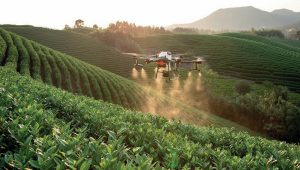
Better nitrogen use
Improvements to nutrient use efficiency (NUE), particularly for nitrogen, can deliver dual environmental and economic benefits. We report on recent developments in nitrogen management and global progress on NUE.
Improvements to nutrient use efficiency (NUE), particularly for nitrogen, can deliver dual environmental and economic benefits. We report on recent developments in nitrogen management and global progress on NUE.
More than 230 delegates from 45 countries participated in CRU’s Sustainable Fertilizer Production Technology Forum, 20-23 September 2021. To highlight this successful virtual event, we report on keynote and selected technical presentations.
China’s private sector Shenghong Petrochemical refining complex is targeting a startup in late November, following the receipt of its first cargo of crude in October. The greenfield refining complex in the eastern Lianyungang petrochemical zone has a capacity of 16 million t/a, including a 320,000 bbl/d crude unit – the largest single stream CDU in China – and a 76,000 bbl/d naphtha reformer. Product capacities include 56,000 bbl/d of gasoline, 41,000 bbl/d of diesel and 32,000 bbl/d of jet fuel. Construction began in mid-2019, delayed from 2018 by late approval of its environmental impact assessment, but has been achieved within two months of the scheduled completion date in spite of the coronavirus pandemic. Shenghong Petrochemical is owned by Eastern Shenghong, a producer of petrochemical products and chemical fibres.
Rapidly escalating natural gas prices forced plant closures across Europe during September. Worst affected was the UK, where a fire at a cross-Channel electricity cable and low output from wind energy has, combined with low domestic storage capacity led to a surge in demand for gas for power stations and wholesale gas prices reached a record 350 pence per therm (equivalent to $46/ MMBtu) in October. On September 15th, CF Industries announced that it was halting operations at both its Billingham and Ince fertilizer plans due to high gas prices. Although ammonia prices have also risen, they have not kept pace with gas price rises, and there is a limit to what farmers could be expected to pay. CF CEO Anthony Will said: “$900 is the gas cost in a tonne of ammonia and the last trade in the ammonia market that was done was $700 a tonne”. As these plants supply most of the UK’s carbon dioxide for food and drink manufacture, the government said it would provide “limited financial support” to keep the Billingham plant operational, and that plant re-started on September 21st. Meanwhile, BASF closed its Antwerp and Ludwigshafen plants in Belgium and Germany due to what the company called “extremely challenging” economics. Fertiberia ceased production at its Palos de la Frontera site in Spain, and Puertellano remained down for scheduled maintenance. Yara shut 40% of its European ammonia production in September, and OCI partially closed its Geleen plant in the Netherlands. Achema in Lithuania decided against restarting its ammonia plant following maintenance in August, and OPZ in Ukraine shut one ammonia line at Odessa, with Ostchem and DniproAzot likely to follow. Borealis in Austria also reduced production.
Topsoe has begun operations at a demonstration plant for the production of methanol from biogas. The aim is to validate the company’s electrified technology for cost-competitive production of sustainable methanol from biogas as well as other products. The project is supported by the EUDP Energy Technology Development and Demonstration Program and is developed together with Aarhus University, Sintex A/S, Blue World Technology, Technical University of Denmark, Energinet A/S, Aalborg University, and Plan-Energi. The demonstration plant is located at Aarhus University’s research facility in Foulum, and will have an annual capacity of 7.9 t/a of CO 2 -neutral methanol from biogas and green power and is scheduled to be fully operational by the beginning of 2022. It uses Topsoe’s eSMR ™ technology, which is CO 2 -neutral when based on biogas as feedstock and green electricity for heating. It also uses half the CO 2 that makes up about 40% of biogas and typically is costly to separate and vent in production of grid quality biogas.
Reducing carbon footprint in the synthesis of chemicals is a new challenge, a necessary requirement in the pursuit of sustainable products designed to minimise environmental impacts during their whole lifecycle. So-called “green” technologies for ammonia, methanol and hydrogen are being developed to meet these challenges. Casale, Linde, thyssenkrupp Industrial Solutions, Toyo Engineering Corporation, Haldor Topsoe and Stamicarbon report on some of their latest developments.
Major fertilizer industry players such as Stamicarbon, Nutrien and CF Industries are ramping up investment in ‘green’ and ‘blue’ fertilizer production. Consequently, low-carbon production technologies are being scaled-up and deployed commercially.
Johnson Matthey and MyRechemical have formed an alliance to commercially develop waste to methanol technology. In this article, two different approaches to waste disposal and chemical production are analysed: a post combustion scenario with waste incineration and hydrogenation of the CO2 recovered from flue gas to produce methanol, and a precombustion approach with waste gasification followed by conversion of synthesis gas into methanol.
Maire Tecnimont SpA says that its subsidiaries MET Development, Stamicarbon and NextChem have collectively begun work on a renewable power-to-fertilizer plant in Kenya. MET Development has signed an agreement with Oserian Development Company for the development of the plant at the Oserian Two lakes Industrial Park, on the southern banks of Lake Naivasha, 100 km north of Nairobi.
We highlight the large-scale nitrogen projects that are currently under development across the globe – with a focus on ammonia and urea technology licensors and engineering contractors.