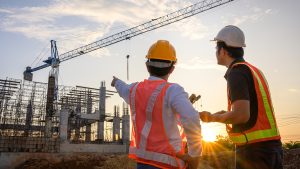
Contract expected on oil project
Spetco’s contract with the Kuwait Oil Company (KOC) to install depletion compression systems and sulphur recovery units (SRUs) is said to be awaiting final approval. The $460 million project will upgrade two key facilities in North Kuwait, and Spetco says that it expects project execution will start quickly after final approval. The project involves installing new units at the Early Production Facility 50 (EPF-50) and Jurassic Production Facility 3 (JPF-3) using uses a build-own-operate-transfer (BOOT) contract model. The contract was originally tendered in 2023, but scope changes meant that the deadline has been extended several times.