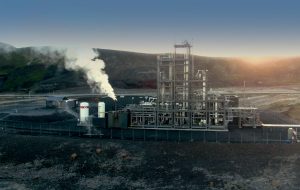
Carbon dioxide as a feedstock
Falling costs for production of hydrogen by electrolysis are encouraging more serious consideration of using recovered carbon dioxide as a feedstock for chemicals and even fuels production.
Falling costs for production of hydrogen by electrolysis are encouraging more serious consideration of using recovered carbon dioxide as a feedstock for chemicals and even fuels production.
Fugitive dust emissions during the handling and storage of formed sulphur can result in negative environmental impacts and under specific conditions result in an explosion hazard. Enersul has developed a dust suppression system specifically targeted at controlling sulphur dust particles. The Enersul SafeFoam Transfer System (STS) reduces sulphur fines at critical transfer points throughout any sulphur handling system, resulting in a significantly safer and more environmentally friendly sulphur handling system.
IPCO provides an update on its latest activities, with flexible processes enabling IPCO’s project for the first drum granulation plant in Europe to remain on track despite unprecedented Covid-19 restrictions.
US crude production dropped rapidly during April and May, but figures released by the Energy Information Administration (EIA) showed that this had plateaued and there have been some well reactivations and drawdowns from crude stocks. Total production curtailments in North America were more than 2.5 million bbl/d in May. ConocoPhillips Chairman and CEO Ryan Lance said in remarks to the media that a return to pre-outbreak production levels of 13 million bbl/d looked “pretty difficult”, although a recovery to 11 million bbl/d or possibly as high as 12 million bbl/d would be possible, depending upon OPEC moves. About one third of the company’s production was shut in as of the start of June – some 400,000 bbl/d. Lance argued that low cost shale oil resources still exist in the US, but there will be pressure on companies to reduce capital spending. The Covid19 outbreak has had a major impact in investment announcements, with a large number of project delays in the US due to uncertainty over future demand levels. Planned US exploration and production expenditure is down by 50% for the second half of 2020, while the rig count was down 60% on February.
The removal of hydrogen sulphide (H2 S) has become increasingly important as the oil and gas industry moves towards more efficient and sustainable production of lower emission clean fuels. BASF and ExxonMobil* have jointly developed a proprietary amine, OASE® sulfexx™ , to help refiners and gas processors achieve sulphur removal targets while reducing their carbon footprint via lower energy consumption. This new solvent technology is suitable for low and high pressure applications and shows superior performance characteristics over generic and promoted MDEA formulations, as well as sterically hindered amines such as FLEXSORB™ SE and SE Plus.
With increasing frequency, companies that have molten sulphur on site must put environmental controls on the vent streams from molten sulphur pits, storage tanks and loading operations. This article* describes the typical characteristics of molten sulphur vent gas streams as well as some of the important chemistry related to these systems in caustic scrubbers. Solids deposition issues observed in the field with caustic scrubbers operating on actual molten sulphur vent gas streams are presented. Design and operational strategies to mitigate plugging in molten sulphur vent gas scrubbers are also summarised in this article by D. J. Sachde, K. E. McIntush, D. L. Mamrosh , and C. M. Beitler of Trimeric Corporation.
At the end of last year, in our November/ December 2019 issue, I remarked upon the fresh impetus that the International Maritime Organisation’s (IMO) target of reducing carbon emissions from shipping by 50% in 2050 (compared to a 2008 baseline) had given to the idea of using ammonia as a shipping fuel. This year, in spite of You Know What, things seem to have, if anything, accelerated.
A round-up of current and proposed projects involving non-nitrogen synthesis gas derivatives, including methanol, hydrogen, synthetic/substitute natural gas (SNG) and gas- and coal to liquids (GTL/CTL) plants.
Air Products and Haldor Topsoe have signed a global alliance agreement. Under the terms of the agreement the two companies will use their combined market network for developing potential projects and the combination of their expertise on large-scale ammonia, methanol and/or dimethyl ether (DME) plants to be developed and built globally. It gives Air Products access to Topsoe’s technology licenses and the supply of engineering design, equipment, high-performance catalysts and technical services for ammonia, methanol and DME plants that are built, owned and operated by Air Products. It also allows for the integration of Topsoe’s technology into many Air Products’ technologies including gasification of various feedstocks, and synthesis gas processes.
There is an urgent need to limit the rise in global temperatures to avoid severe environmental and societal impact. This can be expressed as a target to achieve net zero carbon emissions by 2050. The provision of decarbonised hydrogen at scale is an essential step in helping to achieve net zero. Johnson Matthey’s Low Carbon Hydrogen (LCH) technology permits the needs of scale and urgency to be met. J. Pach of Johnson Matthey presents a serious response to a serious threat.