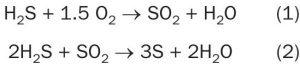
Better monitoring and control in Claus plants
Applied Analytics discusses potential improvements made possible with data and analytical measurements fed into improved mathematical models to produce a more proactive approach to control and better performance of sulphur recovery units, AMETEK Process Instruments explains the benefits of feed forward control, SICK reports on reliable continuous emission monitoring systems and WIKA introduces a new purge-free system to measure refractory temperature in the Claus reaction furnace.