Nitrogen+Syngas 394 Mar-Apr 2025
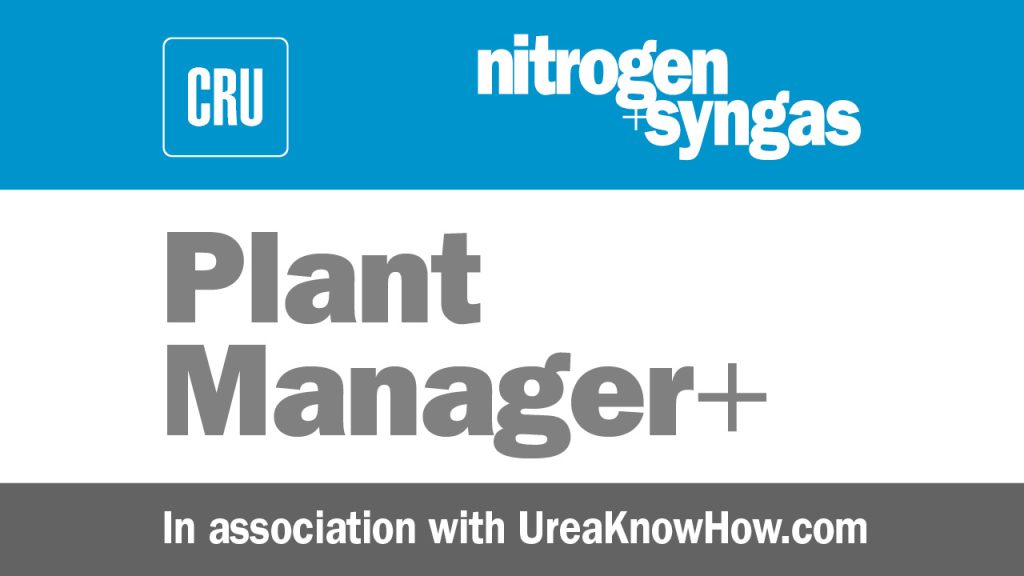
19 March 2025
How to solve stripper efficiency issues (part 5)
In part 5 of this series on stripper efficiency issues we conclude the discussion with a focus on fouling inside stripper tubes.
Fouling inside tubes
During operation solid iron oxides deposit as a scale in the bottom part of the stripper tubes. While corrosion rates are highest in the top part of the tubes, scaling in the stripper tubes takes place in the bottom half of the tubes.
What are the consequences of this scaling?
The scales lead to a lower stripper efficiency resulting in a larger recycle of ammonium carbamate via the recirculation section. This recycle via the recirculation section also contains water (some 35 wt-%), which negatively influences the urea conversion rate in the reactor. This leads to a higher load on the stripper, whose capacity is already limited due to the scaling leading to even lower stripper efficiency. This negative spiral leads to more steam consumption and possibly a lower plant load or more ammonia losses. 1% lower urea conversion leads to some 25 kg/t higher steam consumption or for a 2,000 t/d urea plant: €180k/year additional steam costs (2,000 t/d * 365 days/year * 25 kg/t * €10/t steam * 1/1000 t/kg).
A lower stripper efficiency leads to a higher load on the recirculation heater and in case that heater is also already limited due to scaling, more load will be put on the further downstream sections. This will lead to more ammonia emissions from, e.g., the urea solution tank, via the stack to atmosphere. For example, 50 kg/hour more ammonia emission will lead to €175k/year additional losses (50 kg/hr * 24 hr/day * 365 days/yr * €400/t NH3 * 1/1000 t/kg).
The layer of scales has a negative influence on the heat transfer from the steam side (shell) to the process side (tubes). A larger steam pressure will be required to compensate for this influence. This leads to higher tube wall temperatures. The corrosion rate is exponentially related with the temperature (every 10°C higher temperature doubles the corrosion rate). A higher tube temperature thus increases the corrosion rate leading to a shorter lifetime of the stripper. One year shorter lifetime will cost the end user some €200k (assuming €4 million for a new stripper which has a typical lifetime of 20 years).
And finally, in case the scaling on the stripper tubes becomes too thick it will no longer be easy/possible to perform eddy current wall thickness measurements leading to a risk of unexpected tube ruptures. This leads to large ammonia emissions and an unexpected shutdown.
The scales in the stripper tubes are too hard to be removed by high pressure water flushing. Stamicarbon, together with VECOM in the Netherlands, has developed a chemical cleaning procedure to remove these scales.