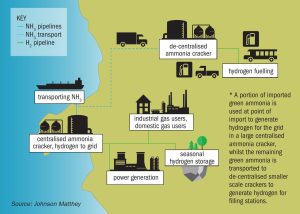
Converting clean ammonia back into hydrogen
Advances in clean hydrogen and ammonia production is fuelling worldwide interest in a new market for hydrogen and ammonia to provide a reliable low-carbon energy future. Ammonia cracking, the dissociation of ammonia back into hydrogen, delivers a pathway to large-scale sustainable hydrogen production. In this article KBR, Johnson Matthey, thyssenkrupp Uhde, Duiker, Proton Ventures and Casale report on their technologies and approaches to ammonia cracking in a low carbon economy.