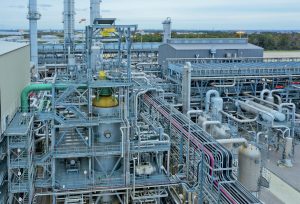
Towards an emerging hydrogen economy
Low carbon intensity hydrogen and ammonia production schemes from KBR, Air Liquide, Mitsubishi Heavy Industries, Casale and Johnson Matthey.
Low carbon intensity hydrogen and ammonia production schemes from KBR, Air Liquide, Mitsubishi Heavy Industries, Casale and Johnson Matthey.
“ The need for technical knowledge and insights has never been more important.”
Ammonia prices are expected to remain soft moving through January with little in the way of price support from both a supply and demand perspective. Weakened global sentiment was characterised by news of January’s Tampa settlement $100/t down on December at $525/t CFR, with further declines anticipated in Q1 once the Gulf Coast Ammonia (GCA) project comes online. Traders returned to their desks in the New Year and ammonia prices extended losses amid a stable supply outlook and a distinct lack of downstream industrial and fertilizer demand.
Data has always been crucial for successful operations in the chemical industry, but the growing volume of data is only as good as our ability to analyse it. Now, the market is about to experience a step change in data assessment, and Clariant is fully on track, thanks to cutting-edge technologies for real-time data monitoring, visualisation, and information exchange.
KBR offers an end-to-end digitalisation solution specifically designed for green ammonia plants to balance the available renewable resources and consistently deliver the lowest levelised cost of green ammonia (LCOA). This article outlines some of the key modules of the KBR end-toend digitalisation solution developed to overcome the challenges in green ammonia operation and achieve best in class, safe and reliable plant operation.
Ammonia prices are expected to remain soft moving through January into February, with little in the way of price support from both a supply and demand perspective. January’s Tampa settlement was $100/t down on December at $525/t CFR.
OCI Global says that it has reached an agreement for the sale of 100% of its interest in its large-scale nitrogen fertilizer subsidiary the Iowa Fertilizer Company LLC, located in Wever, Iowa, to Koch Ag & Energy Solutions for $3.6 billion. Completion of the transaction remains subject to US anti-trust approval and other customary closing conditions. The transaction is expected to close in 2024. Morgan Stanley & Co. International plc is serving as financial advisor to OCI on the transaction. IFCO produced 1.2 million t/a of urea ammonium nitrate (UAN) in 2021 and 700,000 t/a of anhydrous ammonia, as well as 700,000 t/a of diesel exhaust fluid (DEF).
In spite of nearly two years of western sanctions, Russian exports of nitrogen fertilizer have recovered almost to pre-war levels, while high prices led to record earnings in 2022.
As Europe struggles to move away from its previous dependence on imported Russian natural gas, prices have been high and volatile, with a corresponding catastrophic impact upon domestic ammonia production.
We are very pleased to be able to tell you that, as of this issue, Nitrogen+Syngas magazine has a new publisher. Or rather, an old publisher, as the magazine is now once again part of the CRU Group.