Fertilizer International 525 Mar-Apr 2025
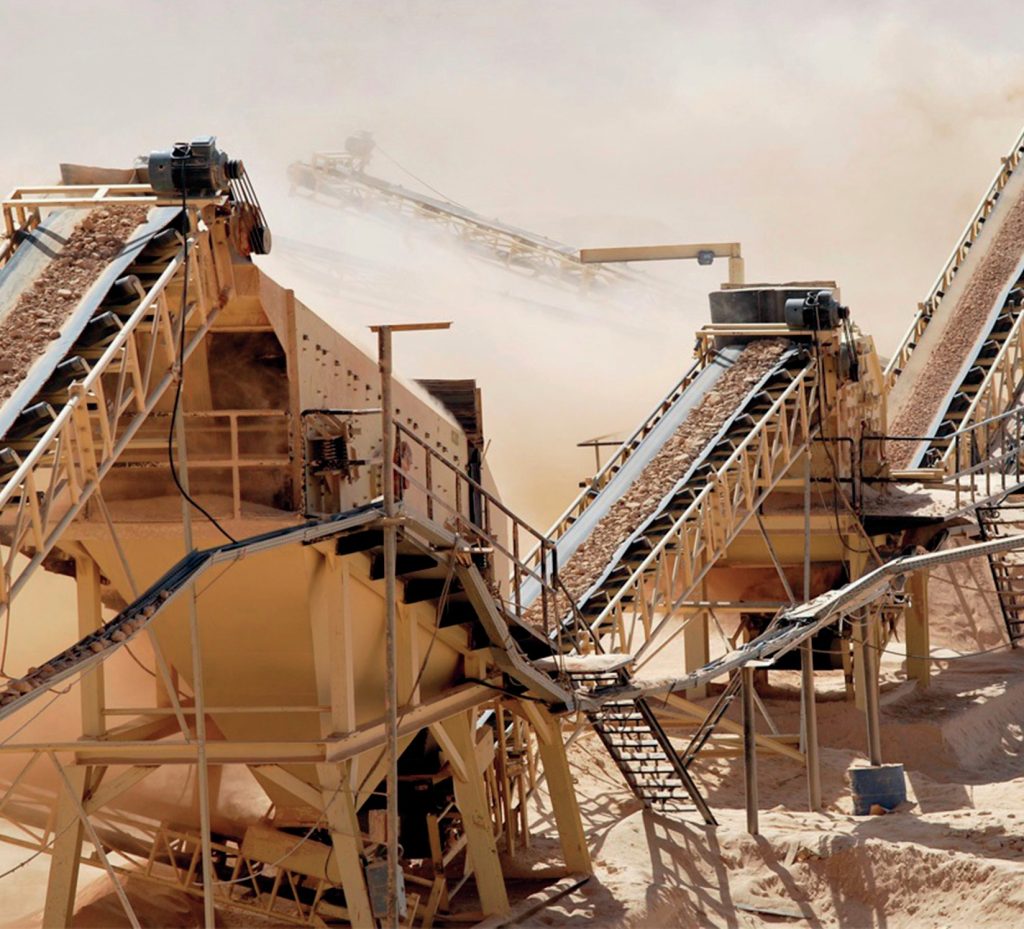
18 March 2025
Phosphates project listing 2025
PROJECT LISTING
Phosphates project listing 2025
Fertilizer International presents a global round-up of phosphate rock, phosphoric acid and finished phosphates projects.
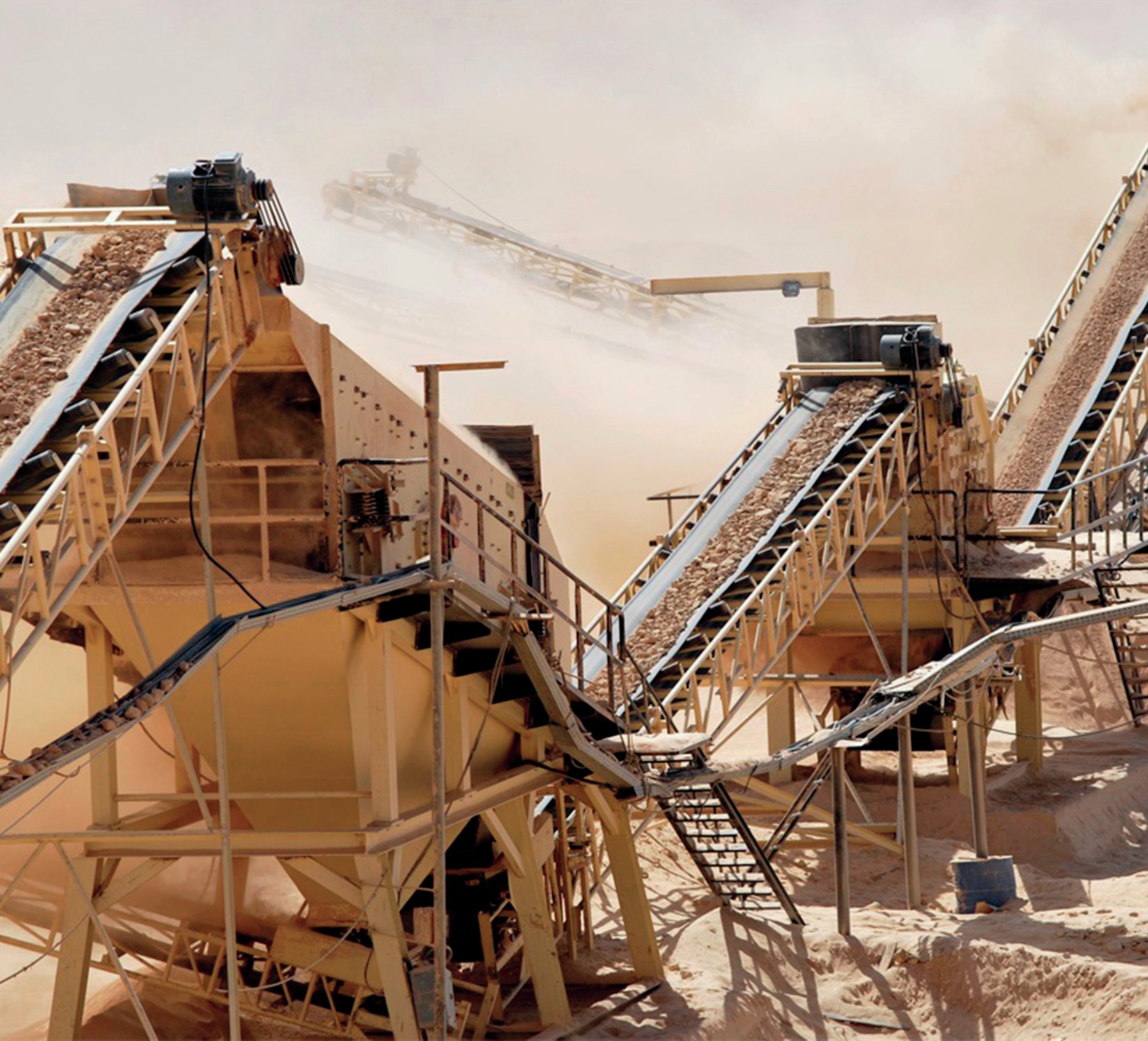
Phosphate rock*
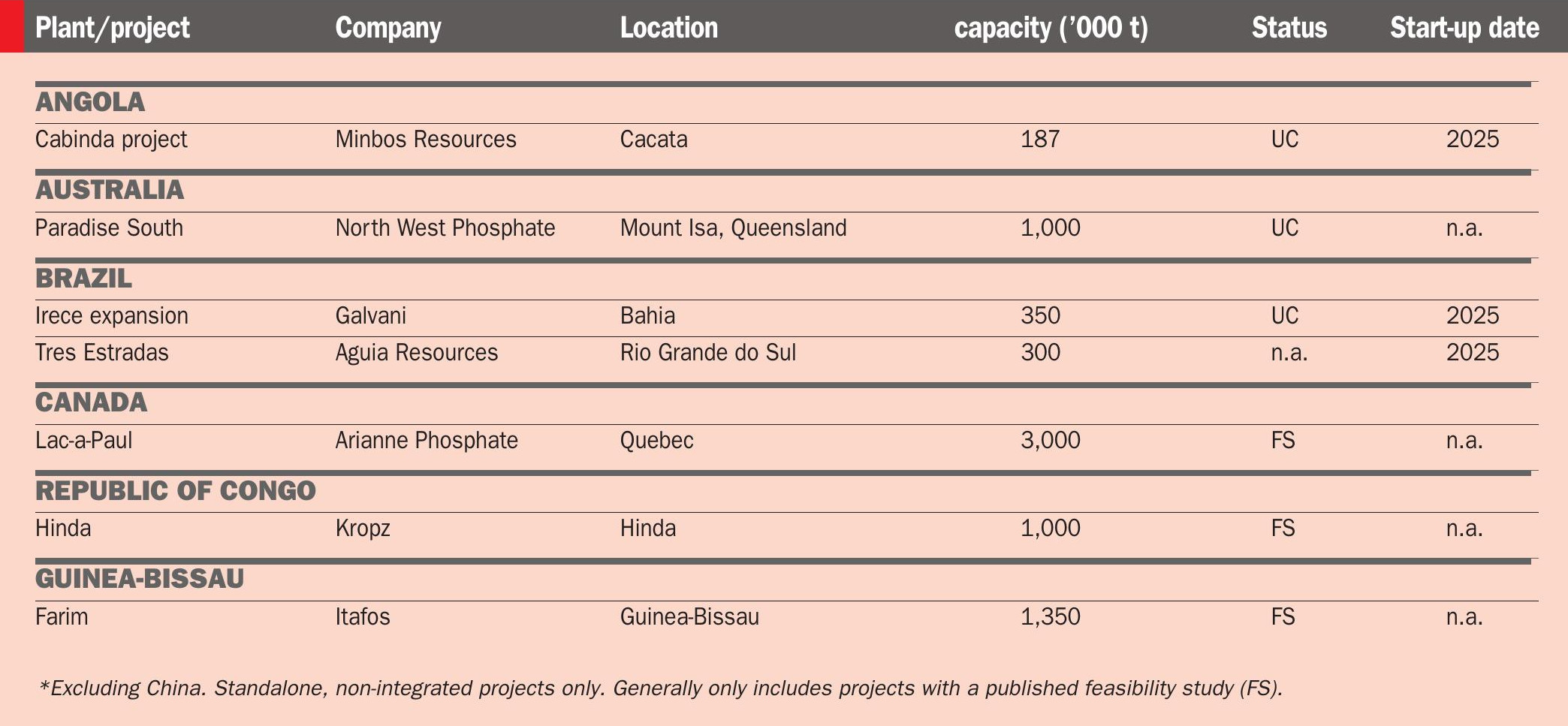
Phosphate fertilizer, phosphoric acid and integrated phosphate rock projects**
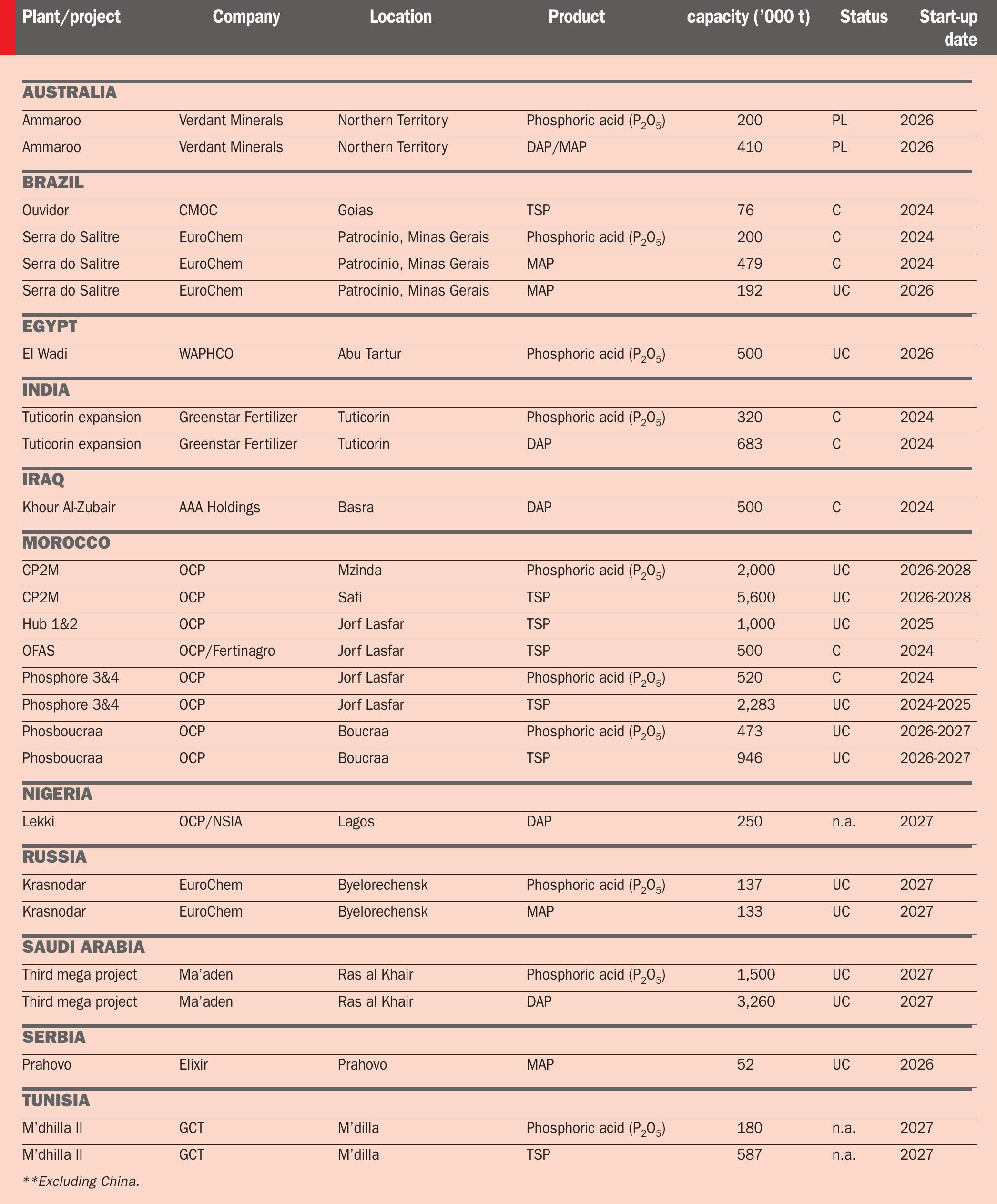
PHOSPHATE TECHNOLOGY AND ENGINEERING PROFILES
Prayon Profile
Good years in perspective
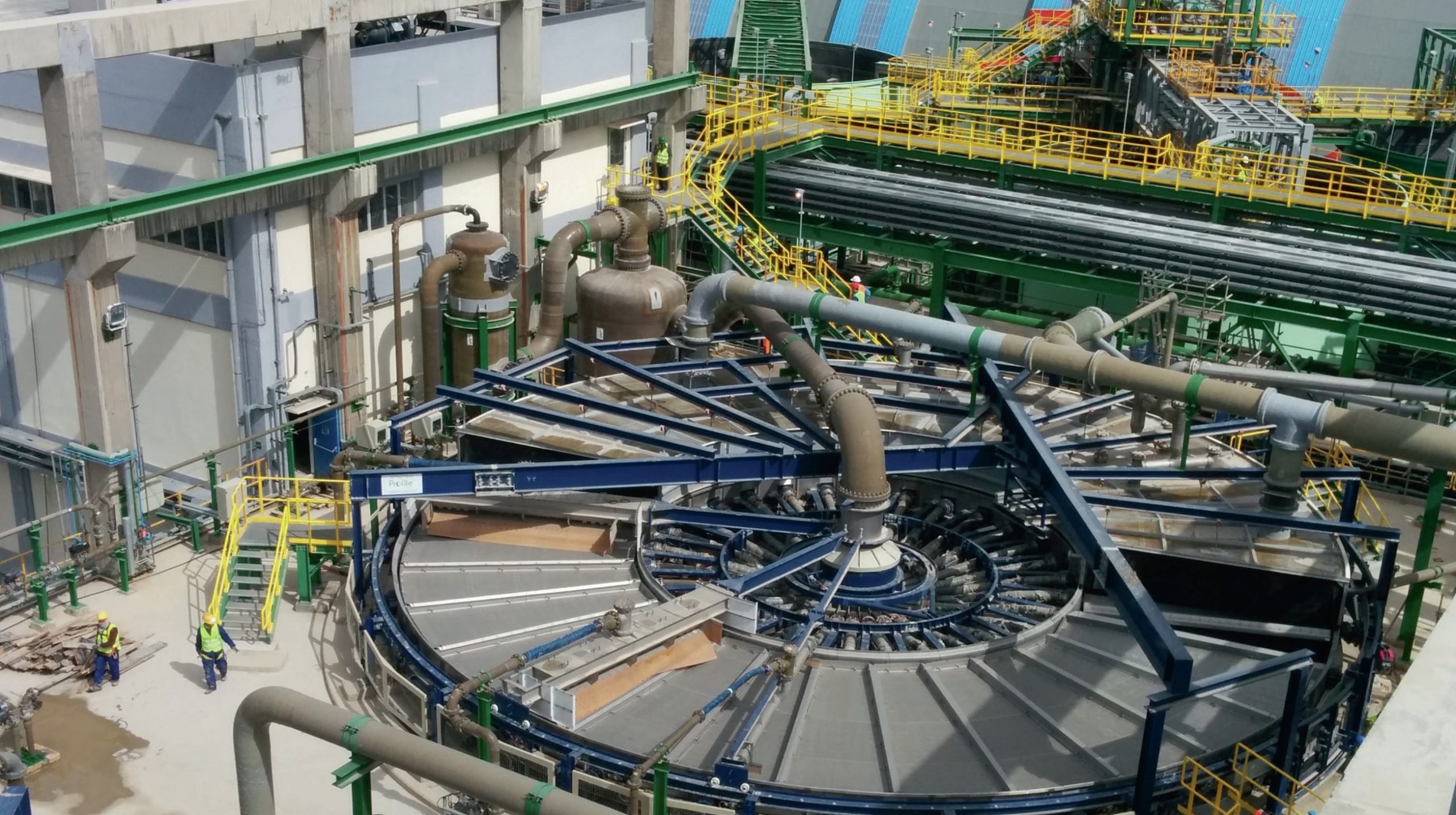
Paul-Henri Legros, general manager, Profile, a division of Prayon s.a. provides a personal update on recent phosphate industry developments:
“Phosphoric acid production in 2024 faced significant obstacles yet achieved notable developments. Globally, the phosphoric acid market continues to grow, despite technological, environmental and regional challenges. This growth is driven primarily by the increased agricultural demand for fertilizers – in response to a rising global population and the need for more and better-quality food as well-being and livelihoods improve.
“Besides agriculture, more and more technical applications are also being developed which require phosphoric acid. Most major phosphate industry players, for example, are anticipating exponential growth in purified phosphoric acid (PPA) capacity in upcoming years for use in LFP car batteries.
“Our company, with its process division Prayon Technologies and equipment division Profile, is uniquely positioned. We not only serve phosphoric acid and phosphate fertilizer producers but also manufacture specialty phosphates ourselves. This makes us optimistic about the future of our business in the short- and mid-term.
“This optimism is reflected in CRU’s own data. These forecast the addition of an extra 2.8 million tonnes (P2O5 ) of extra wet phosphoric acid (WPA) capacity between 2023 and 2028.
“Using our Prayon tilting pan filter, Profile is very proud to be helping deliver new production capacities for future years, across almost all producing countries. Impressively, between 2024 to 2027, we have already supplied and commissioned (or are contracted to do so) the following equipment items:
• Two x 260m² size filters to Saudi Arabia
• Six x 220m² size filters to Morocco
• Two x 260m² size filters to Egypt
• One x 220m² size filter to Jordan.
“For us, this is a very exciting industrial challenge – but it’s also really motivating to be a game changer in the world of phosphoric acid production.
“Prayon is also very keen to play a major role in reducing the environmental impacts of phosphoric acid production. This is really where Prayon Technologies can make a difference through several innovations, new equipment and practices.
“By offering cutting-edge developments – such as methods for gypsum valorisation and the double filtration, DA-HF or the Ecophos phosphoric acid processes – we are making a real difference. These are providing the market with practical options to valorise low-grade phosphate rocks and increase their production output while improving energy efficiency and water management.
“Our customised and long-lasting production equipment is another strength and a real contribution to the world of tomorrow – as is equipment designed to manage and clean effluents. Prayon’s droplet separators and gas scrubbing towers, for example, are very effective at recovering phosphoric acid and fluorosilicic acid, as well as removing cadmium or fluorine.
“At Profile, we are proud to see that our gas scrubbing towers have now moved outside the phosphate industry. In 2025, in collaboration with Prayon Technologies, we are helping an Australian rare earth producer to clean its effluent – an exciting development, for sure.
“Despite challenges, the outlook for phosphoric acid production remains positive, supported by technological innovation and sustainable practices. While it’s taken several years post-Covid for the phosphoric acid market to blossom again, the future does now look very promising, both for equipment providers such as Profile and for our industry overall.”
Prayon Technologies (PRT)
Prayon Technologies (PRT), the licensing division of Prayon, is internationally renowned for its phosphate production technologies. Currently, plants fitted with Prayon technology are responsible for one third of worldwide phosphoric acid production. Prayon’s notable achievements include more than:
• 130 references in over 30 countries
• 120 production processes
• 65 validated phosphate rock types.
Experts at PRT dedicate themselves to designing easily operable and highly reliable phosphoric acid plants. This expertise comes from the company’s know-how and its track record with production plants gained during more than 70 years of experience. Prayon incorporates the very latest process developments into its plant designs to benefit all of the phosphoric acid producers the company works with.
PRT offers the widest range of technologies for phosphoric acid production. Each of the company’s five processes has its own characteristics. This allows Prayon to offer its partners successful tailor-made production options. The ability to deliver operationally successful phosphoric acid plants is reinforced by incorporating premium-quality equipment specifically designed by Profile, the process filtration and liquid equipment division of Prayon.
Alongside the traditional route for producing feed phosphates from high-grade phosphoric acid, Prayon now offers two cutting-edge technologies that can use low-grade phosphate rock as a starting material. These innovative processes can significantly reduce production costs while generating feed phosphates of the same grade.
Prayon is aware that technological innovation will be vital for improving production processes to meet the needs of future generations. This includes developing technologies that are able to capture and use recycled raw materials. These will allow the phosphate industry to convert waste into valuable products while at the same time increasing the size of available phosphate resources.
PRT works closely with phosphoric acid producers to ensure they meet local environmental regulations. Reliable Profile-designed equipment, such as gas scrubbers and towers, enable businesses to reach high performance levels with close to zero emissions. The liquid bleed from these systems is either cleverly recycled into the process or concentrated to generate valuable co-products. Technologies are available to selectively remove deleterious and unwanted impurities (As, Cd, F, SO4, Mg, etc.).
Prayon has also developed leaching technologies – chemical beneficiation processes – for magnesium (Mg), cadmium (Cd) and total organic carbon (TOC). These can be added as stages between the existing mechanical beneficiation and the phosphoric acid plant. These beneficiation innovations will enable phosphate rocks with high Mg, Cd and TOC contents to be used in the production of high-grade fertilizers such as DAP, while meeting environmental standards and optimising production efficiency.
Our in-depth process knowledge and understanding is the key to getting the best from a phosphoric acid plant. Prayon, through its wide range of services, always accompanies the owner at each and every stage of their project – starting by providing a tailor-made plant design all the way through to offering consultancy services during plant operations.
The company’s expertise encompasses:
• Lab to semi-industrial scale testing and validation
• Plant simulation training
• Technical surveys
• Operational excellence through data management and plant optimisation.
GEA Group
With more than 100 years of experience in crystallisation alone, the company offers a range of production plant technologies able to meet the diverse requirements of the phosphate and fertilizer industries. They include:
• Evaporators
• Crystallisers
• Membrane filtration units
• Centrifugal decanter and separators
• Spray and fluid bed dryers for drying crystals or granulation.
GEA specialises in the production of water-soluble monoammonium phosphate (MAP) from phosphoric acid. The innovative production technology offered by the company is capable of manufacturing high-quality water-soluble MAP from lower quality merchant grade acid (MGA). This ground-breaking process reduces opex and/or capex costs as it avoids the need to purchase more expensive purified phosphoric acid (PPA) or integrate a purification line within the fertilizer production plant.
GEA’s manufacturing process can typically deliver a yield (i.e. the amount P2O5 recovered to the crystalline end-product vs the P2O5 contained in the feed acid) of between 50-70 percent. The exact yield depends on the impurity levels in the MGA and the purity/quality requirements (non-soluble content) of the final MAP product.
GEA’s technology for water-soluble MAP production has already been successfully implemented by an Eastern European customer. The new plant avoided considerable capital and operational expenditure by allowing non-purified MGA to be used as the phosphoric acid feed, while still delivering a pure MAP fertilizer with a high market value as the end-product. As a fertilizer, the crystalline end-product offers the following key benefits:
• Avoids clogging problems on spray systems and pumps
• Suitable for fertigation, foliar applications and fertilizer blends
• Low turbidity after dissolution in water
• High-throughput processing
• Free of chlorine, sodium and other deleterious elements
• Moderate solution pH – safer and less corrosive
• Laboratory back-up, support and expertise.
De Smet Agro
De Smet Agro (DSAG) has been providing project management, engineering, procurement and construction management services to the fertilizer industry for more than 65 years. The company, a division of De Smet Engineers & Contractors, is based near Brussels, Belgium, with satellite offices in France, Morocco, and India.
DSAG has strong and globally recognised expertise in the engineering and construction of fertilizer complexes, working in collaboration with multiple partners and different technology licensors. This has enabled the company to deliver more than 250 industrial plants in 35 countries since 1957 – including numerous sulphuric, phosphoric acid and fertilizer granulation plants.
The multi-disciplinary team at DSAG offers engineering services for new ‘greenfield’ plants. The company also offers revamping and capacity improvement projects at existing production sites.
DSAG is recognised worldwide as the most experienced and wide-ranging licensee for Prayon Technologies (PRT), offering all of the company’s industry-leading phosphoric acid production routes, and its processes for phosphoric acid derivatives and by-products. This longstanding cooperation with PRT, which dates from 1960, has delivered many notable project achievements globally.
DSAG has full in-house expertise for all the engineering, procurement and construction supervision steps needed to deliver phosphoric acid projects. (Prayon’s process design package being the starting point for these activities.) The company’s project capabilities cover the complete pro-DSAG possesses in-depth expertise for:
• Single and double crystallisation phosphoric acid processes
• Phosphoric acid purification technologies
• Phosphate salt technologies, including those for animal feed and food phosphates, and new processes such as those for soluble fertilizers
• Dicalcium phosphate (DCP) processes (HCl- or H2SO4 -based) including a phosphoric acid production process based on DCP Fluorine gas scrubbing
• Phosphoric acid concentration and fluosilicic acid recovery
• Phosphate rock solids or slurry handling and storage
• Acidic cooling tower design
• Gypsum transfer as solids or slurry, storage and valorisation.
Additionally, DSAG offers fully proven in-house technologies for nitrogen fertilizer production. The company’s nitrogen process design expertise covers synthesis, evaporation, crystallisation, prilling and granulation units for clients all over the world. Specific areas of expertise include:
• In-house fluidised drum granulation technology for ammonium nitrate products (AN/CAN/ASN) and calcium nitrate (CN)
• Prilling of low-density ammonium nitrate (LDAN).
• Ammonium Sulphate (AS)
DSAG also offers a comprehensive range of construction services for fertilizer granu-lation. These services cover the construction of granulation units for:
• Monoammonium phosphate (MAP)
• Diammonium phosphate (DAP
• NPKs more generally.
The company’s granulation expertise also includes the design of gaseous effluent cleaning systems.
To meet client or project needs, DSAG has the capability to team up with other recognised fertilizer technology providers/contractors, thanks to strong relationships built over decades. This provides industry customers with a single point of contact with complete responsibility for the delivery of their fertilizer projects.
DSAG provides a complete range of services to the fertilizer industry all around the world. These range from technical audits to the full delivery of EP and EPCM contracts and typically include:
• Technical audits
• Prefeasibility, feasibility studies, capex and opex estimates, including all on-site and off-site facilities
• Financial studies Overall project management Front-end engineering design (FEED)
• Basic and detailed engineering design
• Procurement
• Construction management and site supervision Training of client personnel
• Pre-commissioning and commissioning services
• Start-up assistance and performance guarantee tests.
Case study
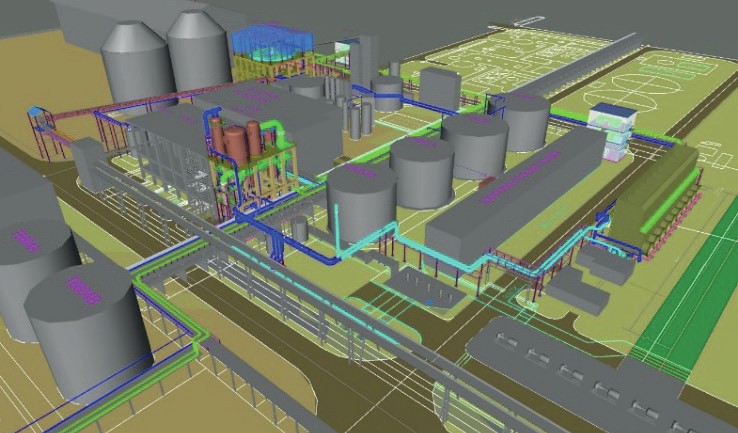
Client: JPMC
Location: Aqaba, Jordan
Project: Revamping an existing phosphoric acid plant
Due to decreased phosphate rock quality, the phosphoric acid plant requires extra facilities such as a rock dryer, a tilting pan filter, a concentration line and an acidic cooling tower to maintain the original capacity and the required merchant grade acid (MGA) quality.