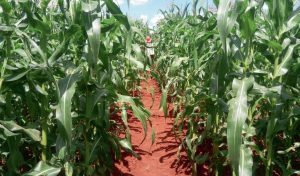
Delivering sulphur nutrition
Sulphur is a vital secondary crop nutrient. It can be delivered in sulphate, thiosulphate and elemental form. The range of product and process options are outlined.
Sulphur is a vital secondary crop nutrient. It can be delivered in sulphate, thiosulphate and elemental form. The range of product and process options are outlined.
China has been the major market for base metals, including copper, nickel, lead and zinc over the past two decades as the country rapidly industrialised. But with China’s growth slowing due to demographics and market saturation, where are metals markets and production of/demand for sulphuric acid likely to go next?
Chinese domestic sulphur supply growth remains strong. Production is expected to rise in 2023, putting pressure on import demand potential. In 2022 total imports were 7.6 million tonnes, with a stable view for the year ahead.
SulGas, South Asia’s sulphur recovery and gas treating conference, returned to a live event in 2023, providing participants with a platform to interact with experts in the field, share best practices and troubleshooting tips with fellow refiners and discuss advanced technologies and operating procedures with technology providers, vendors and licensors.
SO2 breakthroughs remain an ever present threat to the successful operation of reductive, quenchamine-based tail gas clean-up units (TGUs). Effects can range from mild and annoying to quite severe, including failure to comply with environmental permit regulations and refinery shutdown. G . Simon A. Weiland, Nathan A. Hatcher, Prashanth Chandran, Daryl Jensen, Ralph H. Weiland, Jeff Weinfeld of Optimized Gas Treating, Inc. and Michael Huffmaster , Consultant.
Previously, recuperative reforming has been mostly applied for capacity increase revamps, but nowadays it is a key enabler for efficient low carbon hydrogen and syngas production. Jan-Jaap Riegman of Technip Energies, Francesco Baratto of Casale and Stefan Gebert of Clariant discuss the benefits of recuperative reforming for reducing the carbon footprint of existing assets.
Continuing growth in energy uses indicate robust demand for methanol over the coming years, but the current slate of new projects does not look sufficient to meet it. Is methanol approaching a supply crunch?
Market Insight courtesy of Argus Media
On March 20th this year, just as this issue was going to print, the UN Intergovernmental Panel on Climate Change (IPCC) issued its Synthesis Report, one of its 5-7 yearly comprehensive assessments of how the world’s climate is changing and what needs to be done to ameliorate it. In spite of all of the progress that has been made since the 5th Synthesis Report in 2017, the IPCC notes that: “the pace and scale of what has been done so far, and current plans, are insufficient to tackle climate change.” While the body believes that keeping warming to 1.5°C above pre-industrial levels is still possible, it is not likely unless work to decarbonise proceeds more rapidly. In particular, the IPCC suggests that CO2 and equivalent emissions need to fall by 43% by 2030 compared with 2019 values, and 60% by 2035 to achieve this goal.
Brazil’s agricultural industry continues to expand at the same time that most of its nitrogen fertilizer industry has shut down. Meanwhile, Venezuela continues to deal with the consequences of years of underinvestment and mismanagement, and elsewhere, gas discoveries in other parts of the continent have not led to the new plant construction boom that had once been hoped for.