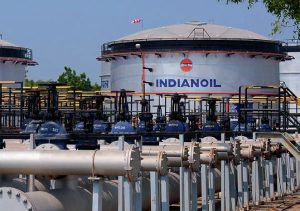
Sulphur Industry News Roundup
Storm Uri which blanketed the southern states of the US with snow, and led to widespread power outages in Texas, has had a major impact upon US Gulf Coast and Southern-Midwest refined products supply. Most Gulf Coast refineries were shut down or forced to operate at reduced rates. IHS Markit estimated that more than 5.2 million bbl/d of Gulf Coast capacity and 730,000 bbl/d in PADD 2 was impacted by the winter weather at its height, and close to 20% of lower 48 US natural gas production was shut-in in the first half of February. A drop in crude oil production of between 2.2 and 4 million bbl/d was estimated.