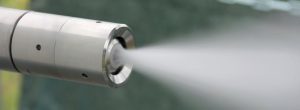
Enhancing sulphuric acid production
In this case study, CS Combustion Solutions presents a comprehensive strategy for the capacity enhancement and optimisation of a sulphuric acid plant that was facing several operational challenges.
In this case study, CS Combustion Solutions presents a comprehensive strategy for the capacity enhancement and optimisation of a sulphuric acid plant that was facing several operational challenges.
This troubleshooting case study describes an incident at one of the sulphur recovery units at BPCL Kochi Refinery, India. Following a maintenance turnaround of the unit in 2022, unusually high H2 S and SO2 were observed at the outlet of the Claus section. This created an additional load on the tail gas reactor, which led to frequent plugging in the quench column and frequent outages in the tail gas unit, creating environmental and reliability issues in the unit. The activities to identify the root cause of the incident are described and the measures to solve the problem are shared.
Large-scale ammonia cracking technology and catalysts will enable the full potential of ammonia to be realised as industries transition towards low carbon energy. In this feature we report on the current status of ammonia cracking processes and catalysts.
Anton Kariagin and Stefan Gebert of Clariant discuss the benefits and commercial performance of the new low temperature shift (LTS) catalyst – ShiftMax 217 Plus. A case study demonstrates the benefits of this catalyst, providing ultra-low methanol formation resulting in increased ammonia production and/or energy savings.
Johnson Matthey's latest KATALCO™ 71-7F high temperature shift catalyst with its robust shape provides lower lifetime pressure drop.
Cobalt-molybdenum (CoMo) catalysts are integral components of tail gas units (TGUs), playing a vital role in reducing harmful sulphur dioxide (SO2 ) emissions arising from Claus sulphur recovery units. Effective activation of these catalysts is essential for their optimal performance. The consequence of sulphiding at low temperatures and atmospheric pressure in low temperature TGUs is to compromise effectiveness of catalyst activation. In the final part of this two-part article, Michael Huffmaster , Consultant, presents case study results using a discrete reactor model incorporating heat, mass transfer, and activation reaction kinetics to assess the impacts of these variables on in-bed temperature profile and activation effectiveness. Tailoring gas rate, composition, and temperature progression can achieve in-bed exotherms which improve CoMo catalyst activation effectiveness for low temperature tail gas units.
Catalyst development for nitric acid plants is strongly dependent on operating pressures and nitrogen loading levels. Dr Hadi Nozari of Johnson Matthey provides a review of some key catalyst design principles, emphasising the critical role of operating pressure in catalyst selection and highlighting the innovative contributions of Johnson Matthey in advancing catalyst technology for ultra-high-pressure ammonia oxidation in nitric acid plants.
Cobalt-molybdenum (CoMo) catalysts are integral components of tail gas units (TGUs), playing a vital role in reducing harmful sulphur dioxide (SO2 ) emissions arising from Claus sulphur recovery units. Effective activation of these catalysts is essential for their optimal performance. The consequence of sulphiding at low temperatures and atmospheric pressure in low temperature TGUs is to compromise effectiveness of catalyst activation. In the first part of this two-part article, Michael Huffmaster , Consultant, explores CoMo catalyst activation at low pressure, focusing on sulphiding reaction pathways and the impact of temperature and the composition of the sulphiding media on reaction kinetics, specifically the concentration of H2 , H2 S, and H2 O.
MECS, Inc. (MECS) has developed a new impaction-based mist eliminator called Brink® Prime Impact™ , which offers equivalent or improved efficiency at higher throughput and the same pressure drop as traditional impaction beds, resulting in the ability to debottleneck existing inter-pass absorption towers and final absorption towers in sulphuric acid plants or design new or replacement towers with smaller diameters, thus reducing investment cost.
Axens has developed a new titania-based catalyst named CRS 41, which has a much larger porosity than its renowned predecessor, CRS 31 catalyst. Thanks to an improved catalyst manufacturing process and a new recipe, the porosity of CRS 41 has been increased while preserving the mechanical resistance for loading, allowing customers to optimise their capex by either reducing the Claus reactor size or loading volume of TiO2 catalyst.