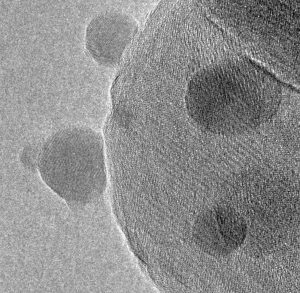
A new generation of methanol catalysts
Haldor Topsoe has launched a new methanol synthesis catalyst, MK-181 PRIME, based on new technology developed via close study of copper-zinc interactions on the catalyst surface.
Haldor Topsoe has launched a new methanol synthesis catalyst, MK-181 PRIME, based on new technology developed via close study of copper-zinc interactions on the catalyst surface.
Olefins production from methanol, particularly in China, has come to dominate the methanol market over the past few years. However, environmental and market concerns complicate the outlook there.
Alistair Wallace, Head of Fertilizer Research, Argus Media, assesses price trends and the market outlook for nitrogen.
Paving the way for commercially attractive, sustainable, decarbonised fertilizer production, J. Dobrée of Stamicarbon BV discusses the latest developments for nitrate fertilizer production based on renewable feedstocks sourced from solar and wind energy. Stamicarbon has upgraded plant designs used in the past to create a new type of small-scale fertilizer plant capable of producing a product mix that can be adjusted to meet specific local requirements with maximised output value, thereby maintaining a competitive position towards imported products and large-scale producers.
Evaporation and crystallisation are widely used throughout the fertilizer industry. Major applications and the types of equipment used are reviewed by Laurent Palierne and Norbert Strieder of GEA Group.
CRU’s Laura Cross guides us through the current Covid-19 crisis and flags up the unique risks faced by the fertilizer industry as the pandemic unfolds.
We highlight recent innovations in sulphuric acid plant design and construction. NORAM and CPPE are offering a new hybrid sulphuric acid process. KVT, meanwhile, has upgraded its wet sulphuric acid technology to reduce capex, opex and emissions. Improved methods of construction and new materials from Koch Knight are also helping to optimise acid tower design
Nutrien is the world’s largest crop nutrient company with a market capitalisation of almost $20 billion (Figure 1). This fertilizer industry giant produces and distributes over 25 million tonnes of potash, nitrogen and phosphate products for agricultural, industrial and feed customers globally. The company’s agriculture retail business also serves over 500,000 growers worldwide through a network of international outlets.
Three large-scale phosphoric acid plants constructed as part of the world-class Umm Wu’al project in Saudi Arabia are now fully operational. James Byrd of Worley (formerly Jacobs ECR) describes the execution of the project from basic engineering through to plant performance tests.
We profile the US ‘big three’ North American phosphate producers, Mosaic, Nutrien and Simplot, and disruptive market entrant Itafos.