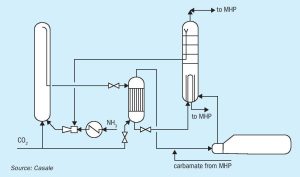
Nitrogen technology showcase
We highlight recent production advances and innovations in nitrogen fertilizer production from Casale and Stamicarbon, two global leaders in process technology.
We highlight recent production advances and innovations in nitrogen fertilizer production from Casale and Stamicarbon, two global leaders in process technology.
IPCO has expanded its Rotoform range with the high yield XG model for granulation of suspensions. Designed for applications such as sulphur bentonite and urea mixes as well as NPK and other fertilizers, this new Rotoform model can convert solid-containing product melts into consistent, high quality pastilles from 2-4 mm diameter.
Paradeep Phosphates Limited (PPL) and Mangalore Chemicals & Fertilizers Limited (MCFL) have agreed to merge.
Low carbon intensity hydrogen and ammonia production schemes from KBR, Air Liquide, Mitsubishi Heavy Industries, Casale and Johnson Matthey.
Granulation technology generates a premium urea end-product in large volumes capable of withstanding lengthy storage and extreme shipping conditions. Prilling technology, meanwhile, given its typically lower investment cost, can be an attractive option for smaller-scale urea producers supplying local markets. Stamicarbon’s Dr Wilfried Dirkx, Ahmed Shams and Branislav Manic explore the technology options for urea finishing.
BHP has approved an investment of $4.9 billion (CAD 6.4 billion) in stage two of its Jansen potash project (Jansen Stage 2) in Saskatchewan, Canada.
Ballestra, Nitricity, Solex Thermal Science and Stamicarbon showcase their state-ofthe-art equipment and technologies.
The first global review of phosphate rock resources since 2010 has reported that technically recoverable reserves should last for more than 300 years.
Fertilizer plant owners are installing highly efficient and reliable scrubbing equipment to satisfy increasingly strict emissions regulations globally. We highlight recent advances in scrubbing performance and technology.
Sulphur run-down lines are typically sized by referencing past projects and ‘rules of thumb’. Very little analysis is performed to identify the impacts of slope, fittings, valves, etc. It is critical to maintain an open vapour path from the condenser to the sealing device. CSI has observed problems in the field which appear to be caused by undersized run-down lines. CSI developed a method of predicting the liquid level in a run-down line that considers the most common elements. This was accomplished by building a full-scale model of a run-down line that evaluated pipe NPS, pipe slope, rod-out-cross elbows, rod-out cross elevation drops, and liquid viscosity. This article* presents the testing and development of the predictive method as well as the predictive method itself.