Fertilizer International 525 Mar-Apr 2025
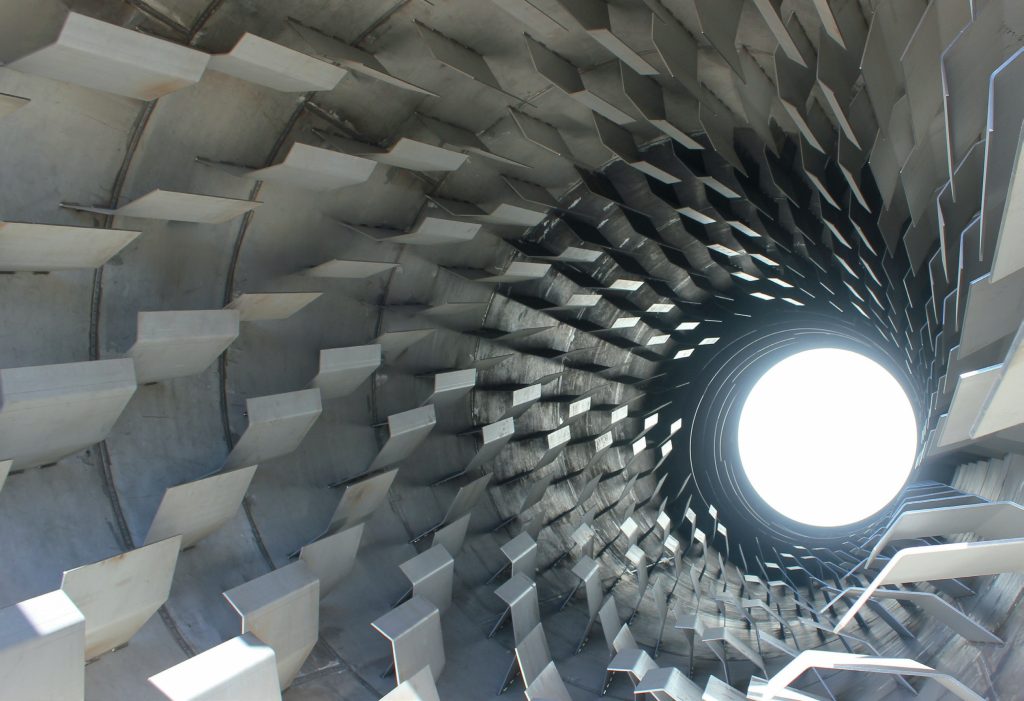
18 March 2025
Rotary coolers: the key to superior fertilizer cooling
FOCUS ON COOLING EQUIPMENT
Rotary coolers: the key to superior fertilizer cooling
Effective cooling is a vital step in fertilizer production as it directly impacts product quality, operational safety, and process efficiency. Rotary coolers combine durability and flexibility with the delivery of uniform results. They remain a popular choice with fertilizer producers, explains Shane Le Capitaine of FEECO International, thanks to their ability to meet the industry’s rigorous demands.
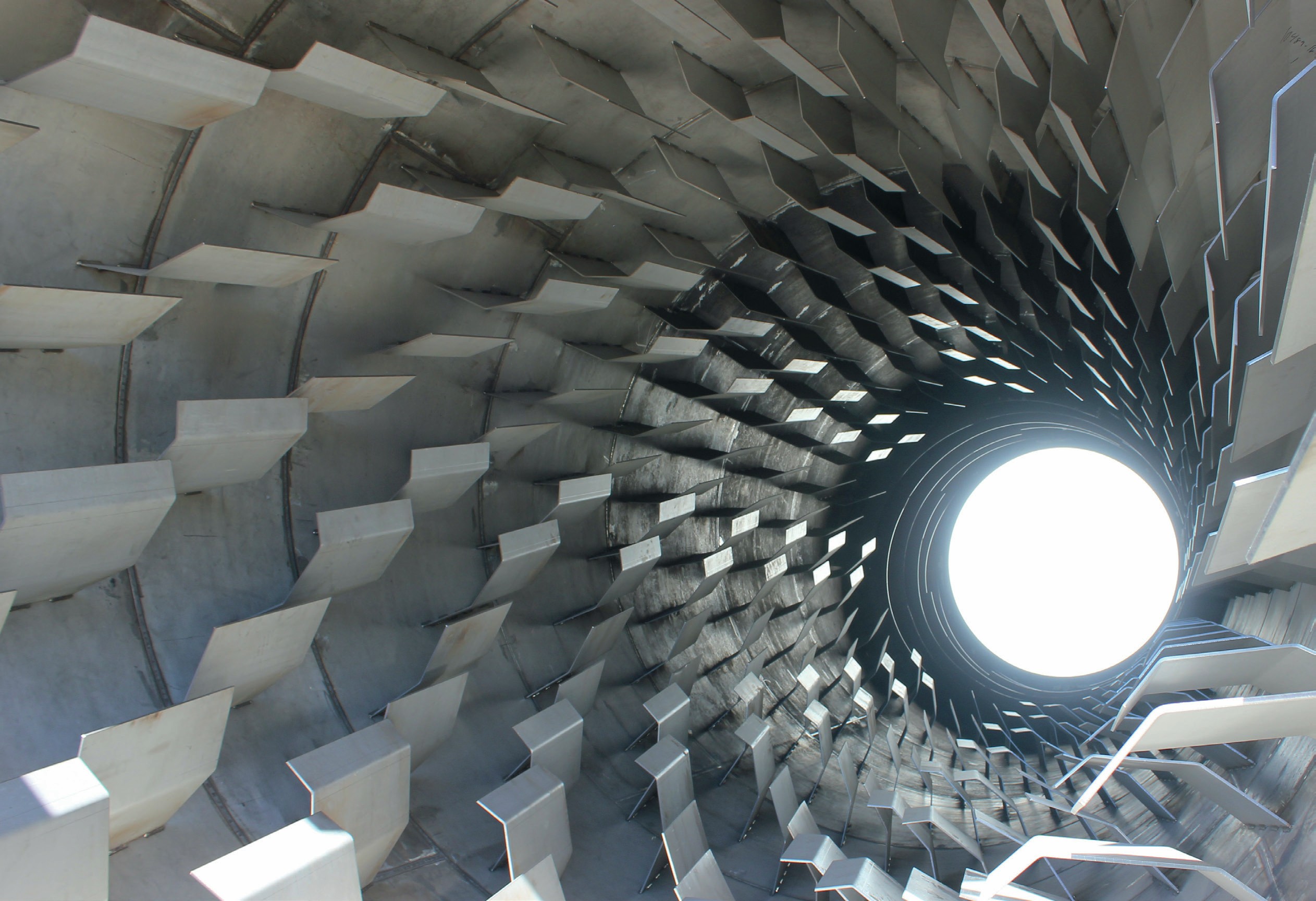
Introduction
From preventing caking to safeguarding downstream equipment, proper cooling is essential for producing a resilient, high-performance fertilizer product. Among the available cooling technologies, rotary coolers continue to dominate, offering robust performance, design flexibility, and consistent results. This article explores the importance of cooling in fertilizer production, the advantages of rotary coolers, and key considerations for optimising the cooling process.
Why cooling is necessary
Whether producing diammonium phosphate (DAP), ammonium sulphate, potash, NPK, or something in between, cooling is a vital finishing step in the fertilizer production process, achieving several objectives that allow fertilizer producers to bring a quality product to market. By cooling product exiting the dryer, fertilizer producers can:
Prevent caking. As any fertilizer producer can confirm, the presence of caking is highly problematic, resulting in lost product, process upsets in downstream equipment, and dangerous storage conditions.
Caking occurs when crystal bridges begin to form between particles. While additional measures to combat caking may be necessary, depending on the type of fertilizer and its hygroscopicity, cooling helps to maintain product integrity and reduce the potential for caking.
When warm granules are not properly and uniformly cooled, moisture can migrate within the product or between particles, allowing crystal bridges to form. These interparticle bridges are the foundation of product caking.
Valuably, cooling the product exiting the dryer, by stabilising the moisture content, prevents caking and promoting a more flowable product.
Reduce potential for bacterial growth. In addition to preventing the formation of crystal bridges, reducing the material’s temperature also helps to guard against bacterial or mould growth during storage.
Protect downstream equipment. Fertilizer typically exits the dryer at around 90°C (200°F), a temperature that could easily damage handling and bagging equipment. Cooling the product down to less than 50°C (120°F) is therefore an effective measure for protecting downstream equipment from potential heat damage.
Create a more resilient product. Cooling is the final step needed for producing a finished, resilient, and flowable fertilizer product that is less prone to attrition and dust generation. Importantly, by stopping the drying process, it prevents over drying and potential product degradation from any residual heat.
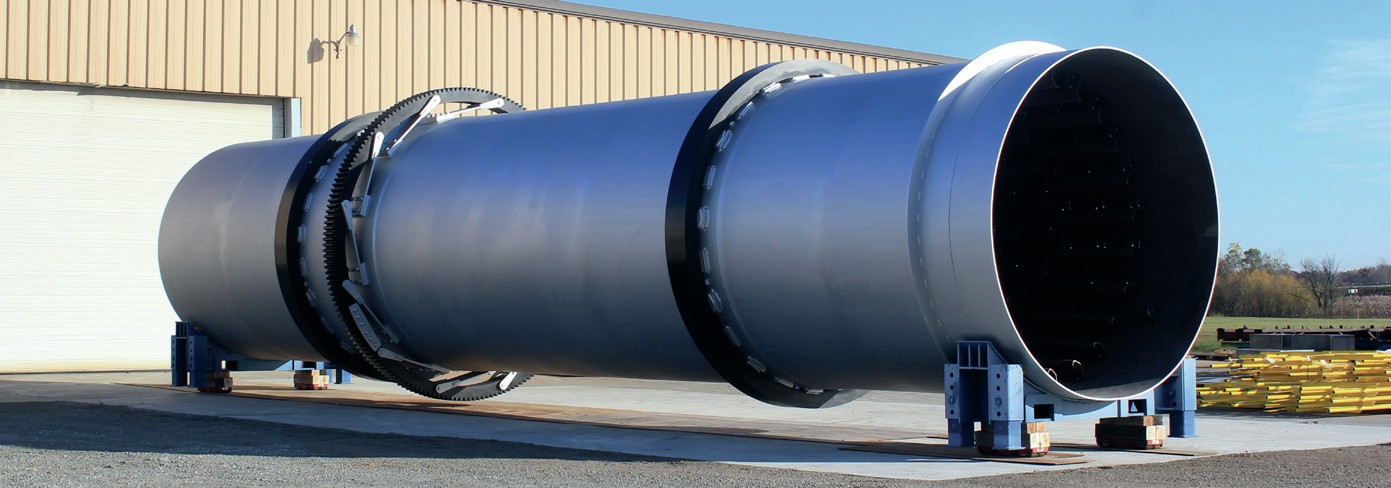
Why rotary cooling?
Although alternative technologies exist, rotary coolers remain a preferred technology among fertilizer producers for a number of reasons:
Heavy-duty build. Constructed from heavy-duty materials and equipped with robust drive assemblies, rotary coolers are incredibly durable. When properly maintained, rotary coolers can provide decades of unwavering service, despite the harsh demands of continuous fertilizer production.
Flexible design. Rotary coolers offer a high potential for customisation, particularly when it comes to maximising heat transfer efficiency. Flights – material lifters affixed to the cooler shell interior – pick up material and allow it to cascade through the chilled air stream in the drum’s cross section. Both flight geometry and pattern can be customised to work best with the material being handled. Taking account of the angle of repose, crush strength, and other properties helps achieve the most efficient results possible.
Capacity. Fertilizer producers also continue to use rotary coolers for their high throughput. This is unsurprising given that the large tonnages typical of the industry. For example, a rotary cooler with a 10-foot diameter and 40-foot length can easily handle up to 200 t/h of granulated fertilizer, depending on the material’s bulk density and cooling requirements.
Uniform results. The fertilizer market has become increasingly discerning thanks to advances in technology. Consequently, product quality issues such as dust and caking are simply no longer acceptable.
Cooling equipment must be able to consistently deliver uniform results, as any variation could result in lower product quality. And where uniformity is concerned, rotary coolers offer the most effective solution for many producers. That is because the heat transfer efficiency created from the flights, paired with the tumbling action of the drum, ensures all solids are uniformly exposed to the cooling medium.
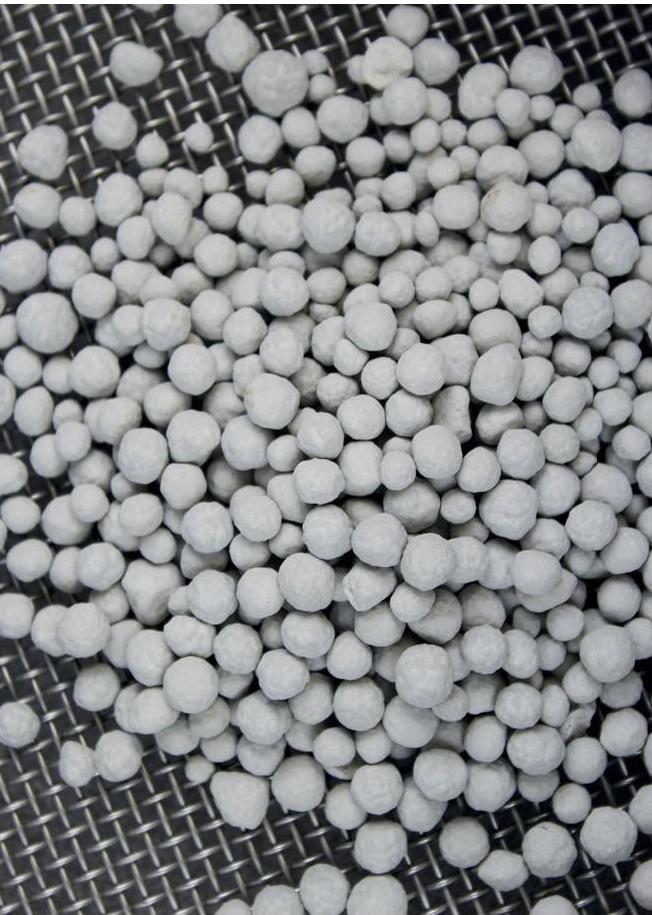
Factors to consider in fertilizer cooling
Several factors must be considered in the design and operation of a rotary cooler for fertilizer:
Material compatibility. Fertilizer products are frequently corrosive, abrasive, or both. This requires careful selection of construction materials to ensure material compatibility, particularly at the cooler inlet, where the higher temperature of the incoming material may exacerbate wear.
Poorly chosen construction materials for components in contact with the fertilizer product – such as the cooler shell and flights – will result in rapid degradation of exposed parts.
Retention time. Also referred to as residence time, this is the amount of time required to reach the desired product outlet temperature under the process conditions. In cooler design, retention time is calculated from a combination of factors including feed rate, drum speed, drum slope, air flow velocity, and drum size (length and diameter).
If the cooler is engineered based on representative product data, retention time is unlikely to need adjustment. However, to optimise cooling conditions, it may be necessary to increase retention time, especially if process conditions change, or operators struggle to achieve efficiency.
In existing systems, retention time can be increased using one of two main approaches: either by installing a dam or by slowing the drum’s rotational speed. Both options have potential process implications and therefore should be carried out with the help of an expert.
Entrainment. This occurs when particles become suspended in the air flow and are carried out through the exhaust gas system. This is problematic for a number of reasons.
While a dust collection system is already required, excessive fines in the off gases will either need to be reintegrated into the system, used elsewhere, or taken as a loss.
Care, therefore, must be taken during the initial design stages to reduce the potential for entrainment. Minimising entrainment relies on finding the right balance between drum size, air flow velocity, particle size distribution, and bulk density.
Efficiency. The high rates of production associated with fertilizer plants make optimising for efficiency particularly important, as even small inefficiencies can quickly turn into major losses.
Cooling efficiency can generally be measured by comparing the temperature of the inlet material with the outlet gas temperature – with the difference between the two being a good indicator of efficiency. A small temperature difference is desirable as it indicates that the air flow has extracted as much heat as possible from the material.
A well-optimised rotary cooler achieves an outlet gas temperature within 10°C (15°F) of the inlet material temperature, indicating maximum heat absorption by the cooling medium. A large temperature difference, in contrast, indicates unused cooling potential and consequently wasted energy.
While the original design of the cooler is a major factor in the unit’s operating efficiency, further efficiencies can be gained by recycling air to reduce mechanical cooling or air treatment requirements on the front end of the system.
Optimising efficiency also reduces the load and strain on auxiliary systems such as fans, motors, and dust collection systems, contributing not only to lower energy costs but also to a longer service life and lower maintenance costs.
Conclusions
Effective cooling is indispensable in fertilizer production, serving as a vital step that directly impacts product quality, operational safety, and process efficiency. Rotary coolers, with their durability, flexibility, and ability to deliver uniform results, remain a preferred choice for handling the rigorous demands of this industry.
By considering factors such as material compatibility, retention time, and entrainment during system design and operation, fertilizer producers can achieve an efficient, reliable cooling process that delivers a high-quality product ready for market. In future, innovative cooling solutions will play a key role in helping the fertilizer industry meet increasing quality standards and production demands.