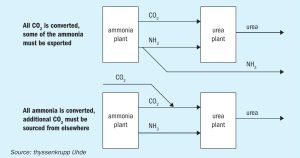
Revamp activities in urea plants
Urea revamp activities are performed to achieve improvements of the urea plant. Besides the typical capacity increase there are many options to reduce operation costs, increase plant availability or reduce environmental impact. In this article Marc Wieschalla of thyssenkrupp Uhde GmbH provides an overview of some of the options from an EPC contractor point of view.