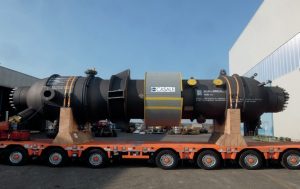
Maximising urea plant efficiency and reliability
From new materials of construction and improved equipment designs to the latest digital tools, Casale, thyssenkrupp Industrial Solutions, Saipem, TOYO and Stamicarbon report on some of their latest achievements.