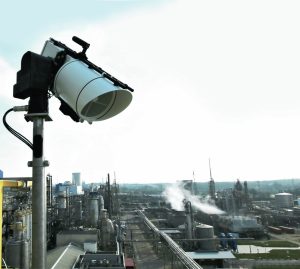
On the lookout for gas leaks
Scanfeld™ is the world’s first remote sensing solution for fully automated early-warning gas leak detection for chemical plants. Using FTIR spectroscopy, Scanfeld™ identifies hundreds of different gases in real time from kilometres away. With just a few Scanfeld™ sensor units, large production sites, tank farms, or gas loading areas can be monitored reliably. Gas leaks are quickly detected, and the formation of dangerous gas clouds is monitored, measured, and visualised. René Braun of Grandperspective discusses how the system works and how it is being applied in industry.