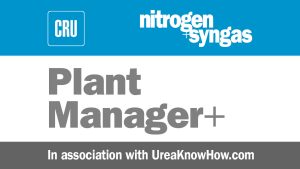
Incident No. 3: Backflow in pressurised leak detection system for loose liner of HP scrubber
This case study describes a backflow scenario in a pressurised leak detection system. Backflow can occur in case of a relatively large leak (crack in liner), where the flowmeter installed downstream of the equipment acts as a flow restriction, allowing pressure to build up.