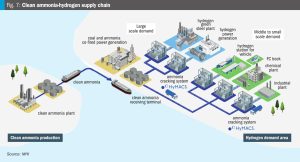
Low temperature ammonia cracking technology
Mitsubishi Heavy Industries is developing a low temperature ammonia cracking technology (HyMACS™ ) that leverages exhaust heat from existing sources, such as boilers, steam turbines, engines, and heating furnaces. This innovative approach, which also includes the development of more efficient membrane separation technology using molecular sieves for hydrogen purification, is designed to offer a more sustainable, reliable and cost-effective pathway towards hydrogen production.