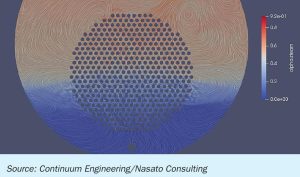
Hidden opportunity: the water side of sulphur recovery units
Failure investigations, equipment design and process upgrade projects for SRUs often overlook the impact of water quality. In this article E. Nasat o of Nasato Consulting and L. Huchler of MarTech Systems explore impacts of higher heat transfer rates, control of boiler and condenser water chemistry, conventional equipment design/configurations and monitoring program designs. SRU operators can improve the effectiveness of their failure investigations by implementing a broader, more holistic approach that assesses equipment design, process conditions, operating protocols and water quality issues.