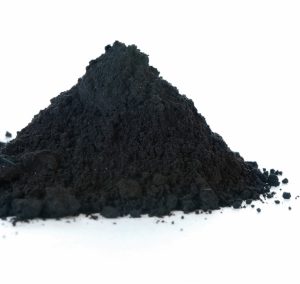
Methane pyrolysis – hope or hype?
Cansu Doganay of Lux Research takes a look at the current technology landscape for methane pyrolysis for producing low-carbon hydrogen from natural gas.
Cansu Doganay of Lux Research takes a look at the current technology landscape for methane pyrolysis for producing low-carbon hydrogen from natural gas.
Air Liquide presents the results of an internal study to identify preferred natural gas-based plant configurations at a methanol capacity of 250 t/d. Delivering small capacity plants requires a focus on the total cost of ownership (TCO) for the economics to be successful, in addition to the CO 2 footprint of the operation. As found by this study, SMR concepts are naturally power balanced for standalone greenfield operations and show no particular advantage for power import in a brownfield setting. POX and ATR cases are greatly improved and even advantaged in a brownfield setting compared to SMR when shifting from power balance to power import cases.
Advanced Methanol Amsterdam (AMA) is a production facility, that will be realised in the Port of Amsterdam's Biopark, which is destined to produce advanced methanol that meets the European renewable energy directive (RED) requirements. Once completed, AMA will be the flagship production site for GIDynamics and GIDARA Energy and for its High Temperature Winkler (HTW ® ) gasification technology. AMA will also be the first of its kind green methanol unit designed by Casale.
NORAM has recently introduced a patented acid entrainment mitigation device (EMD) to deal with acid mist carryover from sulphuric acid towers.
Topsoe has made a number of changes to its board. Kim Saaby Hedegaard has been appointed as the company’s new Executive Vice President, Power-to-X. Hedegaard has served as interim Head of Power-to-X since May 2022. Before that, he held the position as Chief Operations Officer (COO). He joined Topsoe in 1999 and has since held various leadership positions within engineering, technology, and sales. Since 2017, he was responsible for Catalyst Production and Technology globally. He holds a MSc in chemical engineering from the Technical University of Denmark. He is replaced as COO by Andreas Bruun Jørgensen.
The capabilities of OGT’s ProTreat ® simulator were recently enhanced by the addition of gas treating with hybrid solvents. The functionality was developed generically to make it as broadly applicable as possible. In this article, Ralph H. Weiland of Optimized Gas Treating investigates the effect of TEG as a contaminant on the performance of DEA, MDEA, and piperazine-promoted MDEA in a gas treating application.
With energy prices skyrocketing, sulphuric acid plant operators face a heightened challenge to improve plant efficiency. Martin Alvarez from Topsoe discusses how the company’s new high-activity catalyst, VK38+, can help acid plants maximise energy efficiency to secure important economic benefits while simultaneously reducing their carbon footprint.
Daniel R. Egger of Sulzer Chemtech Ltd discusses mist elimination challenges in strong sulphuric acid applications and presents the unique Sulzer KnitMesh XCOAT™ mist eliminator as an ideal solution for corrosive services such as in sulphuric acid drying towers.
At the organisation’s first face to face meeting since covid, in Vienna in early October, OPEC+ ministers agreed to cut global oil supplies by 2 million bbl/d in November. OPEC+ is a group of 24 oil-producing nations, made up of the 14 members of the Organisation of Petroleum Exporting Countries (OPEC), and 10 other non-OPEC members, including Russia. In a statement, the group said the decision to cut production was made “in light of the uncertainty that surrounds the global economic and oil market outlooks.”
Refractories are heat resistant materials used in high temperature processes to protect industrial equipment such as utility boilers, heaters, and ammonia primary and secondary reformers against heat and chemical attack. In this article Hasan Akbari of Kermanshah petrochemical Industrial company (KPIC) reports on experiences of different stages of refractory casting in the secondary reformer of an ammonia plant, located in Kermanshah province of Iran (KPIC – Phase II). The pouring operation was carried out in three stages and each section was cast nonstop for a period of three days in total.