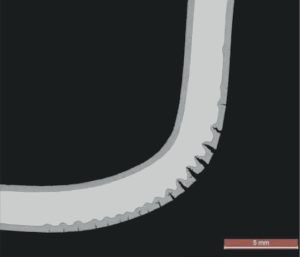
Nitriding in ammonia converters: behaviour, experience, and solution
The internals of ammonia synthesis converters are generally made of austenitic stainless steel to withstand the harsh operating conditions (high temperature, high pressure and synthesis gas containing hydrogen and ammonia). Since nitriding is the most critical material degradation for the converter internals, Casale has set up a large nitriding analysis campaign. In the last decade, samples of materials operated under different pressures and temperatures and for different time spans have been tested and analysed. The data obtained has been used to increase nitriding knowledge and to establish a correlation to predict nitriding rate to allow the most suitable material and relevant thickness to be selected. L. Redaelli and G. Deodato of Casale report on how this correlation was established and provide valuable insight on this phenomenon and how to predict and control it.