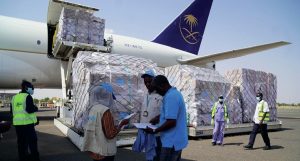
2020 A tumultuous year
A look back at some of the major events of 2020 for the nitrogen and syngas-based industries, as well as a look forward as to how 2021 might look.
A look back at some of the major events of 2020 for the nitrogen and syngas-based industries, as well as a look forward as to how 2021 might look.
thyssenkrupp Industrial Solutions discusses a revamping concept to reduce CO2 emissions by replacing some of the hydrogen in the front end of the ammonia plant with green hydrogen, KBR and Casale report on revamp options to increase the capacity of vintage ammonia plants in the former Soviet Union, Johnson Matthey presents a novel integrated ammonia flowsheet for the production of ammonia, methanol, urea and UFC and Arvos | Schmidtsche Schack discusses the benefits of a new process gas boiler.
Ammonia prices have been on a rising trend over the past few months as plant closures begin to make themselves felt. Yara’s Baltic ammonia price also rose sharply at the start of October, and Nutrien’s announcement of the closure of its PCS-03 plant on Trinidad helped lift prices, with Yara and Mosaic’s contract prices rising $16/t in October.
Market Insight courtesy of Argus Media
Recent protests in Belarus have triggered a wave of share price volatility, London’s Financial Times reported on 18th August.
The last three years has seen a renaissance in fertilizer production and blending in sub-Saharan Africa. We highlight the expansion of capacity in Nigeria and other countries within the region.
Enhanced efficiency fertilizers (EEFs) occupy a small but high-value segment of the overall fertilizer market, although their production and use is accelerating. This trend is unsurprising given that their higher costs are usually more than offset by better efficiency and lower application rates.
The ammonia market continues to be oversupplied, and prices have dropped to historically low levels. Yuzhnyy rates dropped to $175/t f.o.b. in July. In spite of shutdowns in Trinidad and elsewhere, demand remains sluggish and recovery from the Covid epidemic is patchy, especially in the US.
Spanish fertilizer producer Fertiberia is teaming up with energy firm Iberdrola to build Europe’s largest plant for generating green hydrogen for industrial use – in this case ammonia production. The 100MW solar plant and accompanying 20 MWh lithium-ion battery system and 20MW electrolytic hydrogen production system will be built at a cost of $174 million, and electrolyse water to produce 720 t/a of hydrogen. When fed into Fertiberia’s existing ammonia plant at Puertollano, 250km south of Madrid, the hydrogen will allow a 10% reduction in natural gas use by the plant, saving the company 39,000 t/a in annual CO 2 emissions. Start-up is planned for 2021. Fertiberia will also use electrolysis-generated oxygen as a raw material for nitric acid, which is used to produce ammonium nitrate at the site.
TechnipFMC’s EARTH ® technology, with its structured catalyst jointly developed by TechnipFMC and Clariant, has been proven to be a cost effective way to drastically improve productivity and energy efficiency of the steam reforming process, while reducing the CO 2 footprint per unit hydrogen and syngas product. The technology can be applied in projects to increase the capacity of ammonia and methanol plants and allows significant reduction of greenhouse gas emissions. S. Walspurger of Technip Benelux B.V. and S. Gebert of Clariant GmbH report on the EARTH ® technology and its applications.