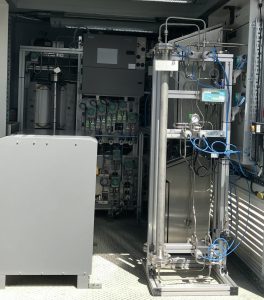
Highly optimised ammonia synthesis catalysts
Ammonia synthesis catalysts have seen major improvements over the last 100 years, and they are highly optimised with respect to activity, thermal stability, and poisoning resistance. Improving such catalysts even further requires a deep understanding of their structure and the impact of different parameters on performance. Clariant, Johnson Matthey and Topsoe report on their studies and developments in ammonia synthesis catalysts.