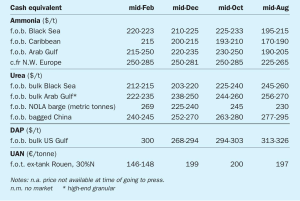
Price trends
Alistair Wallace, Head of Fertilizer Research, Argus Media, assesses price trends and the market outlook for nitrogen.
Alistair Wallace, Head of Fertilizer Research, Argus Media, assesses price trends and the market outlook for nitrogen.
The falling film high pressure carbamate condenser (HPCC) was the first type of high pressure carbamate condenser applied in urea stripping plants. Did you know that the first Snamprogetti stripping plants also had falling film carbamate condensers? In 1978 Mr Umberto Zardi, later founder of Casale, invented the horizontal kettle type condenser for Snamprogetti urea plants.
Lessons can be learned from the challenges faced during the construction, commissioning and start-up phases of major projects. In this article challenges and experiences are shared from the recent successful commissioning of ammonia and urea plants around the world, including projects in Indonesia, India, Egypt and the Middle East.
New ammonia and urea plants in Nigeria and Ethiopia are part of a wave of new capacity in Sub-Saharan Africa, and may help pull up regional demand from its current low base level.
The impact of coronavirus on both supply and demand continues to provide considerable uncertainty to the market. With much of Hubei province on lockdown, and a corresponding reduction in ammonia demand for DAP production, Chinese imports appear to be down, pushing more ammonia onto the international market and creating generally bearish sentiment.
AmoMax ® -Casale is a new ammonia synthesis catalyst jointly developed by Casale and Clariant. Retaining the same superior resistance to ageing, poisoning and mechanical strength as the well-known wustite-based catalyst, AmoMax ® 10, the new catalyst is significantly more active. C. Berchthold of Clariant and S. Panza of Casale explain the advantages of AmoMax ® -Casale and share the start-up experience of the first commercial reference.
At the Nitrogen+Syngas Conference 2020, held in The Hague, Netherlands, Haldor Topsoe launched its new TITAN ™ series of steam reforming catalysts. The company says that the new series, which consists of the RC-67 TITAN and RK-500 TITAN catalysts, offers improved performance and longer catalyst lifetime thanks to the hibonite-rich composition. The addition of titanium promoters adds exceptional mechanical strength while a seven-hole cylindrical shape yields both a very low pressure drop and a high surface area. Pressure drop build-ups in syngas plants can cause unscheduled downtime and cost millions of dollars, while thermal instability during operation can lead to operational risk and reduce plant lifetime. Topsoe says that the catalysts can mitigate these risks, ensuring lower operating costs, increased profit margins, and reduced energy usage.
Schoeller-Bleckmann Nitec (SBN), an experienced manufacturer of high pressure equipment for ammonia and urea plants for many years, also helps customers when things go wrong. SBN has come to the aid of operators on numerous occasions, helping them return their plant to operation as soon as possible when a problem occurs. R. Bunzl discusses SBN’s approach to finding solutions to a number of exceptional problems in urea equipment.
This year’s Nitrogen + Syngas conference was held from 17-19 February in The Hague, Netherlands.
The grave economic and human health consequences of the global spread of coronavirus (Covid-19) deepened in March.