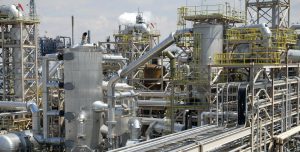
Sulphuric Acid News Roundup
DuPont has agreed to sell its Clean Technologies business for $510 million to an international private equity consortium, comprising BroadPeak Global, Asia Green Fund and The Saudi Arabian Industrial Investments Company (Dussur). The new, independent company has been named Elessent Clean Technologies and will be a global leader in process technologies to drive sustainability and carbon neutrality in the metal, fertilizer, chemical and oil refining industries. Elessent retains exclusive rights to the technologies, expertise, products, and services including: MECS® sulphuric acid and environmental technologies, BELCO® scrubbing technologies, STRATCO® alkylation technology and IsoTherming® hydroprocessing technology. Derived from the words “element” and “essential,” Elessent says that it will help customers produce, optimise or separate essential elements every day, creating clean alternatives to traditional industrial processes to minimise the impact on the environment while enabling our customers to produce essential elements critical to everyday life.