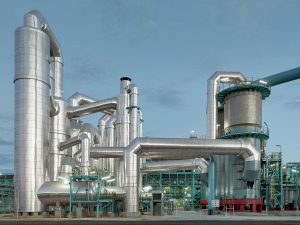
Sulphuric acid markets
Although 2019 had been a volatile year for acid markets, with shutdowns disrupting supply, the coronavirus outbreak wrought even more havoc in 2020, across both supply and demand.
Although 2019 had been a volatile year for acid markets, with shutdowns disrupting supply, the coronavirus outbreak wrought even more havoc in 2020, across both supply and demand.
Several highly corrosion resistant materials are available today for use in handling process fluids encountered in the production of concentrated sulphuric acid. These alloys, properly selected for the operating conditions, provide the benefits of long operating life under harsh operating conditions extending the period of uninterrupted production cycles and lowering the incidence of catastrophic equipment failure. In this article, M. J. Cooke of Weir Minerals discusses materials of construction for pumps, valves and piping used in the production of sulphuric acid.
In early October Tesla held a ‘battery day’ event at its headquarters in Fremont, California. Speaking at the event, company founder and CEO Elon Musk outlined his vision for the electric car industry over the coming decades, and spoke particularly to his ambitions for the nickel industry. He had already called for more mining of nickel earlier in the year, and has said that Tesla is developing cathodes that will contain higher nickel and no cobalt. The latter comes after a lawsuit against Tesla and several other high-tech US firms for allegedly supporting human rights violations by buying cobalt from the Democratic Republic of Congo. Musk echoed the potential ‘reputational risk’ for the nickel market and called for more sustainable nickel production, dangling the prospect of a “giant contract” with any miners that could produce nickel in an “environmentally sensitive way.” Tesla is reportedly in discussions with Vale and BHP as well as the Indonesian government concerning potential investments in nickel production.
As urea plants grow in capacity, so does the need for finishing technologies with higher capacities. Barbara Cucchiella , senior process engineer at Stamicarbon, describes how her team has risen to the challenge of the global trend for larger granulation plants.
The US Environmental Protection Agency (EPA) and the US Department of Agriculture (USDA) have announced the ‘Next Gen Fertilizer Challenge’, a joint EPA-USDA partnership and competition to advance agricultural sustainability in the United States. The competition includes two challenges that seek proposals for new and existing fertilizer technologies to maintain or improve crop yields while reducing the impacts of fertilizers on the environment.
Recent protests in Belarus have triggered a wave of share price volatility, London’s Financial Times reported on 18th August.
K. Hanlon Kinsberg and J. Lewis of Comprimo review the main approaches for mercaptan removal in gas processing plants, based on past project experience and generally accepted industry practice.
Reg Adams of pigments and titanium dioxide consultancy Artikol reviews the demand for sulphuric acid in the manufacture of TiO2 , and the prospects for consumption over the next few years.
Haldor Topsoe and Comprimo® have announced a global strategic alliance to jointly license the TopClaus sulphur removal and recovery technology. TopClaus combines Topsoe’s energy efficient wet sulphuric acid (WSA) process with the industry-standard Claus process, enabling plant operators to handle acid gases and achieve sulphur removal efficiencies of above 99.9%. The Claus part of the unit recovers elemental sulphur from acid gases, and the tail gases from the Claus unit are then treated in the WSA unit, where the remaining sulphur compounds are converted into sulphuric acid.
DuPont Clean Technologies has announced the successful startup and performance test of a 300,000 t/a STRATCO® alkylation unit licensed at the Hengli Petrochemical Company’s new refinery complex on Changxing Island in the Harbour Industrial Zone, China. The new alkylation unit enables Hengli to produce high-quality alkylate from a 100% isobutylene feed stream, catalysed by sulphuric acid. This first-of-a-kind unit was developed through DuPont research into the best ways to maximise product octane and minimise end point with this feedstock. Hengli had awarded DuPont the contract for the new alkylation unit as well as a MECS® sulphuric acid regeneration unit in 2015.