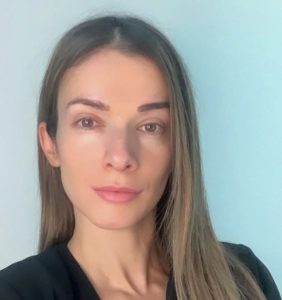
People
CRU has appointed Zain Ajlouni as its regional director of sales, marketing and customer services for the Middle East and Northern Africa (MENA). She will be Dubai-based and cover the mining, metals and fertilizer sectors across the region.
CRU has appointed Zain Ajlouni as its regional director of sales, marketing and customer services for the Middle East and Northern Africa (MENA). She will be Dubai-based and cover the mining, metals and fertilizer sectors across the region.
Some 410 delegates from 208 companies and 45 countries participated virtually in the IFA Global Sustainability Conference, 28-31 March 2022. We report on the main highlights of this four-day event.
The recently-published IEA Ammonia Technology Roadmap sets out a future pathway for decarbonising the nitrogen industry. New technology options for low-carbon ammonia production are emerging and project activity is on the rise.
By using modular construction, operational modelling and digital plant control, thyssenkrupp Uhde can offer customers fast-build, capital efficient green ammonia plants. Dr Christian Renk and Dr Klaus Nölker explain the company’s innovative approach to plant construction, design and control.
The Woodsmith polyhalite project in the UK is starting to benefit from Anglo American’s ownership, with the mining major leveraging its key advantages to good effect. These include the company’s operational size and financial stability, its vast mineral extraction experience, and premium product marketing expertise. The company also believes that the fertilizer sector will benefit from its leadership in mining industry sustainability.
Heat recovery systems at sulphuric acid plants have been providing carbon-free energy for decades now and continue to improve. There is also potential to combine the clean power generated at acid plants with hydrogen production from water electrolysis. This could provide the basis for green fertilizer production.
Economically viable production of green ammonia requires plants that can react to fluctuations in renewable power thanks to their flexible design. Casale’s Francesco Baratto, Giovanni Genova and Sergio Panza explain how new tools are helping design green ammonia plants that deliver the highest possible production at the lowest possible cost.
Nitrogen+Syngas’s annual listing of new ammonia, urea, nitric acid and ammonium nitrate plants.
On February 27th, in a speech to the Bundestag, Germany’s chancellor Olaf Scholz described the events then unfolding as a “zeitenwende” – a historical turning point. He was speaking of German foreign and security policy, but it seems likely that Russia’s February 24th invasion of Ukraine may end up marking a break with the past in many different ways. Last issue’s Editorial was written when Russia’s ‘special military operation’ was still only a few days old, and the situation was still very fluid. Two months on, and for all of the uncertainties remaining, some glimpses of the way that things are changing are becoming clearer.
A new fully automated process has been developed that combines real time H2 S readings from an H2 S analyser and Q2 Technologies’ proprietary scavenger chemistry to treat high H2 S crude oil on demand. The process provides an efficient and effective way to administer the chemical product to avoid overtreating or undertreating. In some cases, the end user is seeing greater than 50% savings. It is a unique confluence of technology including IoT, advanced chemistry, and oil and gas personnel incentivised to demonstrate continuous improvement.