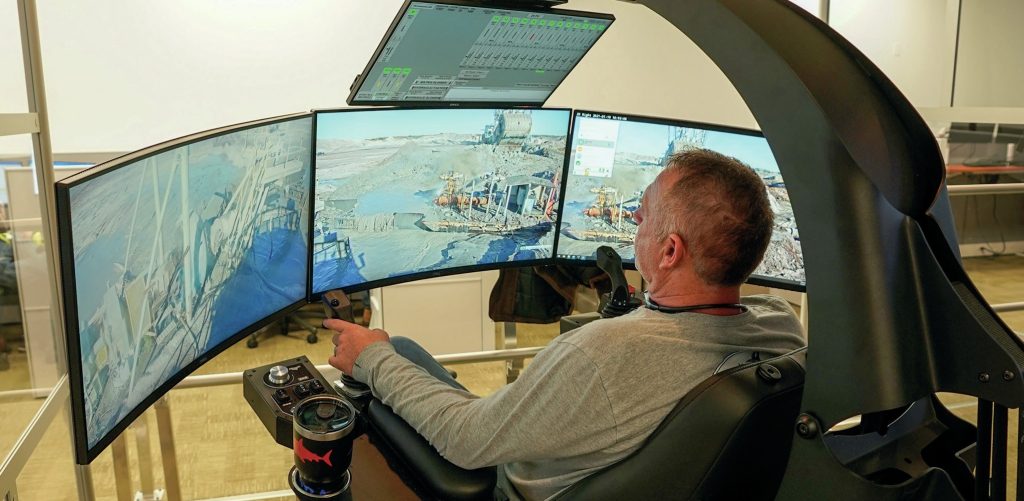
18 March 2025
North America’s potash and phosphate industries
CENTRES OF P&K EXCELLENCE
North America’s potash and phosphate industries
With CRU’s Phosphates+Potash Expoconference returning to North America in 2025, we profile the region’s phosphate and potash industries – focusing in on Florida and Saskatchewan, those two centres of P&K excellence.
US industry overview
The United States is the world’s fourth largest fertilizer consuming region, being responsible for around 9% of global consumption and ranked behind only China, India and Brazil globally. On an individual nutrient basis, the country is also the world’s third largest nitrogen and potash consumer and fourth largest consumer of phosphates (Fertilizer International 522, p14)
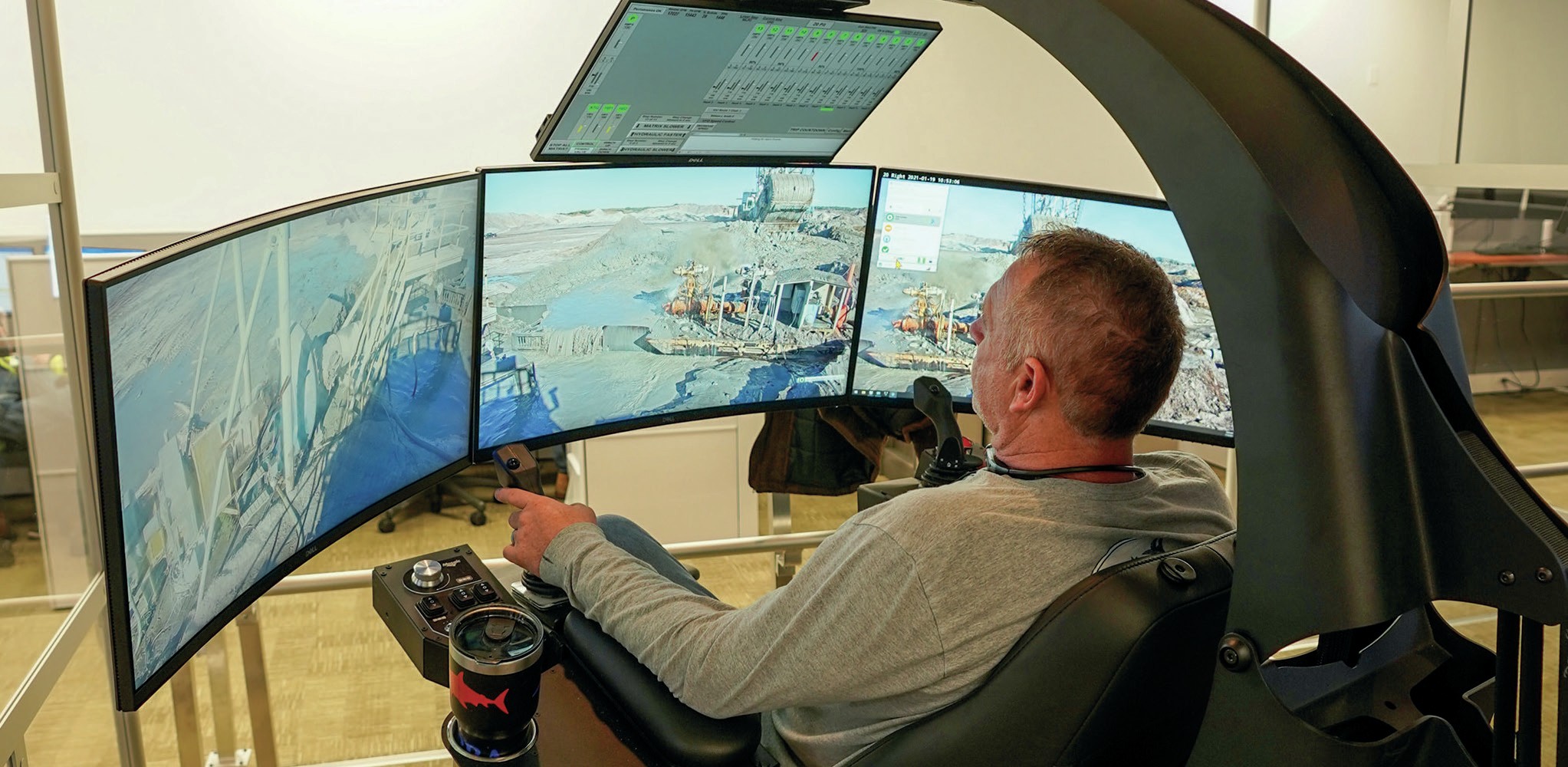
Overall, the US fertilizer industry, is ranked fourth in the world, in terms of total production capacity (22.7 million nutrient tonnes), exceeded by China (81.0 million nutrient tonnes), Russia (31.5 million nutrient tonnes) and its northern neighbour Canada (27.1million nutrient tonnes)1.
US fertilizer production is stable but in relative decline – with the country’s capacity for phosphate and nitrogen fertilizers being overtaken by Morocco and India, respectively, in recent years.
US phosphate and potash industries
The US can draw on 9.3 million tonnes of domestic production capacity for diammonium phosphate and monoammonium phosphate (DAP and MAP). Following several decades of consolidation, phosphate industry ownership is highly concentrated (Fertilizer International 496, p40) with just four companies – Mosaic, Nutrien, JR Simplot and Itafos – operating nine DAP/MAP production sites across Florida, Idaho, Louisiana, North Carolina and Wyoming (Figure 1).
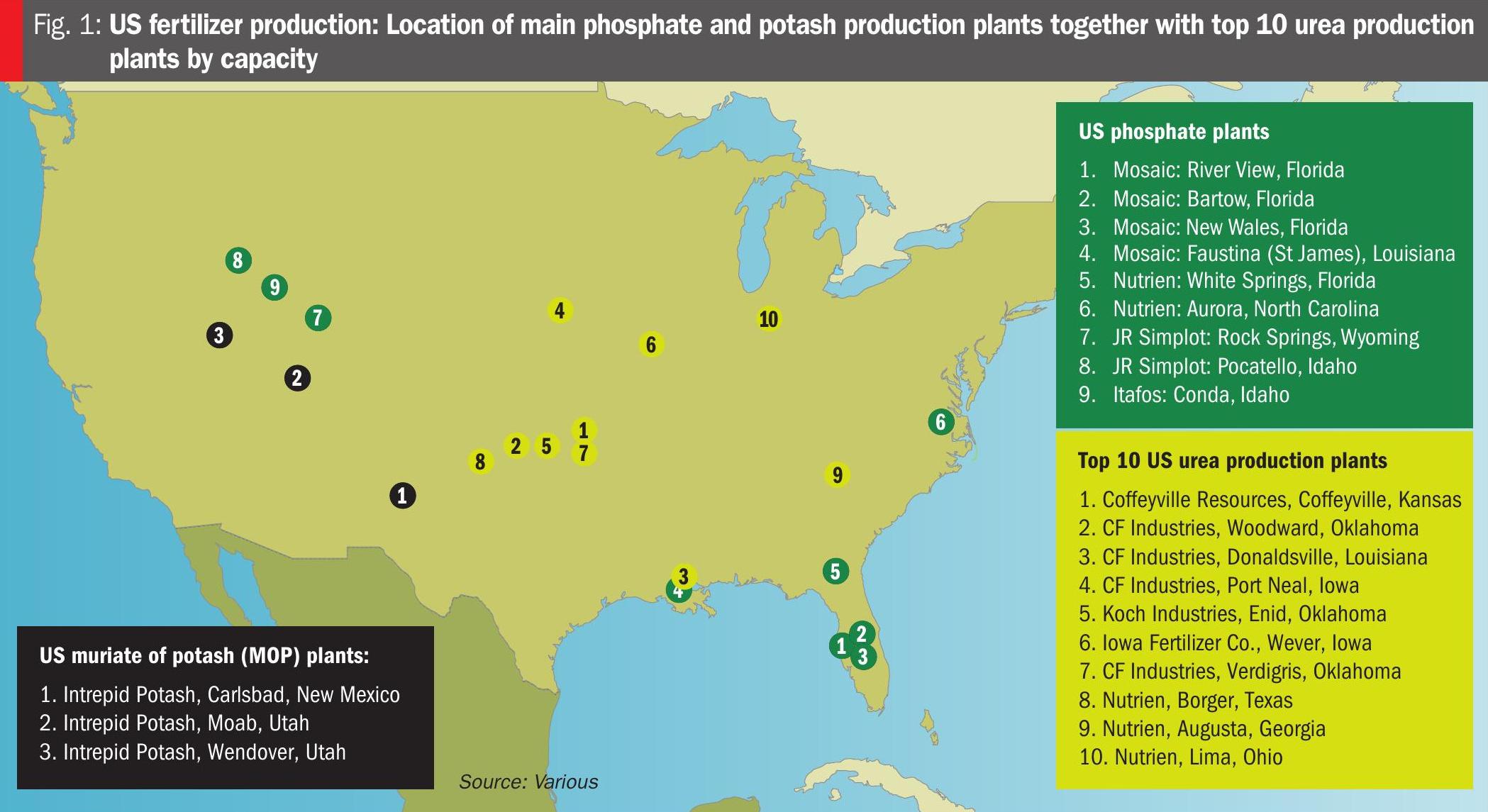
FLORIDA – WHERE IT ALL STARTED
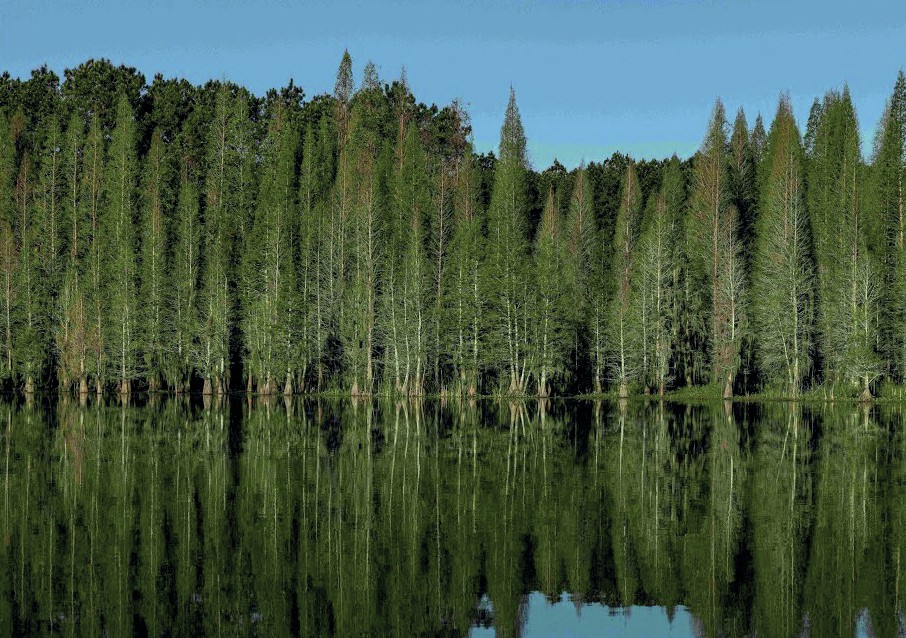
Florida’s pre-eminence as a phosphate-producing region dates back to the industry’s earliest days. Phosphate rock deposits near Hawthorne in Alachua County were the first to be mined in 1883.
The discovery of exceptionally large phosphate reserves in Florida during the late 19th century came at a time when agriculture was also of increasing importance to the state’s burgeoning economy. Although phosphate mining was a primitive affair in those pioneering times, early Florida settlers were quick to recognise the agronomic benefits of phosphate, which were readily apparent when applied to the citrus trees they were planting in ever larger numbers.
Florida leads, others follow
Indeed, the presence of abundant citrus groves on its doorstep provided Florida’s nascent phosphate industry with a ready-made market. It was this near-perfect match of supply and demand in Florida that created ideal conditions for a number of crucial and landmark mining and production innovations. In the 1920s and 1930s, a growing market, and the drive for greater efficiency and lower costs, provided all the incentives necessary for the introduction of draglines and the development of flotation and other beneficiation technologies.
As process engineering improved, and agricultural knowledge also grew, Florida’s phosphate producers introduced new downstream processes, pioneered by the Tennessee Valley Authority (TVA) in the 1960s, to manufacture more concentrated phosphate fertilizers. The new high-analysis products –monoammonium phosphate (MAP) and diammonium phosphate (DAP) – were able to deliver more phosphate to farmers at a lower cost. As a consequence, ammoniated phosphates ended up displacing superphosphate as Florida’s primary fertilizer commodity. This development ultimately transformed what had been largely a mining industry in Florida into a chemicals business.
As the 20th Century progressed, Florida’s state of the art phosphate production processes offered a mining and manufacturing template which others could learn from and follow. The landmark developments pioneered in the state became standard phosphate industry practice, setting an operational benchmark for the other phosphate-producing countries which have emerged around the world subsequently.
Eventually eclipsed
For decades during the post-war period, Florida enjoyed a commanding position globally as a supplier of phosphate rock and finished phosphate products. But since the 1990s the state’s global hegemony has been increasingly challenged by the rise of other centres of phosphate production – in China, Morocco, India, Saudi Arabia, Russia, Brazil and elsewhere. Having once been a major phosphate import market, China, in particular, has transformed itself through a crash programme of industrialisation into the world’s largest producer of finished phosphates and a net exporter.
Seamless reinvention
To its credit, North America’s phosphate industry has neither stood still or been left behind. Instead, it has parlayed its world-class expertise to become the purveyor of process engineering, technology, products and services to the global phosphate industry (Fertilizer International 489, p31). North American phosphate producers such as The Mosaic Company, with acumen and foresight, have secured their competitive position and continued market access – via a programme of global acquisitions and investments, and by forging strategic partnerships internationally.
Canada – preeminent in potash
Canada is the world’s third largest producer of primary (NPK) plant nutrients, a position achieved thanks to the unequalled might of its potash industry and strengths in nitrogen manufacturing (Fertilizer International 490, p18). The country’s fertilizer industry, while highly export oriented, also serves a large domestic agricultural market.
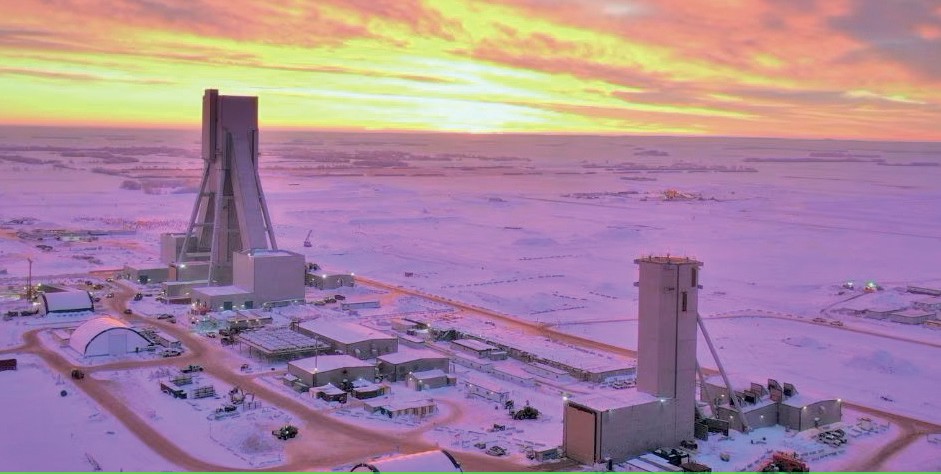
Some 95 percent of potash and 40 percent of nitrogen products are exported. In fact, Canadian fertilizers are traded with over 75 countries and represent some two percent of the nation’s total exports. Importantly, Canada is ranked as the number potash producer globally, with 10 major operations in Saskatchewan providing production capacity in excess of 25 million tonnes (Figure 5).
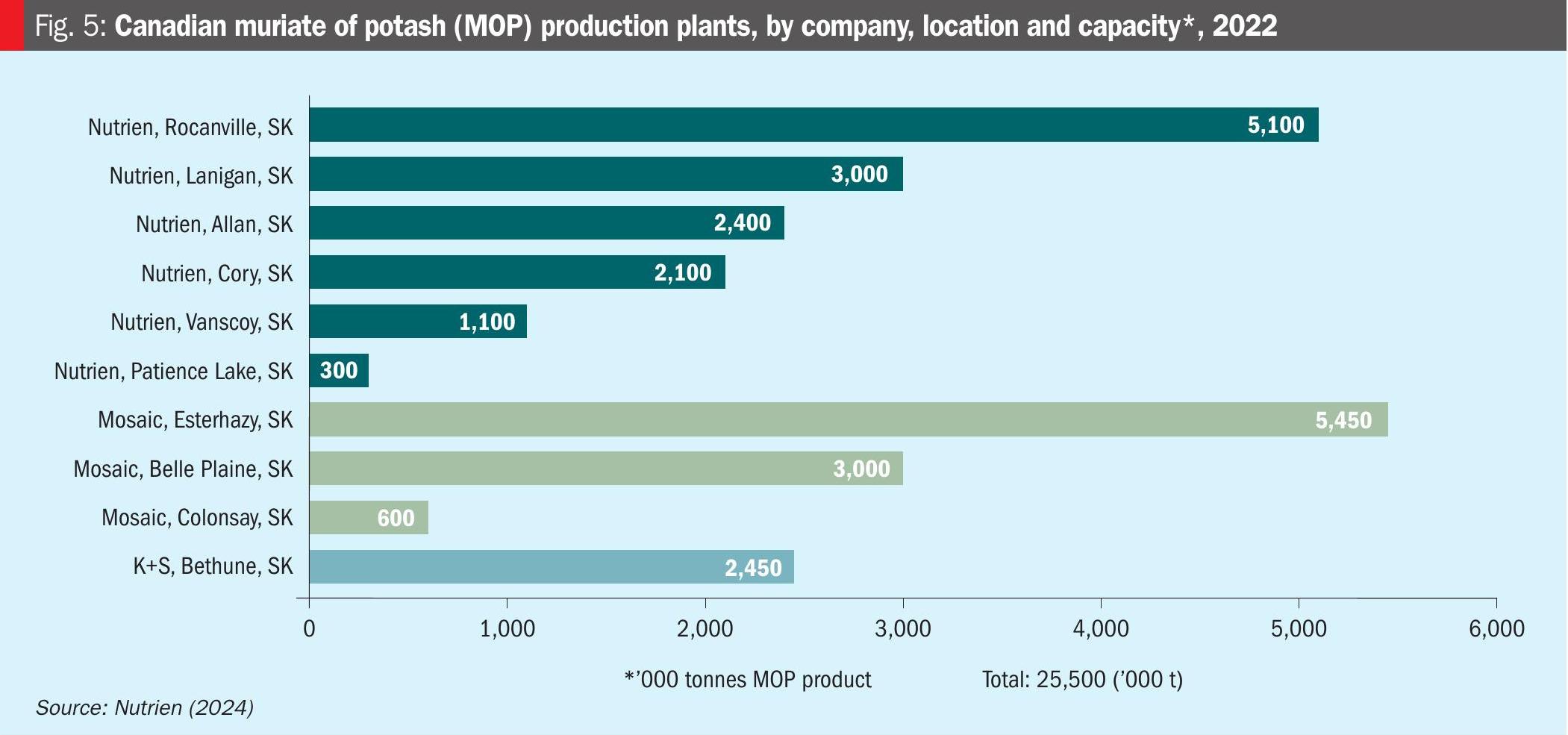
Canada exported more than 22.4 million tonnes of potash in 2023, making it by far the world’s largest exporter, the US, Brazil and China being the main export destinations. Consequently, potash exports are a major revenue earner for the country.
Fertilizer production (mining, processing and manufacture) in Canada is on the rise and generates $23.5 billion in economic activity and $12.7 billion in GDP. The industry supports over 76,000 jobs, directly and indirectly, throughout the supply chain and contributes over $5 billion in wages annually.
References