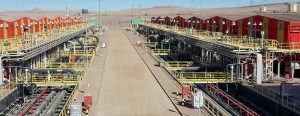
Sulphuric acid leaching
There was a rapid increase in sulphuric acid demand for copper, uranium and nickel leaching from 1995-2015, but over the past few years growth in this sector has slowed dramatically. Now however there are signs that demand is starting to pick up again with several new projects under development.