Fertilizer International 525 Mar-Apr 2025
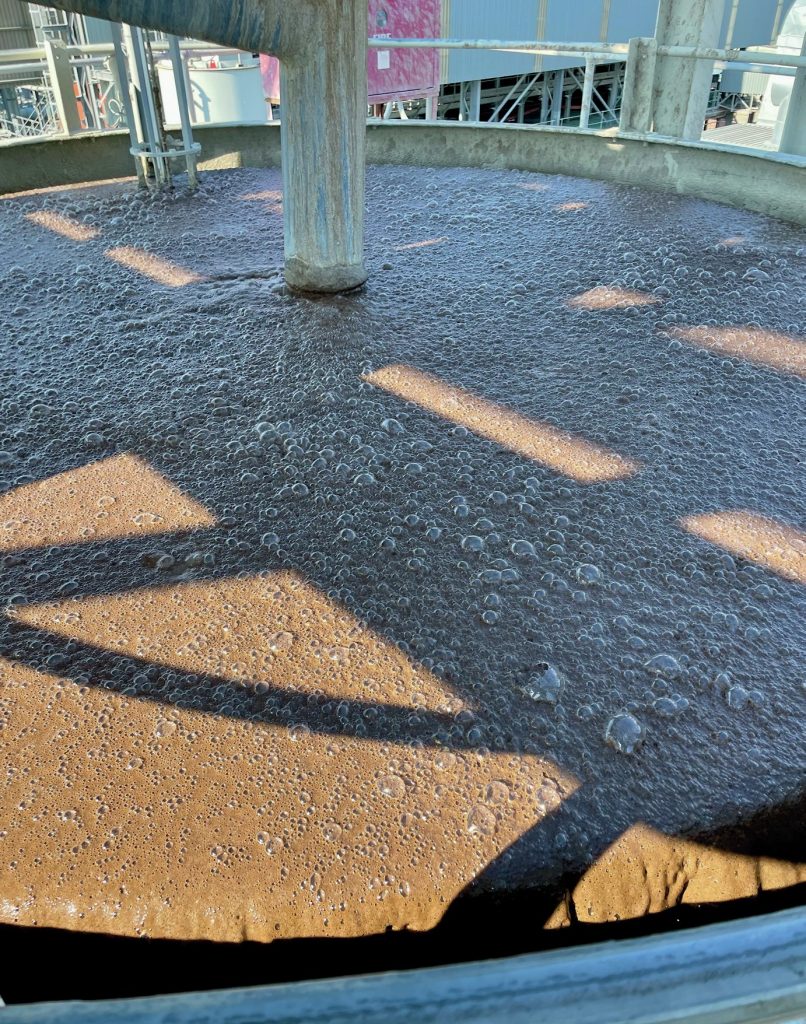
18 March 2025
Proven reagent innovations for phosphate flotation
P&K FLOTATION
Proven reagent innovations for phosphate flotation
In comparison to the conventional ‘Crago’ froth flotation process for phosphate ore beneficiation, the new reagent schemes introduced in this article achieve superior rougher flotation performance without requiring pH control during conditioning. As Arkema’s Guoxin Wang and Zhengxing Gu explain, this approach eliminates the need for diesel or fuel oil, simplifies the flotation process, and utilises more sustainable reagents.
Introduction
Phosphate ore mining and beneficiation involves multiple stages including: matrix mining, slurry transportation, washing, sizing, froth flotation, product handling, waste disposal, and water management.
The froth flotation of sedimentary phosphate ore practiced in Florida is typically divided into two circuits based on feed particle size. The coarse flotation circuit handles the -14+35-mesh fraction, while the fine flotation circuit processes the -35+150-mesh fraction.
The flotation circuit, an integral part of phosphate beneficiation, primarily uses the ‘Crago’ process developed in the 1940s. In this process, the phosphate feed is conditioned with a fatty acid collector and fuel oil or diesel as a secondary collector at a pH range of 9.0 to 9.3, with pH controlled using soda ash or ammonia. The rougher concentrate – consisting of phosphate and some fine quartz particles – is firstly scrubbed with sulphuric acid to remove fatty acids from phosphate particle surfaces and then undergoes a further flotation stage with an amine collector to obtain the final phosphate concentrate.
However, the use of fuel oil or diesel in the Crago process raises significant environmental concerns, due to their slow biodegradation compared to other reagents like fatty acids. Additionally, they may contain hazardous substances such as benzene, toluene, ethylbenzene, and xylene. The process also requires pH control, which complicates beneficiation and poses handling issues, particularly when hazardous pH modifiers like caustic soda and ammonia are used.
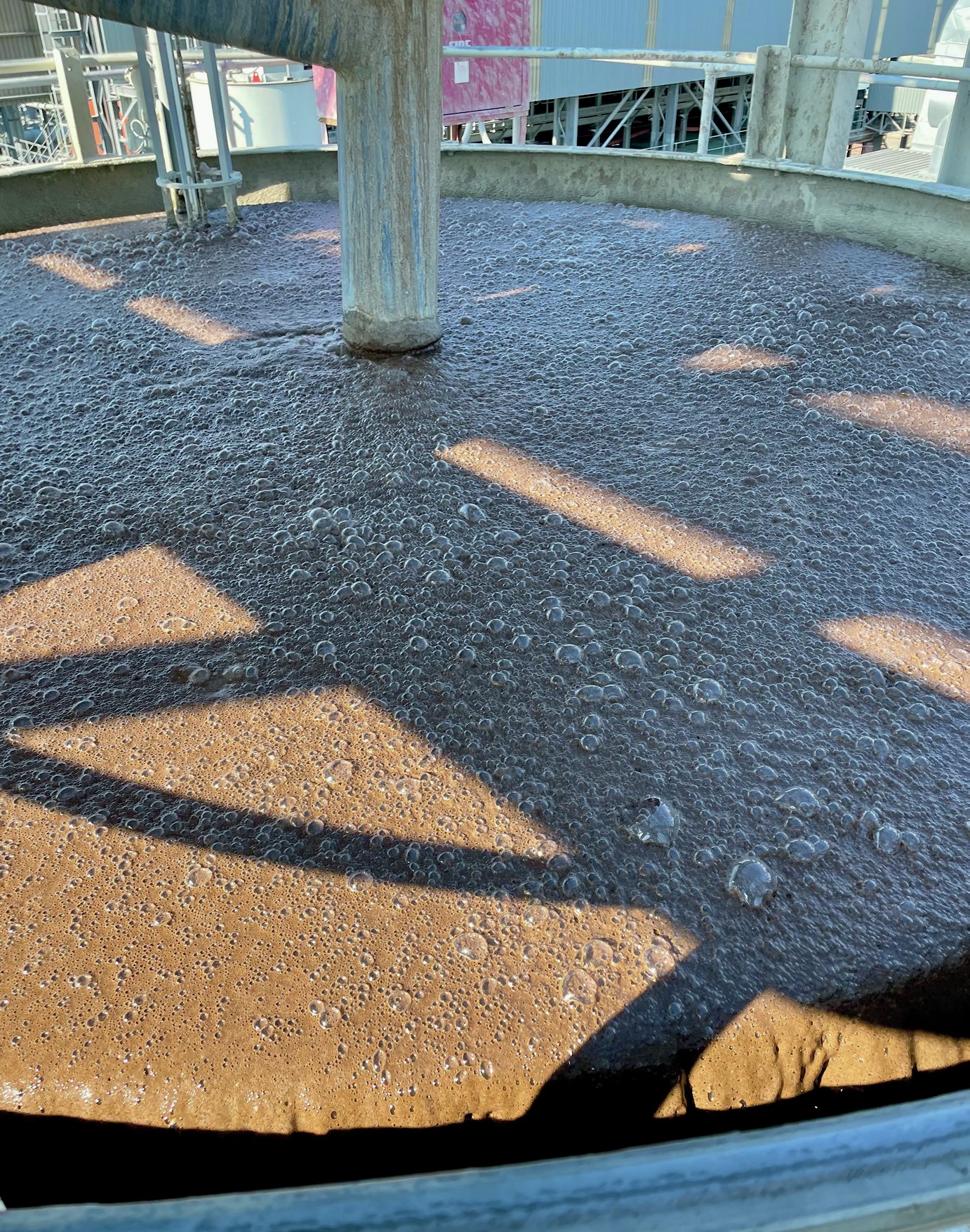
In recent years, Arkema has focused on developing new reagents for rougher flotation circuits that eliminate the need for pH modifiers and diesel (or fuel oil). These new reagent schemes simplify the flotation process, utilise more sustainable reagents, and enhance environmental stewardship.
In this article, phosphate feed samples from various mines were beneficiated using the rougher flotation circuit of the Crago process. We discuss the results of laboratory studies and plant trials and highlight the positive outcomes obtained for the new reagent schemes in three case studies.
Case study 1: Mine A – without pH modifier and fuel oil (patent granted)
In Mine A, the feed for the traditional rougher flotation process was conditioned with CustoFloat® FA (CF-FA) as the primary collector and fuel oil (FO) as the secondary collector in a 70:30 ratio, at a pH of 9.3, adjusted with soda ash (SA) as a pH modifier. After rougher flotation, the concentrate underwent acid scrubbing and amine flotation to produce the final concentrate.
Arkema developed a new collector, CustoFloat® 71C (CF71C), to streamline the process and eliminate the need for fuel oil. In this patent-granted reagent scheme, the feed was conditioned with the new CustoFloat® 71C collector and the promoter CustoPrep® 46 (CP46) without using fuel oil or a pH modifier.
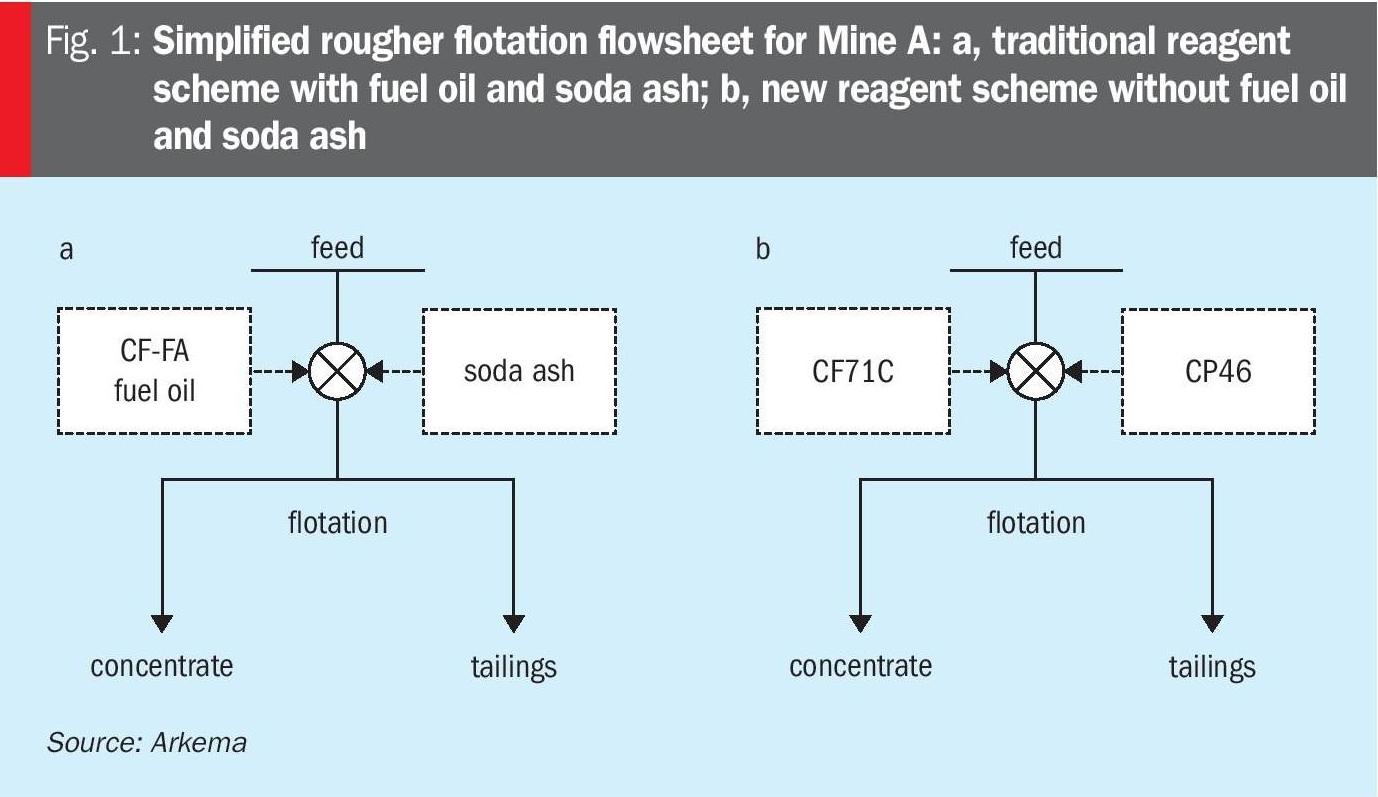
Figure 1 illustrates the simplified flotation flowsheets of both the traditional and the new reagent schemes. During the tests, the dosage of CustoPrep® 46 was varied at a fixed level of CustoFloat® 71C, and vice versa. Tables 1a and 1b summarise the lab and plant flotation results. The results show that the new reagent scheme achieved higher P 2 O 5 recovery while eliminating the need for fuel oil and pH modifiers.
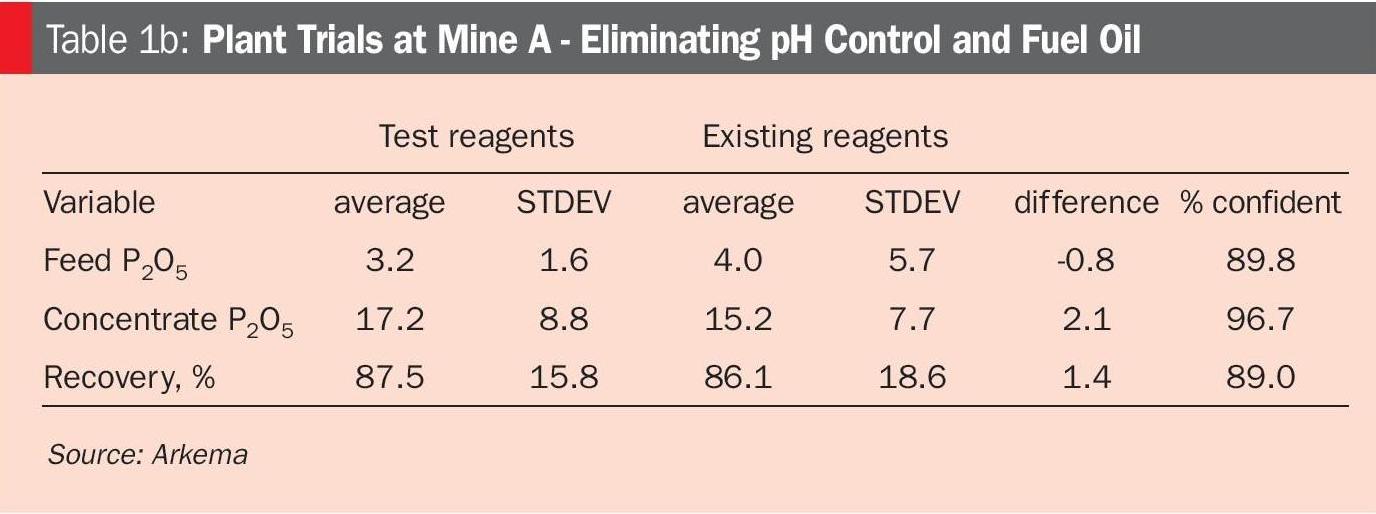
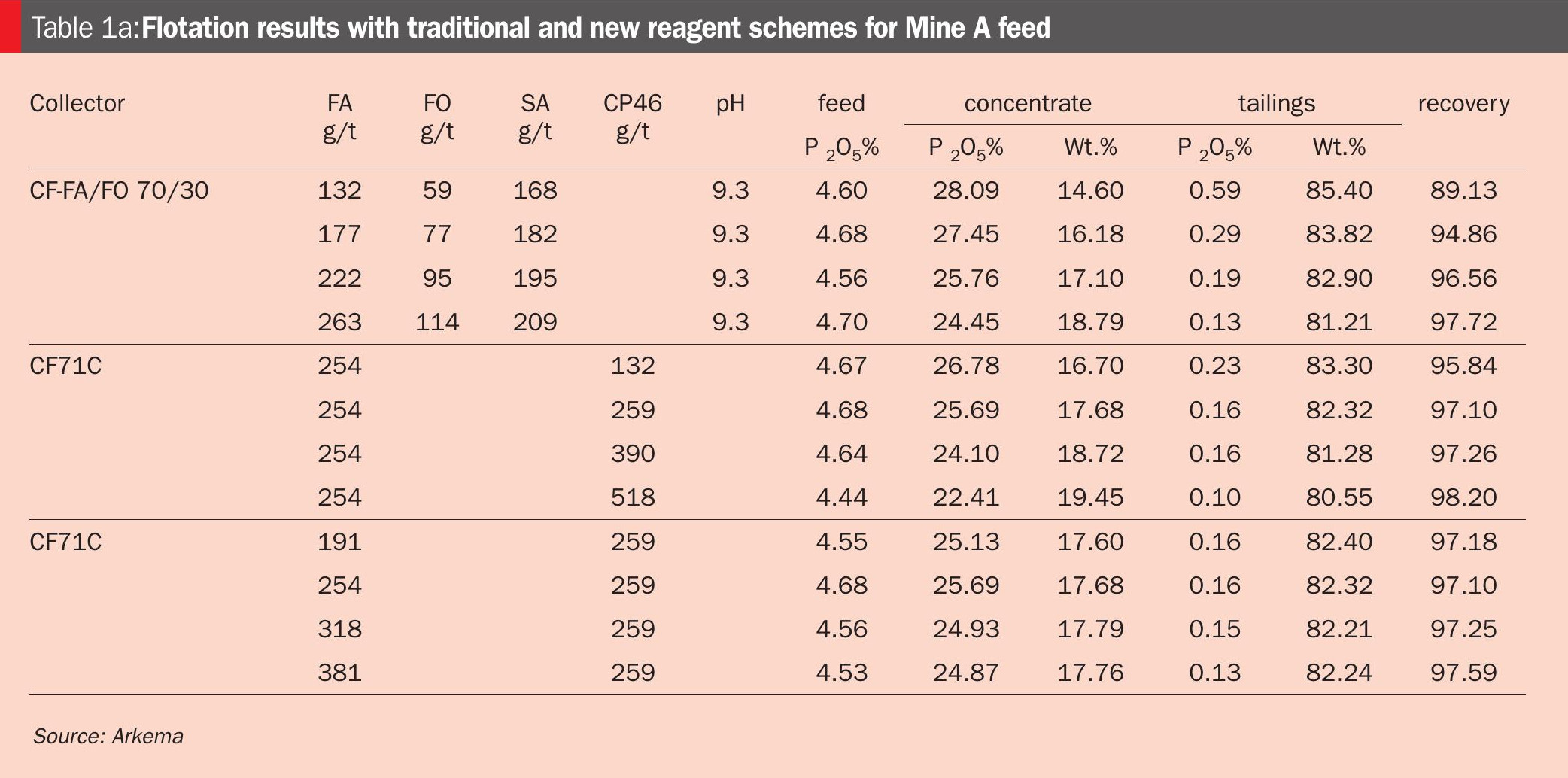
Summary of Mine A results:
- A month-long trial was conducted yielding positive results even with a lower feed grade
- The new reagent system resulted in higher rougher concentrate grade, leading to approximately 15% less CustAmine® consumption for silica flotation and an approximate 4% increase in overall recovery
- No soda ash needed for pH control
- Lower collector usage.
Case study 2: Mine B – without saponification and diesel (patent pending)
In Mine B, the fatty acid (FA) type collector is traditionally pre-saponified with soda ash, preparing it as a 5% soap dispersion, and the feed is conditioned prior to phosphate flotation with a soap collector and diesel at about 70% solids. Arkema formulated a new fatty acid type collector, CustoFloat® 390 (CF390), for Mine B. This new collector eliminates the need for pre-saponification and diesel, simplifying the process and potentially enhancing results.
Figure 2 shows the simplified flotation flowsheets for both the traditional and new reagent schemes. The flotation results for Mine B’s feed are summarised in Table 2. Notably, the new reagent scheme achieves better P2 O5 recovery compared to the traditional regent scheme.
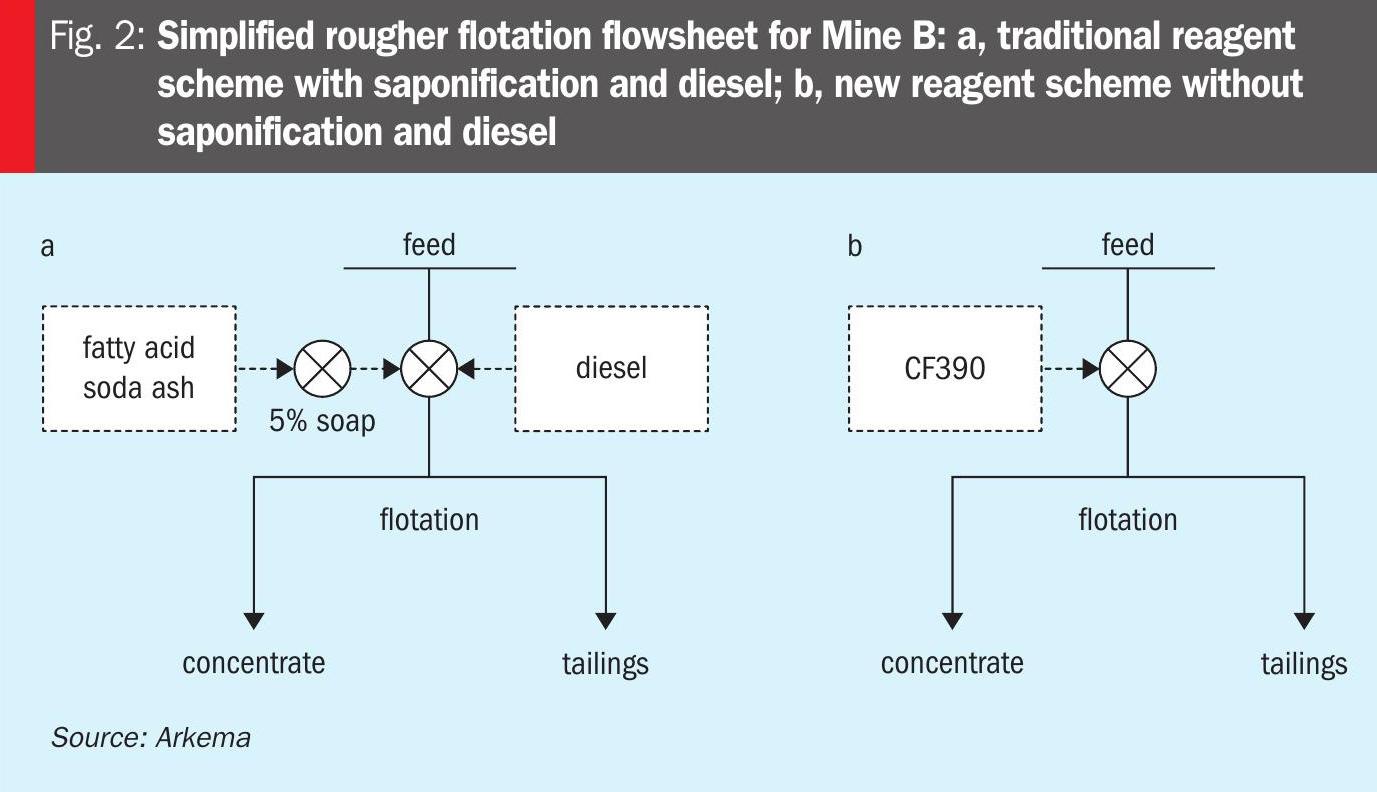
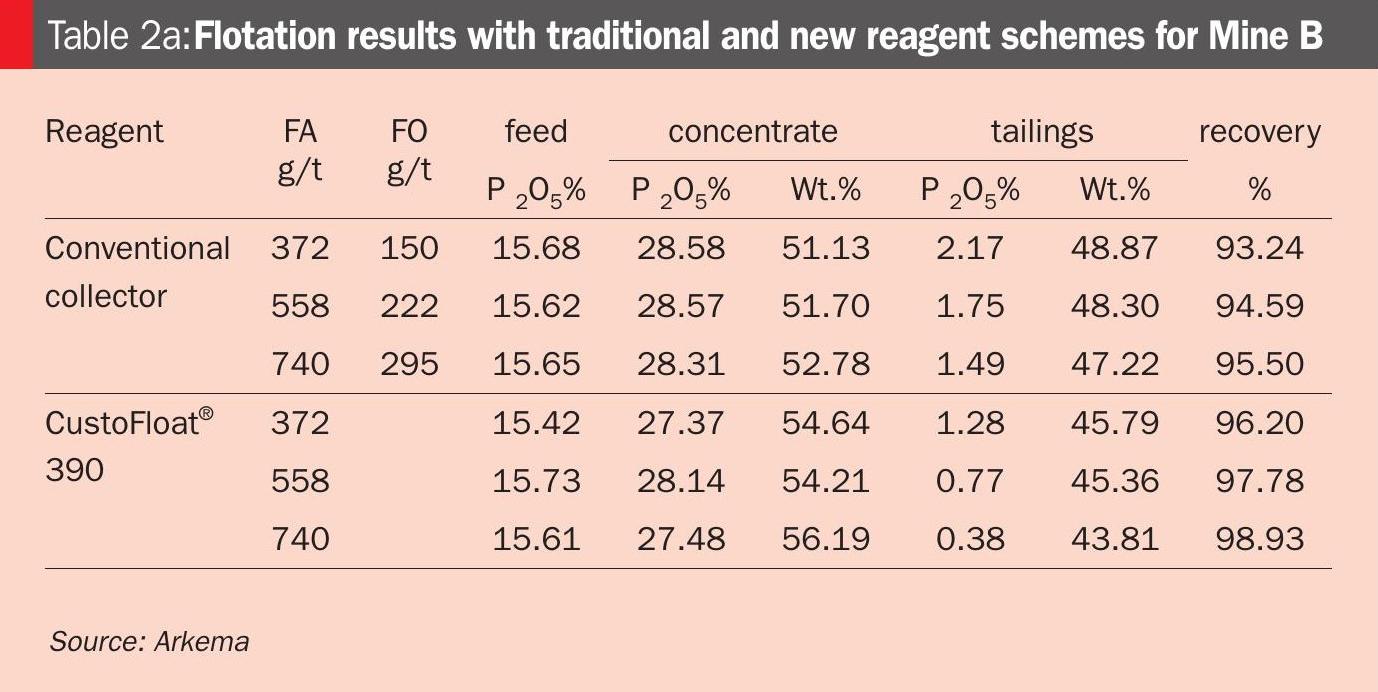
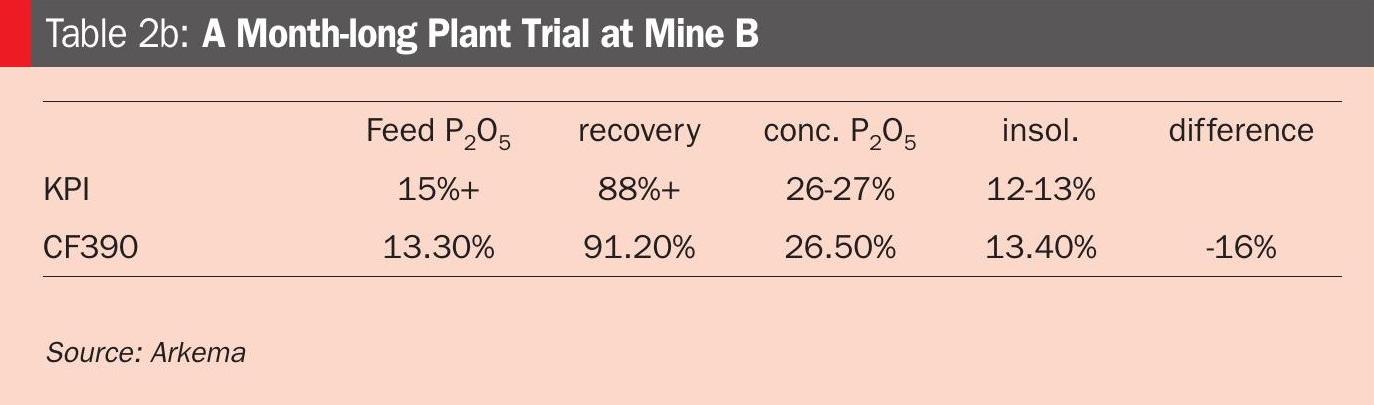
Summary of Mine B results:
- No diesel was consumed during the trial
• No soda ash was consumed (i.e., no saponification), simplifying the process
• Reduced sulphuric acid consumption for de-oiling
• Collector consumption was reduced
• Improved recovery.
“Arkema’s new reagent schemes, designed for various phosphate ores from different phosphate mines, have demonstrated superior separation performance without the need for the fuel oil, diesel, or pH modifiers required in conventional phosphate processing flowsheets.”
Case study 3: Mine C – without saponification and diesel
In Mine C, the ore is mined and initially sized at 35 mesh (0.425 mm) to reject low P2 O5 oversize waste, and then further sized at 65 mesh (0.212 mm) to obtain the -35+65 mesh (-0.425+0.212 mm) coarse feed. The minus 65 mesh fraction is deslimed at 400 mesh (0.038 mm) to remove fines, resulting in a -65+400 mesh (-0.212+0.038 mm) fine feed.
Traditionally, the beneficiation plant used a fatty acid soap collector and diesel for both the coarse and fine feeds in the flotation process. The rougher concentrate is then acid scrubbed, rinsed and amine flotation is then carried out to produce the final concentrate. Recently, a new reagent scheme was recommended for the rougher floatation circuit. This introduced CustoFloat® 391, a fatty acid collector, to replace the combination of soap and diesel used in the original flowsheet.
The lab flotation results for both coarse and fine feeds, using the traditional and new reagent schemes, are summarised in Table 3. Results confirm that the new reagent scheme achieves similar or better flotation performance, with significantly lower reagent consumption, while also eliminating the use of diesel. This new scheme has been in commercial use since 2022.
Conclusions
The conventional ‘Crago’ flotation process for the beneficiation of sedimentary phosphate ore typically involves conditioning the phosphate feed with a mixture of a fatty acid type collectors and fuel oil (or diesel) at alkaline pH, with solids exceeding 70% for rougher flotation. In contrast, the new reagent schemes described in this article achieve superior rougher flotation performance without requiring pH control during conditioning.
This approach eliminates the need for diesel or fuel oil, simplifies the flotation process, and utilises more sustainable reagents, contributing to enhanced environmental stewardship. Subsequently, these new reagent schemes have been successfully commercialised, offering more efficient alternatives to traditional flotation methods.
It is important to note that, in general, there is no ‘universal’ reagent or reagent scheme for phosphate ore processing. Instead, reagents need to be developed according to the specific characteristics of each phosphate ore.
As shown in this article, Arkema’s new reagent schemes, designed for various phosphate ores from different phosphate mines, have demonstrated satisfactory separation performance without the need for fuel oil, diesel, or pH modifiers required in conventional phosphate processing flowsheets. The success of these new schemes has been proven through beneficiation plant trials and subsequent commercial operations.
CRU Phosphates+Potash Expoconference 2025
Guoxin Wang of Arkema will be available to discuss flotation technology at the conference in Orlando.
Note: CustAmine, CustoFloat and CustoPrep are registered trademarks of the Arkema Group of Companies.